Introduction to 6 Layer PCBs and Power Delivery
Six-layer printed circuit boards (PCBs) have become increasingly popular in the electronics industry due to their ability to provide a balance between cost and performance. These boards offer more routing space and better signal integrity compared to four-layer boards, while still being more affordable than eight-layer or higher layer count boards. In this article, we will explore the insights of Rick Hartley, a renowned PCB design expert, on the topic of 6-layer boards and power delivery.
The Advantages of 6 Layer PCBs
- Increased routing space
- Improved signal integrity
- Better power delivery
- Cost-effective solution
The Importance of Proper Power Delivery
Power delivery is a critical aspect of PCB design, as it ensures that all components on the board receive the necessary power to function correctly. Poor power delivery can lead to signal integrity issues, electromagnetic interference (EMI), and even component failure. In 6-layer boards, proper power delivery is even more crucial due to the increased complexity and density of the design.
Key Factors in Power Delivery Design
- Power plane placement
- Decoupling capacitor selection and placement
- Via sizing and placement
- Current density analysis
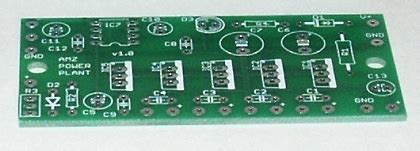
Rick Hartley’s Recommendations for 6 Layer PCB Design
1. Layer Stack-up
A typical 6-layer PCB stack-up consists of the following layers:
Layer | Purpose |
---|---|
Top | Signal |
Inner 1 | Ground Plane |
Inner 2 | Signal |
Inner 3 | Power Plane |
Inner 4 | Signal |
Bottom | Signal |
Rick Hartley emphasizes the importance of placing the ground plane on the layer adjacent to the top layer to provide a low-impedance return path for high-speed signals. The power plane should be placed on the inner layer closest to the bottom layer to minimize the distance between the power plane and the ground plane, reducing the inductance of the power delivery network.
2. Decoupling Capacitors
Decoupling capacitors play a critical role in maintaining power integrity on a PCB. They provide a local source of charge to the components, reducing the voltage ripple and minimizing the effect of transient currents on the power supply. Rick Hartley recommends the following guidelines for decoupling capacitor selection and placement:
- Use a combination of bulk, ceramic, and low-ESR capacitors to cover different frequency ranges
- Place decoupling capacitors as close as possible to the power pins of the components
- Use multiple small-value capacitors in parallel instead of a single large-value capacitor
- Minimize the loop area between the capacitor and the power/ground planes
3. Via Placement and Sizing
Vias are essential for connecting different layers of a PCB, but they can also introduce discontinuities in the signal path and affect the power delivery network. Rick Hartley suggests the following best practices for via placement and sizing:
- Use the smallest via size possible to minimize the inductance and capacitance
- Place vias close to the power pins of the components to reduce the loop area
- Avoid placing vias in the middle of the power plane to minimize the disruption of the current flow
- Use via stitching to connect the ground planes on different layers, creating a low-impedance return path
4. Current Density Analysis
Current density analysis is a technique used to evaluate the current-carrying capacity of the traces and planes on a PCB. It helps identify areas of the board that may be susceptible to thermal issues or voltage drop. Rick Hartley recommends performing current density analysis during the design phase to ensure that the PCB can handle the expected current loads without exceeding the maximum allowable temperature rise or voltage drop.
