What is Circuit Assembly?
Circuit assembly is the process of connecting electronic components to create a functional printed circuit board (PCB). This involves soldering components like resistors, capacitors, integrated circuits (ICs), and connectors onto a PCB according to a specific design. The assembled PCB forms a complete electronic circuit that performs a designated function in an electronic device.
Circuit assembly is a crucial step in electronics manufacturing. The quality and reliability of the assembled PCB directly impacts the performance and longevity of the end product, whether it’s a smartphone, laptop, medical device, automotive component, or industrial equipment.
Types of Circuit Assembly
There are three main types of circuit assembly techniques used in the electronics industry:
-
Through-Hole Assembly (THA): In this method, component leads are inserted into drilled holes on the PCB and soldered onto pads on the opposite side. THA is suitable for larger components and offers strong mechanical bonds. However, it requires more manual labor and takes up more PCB space compared to surface mount techniques.
-
Surface Mount Assembly (SMA): SMA involves placing components directly onto pads on the PCB surface and soldering them in place. Surface mount devices (SMDs) are smaller and can be placed on both sides of the PCB, enabling higher component density and smaller board sizes. SMA is the most common assembly method in modern electronics.
-
Mixed Assembly: Some PCBs use a combination of through-hole and surface mount components to leverage the advantages of both techniques. Mixed assembly is often used when a design includes large connectors or components that are not available in surface mount packages.
The choice of assembly technique depends on various factors such as component availability, board size constraints, performance requirements, manufacturing capabilities, and cost considerations.
Circuit Assembly Process Flow
The typical circuit assembly process involves the following steps:
-
Solder Paste Printing: A thin layer of solder paste is applied onto the PCB pads using a stencil printer. Solder paste is a mixture of tiny solder particles suspended in flux.
-
Component Placement: SMD components are picked and placed onto their respective pads on the PCB. High-speed pick-and-place machines are used for precise and fast component placement.
-
Reflow Soldering: The populated PCB goes through a reflow oven that heats the board to a specific temperature profile. This melts the solder particles in the paste, forming strong electrical and mechanical bonds between the components and pads.
-
Inspection: Automated optical inspection (AOI) systems check for missing components, misalignments, solder defects, and other assembly issues. Manual visual inspection may also be performed.
-
Through-Hole Assembly: If the design includes through-hole components, they are inserted and wave soldered or hand soldered after the surface mount process.
-
Testing: The assembled PCB undergoes various functional tests to verify its performance against design specifications. This may include in-circuit testing (ICT), flying probe testing, boundary scan testing, and functional testing.
-
Conformal Coating: Some PCBs require a protective conformal coating to shield against moisture, dust, chemicals, or extreme temperatures.
-
Final Inspection and Packaging: The finished PCB is visually inspected, cleaned if necessary, and packaged for shipment to the customer or integration into the final product.
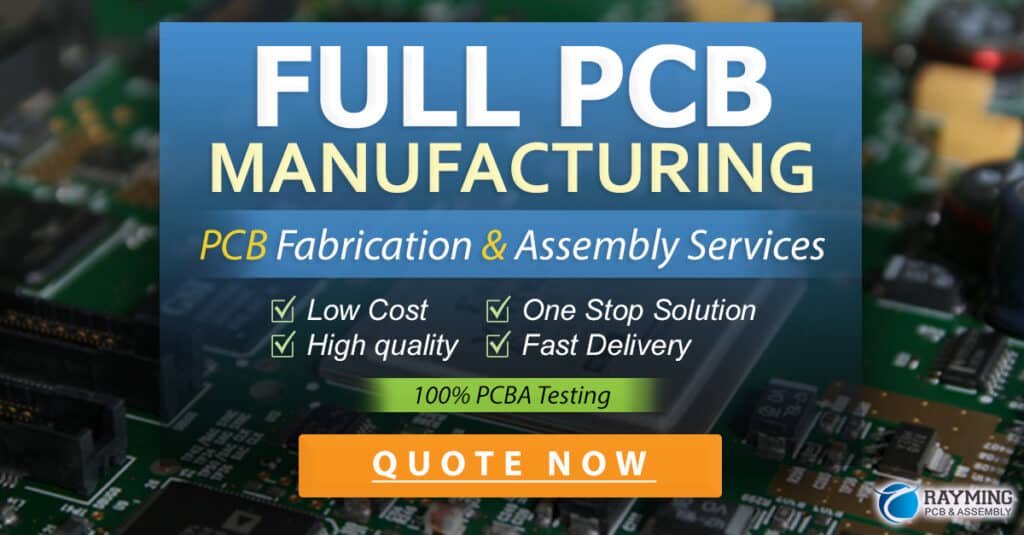
Key Considerations for Quality Circuit Assembly
To ensure high-quality circuit assembly, manufacturers must consider several critical factors:
Component Selection and Sourcing
Using high-quality, reliable components is essential for the overall performance and durability of the assembled PCB. Manufacturers should source components from reputable suppliers and verify their authenticity to avoid counterfeit parts. They should also consider component specifications, packaging, and lead time to ensure compatibility with the assembly process and timely delivery.
