Introduction to Flexible Circuits and SAP/mSAP
Flexible circuits, also known as flex circuits or flexible printed circuit boards (PCBs), are a type of electronic circuit that is built on a flexible substrate material. Unlike traditional rigid PCBs, flexible circuits can bend, fold, and twist without breaking or losing functionality. This makes them ideal for applications where space is limited, the device needs to conform to a particular shape, or the circuit will be subjected to repeated flexing.
The fabrication of flexible circuits involves several key processes, including the application of adhesives to bond the conductive layers to the flexible substrate. Two important adhesives used in this process are Surface Attachment Promoter (SAP) and Modified Surface Attachment Promoter (mSAP). These adhesives play a crucial role in ensuring the reliability and durability of the final flexible circuit product.
Key Advantages of Flexible Circuits
- Space savings: Flexible circuits can be bent and folded to fit into tight spaces
- Conformability: Flex circuits can conform to the shape of the device or enclosure
- Durability: With proper design and materials, flex circuits can withstand repeated flexing
- Weight reduction: Flexible circuits are typically lighter than equivalent rigid PCBs
- Improved signal integrity: Shorter signal paths in flex circuits can reduce noise and interference
The Importance of Adhesives in Flexible Circuit Fabrication
The Role of Adhesives
In a typical flexible circuit, the conductive traces are formed on a flexible dielectric substrate, such as polyimide or polyester. To ensure proper adhesion between the conductive layer (usually copper) and the substrate, an adhesive is applied. The adhesive serves several important functions:
- Bonding: The adhesive creates a strong bond between the conductive layer and the substrate, preventing delamination.
- Flexing: A well-chosen adhesive allows the flexible circuit to bend and flex without cracking or breaking.
- Insulation: The adhesive acts as an additional insulating layer, helping to prevent short circuits.
- Protection: Adhesives can help protect the conductive traces from environmental factors such as moisture and corrosion.
Common Adhesives Used in Flexible Circuits
Several types of adhesives are used in the production of flexible circuits, each with its own set of properties and advantages. Some of the most common include:
Adhesive Type | Key Properties | Typical Applications |
---|---|---|
Acrylic | Good flexibility, low cost | General-purpose flexible circuits |
Epoxy | High strength, good chemical resistance | High-reliability applications, harsh environments |
Polyimide | Excellent thermal and chemical resistance | High-temperature applications, aerospace, and military |
Silicone | High flexibility, wide temperature range | Wearable electronics, medical devices |
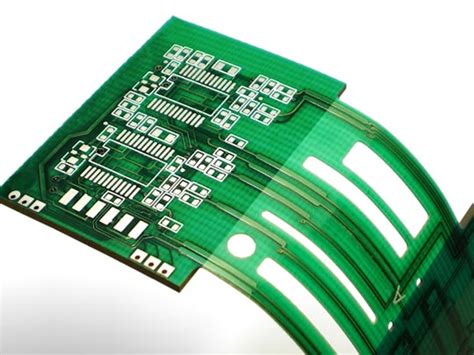
Surface Attachment Promoter (SAP)
What is SAP?
Surface Attachment Promoter, or SAP, is a type of adhesive specifically designed for use in flexible circuit fabrication. SAP is typically a polyimide-based adhesive that is applied to the flexible substrate before the conductive layer is added. The primary purpose of SAP is to improve the adhesion between the substrate and the conductive material, usually copper.
How SAP Works
SAP works by creating a strong chemical bond between the flexible substrate and the conductive layer. The polyimide-based adhesive contains functional groups that can react with both the substrate and the copper, forming a stable and durable interface. This improved adhesion helps prevent delamination and ensures the long-term reliability of the flexible circuit.
Advantages of Using SAP
- Enhanced adhesion: SAP provides a stronger bond between the substrate and conductive layer compared to other adhesives.
- Improved reliability: The strong adhesion provided by SAP helps prevent delamination and improves the overall reliability of the flexible circuit.
- Compatibility: SAP is compatible with a wide range of flexible substrate materials, including polyimide, polyester, and PET.
- Processing advantages: SAP can be easily applied using standard coating methods, such as screen printing or roller coating.
