Introduction to Copper Foil in Flex Circuit Boards
Flexible circuit boards, also known as flex circuits or flexible printed circuit boards (FPCBs), have gained significant popularity in recent years due to their versatility, lightweight nature, and ability to fit into compact spaces. These characteristics make them ideal for various applications, including consumer electronics, medical devices, automotive systems, and aerospace industries. One of the critical components in the manufacturing of flex circuit boards is copper foil, which serves as the conductive layer for the electrical connections.
In this article, we will dive into the world of copper foil for flex circuit boards, focusing on the comparison between two primary types: RA (Rolled Annealed) Copper and ED (Electrodeposited) Copper. We will explore their properties, manufacturing processes, advantages, and disadvantages, as well as their suitability for different applications.
What is Copper Foil?
Copper foil is a thin, flat sheet of copper that is used as the conductive layer in printed circuit boards (PCBs), including flex circuit boards. It is an essential component that enables the electrical connections between various components on the board. Copper foil is typically laminated onto a flexible substrate, such as polyimide or polyester, to create the foundation of a flex circuit board.
The thickness of copper foil used in flex circuits can vary depending on the specific application and design requirements. Common thicknesses range from 9 microns (1/4 oz) to 105 microns (3 oz), with thinner foils being more flexible and suitable for dynamic applications, while thicker foils offer better current-carrying capacity and mechanical stability.
RA Copper: Rolled Annealed Copper Foil
Manufacturing Process
RA Copper, or Rolled Annealed Copper foil, is produced through a mechanical process that involves rolling and annealing. The process begins with high-purity copper ingots, which are heated and cast into thin slabs. These slabs are then repeatedly rolled through a series of rollers to reduce their thickness gradually. The rolling process introduces strain and work hardening into the copper, increasing its strength and hardness.
After the rolling process, the copper foil undergoes annealing, which involves heating the foil to a specific temperature and then allowing it to cool slowly. Annealing relieves the internal stresses introduced during rolling and recrystallizes the copper grains, resulting in a more ductile and formable foil. The annealing process also helps to control the grain structure and mechanical properties of the copper foil.
Properties and Characteristics
RA Copper foil exhibits several distinctive properties that make it suitable for use in flex circuit boards:
-
High ductility: The annealing process gives RA Copper foil excellent ductility, allowing it to be bent, folded, and formed into various shapes without cracking or breaking. This property is crucial for flex circuits that require dynamic bending or folding.
-
Smooth surface: RA Copper foil has a relatively smooth surface compared to ED Copper foil. The smooth surface promotes better adhesion to the substrate and reduces the risk of delamination or adhesion issues.
-
Consistent mechanical properties: The rolling and annealing process results in uniform mechanical properties throughout the copper foil. This consistency is essential for maintaining the integrity and reliability of the flex circuit board.
-
Good electrical conductivity: RA Copper foil offers excellent electrical conductivity, ensuring efficient and reliable signal transmission within the flex circuit.
Advantages and Disadvantages
Advantages of RA Copper foil:
– High ductility and formability
– Smooth surface for better adhesion
– Consistent mechanical properties
– Good electrical conductivity
Disadvantages of RA Copper foil:
– Higher cost compared to ED Copper foil
– Limited availability in ultra-thin thicknesses (below 9 microns)
– Longer lead times due to the multi-step manufacturing process
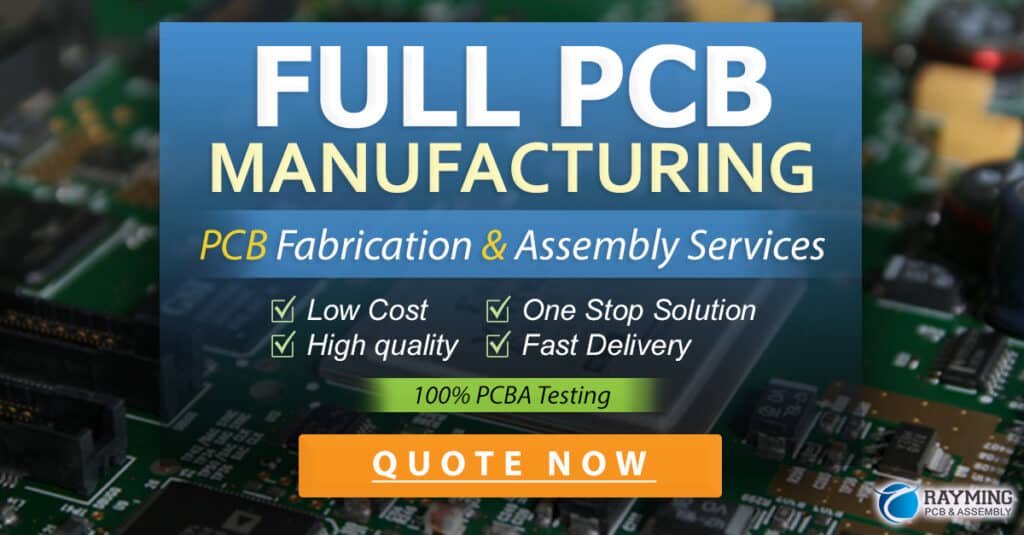
ED Copper: Electrodeposited Copper Foil
Manufacturing Process
ED Copper, or Electrodeposited Copper foil, is produced through an electrochemical process. The process involves electroplating copper onto a rotating stainless steel drum or titanium mandrel, which serves as the cathode. The drum is immersed in an electrolytic solution containing copper ions, and an electrical current is applied. As the current flows, copper ions are reduced and deposited onto the drum surface, forming a thin layer of copper foil.
The thickness of the ED Copper foil can be precisely controlled by adjusting the electroplating parameters, such as current density, plating time, and solution composition. Once the desired thickness is achieved, the copper foil is peeled off the drum and wound onto a roll for further processing or packaging.
