Introduction to Rigid-Flex PCB and Flexible PCB
In the world of printed circuit boards (PCBs), there are various types designed to cater to different applications and requirements. Two notable types are Rigid-Flex PCBs and Flexible PCBs. While both offer flexibility, they have distinct characteristics that set them apart. This article will delve into the differences between Rigid-Flex PCBs and Flexible PCBs, their advantages, applications, and design considerations.
What is a Rigid-Flex PCB?
A Rigid-Flex PCB is a hybrid circuit board that combines rigid and flexible substrates. It consists of multiple layers of flexible PCB substrate, such as polyimide, which are bonded together with rigid PCB layers. The rigid portions provide structural support and house components, while the flexible portions allow for bending and folding, enabling three-dimensional packaging and improved connectivity between rigid sections.
What is a Flexible PCB?
A Flexible PCB, also known as a flex circuit, is a type of PCB that is made entirely of flexible materials, such as polyimide or polyester. Unlike rigid PCBs, Flexible PCBs can bend, twist, and conform to various shapes. They are lightweight, thin, and highly durable, making them ideal for applications that require flexibility and space savings.
Advantages of Rigid-Flex PCBs
Rigid-Flex PCBs offer several advantages over traditional rigid PCBs and Flexible PCBs. Here are some key benefits:
-
Space Savings: Rigid-Flex PCBs allow for three-dimensional packaging, enabling designers to utilize available space more efficiently. By folding and bending the flexible portions, components can be placed closer together, resulting in more compact designs.
-
Improved Reliability: The combination of rigid and flexible layers in Rigid-Flex PCBs provides enhanced reliability compared to separate rigid and flexible circuits. The integrated design eliminates the need for connectors and cables between rigid sections, reducing the risk of connection failures and signal integrity issues.
-
Reduced Weight: Rigid-Flex PCBs eliminate the need for additional connectors and wiring, resulting in overall weight reduction. This is particularly beneficial in applications where weight is a critical factor, such as aerospace and portable devices.
-
Enhanced Durability: The flexible portions of Rigid-Flex PCBs are designed to withstand repeated bending and flexing without compromising the integrity of the circuit. This durability makes them suitable for applications that require frequent movement or are subject to vibrations and shocks.
-
Simplified Assembly: Rigid-Flex PCBs streamline the assembly process by reducing the number of interconnects and connectors required. This simplification leads to faster assembly times, lower manufacturing costs, and improved overall reliability.
Advantages of Flexible PCBs
Flexible PCBs offer their own set of advantages, making them suitable for specific applications. Here are some benefits of Flexible PCBs:
-
Extreme Flexibility: Flexible PCBs are highly flexible and can bend, twist, and conform to various shapes. This flexibility allows them to be used in applications where the PCB needs to fit into tight spaces or follow curved surfaces.
-
Lightweight and Thin: Flexible PCBs are typically thinner and lighter than rigid PCBs. This makes them ideal for weight-sensitive applications, such as wearable devices, where every gram counts.
-
High Durability: Flexible PCBs are designed to withstand repeated bending and flexing without breaking or losing functionality. They can endure harsh environments, vibrations, and shocks, making them suitable for applications that require ruggedness.
-
Dynamic Flexing: Unlike Rigid-Flex PCBs, which have specific flexible zones, Flexible PCBs can flex along their entire length. This dynamic flexing capability allows for more freedom in design and enables unique form factors.
-
Cost-Effective for Simple Designs: For simpler designs that don’t require the complexity of Rigid-Flex PCBs, Flexible PCBs can be a cost-effective solution. They are easier to manufacture and assemble compared to Rigid-Flex PCBs.
