Introduction to PCB Optimization for RF Circuits
Printed Circuit Board (PCB) layout and optimization are critical aspects of RF circuit design. Proper PCB layout techniques can significantly improve the performance, reliability, and manufacturability of RF circuits. In this comprehensive guide, we will delve into the best practices and guidelines for PCB layout and circuit optimization in the context of RF design.
Understanding the Challenges of RF PCB Design
RF PCB design presents unique challenges compared to traditional low-frequency digital or analog designs. Some of the key challenges include:
-
Signal Integrity: RF signals are highly susceptible to noise, interference, and distortion. Maintaining signal integrity is crucial to ensure optimal performance of the RF circuit.
-
Impedance Matching: Proper impedance matching is essential to minimize reflections and ensure maximum power transfer between components in an RF circuit.
-
Electromagnetic Interference (EMI): RF circuits can generate and be affected by EMI, which can lead to degraded performance and compliance issues.
-
Parasitic Effects: Parasitic capacitances, inductances, and resistances can significantly impact the behavior of RF circuits, especially at higher frequencies.
PCB Material Selection for RF Circuits
The choice of PCB material plays a vital role in the performance of RF circuits. The key properties to consider when selecting a PCB material for RF applications include:
-
Dielectric Constant (εr): A stable and consistent dielectric constant is essential to maintain controlled impedance and minimize signal distortion.
-
Loss Tangent (tanδ): Low loss tangent materials help minimize signal attenuation and maintain signal integrity.
-
Thermal Stability: RF circuits often generate significant heat, so the PCB material should have good thermal stability to prevent warping and maintain mechanical integrity.
Some commonly used PCB materials for RF applications include:
Material | Dielectric Constant (εr) | Loss Tangent (tanδ) | Applications |
---|---|---|---|
FR-4 | 4.3-4.7 | 0.02 | Low-cost, general-purpose RF |
Rogers RO4003C | 3.38 | 0.0027 | High-frequency, low-loss RF |
Rogers RO4350B | 3.48 | 0.0037 | High-frequency, low-loss RF |
PTFE (Teflon) | 2.1 | 0.0002 | Very high-frequency, ultra-low-loss RF |
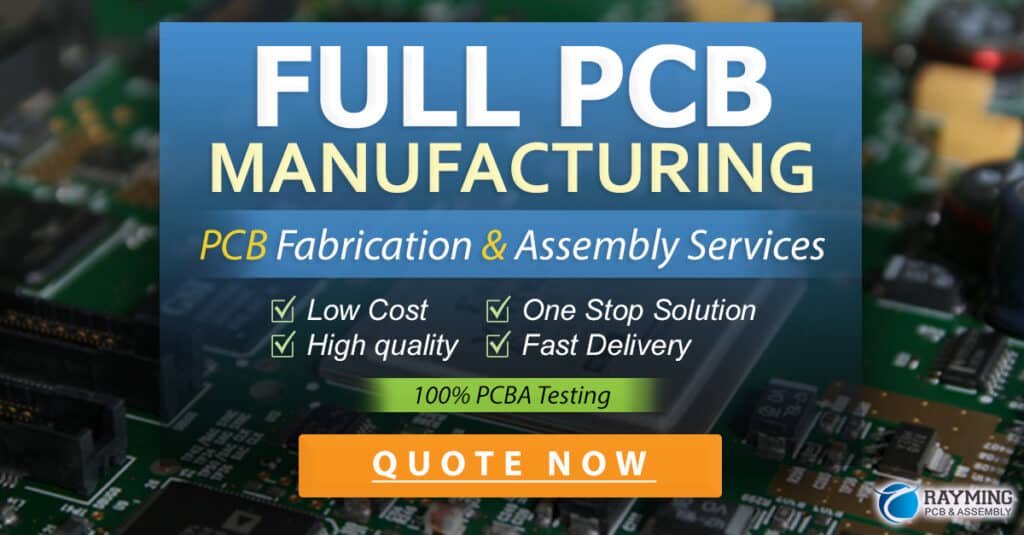
Controlled Impedance in RF PCB Layout
Maintaining controlled impedance is crucial for optimal signal propagation and minimizing reflections in RF circuits. The characteristic impedance of a transmission line is determined by its geometry and the properties of the PCB material. The two main types of transmission lines used in RF PCB design are:
- Microstrip: A microstrip transmission line consists of a conductive trace on the top layer of the PCB, with a ground plane on the bottom layer. The characteristic impedance of a microstrip line is given by:
Z0 = (87 / √(εr + 1.41)) * ln(5.98 * h / (0.8 * w + t))
where:
– Z0 is the characteristic impedance
– εr is the dielectric constant of the PCB material
– h is the thickness of the dielectric
– w is the width of the trace
– t is the thickness of the trace
- Stripline: A stripline transmission line consists of a conductive trace embedded between two ground planes. The characteristic impedance of a stripline is given by:
Z0 = (60 / √εr) * ln(4 * b / (0.67 * π * (0.8 * w + t)))
where:
– Z0 is the characteristic impedance
– εr is the dielectric constant of the PCB material
– b is the distance between the ground planes
– w is the width of the trace
– t is the thickness of the trace
To achieve controlled impedance, the PCB layout designer must carefully choose the trace dimensions and spacing based on the desired characteristic impedance and the properties of the chosen PCB material.
Grounding and Shielding Techniques
Proper grounding and shielding are essential to minimize noise, interference, and crosstalk in RF circuits. Some key techniques include:
-
Ground Planes: Use uninterrupted ground planes on one or more layers of the PCB to provide a low-impedance return path for RF currents and minimize radiation.
