Introduction to RoHS 2 and its Impact on PCB Manufacturing
The Restriction of Hazardous Substances Directive (RoHS) is a set of guidelines that aims to restrict the use of certain hazardous substances in electrical and electronic equipment (EEE). RoHS was first introduced in the European Union (EU) in 2002, and since then, it has undergone several revisions to keep up with the evolving technology and environmental concerns. The most recent version, RoHS 2 (Directive 2011/65/EU), came into effect on January 3, 2013, and has had a significant impact on the PCB manufacturing industry.
RoHS 2 compliance is crucial for PCB manufacturers who want to sell their products in the EU market. The directive restricts the use of ten hazardous substances in EEE, including lead (Pb), mercury (Hg), cadmium (Cd), hexavalent chromium (Cr6+), polybrominated biphenyls (PBB), polybrominated diphenyl ethers (PBDE), bis(2-ethylhexyl) phthalate (DEHP), butyl benzyl phthalate (BBP), dibutyl phthalate (DBP), and diisobutyl phthalate (DIBP).
The Importance of RoHS-Compliant PCBs
Producing RoHS-compliant PCBs is not only a legal requirement but also a responsible choice for the environment and human health. The hazardous substances restricted by RoHS 2 can have severe consequences if not properly managed:
-
Lead (Pb): Lead is a toxic metal that can cause damage to the nervous system, kidneys, and reproductive system. It is especially harmful to children and pregnant women.
-
Mercury (Hg): Mercury is a highly toxic element that can accumulate in the body and cause neurological disorders, kidney damage, and other health issues.
-
Cadmium (Cd): Cadmium is a carcinogenic metal that can cause kidney damage and bone disorders.
-
Hexavalent Chromium (Cr6+): Hexavalent chromium is a carcinogenic substance that can cause respiratory problems, skin irritation, and other health issues.
-
Polybrominated Biphenyls (PBB) and Polybrominated Diphenyl Ethers (PBDE): These are flame retardants that can accumulate in the environment and pose risks to human health and wildlife.
-
Phthalates (DEHP, BBP, DBP, DIBP): These substances are used as plasticizers and can have adverse effects on human health, particularly on the reproductive system.
By producing RoHS-compliant PCBs, manufacturers can contribute to a safer and more sustainable future while ensuring compliance with the EU regulations.
Steps to Produce RoHS 2 Compliant PCB Products
Producing RoHS 2 compliant PCB products requires a systematic approach that involves several key steps:
1. Material Selection
The first step in producing RoHS-compliant PCBs is to select materials that meet the RoHS 2 requirements. This includes choosing laminates, solder masks, and surface finishes that do not contain any of the ten restricted substances.
Some common RoHS-compliant materials used in PCB manufacturing include:
Material Category | RoHS-Compliant Options |
---|---|
Laminates | FR-4, Polyimide, Rogers materials |
Solder Masks | LPI (Liquid Photo Imageable), Dry Film |
Surface Finishes | ENIG (Electroless Nickel Immersion Gold), OSP (Organic Solderability Preservative), Immersion Silver, Immersion Tin |
It is essential to work with reliable suppliers who can provide RoHS-compliant materials and certifications to ensure the final product meets the directive’s requirements.
2. Design Considerations
When designing RoHS-compliant PCBs, several factors need to be considered to ensure the final product’s compliance and functionality:
a. Component Selection
Choose components that are RoHS-compliant and have been sourced from reliable suppliers. Verify the compliance status of each component and maintain proper documentation.
b. Design for Manufacturing (DFM)
Incorporate DFM principles to minimize the use of hazardous substances and facilitate the assembly process. This may include optimizing the PCB layout, choosing appropriate component packages, and defining proper spacing and clearances.
c. Thermal Management
Consider the thermal requirements of the PCB and design accordingly. RoHS-compliant PCBs may have different thermal properties compared to non-compliant boards, so it is essential to account for these differences during the design phase.
3. Manufacturing Process Control
To produce RoHS-compliant PCBs consistently, manufacturers must implement strict process controls and adhere to best practices:
a. Contamination Prevention
Implement measures to prevent cross-contamination between RoHS-compliant and non-compliant materials. This may include dedicated production lines, segregated storage areas, and proper cleaning procedures.
b. Process Parameter Optimization
Optimize the manufacturing process parameters to ensure the quality and reliability of RoHS-compliant PCBs. This may involve adjusting the temperature profiles, exposure times, and other process settings to accommodate the specific requirements of RoHS-compliant materials.
c. Training and Education
Provide adequate training and education to the workforce to ensure they understand the importance of RoHS compliance and follow the necessary procedures to maintain it.
