Introduction to RoHS and its Impact on the PCB Industry
The Restriction of Hazardous Substances (RoHS) directive is a set of regulations that aims to restrict the use of certain hazardous substances in electrical and electronic equipment (EEE). The directive was first introduced by the European Union (EU) in 2003 and has since been adopted by many countries worldwide. The primary goal of RoHS is to protect human health and the environment by reducing the use of harmful substances in EEE, including printed circuit boards (PCBs).
The PCB industry has been significantly impacted by the RoHS directive, as it has had to adapt its manufacturing processes and materials to comply with the regulations. In this article, we will explore the RoHS directive in detail, its impact on the PCB industry, and the challenges and opportunities it presents.
What is RoHS?
RoHS is a directive that restricts the use of six hazardous substances in EEE. These substances are:
- Lead (Pb)
- Mercury (Hg)
- Cadmium (Cd)
- Hexavalent Chromium (Cr6+)
- Polybrominated Biphenyls (PBB)
- Polybrominated Diphenyl Ethers (PBDE)
The directive applies to a wide range of EEE, including household appliances, IT and telecommunications equipment, consumer electronics, lighting equipment, electrical and electronic tools, toys, leisure and sports equipment, and automatic dispensers. PCBs, being an integral part of most EEE, are also subject to RoHS regulations.
RoHS Compliance Thresholds
The RoHS directive sets maximum concentration values (MCVs) for each of the six restricted substances. These MCVs are expressed in weight percentage and apply to homogeneous materials, which are defined as materials that cannot be mechanically disjointed into different materials. The MCVs for each substance are as follows:
Substance | Maximum Concentration Value (MCV) |
---|---|
Lead (Pb) | 0.1% |
Mercury (Hg) | 0.1% |
Cadmium (Cd) | 0.01% |
Hexavalent Chromium (Cr6+) | 0.1% |
Polybrominated Biphenyls (PBB) | 0.1% |
Polybrominated Diphenyl Ethers (PBDE) | 0.1% |
It is important to note that these MCVs apply to each homogeneous material within a product, not to the entire product itself. This means that if a single component of a PCB exceeds the MCV for any of the restricted substances, the entire PCB is considered non-RoHS compliant.
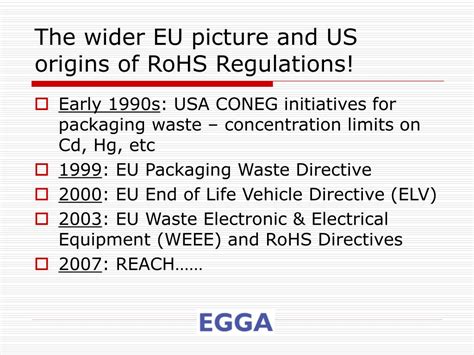
Impact of RoHS on the PCB Industry
The implementation of the RoHS directive has had a significant impact on the PCB industry, affecting various aspects of PCB Design, manufacturing, and assembly processes. Some of the key areas impacted by RoHS include:
Material Selection
One of the most significant challenges faced by the PCB industry in complying with RoHS regulations is the selection of appropriate materials. Traditionally, lead-based solders were widely used in PCB assembly due to their excellent wetting properties, low melting point, and good reliability. However, with the RoHS directive restricting the use of lead, the industry has had to transition to lead-free solders.
Lead-free solders, such as tin-silver-copper (SAC) alloys, have different properties compared to lead-based solders. They generally have higher melting points, which can lead to increased thermal stress on components during the soldering process. Additionally, lead-free solders may have inferior wetting properties, which can result in poor solder joint formation and reduced reliability.
To address these issues, PCB manufacturers have had to invest in research and development to identify suitable lead-free solder alloys and optimize their manufacturing processes accordingly. This has led to the development of various lead-free solder formulations, each with its own set of advantages and disadvantages.
