Rapid prototyping of printed circuit boards (PCBs) has become an essential process in the world of electronics design and manufacturing. As technology advances at a breakneck pace, the ability to quickly iterate and test new designs is crucial for keeping up with market demands and staying ahead of the competition. This article delves into the world of rapid prototyping PCB assembly, exploring its importance, techniques, and best practices.
What is Rapid Prototyping PCB Assembly?
Rapid prototyping PCB assembly is the process of quickly creating functional prototypes of printed circuit boards for testing, evaluation, and design validation purposes. Unlike traditional PCB manufacturing methods, which can take weeks or even months, rapid prototyping allows engineers and designers to produce working prototypes in a matter of days or even hours.
This accelerated process is made possible by leveraging advanced manufacturing technologies, such as desktop PCB milling machines, 3D printers, and specialized software tools. By streamlining the design-to-prototype cycle, rapid prototyping enables faster iterations, quicker identification of potential issues, and more efficient product development.
Why is Rapid Prototyping PCB Assembly Important?
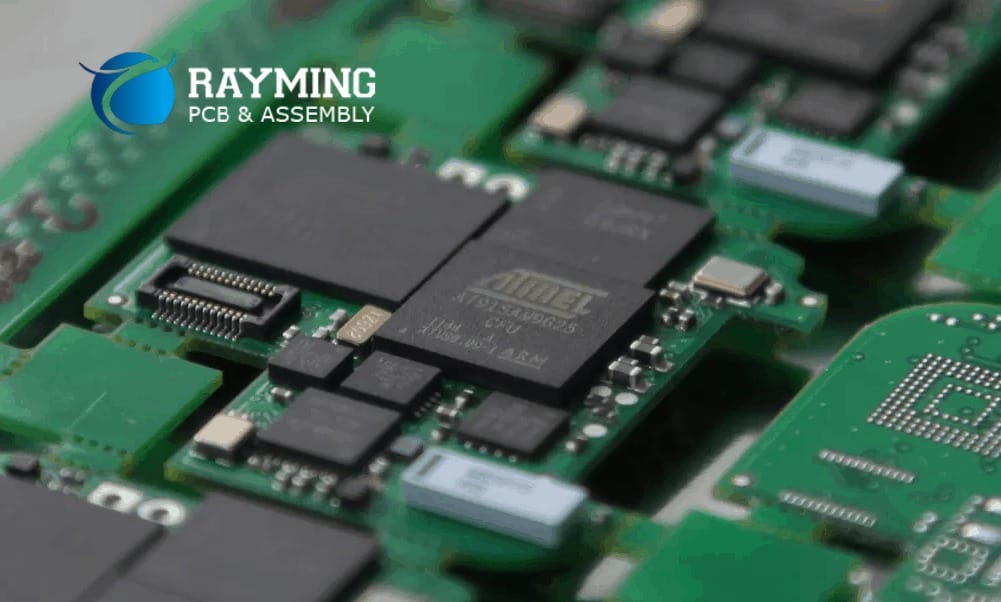
Rapid prototyping PCB assembly offers numerous benefits that make it an invaluable process in the electronics industry:
- Faster Time-to-Market: By reducing the time required to produce working prototypes, companies can bring their products to market more quickly, giving them a competitive edge.
- Cost Savings: Rapid prototyping eliminates the need for costly and time-consuming traditional PCB manufacturing methods during the early stages of product development, resulting in significant cost savings.
- Design Validation and Optimization: Prototyping allows designers to physically test and validate their designs, identify potential issues early in the development cycle, and make necessary adjustments before committing to full-scale production.
- Improved Collaboration and Communication: Physical prototypes facilitate better communication and collaboration among team members, stakeholders, and customers, enabling more effective feedback and decision-making processes.
- Risk Mitigation: By identifying and addressing potential issues early on, rapid prototyping helps mitigate risks associated with product development, reducing the likelihood of costly mistakes and delays.
Rapid Prototyping PCB Assembly Techniques
There are several techniques and methods used in rapid prototyping PCB assembly, each with its own advantages and limitations. Here are some of the most common approaches:
1. Desktop PCB Milling
Desktop PCB milling machines, also known as PCB prototyping machines or PCB plotters, are compact and affordable devices that can quickly produce high-quality PCB prototypes. These machines use computer-controlled milling tools to precisely remove copper from a pre-coated substrate, creating the desired circuit patterns.
Advantages:
- High precision and accuracy
- Ability to create complex designs with tight tolerances
- Relatively low cost compared to traditional PCB manufacturing
Limitations:
- Limited board size and complexity due to the desktop form factor
- Requires specialized software and CAM tools for design preparation
2. 3D Printed PCBs
3D printing technology has opened up new possibilities for rapid prototyping PCBs. With this approach, conductive inks or filaments are used to print the circuit traces and components directly onto a substrate or within a 3D-printed enclosure.