4. Testing and Verification
To ensure RoHS 2 compliance, manufacturers must conduct thorough testing and verification at various stages of the production process:
a. Incoming Material Inspection
Test incoming materials to verify their RoHS compliance status. This may involve using X-ray fluorescence (XRF) analyzers, inductively coupled plasma (ICP) spectroscopy, or other analytical techniques.
b. In-Process Testing
Implement in-process testing to monitor the presence of hazardous substances throughout the manufacturing process. This may include periodic checks using XRF analyzers or other suitable methods.
c. Final Product Testing
Conduct final product testing to ensure the PCB meets the RoHS 2 requirements. This may involve destructive or non-destructive testing methods, such as XRF, ICP, or energy-dispersive X-ray spectroscopy (EDX).
5. Documentation and Certification
Maintaining proper documentation and obtaining the necessary certifications are crucial for demonstrating RoHS 2 compliance:
a. Material Declarations
Collect and maintain material declarations from suppliers for all the materials used in the PCB manufacturing process. These declarations should confirm the RoHS compliance status of each material.
b. Test Reports
Generate and maintain test reports that demonstrate the PCB’s compliance with RoHS 2 requirements. These reports should include details on the testing methods used, the results obtained, and any relevant standards or guidelines followed.
c. Certificates of Compliance (CoC)
Obtain Certificates of Compliance from suppliers and issue them to customers as required. A CoC is a formal document that attests to the RoHS compliance status of the PCB and its components.
Challenges in Producing RoHS-Compliant PCBs
While producing RoHS-compliant PCBs is essential for compliance and environmental sustainability, manufacturers may face several challenges during the process:
1. Sourcing Reliable Materials
Finding reliable suppliers who can consistently provide RoHS-compliant materials can be challenging. Manufacturers must conduct thorough due diligence and maintain strong relationships with their suppliers to ensure a steady supply of compliant materials.
2. Compatibility Issues
RoHS-compliant materials may have different properties compared to their non-compliant counterparts, which can lead to compatibility issues during the manufacturing process. Manufacturers must carefully evaluate the materials and optimize their processes to ensure the final product’s quality and reliability.
3. Cost Implications
Producing RoHS-compliant PCBs may involve higher costs due to the use of specialized materials, additional testing requirements, and process modifications. Manufacturers must find ways to balance these costs while maintaining competitive pricing for their customers.
4. Staying Updated with Regulations
RoHS regulations are subject to change, and manufacturers must stay informed about any updates or revisions to ensure ongoing compliance. This requires dedicated resources to monitor regulatory developments and adapt the manufacturing processes accordingly.
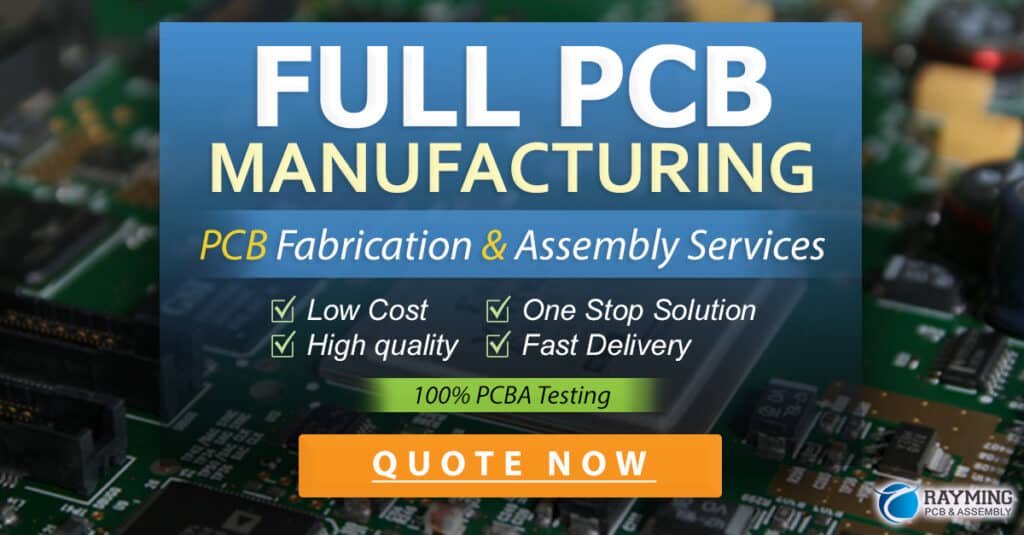
Best Practices for Maintaining RoHS 2 Compliance
To maintain RoHS 2 compliance and minimize the risk of non-compliance, PCB manufacturers should follow these best practices:
-
Establish a RoHS Compliance Policy: Develop a clear and comprehensive RoHS compliance policy that outlines the company’s commitment to meeting the directive’s requirements and the responsibilities of each department or function.