Manufacturing Processes
The transition to RoHS-compliant materials has necessitated changes in PCB manufacturing processes. Some of the key changes include:
-
Higher soldering temperatures: Lead-free solders typically have higher melting points than lead-based solders, requiring higher soldering temperatures. This can lead to increased thermal stress on components and PCBs, potentially affecting their reliability.
-
Modified soldering profiles: To accommodate the higher melting points of lead-free solders, soldering profiles have had to be modified. This includes adjusting peak temperatures, preheat times, and cooling rates to ensure proper solder joint formation and minimize thermal stress.
-
Improved process control: RoHS compliance requires strict control over the manufacturing process to ensure that the MCVs for restricted substances are not exceeded. This has led to the implementation of more stringent process controls, including better monitoring and documentation of material composition and process parameters.
-
Equipment upgrades: The transition to lead-free soldering has required upgrades to manufacturing equipment, such as soldering machines and reflow ovens, to accommodate the higher temperatures and modified soldering profiles.
Supply Chain Management
RoHS compliance has also had a significant impact on supply chain management in the PCB industry. PCB manufacturers must ensure that all components and materials used in their products are RoHS-compliant. This requires close collaboration with suppliers to obtain material declarations and ensure that the supplied components meet the RoHS requirements.
Maintaining an RoHS-compliant supply chain can be challenging, particularly when dealing with a large number of suppliers and components. PCB manufacturers have had to implement strict supplier management processes, including regular audits and material testing, to ensure ongoing compliance.
Cost Implications
Complying with RoHS regulations has had cost implications for the PCB industry. The transition to RoHS-compliant materials and processes has required significant investments in research and development, equipment upgrades, and staff training. Additionally, the increased complexity of RoHS-compliant manufacturing processes and supply chain management has led to higher production costs.
However, it is essential to note that the long-term benefits of RoHS compliance, such as reduced environmental impact and improved human health, can outweigh the initial cost implications.
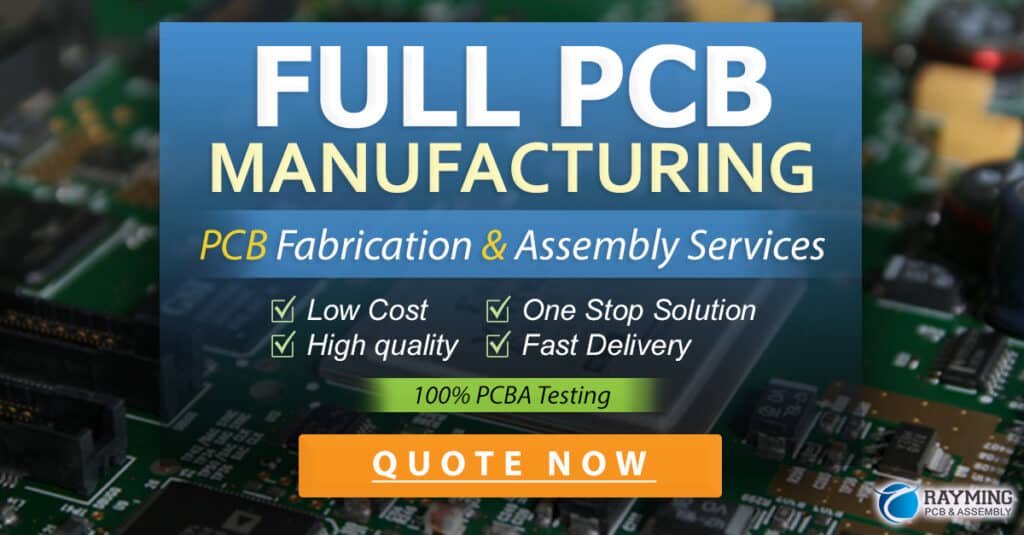
Challenges and Opportunities
While the RoHS directive has presented challenges for the PCB industry, it has also created opportunities for innovation and growth.
Challenges
-
Technical challenges: The transition to lead-free solders and RoHS-compliant materials has presented technical challenges, such as ensuring reliable solder joint formation and managing increased thermal stress on components.