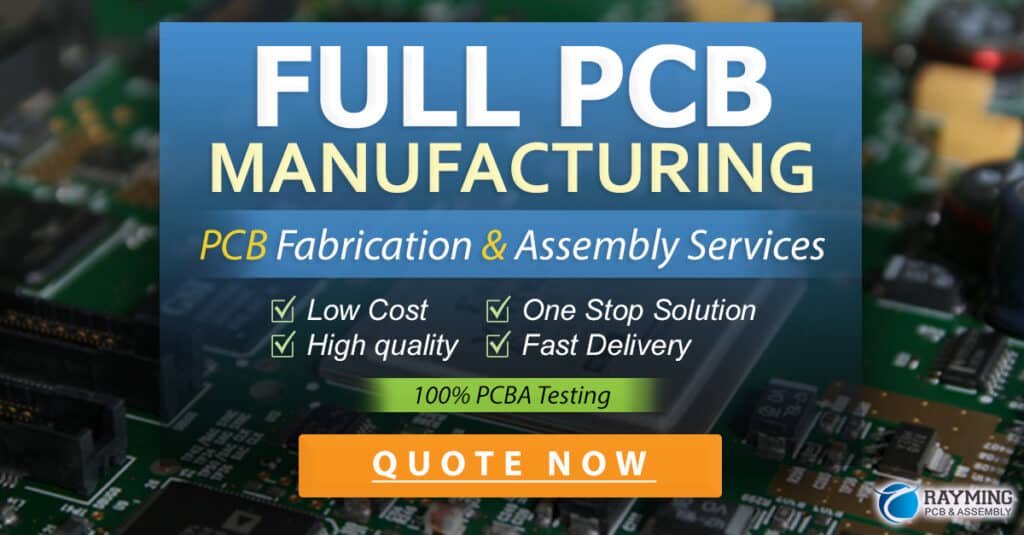
Applications of Rigid-Flex PCBs
Rigid-Flex PCBs find applications in various industries where space savings, reliability, and flexibility are critical. Some common applications include:
-
Aerospace and Defense: Rigid-Flex PCBs are extensively used in aerospace and defense applications due to their ability to withstand harsh environments, reduce weight, and provide reliable performance. They are used in avionics systems, satellites, missiles, and other military equipment.
-
Medical Devices: Rigid-Flex PCBs are employed in medical devices that require compact packaging and reliable functioning. They are used in implantable devices, surgical instruments, diagnostic equipment, and wearable medical devices.
-
Automotive Electronics: The automotive industry utilizes Rigid-Flex PCBs in various electronic systems, such as engine control units, infotainment systems, and advanced driver assistance systems (ADAS). The flexibility and reliability of Rigid-Flex PCBs make them suitable for the demanding automotive environment.
-
Consumer Electronics: Rigid-Flex PCBs are used in consumer electronics devices, such as smartphones, tablets, laptops, and wearables. They enable compact designs, improved connectivity, and enhanced durability in these portable devices.
-
Industrial Automation: Rigid-Flex PCBs are employed in industrial automation systems, including robotics, machine control, and data acquisition systems. Their ability to withstand harsh environments and provide reliable connectivity makes them suitable for industrial applications.
Applications of Flexible PCBs
Flexible PCBs have a wide range of applications across different industries. Some common applications include:
-
Wearable Devices: Flexible PCBs are extensively used in wearable devices, such as fitness trackers, smartwatches, and medical monitoring devices. Their flexibility allows them to conform to the contours of the human body, providing comfort and enabling compact designs.
-
Consumer Electronics: Flexible PCBs are used in various consumer electronics devices, such as digital cameras, mobile phones, and portable audio devices. They enable slim and lightweight designs while providing the necessary connectivity.
-
Medical Devices: Flexible PCBs find applications in medical devices that require flexibility and biocompatibility. They are used in Medical sensors, catheter systems, and implantable devices.
-
Automotive Electronics: Flexible PCBs are employed in automotive applications where flexibility and space savings are essential. They are used in instrument clusters, sensors, and wiring harnesses.
-
Aerospace and Defense: Flexible PCBs are utilized in aerospace and defense applications that require lightweight and flexible solutions. They are used in aircraft wiring, satellite systems, and military communication devices.