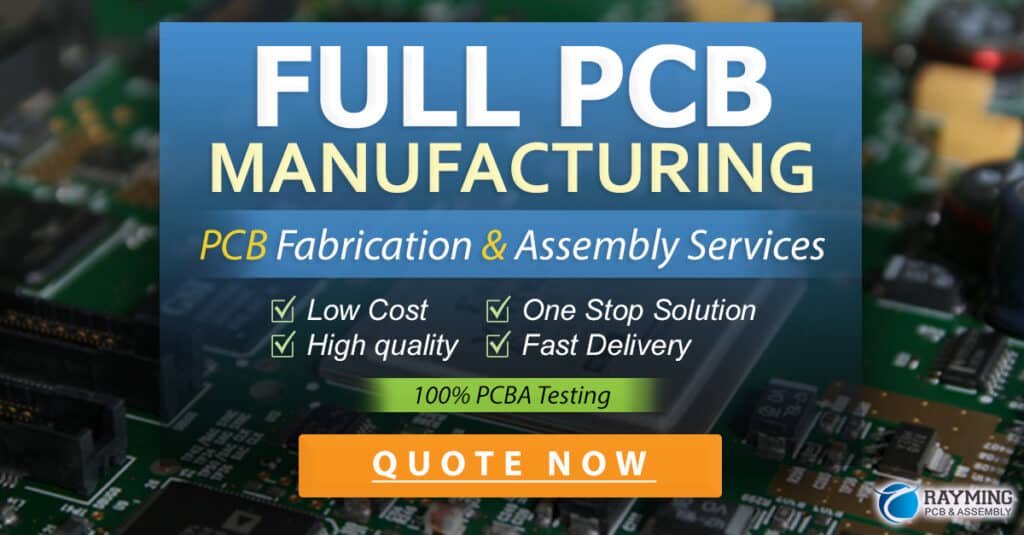
Modified Surface Attachment Promoter (mSAP)
What is mSAP?
Modified Surface Attachment Promoter, or mSAP, is an advanced version of SAP that has been specifically engineered to provide even better performance in flexible circuit applications. Like SAP, mSAP is a polyimide-based adhesive, but it has been modified with additional functional groups and additives to enhance its properties.
How mSAP Differs from SAP
The key difference between mSAP and standard SAP lies in the chemical composition of the adhesive. mSAP contains additional functional groups and additives that provide several benefits over traditional SAP:
- Improved adhesion: mSAP offers even stronger adhesion between the substrate and conductive layer compared to standard SAP.
- Better flexibility: The modified formulation of mSAP allows for greater flexibility, making it ideal for applications that require repeated bending or flexing.
- Enhanced durability: mSAP provides better resistance to environmental factors, such as moisture and temperature changes, improving the overall durability of the flexible circuit.
Advantages of Using mSAP
- Superior performance: mSAP offers better adhesion, flexibility, and durability compared to standard SAP.
- Expanded application range: The enhanced properties of mSAP make it suitable for a wider range of applications, including those with more demanding requirements.
- Improved manufacturing yields: The superior performance of mSAP can lead to fewer defects and higher manufacturing yields, reducing overall production costs.
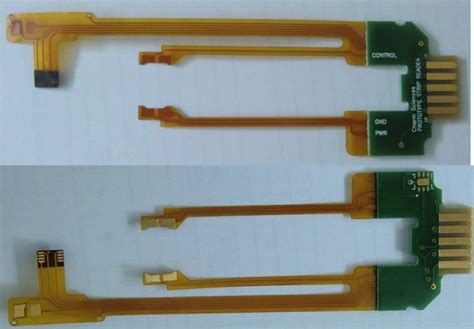
SAP and mSAP Application Processes
Surface Preparation
Before applying SAP or mSAP, the flexible substrate must be properly prepared to ensure good adhesion. This typically involves cleaning the surface to remove any contaminants, such as oils or dust. Some common surface preparation methods include:
- Solvent cleaning: The substrate is cleaned with a solvent, such as isopropyl alcohol, to remove contaminants.
- Plasma treatment: The substrate is exposed to a plasma (ionized gas) to clean the surface and increase its surface energy, improving adhesion.
- Chemical etching: The substrate may be treated with a chemical etchant to roughen the surface and provide better mechanical interlocking with the adhesive.
Adhesive Application Methods
SAP and mSAP can be applied to the flexible substrate using several methods, depending on the specific requirements of the application and the manufacturing process. Some common application methods include:
- Screen printing: The adhesive is applied through a patterned screen onto the substrate. This method is suitable for high-volume production and allows for selective application of the adhesive.
- Roller coating: The adhesive is applied using a roller, which transfers a uniform layer of the adhesive onto the substrate. This method is suitable for large-area coating and continuous processing.
- Spin coating: The substrate is rotated at high speed while the adhesive is dispensed onto the center of the substrate. Centrifugal force spreads the adhesive evenly across the surface. This method is suitable for small-scale production and provides a very uniform coating.
- Spray coating: The adhesive is atomized and sprayed onto the substrate surface. This method is suitable for coating irregular surfaces and can provide a uniform coating with minimal waste.
