What is a Rogers PCB?
A Rogers PCB, also known as a high-frequency printed circuit board, is a specialized type of PCB that is designed to work with high-frequency signals. These PCBs are made using materials from Rogers Corporation, a leading manufacturer of high-performance materials for electronic applications.
Rogers PCBs are known for their excellent electrical properties, including low dielectric loss, high thermal conductivity, and stable performance over a wide range of frequencies. These properties make them ideal for use in applications such as:
- Wireless communication systems
- Radar and satellite systems
- Automotive electronics
- Medical devices
- Aerospace and defense systems
Advantages of Rogers PCBs
Compared to traditional FR-4 PCBs, Rogers PCBs offer several advantages:
-
Low Dielectric Loss: Rogers materials have a low dielectric constant and low loss tangent, which minimizes signal loss and ensures high-quality signal transmission.
-
High Thermal Conductivity: Rogers materials have excellent thermal conductivity, which helps dissipate heat efficiently and prevents overheating of electronic components.
-
Stable Performance: Rogers PCBs maintain stable performance over a wide range of frequencies and temperatures, ensuring reliable operation in demanding environments.
-
Improved Signal Integrity: The low dielectric loss and stable performance of Rogers PCBs help maintain signal integrity, reducing signal distortion and improving overall system performance.
Types of Rogers PCB Materials
Rogers Corporation offers a variety of materials for high-frequency PCBs, each with its own unique properties and benefits. Some of the most popular Rogers PCB materials include:
Rogers RO4000 Series
The RO4000 series is a popular choice for high-frequency applications. These materials offer a low dielectric constant, low loss tangent, and excellent thermal stability. They are ideal for applications such as:
- Wireless communication systems
- Automotive radar systems
- Satellite and aerospace systems
Property | RO4003C | RO4350B | RO4360G2 |
---|---|---|---|
Dielectric Constant (10 GHz) | 3.38 | 3.48 | 6.15 |
Dissipation Factor (10 GHz) | 0.0027 | 0.0037 | 0.0038 |
Thermal Conductivity (W/m/K) | 0.71 | 0.62 | 0.66 |
Rogers RT/duroid Series
The RT/duroid series is another popular choice for high-frequency applications. These materials offer excellent electrical properties, including low dielectric loss and stable performance over a wide range of frequencies. They are ideal for applications such as:
- Wireless communication systems
- Radar and satellite systems
- Aerospace and defense systems
Property | RT/duroid 5870 | RT/duroid 5880 | RT/duroid 6002 |
---|---|---|---|
Dielectric Constant (10 GHz) | 2.33 | 2.20 | 2.94 |
Dissipation Factor (10 GHz) | 0.0012 | 0.0009 | 0.0012 |
Thermal Conductivity (W/m/K) | 0.26 | 0.20 | 0.60 |
Rogers CLTE Series
The CLTE series is designed for applications that require a low coefficient of thermal expansion (CTE). These materials have a CTE that closely matches that of copper, reducing stress and
improving reliability in high-temperature environments. They are ideal for applications such as:
- Automotive electronics
- Power amplifiers
- High-power RF applications
Property | RO3003 | RO3006 | RO3010 |
---|---|---|---|
Dielectric Constant (10 GHz) | 3.00 | 6.15 | 10.2 |
Dissipation Factor (10 GHz) | 0.0013 | 0.0020 | 0.0023 |
Thermal Conductivity (W/m/K) | 0.50 | 0.61 | 0.66 |
Designing with Rogers PCBs
When designing with Rogers PCBs, there are several factors to consider to ensure optimal performance and reliability:
Material Selection
Choosing the right Rogers material for your application is crucial. Consider factors such as the operating frequency, dielectric constant, loss tangent, and thermal conductivity when selecting a material.
Impedance Matching
Proper impedance matching is essential for minimizing signal reflections and ensuring efficient power transfer. Use a PCB design software with built-in impedance calculation tools to accurately design your high-frequency traces.
Grounding and Shielding
Effective grounding and shielding techniques are critical for minimizing electromagnetic interference (EMI) and ensuring signal integrity. Use techniques such as ground planes, via stitching, and shielding to reduce EMI and maintain signal quality.
Thermal Management
Rogers PCBs often dissipate significant amounts of heat due to their high-frequency operation. Proper thermal management is essential for preventing overheating and ensuring reliable performance. Use techniques such as thermal vias, heat sinks, and active cooling to effectively dissipate heat.