Design Considerations for Rigid-Flex PCBs
Designing Rigid-Flex PCBs requires careful consideration of several factors to ensure optimal performance and reliability. Here are some key design considerations:
-
Layer Stack-up: The layer stack-up of a Rigid-Flex PCB is crucial for its functionality and reliability. Designers need to determine the number of layers, the placement of rigid and flexible sections, and the material selection for each layer.
-
Bend Radius: The bend radius is a critical parameter in Rigid-Flex PCB design. It determines the minimum radius at which the flexible portion can be bent without causing damage or affecting the circuit’s performance. Designers must adhere to the recommended bend radius provided by the manufacturer.
-
Copper Thickness: The thickness of the copper traces in the flexible portions should be carefully selected to ensure flexibility and reliability. Thinner copper traces are more flexible but may have limitations in current carrying capacity.
-
Coverlay and Stiffeners: Coverlay is a protective layer applied over the flexible portions to provide insulation and mechanical protection. Stiffeners are used to reinforce specific areas of the flexible circuit, such as connector locations or component mounting areas.
-
Component Placement: The placement of components on Rigid-Flex PCBs requires careful consideration. Components should be placed on the rigid portions whenever possible to avoid stress on the flexible sections during bending.
-
Signal Integrity: Signal integrity is a critical aspect of Rigid-Flex PCB design. Designers must ensure that the signal paths are optimized to minimize crosstalk, electromagnetic interference (EMI), and signal reflections.
-
Manufacturing Constraints: Rigid-Flex PCBs have specific manufacturing constraints that need to be considered during the design phase. Designers should work closely with the manufacturer to ensure that the design is manufacturable and meets the required specifications.
Design Considerations for Flexible PCBs
Designing Flexible PCBs requires attention to several key factors to ensure reliability and performance. Here are some design considerations for Flexible PCBs:
-
Material Selection: The choice of materials for Flexible PCBs is crucial. Common materials include polyimide, polyester, and adhesives. Designers need to select materials that offer the required flexibility, durability, and electrical properties for the specific application.
-
Copper Thickness: Similar to Rigid-Flex PCBs, the thickness of the copper traces in Flexible PCBs should be carefully selected. Thinner copper traces provide better flexibility but may have limitations in current carrying capacity.
-
Bend Radius: The bend radius is a critical parameter in Flexible PCB design. Designers must ensure that the bend radius is within the acceptable range to prevent damage to the copper traces and maintain the circuit’s integrity.
-
Coverlay and Stiffeners: Coverlay is used to provide insulation and mechanical protection to the Flexible PCB. Stiffeners can be added to specific areas to improve the mechanical stability and durability of the circuit.
-
Component Placement: Component placement on Flexible PCBs requires careful consideration. Components should be placed in a way that minimizes stress on the flexible substrate during bending and movement.
-
Strain Relief: Strain relief features, such as anchor points or reinforced areas, should be incorporated into the Flexible PCB design to prevent damage caused by excessive bending or stretching.
-
Manufacturing Constraints: Flexible PCBs have specific manufacturing constraints that need to be taken into account during the design phase. Designers should collaborate with the manufacturer to ensure that the design is manufacturable and meets the required specifications.
Frequently Asked Questions (FAQ)
-
Q: What is the main difference between Rigid-Flex PCBs and Flexible PCBs?
A: The main difference between Rigid-Flex PCBs and Flexible PCBs is that Rigid-Flex PCBs combine rigid and flexible substrates, while Flexible PCBs are made entirely of flexible materials. Rigid-Flex PCBs have specific flexible zones, whereas Flexible PCBs can flex along their entire length. -
Q: When should I choose a Rigid-Flex PCB over a Flexible PCB?