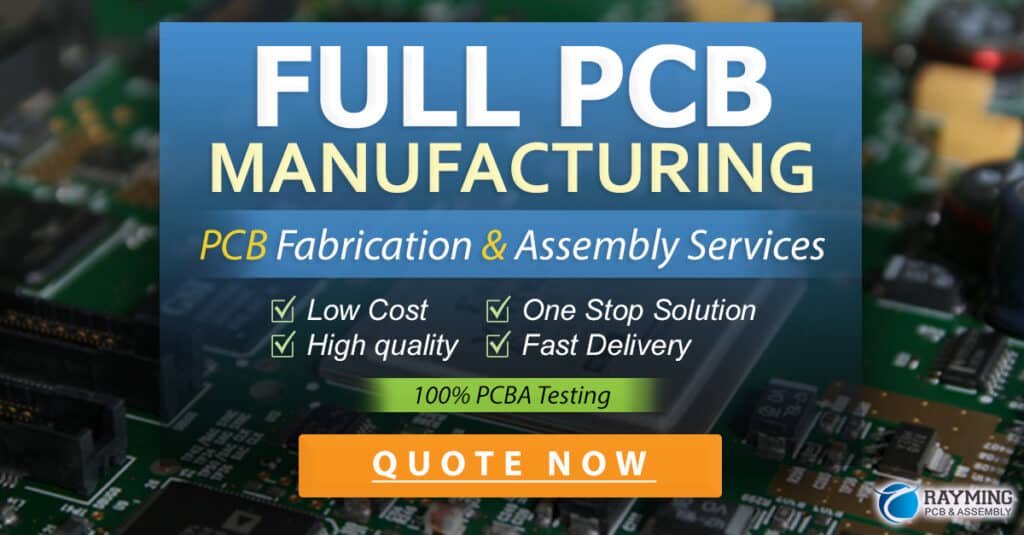
Case Study: Implementing Rick Hartley’s Recommendations
To illustrate the effectiveness of Rick Hartley’s recommendations, let’s consider a case study involving the design of a 6-layer PCB for a high-speed digital system.
The design team followed Rick Hartley’s guidelines for layer stack-up, placing the ground plane on the layer adjacent to the top layer and the power plane on the inner layer closest to the bottom layer. They also carefully selected and placed decoupling capacitors close to the power pins of the components, using a combination of bulk, ceramic, and low-ESR capacitors.
The team minimized the via sizes and placed them close to the power pins of the components to reduce the loop area. They also used via stitching to connect the ground planes on different layers, creating a low-impedance return path.
Finally, the team performed current density analysis to ensure that the PCB could handle the expected current loads without exceeding the maximum allowable temperature rise or voltage drop.
The resulting 6-layer PCB demonstrated excellent power delivery performance, with minimal voltage ripple and low EMI. The system functioned reliably, and the design team attributed much of the success to following Rick Hartley’s recommendations.
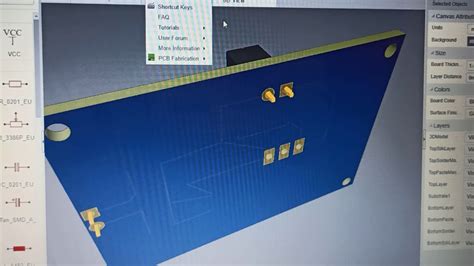
Frequently Asked Questions (FAQ)
-
Q: What are the benefits of using a 6-layer PCB compared to a 4-layer PCB?
A: 6-layer PCBs offer more routing space and better signal integrity compared to 4-layer boards, while still being more cost-effective than higher layer count boards. -
Q: Why is proper power delivery important in PCB design?
A: Proper power delivery ensures that all components on the board receive the necessary power to function correctly, minimizing signal integrity issues, EMI, and component failure. -
Q: What is the recommended layer stack-up for a 6-layer PCB?
A: A typical 6-layer PCB stack-up consists of a signal layer on top, followed by a ground plane, two signal layers, a power plane, and a signal layer on the bottom. -
Q: How do decoupling capacitors help maintain power integrity on a PCB?
A: Decoupling capacitors provide a local source of charge to the components, reducing voltage ripple and minimizing the effect of transient currents on the power supply. -
Q: What is current density analysis, and why is it important in PCB design?
A: Current density analysis is a technique used to evaluate the current-carrying capacity of the traces and planes on a PCB, helping identify areas susceptible to thermal issues or voltage drop. It ensures that the PCB can handle the expected current loads without exceeding the maximum allowable temperature rise or voltage drop.
Conclusion
Designing a 6-layer PCB with proper power delivery requires careful consideration of various factors, such as layer stack-up, decoupling capacitor selection and placement, via sizing and placement, and current density analysis. By following Rick Hartley’s recommendations, PCB designers can create boards that offer excellent power delivery performance, signal integrity, and reliability.
As demonstrated in the case study, implementing these guidelines can lead to successful 6-layer PCB designs that meet the demanding requirements of modern electronic systems. By staying up-to-date with the latest best practices and insights from experts like Rick Hartley, PCB designers can continue to push the boundaries of what is possible with 6-layer boards and power delivery.
No responses yet