Introduction to Rigid-Flex PCBs
Rigid-flex PCBs are a unique combination of rigid and flexible printed circuit boards that offer numerous advantages over traditional PCBs. They consist of multiple layers of flexible and rigid substrates laminated together, allowing for three-dimensional packaging and improved electrical performance. Rigid-flex PCBs are widely used in applications that require high reliability, such as aerospace, military, and medical devices.
Advantages of Rigid-Flex PCBs
- Space savings: Rigid-flex PCBs allow for more compact packaging, as they can be folded and bent to fit into tight spaces.
- Improved reliability: The elimination of connectors and wires between rigid and flexible sections reduces the risk of mechanical failures and improves overall reliability.
- Enhanced electrical performance: Rigid-flex PCBs minimize signal loss and interference by reducing the number of interconnects and providing shorter signal paths.
- Reduced assembly costs: The integration of rigid and flexible sections reduces the number of components and simplifies the assembly process, leading to lower assembly costs.
- Increased design flexibility: Rigid-flex PCBs offer greater design freedom, allowing for unique shapes and configurations that are not possible with traditional PCBs.
Factors Affecting Rigid-Flex PCB Costs
Several factors contribute to the cost of rigid-flex PCBs, including:
- Material selection
- Layer count and thickness
- Size and complexity of the design
- Quantity ordered
- Manufacturing process and lead time
Material Selection
The choice of materials used in rigid-flex PCBs has a significant impact on the overall cost. The most common materials used for the flexible layers are polyimide (PI) and polyethylene terephthalate (PET). PI is more expensive than PET but offers better thermal stability and mechanical properties. For the rigid layers, standard FR-4 material is typically used.
Layer Count and Thickness
The number of layers and their thickness also affect the cost of rigid-flex PCBs. As the layer count increases, so does the cost, due to the added complexity of the manufacturing process. Thicker layers also contribute to higher costs, as they require more material and processing time.
Size and Complexity of the Design
The size and complexity of the rigid-flex PCB design play a crucial role in determining the cost. Larger designs require more material and processing time, resulting in higher costs. Complex designs with intricate routing, tight tolerances, and multiple bend regions also increase the manufacturing costs.
Quantity Ordered
As with most manufacturing processes, the quantity of rigid-flex PCBs ordered has a significant impact on the cost per unit. Higher quantities benefit from economies of scale, as the fixed costs associated with setup and tooling are spread across more units, resulting in lower prices per PCB.
Manufacturing Process and Lead Time
The manufacturing process for rigid-flex PCBs is more complex and time-consuming than that of standard rigid PCBs. This increased complexity contributes to higher costs and longer lead times. Rush orders or expedited manufacturing services will also result in higher costs.
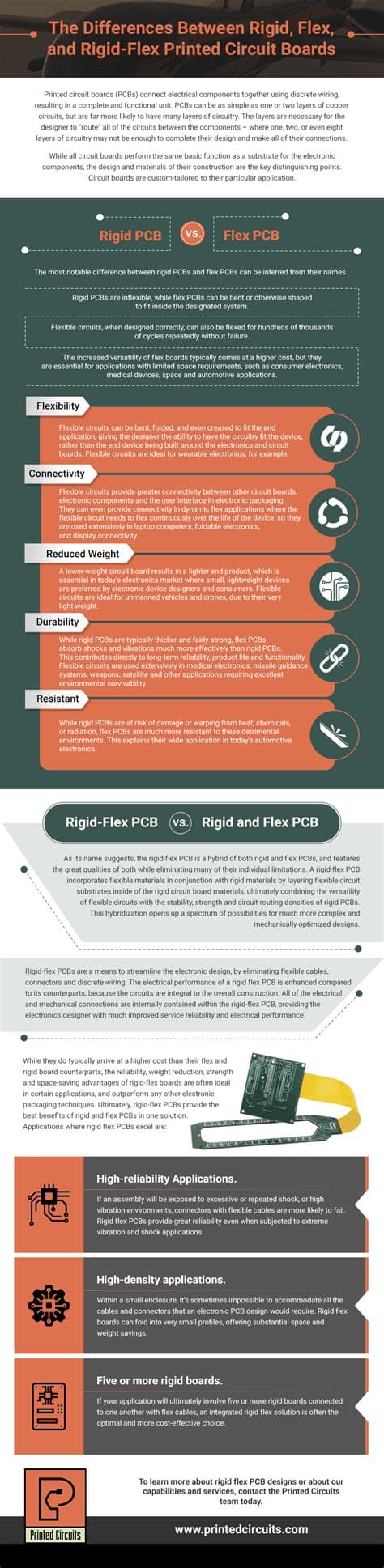
Cost Comparison: Rigid-Flex vs. Traditional PCBs
To illustrate the cost difference between rigid-flex and traditional PCBs, consider the following example:
PCB Type | Layer Count | Size (mm) | Quantity | Lead Time (days) | Cost per Unit |
---|---|---|---|---|---|
Traditional Rigid | 4 | 100 x 100 | 100 | 10 | $10 |
Rigid-Flex | 4 (2 rigid, 2 flex) | 100 x 100 | 100 | 20 | $25 |
In this example, the rigid-flex PCB costs 2.5 times more than the traditional rigid PCB, due to the added complexity of the manufacturing process and the use of flexible materials. However, the benefits of using a rigid-flex PCB, such as space savings, improved reliability, and enhanced electrical performance, can often justify the higher cost in applications that require these features.