A: Rigid-Flex PCBs are preferred when the design requires a combination of structural support, three-dimensional packaging, and improved connectivity between rigid sections. They are suitable for applications that demand space savings, reliability, and durability. Flexible PCBs are chosen when extreme flexibility and conformity to various shapes are the primary requirements. -
Q: Are Rigid-Flex PCBs more expensive than Flexible PCBs?
A: Yes, Rigid-Flex PCBs are generally more expensive than Flexible PCBs due to their complex manufacturing process and the combination of rigid and flexible materials. Flexible PCBs are more cost-effective for simpler designs that don’t require the added complexity of Rigid-Flex PCBs. -
Q: Can Rigid-Flex PCBs be used in harsh environments?
A: Yes, Rigid-Flex PCBs are designed to withstand harsh environments, including extreme temperatures, vibrations, and shocks. They are commonly used in aerospace, defense, and automotive applications where reliability and durability are critical. -
Q: What are the common challenges in designing Rigid-Flex PCBs?
A: Designing Rigid-Flex PCBs comes with challenges such as determining the optimal layer stack-up, ensuring proper bend radius, managing signal integrity, and adhering to manufacturing constraints. Designers need to carefully consider these factors to ensure the functionality and reliability of the Rigid-Flex PCB.
Conclusion
Rigid-Flex PCBs and Flexible PCBs are two distinct types of printed circuit boards that offer unique advantages and cater to different application requirements. Rigid-Flex PCBs combine the benefits of rigid and flexible substrates, enabling space savings, improved reliability, and three-dimensional packaging. They are widely used in industries such as aerospace, defense, medical devices, automotive electronics, and consumer electronics.
On the other hand, Flexible PCBs offer extreme flexibility, lightweight construction, and the ability to conform to various shapes. They are commonly employed in wearable devices, consumer electronics, medical devices, and applications that require dynamic flexing.
When deciding between Rigid-Flex PCBs and Flexible PCBs, designers need to consider factors such as the application requirements, space constraints, reliability needs, and cost implications. Careful design considerations, including material selection, bend radius, component placement, and manufacturing constraints, are essential for both types of PCBs to ensure optimal performance and reliability.
As technology continues to advance, the demand for Rigid-Flex PCBs and Flexible PCBs is expected to grow, driven by the increasing complexity and miniaturization of electronic devices. Understanding the differences, advantages, and design considerations of these PCB types will enable engineers and designers to make informed decisions and create innovative solutions for a wide range of applications.
Feature | Rigid-Flex PCB | Flexible PCB |
---|---|---|
Substrate | Combination of rigid and flexible materials | Entirely flexible materials |
Flexibility | Specific flexible zones | Flexible along the entire length |
Structural Support | Provided by rigid portions | Limited structural support |
Three-Dimensional Packaging | Enables compact and efficient packaging | Limited three-dimensional packaging capability |
Reliability | Enhanced reliability due to integrated design | Reliable for applications requiring flexibility |
Weight | Reduced weight compared to separate rigid and flexible circuits | Lightweight and thin |
Durability | Designed to withstand repeated bending and flexing | High durability and ability to withstand dynamic flexing |
Cost | Generally more expensive due to complex manufacturing process | Cost-effective for simpler designs |
Table 1: Comparison of key features between Rigid-Flex PCBs and Flexible PCBs.
In summary, Rigid-Flex PCBs and Flexible PCBs offer distinct advantages and are suited for different application requirements. Rigid-Flex PCBs provide a combination of structural support, improved reliability, and three-dimensional packaging, making them ideal for space-constrained and high-reliability applications. Flexible PCBs, on the other hand, offer extreme flexibility, lightweight construction, and the ability to conform to various shapes, making them suitable for applications that require dynamic flexing and compact designs.
Designers must carefully evaluate the specific requirements of their application and consider factors such as flexibility, reliability, space constraints, and cost when choosing between Rigid-Flex PCBs and Flexible PCBs. By understanding the differences and design considerations of these PCB types, engineers can make informed decisions and create innovative solutions that meet the evolving demands of modern electronics.
No responses yet