-
Supply chain complexity: Maintaining an RoHS-compliant supply chain can be complex and time-consuming, requiring close collaboration with suppliers and regular material testing.
-
Cost implications: Complying with RoHS regulations has required significant investments in research and development, equipment upgrades, and staff training, leading to increased production costs.
Opportunities
-
Environmental and health benefits: By reducing the use of hazardous substances in EEE, the RoHS directive contributes to improved environmental and human health outcomes.
-
Innovation: The challenges presented by RoHS compliance have driven innovation in the PCB industry, leading to the development of new materials, processes, and technologies.
-
Market differentiation: Companies that successfully navigate the challenges of RoHS compliance can differentiate themselves in the market by offering environmentally friendly and compliant products.
-
Increased global harmonization: As more countries adopt RoHS-like regulations, the PCB industry has the opportunity to benefit from increased global harmonization of standards, which can streamline compliance efforts and reduce trade barriers.
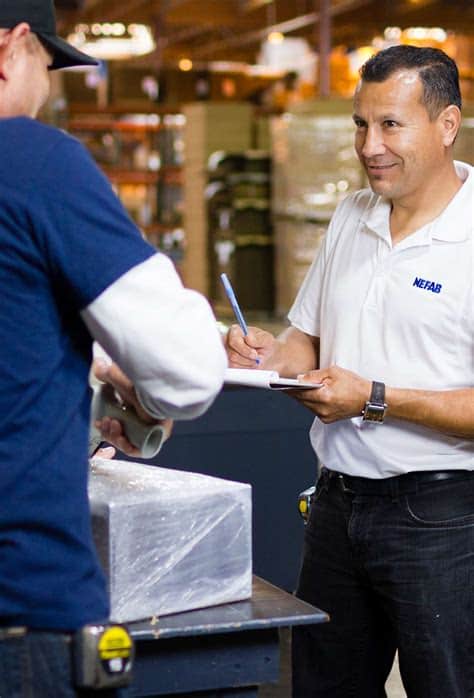
Frequently Asked Questions (FAQ)
-
What is the RoHS directive?
The RoHS (Restriction of Hazardous Substances) directive is a set of regulations that aims to restrict the use of certain hazardous substances in electrical and electronic equipment (EEE), including printed circuit boards (PCBs). -
Which substances are restricted under RoHS?
The six substances restricted under RoHS are lead (Pb), mercury (Hg), cadmium (Cd), hexavalent chromium (Cr6+), polybrominated biphenyls (PBB), and polybrominated diphenyl ethers (PBDE). -
What are the maximum concentration values (MCVs) for RoHS-restricted substances?
The MCVs for lead, mercury, hexavalent chromium, PBB, and PBDE are 0.1% by weight in homogeneous materials, while the MCV for cadmium is 0.01% by weight. -
How has the RoHS directive impacted the PCB industry?
The RoHS directive has significantly impacted the PCB industry by requiring changes in material selection, manufacturing processes, supply chain management, and increasing production costs. However, it has also driven innovation and created opportunities for environmentally friendly products. -
What are some of the challenges faced by the PCB industry in complying with RoHS?
Some of the challenges faced by the PCB industry in complying with RoHS include technical challenges related to lead-free soldering, supply chain complexity, and cost implications associated with the transition to RoHS-compliant materials and processes.
Conclusion
The RoHS directive has had a profound impact on the PCB industry, requiring significant changes in material selection, manufacturing processes, and supply chain management. While complying with RoHS regulations has presented challenges, it has also driven innovation and created opportunities for the development of environmentally friendly products.
As the global regulatory landscape continues to evolve, with more countries adopting RoHS-like regulations, the PCB industry must remain proactive in addressing the challenges and seizing the opportunities presented by these changes. By embracing RoHS compliance and prioritizing environmental and human health concerns, the PCB industry can contribute to a more sustainable future while remaining competitive in an increasingly regulated market.
No responses yet