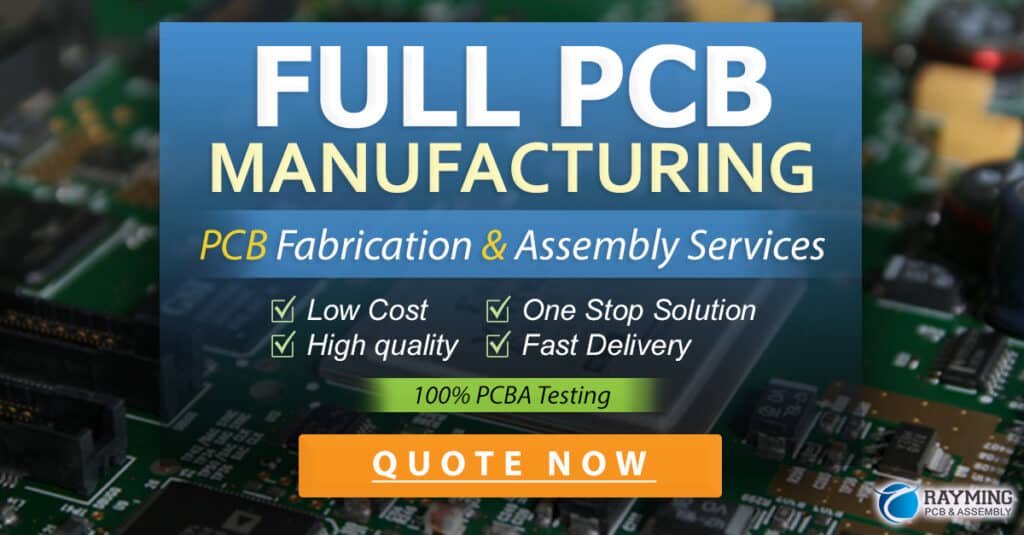
Manufacturing Rogers PCBs
Manufacturing Rogers PCBs requires specialized equipment and expertise due to the unique properties of Rogers materials. Some key considerations for manufacturing Rogers PCBs include:
Material Handling
Rogers materials require careful handling to prevent damage and ensure optimal performance. Manufacturers must follow strict guidelines for storage, handling, and processing to maintain the integrity of the materials.
Drilling and Routing
Drilling and routing Rogers PCBs requires specialized equipment and techniques to prevent delamination and ensure clean, accurate holes and edges. Manufacturers must use high-quality carbide drill bits and optimize their drilling parameters for each specific Rogers material.
Lamination
Laminating Rogers PCBs requires precise temperature and pressure control to ensure proper bonding and prevent warping or delamination. Manufacturers must follow the recommended lamination profiles for each Rogers material to achieve optimal results.
Plating and Finishing
Plating and finishing Rogers PCBs requires careful process control to ensure good adhesion and prevent damage to the material. Manufacturers must use compatible plating and finishing processes that do not degrade the electrical or mechanical properties of the Rogers material.
Frequently Asked Questions (FAQ)
-
Q: What are the main advantages of using Rogers PCBs over traditional FR-4 PCBs?
A: Rogers PCBs offer several advantages over traditional FR-4 PCBs, including lower dielectric loss, higher thermal conductivity, and more stable performance over a wide range of frequencies and temperatures. These properties make Rogers PCBs ideal for high-frequency applications that require superior signal integrity and reliability. -
Q: Can I use standard PCB design software to design Rogers PCBs?
A: Yes, most standard PCB design software packages can be used to design Rogers PCBs. However, it is important to use software with built-in impedance calculation tools and to follow best practices for high-frequency design, such as proper grounding, shielding, and thermal management. -
Q: Are Rogers PCBs more expensive than traditional FR-4 PCBs?
A: Yes, Rogers PCBs are generally more expensive than traditional FR-4 PCBs due to the specialized materials and manufacturing processes required. However, the superior performance and reliability of Rogers PCBs often justify the higher cost for high-frequency applications. -
Q: Can Rogers PCBs be manufactured using the same equipment as traditional PCBs?
A: Manufacturing Rogers PCBs requires specialized equipment and expertise due to the unique properties of Rogers materials. While some standard PCB manufacturing equipment can be used, additional equipment and process controls are often necessary to ensure optimal results. -
Q: What should I consider when selecting a Rogers PCB material for my application?
A: When selecting a Rogers PCB material, consider factors such as the operating frequency, dielectric constant, loss tangent, and thermal conductivity. Each Rogers material has its own unique properties and benefits, so it is important to choose a material that is well-suited for your specific application requirements.
Conclusion
Rogers PCBs are a specialized type of high-frequency PCB that offer superior performance and reliability compared to traditional FR-4 PCBs. With their low dielectric loss, high thermal conductivity, and stable performance over a wide range of frequencies and temperatures, Rogers PCBs are ideal for demanding applications such as wireless communication systems, radar and satellite systems, automotive electronics, medical devices, and aerospace and defense systems.
When designing with Rogers PCBs, it is important to choose the right material for your application, follow best practices for high-frequency design, and work with a manufacturer that has the specialized equipment and expertise necessary to produce high-quality Rogers PCBs.
By understanding the unique properties and benefits of Rogers PCBs, as well as the key considerations for design and manufacturing, you can ensure that your high-frequency electronic systems deliver optimal performance and reliability.
No responses yet