Properties and Characteristics
ED Copper foil possesses several unique properties that differentiate it from RA Copper foil:
-
Fine-grained structure: The electrodeposition process results in a fine-grained microstructure, which contributes to the foil’s mechanical strength and resistance to fatigue.
-
High tensile strength: ED Copper foil exhibits higher tensile strength compared to RA Copper foil, making it more resistant to tearing or breaking during the manufacturing process or in applications that require high mechanical stress.
-
Matte and shiny sides: ED Copper foil has a distinct matte side and shiny side. The matte side, which is the side in contact with the drum during electrodeposition, has a rougher surface that promotes better adhesion to the substrate. The shiny side, on the other hand, has a smoother surface and is typically used for the outer layer of the flex circuit.
-
Availability in ultra-thin thicknesses: ED Copper foil can be produced in ultra-thin thicknesses, down to 5 microns or less. This makes it suitable for applications that require extremely thin and lightweight flex circuits.
Advantages and Disadvantages
Advantages of ED Copper foil:
– Lower cost compared to RA Copper foil
– High tensile strength and resistance to fatigue
– Availability in ultra-thin thicknesses
– Faster production process
Disadvantages of ED Copper foil:
– Lower ductility compared to RA Copper foil
– Rougher surface on the matte side, which may require additional surface treatment for improved adhesion
– Potential for higher surface roughness and irregularities
Comparison Table: RA Copper vs ED Copper
Property | RA Copper | ED Copper |
---|---|---|
Manufacturing Process | Rolling and annealing | Electrodeposition |
Ductility | High | Lower than RA Copper |
Surface Roughness | Smooth | Matte side rougher than RA |
Tensile Strength | Lower than ED Copper | High |
Availability | Limited in ultra-thin thicknesses | Available in ultra-thin thicknesses |
Cost | Higher than ED Copper | Lower than RA Copper |
Lead Time | Longer due to multi-step process | Faster production process |
Applications and Suitability
The choice between RA Copper and ED Copper foil for flex circuit boards depends on various factors, including the specific application requirements, design constraints, and cost considerations.
RA Copper foil is often preferred in applications that require:
– High flexibility and dynamic bending
– Smooth surface for better adhesion and lamination
– Consistent mechanical properties throughout the foil
Examples of applications where RA Copper foil is commonly used include:
– Wearable electronics
– Medical devices with flexible sensors or electrodes
– Automotive applications with dynamic flexing requirements
– Aerospace and defense applications with stringent reliability requirements
On the other hand, ED Copper foil is suitable for applications that prioritize:
– Ultra-thin and lightweight flex circuits
– High tensile strength and resistance to mechanical stress
– Cost-sensitive applications that can tolerate slightly lower ductility
Examples of applications where ED Copper foil is often used include:
– Consumer electronics with compact and lightweight designs
– High-density interconnects (HDI) in flex circuits
– Flexible displays and touch panels
– Flexible solar cells and photovoltaic modules
It’s important to note that the choice between RA Copper and ED Copper foil is not always clear-cut, and there may be instances where either type can be used successfully. The decision ultimately depends on a careful evaluation of the specific application requirements, manufacturing capabilities, and cost-benefit analysis.
Frequently Asked Questions (FAQ)
- What is the main difference between RA Copper and ED Copper foil?
-
The main difference lies in their manufacturing processes. RA Copper foil is produced through a mechanical process involving rolling and annealing, while ED Copper foil is produced through an electrochemical process called electrodeposition.
-
Which type of copper foil is more flexible, RA Copper or ED Copper?
-
RA Copper foil is generally more flexible and ductile compared to ED Copper foil. The annealing process in RA Copper foil production results in a more formable and bendable foil.
-
Can ED Copper foil be used for applications that require ultra-thin flex circuits?
-
Yes, ED Copper foil is available in ultra-thin thicknesses, down to 5 microns or less. This makes it suitable for applications that demand extremely thin and lightweight flex circuits.
-
Is RA Copper foil more expensive than ED Copper foil?
-
Yes, RA Copper foil is typically more expensive than ED Copper foil due to the multi-step manufacturing process and longer lead times involved in its production.
-
Which type of copper foil has a smoother surface, RA Copper or ED Copper?
- RA Copper foil has a relatively smoother surface compared to ED Copper foil. The matte side of ED Copper foil has a rougher surface, which may require additional surface treatment for improved adhesion.
Conclusion
Copper foil plays a crucial role in the manufacturing of flex circuit boards, serving as the conductive layer that enables electrical connections between components. RA Copper and ED Copper foil are two primary types of copper foil used in the industry, each with its own unique properties, manufacturing processes, advantages, and disadvantages.
RA Copper foil, produced through rolling and annealing, offers high ductility, a smooth surface, and consistent mechanical properties. It is well-suited for applications that require dynamic bending and reliable performance. ED Copper foil, produced through electrodeposition, provides high tensile strength, availability in ultra-thin thicknesses, and cost-effectiveness. It is often used in applications that prioritize lightweight designs and cost savings.
When choosing between RA Copper and ED Copper foil for a specific flex circuit application, designers and manufacturers must carefully consider the application requirements, design constraints, and cost factors. By understanding the properties and characteristics of each type of copper foil, they can make informed decisions that optimize the performance, reliability, and cost-effectiveness of their flex circuit boards.
As technology continues to advance and the demand for flexible electronics grows, the importance of selecting the appropriate copper foil for flex circuit boards will only increase. By staying informed about the latest developments in copper foil technology and the specific needs of their applications, designers and manufacturers can ensure that they are utilizing the most suitable materials to create high-quality, reliable, and innovative flex circuit solutions.
No responses yet