-
Via Stitching: Place closely spaced vias along the edges of ground planes to create a continuous shield and prevent leakage of RF energy.
-
Compartmentalization: Divide the PCB into separate compartments for different functions (e.g., RF, digital, power) and use shielding techniques to isolate them from each other.
-
Trace Routing: Route RF traces away from noise sources and sensitive components, and use techniques like stripline or coplanar waveguide to minimize crosstalk.
Component Placement and Layout Optimization
Optimal component placement and layout are critical for RF circuit performance and manufacturability. Some guidelines to follow include:
-
Place RF components close to each other to minimize trace lengths and parasitic effects.
-
Use surface-mount devices (SMDs) whenever possible to reduce lead inductance and improve high-frequency performance.
-
Orient components to minimize coupling and interference, and to facilitate proper grounding and shielding.
-
Consider the effects of component placement on thermal management and mechanical stress.
-
Follow manufacturer recommendations for pad sizes, spacings, and layout patterns.
Simulation and Verification
Simulation and verification are essential steps in the RF PCB design process to ensure optimal performance and catch potential issues before fabrication. Some key aspects to consider include:
-
Electromagnetic (EM) Simulation: Use EM simulation tools to analyze the behavior of RF traces, components, and structures, and to optimize the layout for minimum loss and maximum performance.
-
Circuit Simulation: Use circuit simulation tools to verify the functionality and performance of the RF circuit, including impedance matching, gain, noise, and linearity.
-
Design Rule Checking (DRC): Perform DRC to ensure that the PCB layout meets the manufacturing and assembly constraints, such as minimum trace widths, spacings, and hole sizes.
-
Signal Integrity Analysis: Use signal integrity analysis tools to evaluate the quality of RF signals, including rise times, overshoot, and ringing, and to optimize the layout for maximum signal integrity.
Manufacturing and Assembly Considerations
To ensure successful manufacturing and assembly of RF PCBs, consider the following:
-
Choose a reputable PCB fabricator with experience in RF PCB manufacturing and the capability to meet the required specifications, such as controlled impedance and tight tolerances.
-
Provide comprehensive documentation, including PCB layout files, assembly drawings, and bill of materials (BOM), to the fabricator and assembler.
-
Specify the required surface finish, such as immersion silver or gold, to ensure good solderability and high-frequency performance.
-
Consider the effects of PCB panelization and routing on the RF performance, and work with the fabricator to optimize the panel layout and routing strategy.
-
Perform thorough testing and inspection of the manufactured PCBs and assembled boards to ensure conformance to specifications and catch any defects or issues.
Frequently Asked Questions (FAQ)
- What is the best PCB material for RF applications?
-
The best PCB material for RF applications depends on the specific requirements of the circuit, such as frequency, loss, and cost. Common high-performance RF materials include Rogers RO4003C, Rogers RO4350B, and PTFE (Teflon). For lower-cost applications, FR-4 may be sufficient.
-
How can I minimize crosstalk in my RF PCB layout?
-
To minimize crosstalk in an RF PCB layout, use techniques such as:
- Separating RF traces from each other and from other signal traces
- Using stripline or coplanar waveguide structures to confine the RF fields
- Placing ground planes between layers to provide shielding
- Routing traces orthogonally to each other to minimize coupling
-
What is the difference between microstrip and stripline transmission lines?
-
Microstrip transmission lines consist of a conductive trace on the top layer of the PCB, with a ground plane on the bottom layer. They are easier to fabricate but more susceptible to interference and radiation. Stripline transmission lines consist of a conductive trace embedded between two ground planes, providing better shielding and isolation but requiring more layers and complexity.
-
How can I ensure controlled impedance in my RF PCB?
-
To ensure controlled impedance in an RF PCB:
- Choose a suitable PCB material with stable dielectric constant and low loss tangent
- Use a controlled impedance calculator or simulation tool to determine the trace dimensions and spacing for the desired characteristic impedance
- Specify the controlled impedance requirements to the PCB fabricator and work with them to ensure compliance
- Perform impedance testing on the fabricated PCBs to verify conformance to specifications
-
What are some common mistakes to avoid in RF PCB layout?
- Common mistakes to avoid in RF PCB layout include:
- Neglecting to use a ground plane or providing insufficient grounding
- Routing RF traces too close to each other or to other signal traces
- Using incorrect transmission line structures or dimensions for the desired impedance
- Placing components too far apart, leading to long traces and increased losses
- Ignoring the effects of via placement and routing on RF performance
- Not performing sufficient simulation, verification, and testing before fabrication and assembly
Conclusion
PCB layout and optimization are critical aspects of RF circuit design, directly impacting the performance, reliability, and manufacturability of the final product. By following the guidelines and best practices outlined in this article, engineers and designers can create robust and high-performance RF PCBs that meet the demanding requirements of modern applications.
From selecting the appropriate PCB materials and controlled impedance structures to implementing effective grounding, shielding, and component placement strategies, a well-optimized RF PCB layout is essential for success in today’s competitive market. By leveraging simulation, verification, and testing techniques, and working closely with experienced PCB fabricators and assemblers, designers can ensure that their RF products meet the highest standards of quality and performance.
As the world continues to embrace wireless technologies and push the boundaries of RF innovation, the importance of skilled RF PCB layout and optimization will only continue to grow. By staying up-to-date with the latest techniques and best practices, and by collaborating with industry partners and experts, RF designers can unlock new possibilities and drive the future of wireless communication and sensing.
No responses yet