Advantages:
- Ability to create complex 3D geometries and integrated enclosures
- Rapid iteration and customization
- Low material costs and minimal setup time
Limitations:
- Limited precision and resolution compared to traditional PCB manufacturing
- Restricted material choices and potential reliability concerns
3. Chemical Etching
Chemical etching is a more traditional method of rapid prototyping PCBs, where a copper-clad substrate is selectively etched using chemicals to create the desired circuit patterns. This process can be performed manually or with the aid of specialized equipment.
Advantages:
- Relatively simple and inexpensive process
- Capable of producing high-quality prototypes
Limitations:
- Potential environmental and safety concerns due to the use of chemicals
- Limited design complexity and feature size
- Requires additional steps for component assembly
4. Outsourced Rapid Prototyping Services
For more complex or high-volume prototyping needs, many companies offer specialized rapid prototyping services. These services typically utilize advanced manufacturing techniques, such as laser direct structuring (LDS), injection molding, or automated assembly lines.
Advantages:
- Access to advanced manufacturing technologies and expertise
- Ability to produce high-quality and complex prototypes
- Scalability to handle larger volumes
Limitations:
- Higher costs compared to in-house prototyping methods
- Potential lead time delays due to outsourcing
Best Practices for Rapid Prototyping PCB Assembly
To maximize the benefits of rapid prototyping PCB assembly and ensure successful prototypes, it’s essential to follow best practices:
- Design for Prototyping: Optimize your PCB designs specifically for rapid prototyping techniques, taking into account the limitations and capabilities of the chosen method.
- Leverage CAD/CAM Tools: Utilize specialized computer-aided design (CAD) and computer-aided manufacturing (CAM) software tools to streamline the design-to-prototype workflow and ensure accurate translation of your designs.
- Establish a Systematic Prototyping Process: Develop a well-defined prototyping process that includes steps for design review, prototype fabrication, assembly, testing, and documentation.
- Implement Version Control: Implement version control systems to track changes and revisions to your PCB designs, ensuring traceability and enabling easy comparison between iterations.
- Conduct Thorough Testing and Validation: Thoroughly test and validate your prototypes to identify and address potential issues before proceeding to full-scale production.
- Collaborate and Seek Feedback: Involve stakeholders, team members, and end-users throughout the prototyping process to gather valuable feedback and insights for design improvements.
- Optimize for Manufacturability: While prototyping, consider the manufacturability of your designs to ensure a smoother transition to full-scale production.
- Stay Up-to-Date with Emerging Technologies: Continuously monitor and adopt new rapid prototyping technologies and techniques to maintain a competitive edge and leverage the latest advancements.
FAQs
- Q: What is the main advantage of rapid prototyping PCB assembly? A: The primary advantage of rapid prototyping PCB assembly is the ability to quickly produce functional prototypes, enabling faster design iterations, early identification of issues, and reduced time-to-market.
- Q: Can rapid prototyping techniques be used for low-volume production runs? A: While primarily intended for prototyping, some rapid prototyping techniques, such as desktop PCB milling or 3D printing, can be suitable for low-volume production runs, depending on the specific requirements and constraints.
- Q: How does the cost of rapid prototyping compare to traditional PCB manufacturing? A: Rapid prototyping techniques generally have lower upfront costs compared to traditional PCB manufacturing methods, especially during the early stages of product development. However, for larger production volumes, traditional manufacturing methods may be more cost-effective.
- Q: Can rapid prototyping techniques produce high-quality and reliable PCBs? A: While the primary goal of rapid prototyping is to produce functional prototypes quickly, some techniques, such as desktop PCB milling or outsourced rapid prototyping services, can produce high-quality and reliable PCBs suitable for certain applications or low-volume production runs.
- Q: What are the limitations of rapid prototyping PCB assembly techniques? A: Limitations of rapid prototyping PCB assembly techniques can include restricted board size and complexity, limited material choices, potential reliability concerns, and reduced precision and accuracy compared to traditional PCB manufacturing methods.
Conclusion
Rapid prototyping PCB assembly has revolutionized the electronics industry by enabling faster design iterations, accelerated product development cycles, and more efficient validation processes. With a range of techniques and methods available, engineers and designers can choose the approach that best suits their specific needs and constraints.
By following best practices and staying up-to-date with emerging technologies, companies can leverage the power of rapid prototyping to gain a competitive edge, reduce time-to-market, and deliver innovative products more efficiently. As technology continues to evolve, the importance of rapid prototyping PCB assembly will only continue to grow, driving innovation and shaping the future of electronics design and manufacturing.
No responses yet