Curing and Post-Processing
After the SAP or mSAP has been applied, it must be cured to fully cross-link the adhesive and achieve its final properties. Curing is typically done by exposing the adhesive to heat, either in an oven or using inline heating methods. The specific curing temperature and time will depend on the adhesive formulation and the substrate material.
Post-processing steps may include:
- Lamination: The conductive layer (e.g., copper foil) is laminated onto the adhesive-coated substrate using heat and pressure.
- Patterning: The conductive layer is patterned using photolithography and etching to create the desired circuit layout.
- Cover layer application: A protective cover layer, such as a solder mask or coverlay, may be applied over the circuit to provide additional insulation and protection.
Future Trends and Developments
As the demand for flexible electronics continues to grow, there is an ongoing need for improved adhesives and processing techniques. Some of the key trends and developments in the field of SAP and mSAP include:
Advanced Adhesive Formulations
Researchers are continually developing new adhesive formulations with enhanced properties, such as:
- Improved thermal stability for high-temperature applications
- Greater flexibility and stretchability for wearable electronics
- Increased conductivity for better electrical performance
- Lower curing temperatures for compatibility with heat-sensitive substrates
Nanomaterial-Reinforced Adhesives
The incorporation of nanomaterials, such as carbon nanotubes or graphene, into SAP and mSAP formulations is an area of active research. These nanomaterials can provide several benefits, including:
- Enhanced mechanical strength and durability
- Improved thermal and electrical conductivity
- Increased adhesion to substrates
- Better resistance to environmental factors
Environmentally Friendly Adhesives
As environmental concerns continue to grow, there is an increasing focus on developing eco-friendly adhesives for flexible circuit fabrication. This includes:
- Bio-based adhesives derived from renewable resources
- Adhesives with low volatile organic compound (VOC) content
- Recyclable or biodegradable adhesive formulations
High-Speed Processing Techniques
To meet the growing demand for flexible circuits, manufacturers are seeking ways to increase production speed and efficiency. This includes the development of high-speed processing techniques for adhesive application and curing, such as:
- Rapid thermal processing (RTP) for fast curing of adhesives
- Continuous roll-to-roll processing for high-volume production
- Automated adhesive application systems for improved consistency and reduced waste
FAQs
- What are the key differences between SAP and mSAP?
-
SAP is a polyimide-based adhesive used in flexible circuit fabrication to improve adhesion between the substrate and conductive layer. mSAP is an advanced version of SAP that has been modified with additional functional groups and additives to provide even better adhesion, flexibility, and durability.
-
Can SAP and mSAP be used with any flexible substrate material?
-
SAP and mSAP are compatible with a wide range of flexible substrate materials, including polyimide, polyester, and PET. However, the specific adhesive formulation may need to be optimized for the chosen substrate to ensure the best performance.
-
What are the most common application methods for SAP and mSAP?
-
The most common application methods for SAP and mSAP include screen printing, roller coating, spin coating, and spray coating. The choice of application method depends on factors such as the size of the substrate, the required coating uniformity, and the production volume.
-
How does the curing process work for SAP and mSAP?
-
After application, SAP and mSAP must be cured to fully cross-link the adhesive and achieve their final properties. Curing is typically done by exposing the adhesive to heat, either in an oven or using inline heating methods. The specific curing temperature and time will depend on the adhesive formulation and the substrate material.
-
What are some of the future trends in SAP and mSAP development?
- Future trends in SAP and mSAP development include advanced adhesive formulations with improved thermal stability, flexibility, and conductivity; the incorporation of nanomaterials for enhanced performance; the development of environmentally friendly adhesives; and the adoption of high-speed processing techniques for increased production efficiency.
Conclusion
Surface Attachment Promoter (SAP) and Modified Surface Attachment Promoter (mSAP) are essential components in the fabrication of flexible circuits. These polyimide-based adhesives provide strong adhesion between the flexible substrate and the conductive layer, ensuring the reliability and durability of the final product. mSAP offers even better performance compared to standard SAP, with improved adhesion, flexibility, and resistance to environmental factors.
As the demand for flexible electronics continues to grow, ongoing research and development efforts are focused on creating advanced adhesive formulations, incorporating nanomaterials, developing eco-friendly adhesives, and improving processing techniques. These advancements will enable the production of higher-performance flexible circuits for a wide range of applications, from consumer electronics to medical devices and aerospace systems.
By understanding the role of SAP and mSAP in flexible circuit fabrication and staying up-to-date with the latest trends and developments, engineers and manufacturers can design and produce cutting-edge flexible electronics that meet the evolving needs of their customers.
No responses yet