-
Conduct Regular Audits: Perform regular internal audits to assess the effectiveness of the RoHS compliance program and identify any areas for improvement. This may include reviewing material declarations, test reports, and manufacturing processes.
-
Engage with Stakeholders: Maintain open communication with suppliers, customers, and other stakeholders to ensure a shared understanding of RoHS requirements and expectations. This can help identify potential issues early and facilitate collaborative problem-solving.
-
Invest in Training and Education: Provide ongoing training and education to employees to keep them informed about RoHS requirements, best practices, and any updates to the regulations. This can help foster a culture of compliance and continuous improvement.
-
Continuously Monitor and Improve: Regularly review and assess the RoHS compliance program to identify opportunities for improvement. This may involve implementing new technologies, optimizing processes, or adopting industry best practices to enhance compliance and efficiency.
Frequently Asked Questions (FAQ)
-
What is RoHS 2, and how does it differ from the original RoHS directive?
RoHS 2 (Directive 2011/65/EU) is an updated version of the original RoHS directive (Directive 2002/95/EC). The main differences include an expanded scope to cover additional product categories, the inclusion of four phthalates as restricted substances, and more stringent compliance requirements for manufacturers. -
What are the ten substances restricted under RoHS 2?
The ten substances restricted under RoHS 2 are lead (Pb), mercury (Hg), cadmium (Cd), hexavalent chromium (Cr6+), polybrominated biphenyls (PBB), polybrominated diphenyl ethers (PBDE), bis(2-ethylhexyl) phthalate (DEHP), butyl benzyl phthalate (BBP), dibutyl phthalate (DBP), and diisobutyl phthalate (DIBP). -
How can PCB manufacturers ensure their products are RoHS 2 compliant?
PCB manufacturers can ensure RoHS 2 compliance by selecting RoHS-compliant materials, implementing strict process controls, conducting thorough testing and verification, and maintaining proper documentation and certifications. Engaging with reliable suppliers and staying updated with regulatory requirements are also crucial for maintaining compliance. -
What are the consequences of non-compliance with RoHS 2?
Non-compliance with RoHS 2 can result in significant legal and financial consequences, including fines, product recalls, and damage to the company’s reputation. In some cases, non-compliant products may be banned from the EU market, leading to loss of business opportunities. -
How can customers verify the RoHS 2 compliance status of a PCB product?
Customers can verify the RoHS 2 compliance status of a PCB product by requesting material declarations, test reports, and Certificates of Compliance from the manufacturer. These documents should provide evidence that the product meets the RoHS 2 requirements and has been manufactured using compliant materials and processes.
Conclusion
Producing RoHS 2 compliant PCB products is a critical responsibility for manufacturers who want to sell their products in the EU market and contribute to a more sustainable future. By following the steps outlined in this article, including material selection, design considerations, process control, testing, and documentation, manufacturers can ensure their PCBs meet the RoHS 2 requirements and minimize the risk of non-compliance.
However, producing RoHS-compliant PCBs is not without its challenges, such as sourcing reliable materials, addressing compatibility issues, managing costs, and staying updated with regulations. To overcome these challenges and maintain ongoing compliance, manufacturers should adopt best practices such as establishing a RoHS compliance policy, conducting regular audits, engaging with stakeholders, investing in training and education, and continuously monitoring and improving their processes.
By prioritizing RoHS 2 compliance and staying committed to environmental sustainability, PCB manufacturers can not only meet the legal requirements but also contribute to a safer and healthier future for all.
No responses yet