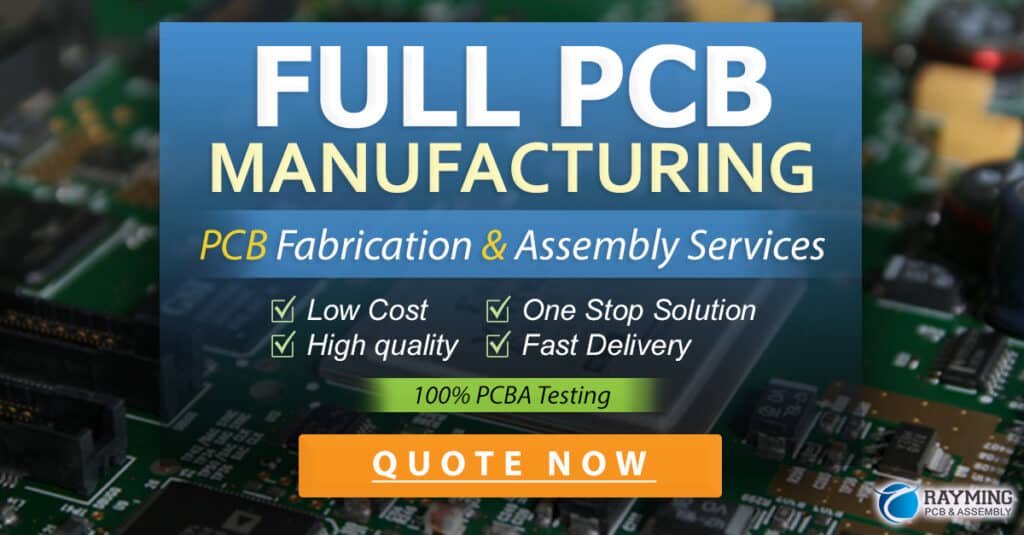
Cost Optimization Strategies for Rigid-Flex PCBs
To minimize the cost of rigid-flex PCBs, consider the following strategies:
- Simplify the design: Minimize the number of layers, reduce the complexity of routing, and optimize the placement of components to simplify the manufacturing process.
- Use standard materials: Whenever possible, use standard materials such as FR-4 for the rigid layers and polyimide for the flexible layers to avoid the added cost of custom materials.
- Minimize the number of bend regions: Each bend region adds complexity to the manufacturing process, so minimizing the number of bends can help reduce costs.
- Opt for larger quantities: Ordering larger quantities of rigid-flex PCBs can result in lower costs per unit, as the fixed costs are spread across more units.
- Plan ahead for longer lead times: Rigid-flex PCBs require longer lead times compared to traditional PCBs, so planning ahead and allowing for sufficient manufacturing time can help avoid rush fees and expedited services.
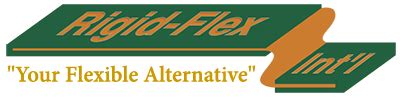
Future Trends in Rigid-Flex PCB Technology
As technology advances, the demand for more compact, reliable, and high-performance electronic devices will continue to drive the development of rigid-flex PCBs. Some of the future trends in rigid-flex PCB technology include:
- Increased use of high-density interconnect (HDI) technology: HDI allows for finer pitch and smaller via sizes, enabling even more compact designs and improved electrical performance.
- Adoption of advanced materials: New materials, such as liquid crystal polymer (LCP) and polytetrafluoroethylene (PTFE), offer superior thermal stability, low dielectric constant, and low loss, making them ideal for high-frequency applications.
- Integration of embedded components: Embedding active and passive components within the layers of a rigid-flex PCB can further reduce the size and improve the performance of electronic devices.
- Growth in the use of 3D printing technology: 3D printing technology can potentially revolutionize the manufacturing process of rigid-flex PCBs, enabling faster prototyping and more complex designs.
Frequently Asked Questions (FAQ)
-
Q: What is the typical lead time for rigid-flex PCBs?
A: The lead time for rigid-flex PCBs is usually longer than that of traditional rigid PCBs, ranging from 3 to 6 weeks, depending on the complexity of the design and the manufacturer’s capacity. -
Q: Can rigid-flex PCBs be used in high-temperature environments?
A: Yes, rigid-flex PCBs can be designed to withstand high temperatures by using appropriate materials, such as polyimide, which has a high glass transition temperature and excellent thermal stability. -
Q: Are rigid-flex PCBs more durable than traditional PCBs?
A: Yes, rigid-flex PCBs are generally more durable than traditional PCBs, as they eliminate the need for connectors and wires between rigid and flexible sections, reducing the risk of mechanical failures. -
Q: Can rigid-flex PCBs be reworked or repaired?
A: Reworking or repairing rigid-flex PCBs can be challenging due to the complexity of the design and the presence of flexible layers. However, skilled technicians with the proper equipment can perform repairs when necessary. -
Q: Are there any limitations to the number of layers in a rigid-flex PCB?
A: While there is no inherent limitation to the number of layers in a rigid-flex PCB, the cost and complexity of the manufacturing process increase significantly with higher layer counts. Most rigid-flex PCBs have between 4 and 12 layers, with some high-end designs featuring up to 20 layers.
Conclusion
Rigid-flex PCBs offer numerous advantages over traditional PCBs, including space savings, improved reliability, enhanced electrical performance, and increased design flexibility. However, these benefits come at a higher cost compared to standard rigid PCBs, due to the added complexity of the manufacturing process and the use of specialized materials.
Understanding the factors that affect the cost of rigid-flex PCBs, such as material selection, layer count, design complexity, quantity, and lead time, can help designers and managers make informed decisions when considering the use of rigid-flex technology in their products. By implementing cost optimization strategies and staying informed about future trends in rigid-flex PCB technology, companies can leverage the benefits of this innovative approach to PCB design while managing costs effectively.
As the demand for more compact, reliable, and high-performance electronic devices continues to grow, rigid-flex PCBs will play an increasingly important role in enabling the next generation of products across various industries, from consumer electronics to aerospace and medical devices.
No responses yet