PCB Design for Manufacturing (DFM)
The PCB design should adhere to DFM guidelines to facilitate smooth assembly and minimize defects. This includes:
– Choosing appropriate component packages and footprints
– Providing adequate spacing between components for placement and soldering
– Optimizing component orientation for efficient assembly
– Avoiding complex or unnecessary routing
– Specifying clear and accurate assembly instructions
Close collaboration between the PCB designer and the assembly team is crucial to identify and resolve potential manufacturing issues early in the design stage.
Process Control and Optimization
Manufacturers must establish robust process controls to maintain consistency and minimize variability in the assembly process. This involves:
– Developing and documenting standard operating procedures (SOPs)
– Regularly calibrating and maintaining equipment
– Monitoring process parameters such as solder paste print quality, component placement accuracy, and reflow temperature profiles
– Implementing statistical process control (SPC) techniques to identify trends and make data-driven decisions
– Continuously improving processes through root cause analysis and corrective actions
Cleanliness and Contamination Control
Cleanliness is critical in circuit assembly as contaminants can lead to defects, reduced reliability, and premature failure. Manufacturers should implement contamination control measures such as:
– Maintaining a clean and organized production environment
– Using appropriate personal protective equipment (PPE) and enforcing proper hygiene practices
– Storing components and materials in a controlled environment to prevent moisture, dust, or electrostatic discharge (ESD) damage
– Regularly cleaning and inspecting tools, equipment, and workstations
– Using high-quality, clean solder paste and flux
Training and Skill Development
Skilled and well-trained operators are essential for achieving high-quality circuit assembly. Manufacturers should invest in comprehensive training programs that cover:
– Assembly techniques and best practices
– Equipment operation and maintenance
– Quality control and inspection methods
– Safety and ESD Prevention
– Continuous improvement and problem-solving skills
Regular skill assessments and refresher training can help maintain a high level of competence and adaptability among the assembly team.
Common Circuit Assembly Defects and Prevention
Despite best efforts, defects can occur during the assembly process. Some common defects include:
-
Solder Bridges: Unintended connections between adjacent pads or pins due to excess solder. Prevention: Optimize solder paste volume, use proper stencil design, and maintain consistent reflow temperature profile.
-
Tombstoning: SMD components standing on one end due to uneven solder melting or component misalignment. Prevention: Ensure balanced solder paste deposition, use appropriate component placement pressure, and optimize reflow profile.
-
Cold Solder Joints: Dull, grainy, or incomplete solder joints resulting from insufficient heat, poor wetting, or contamination. Prevention: Maintain proper reflow temperature, use clean materials, and ensure adequate flux activity.
-
Component Shift or Misalignment: Components moving from their intended position during placement or reflow. Prevention: Use appropriate placement pressure, optimize PCB support, and control reflow conveyor speed.
-
Insufficient or Excessive Solder: Too little solder can lead to weak joints, while too much solder can cause bridging or shorts. Prevention: Control solder paste volume, use correct stencil aperture sizes, and optimize reflow profile.
Implementing a comprehensive quality management system, regular process audits, and continuous improvement initiatives can help minimize defects and improve overall assembly quality.
Automated Optical Inspection (AOI) in Circuit Assembly
AOI is a critical quality control step in circuit assembly that uses high-resolution cameras and advanced image processing algorithms to detect assembly defects. AOI systems compare the assembled PCB against a reference image or CAD data to identify issues such as:
- Missing, misaligned, or incorrect components
- Solder defects (bridges, insufficient solder, tombstoning)
- Polarity or orientation errors
- Damaged or lifted pads
- Incorrect or missing markings
AOI offers several advantages over manual inspection:
– High speed and throughput
– Consistent and objective defect detection
– Reduced human error and fatigue
– Traceable and auditable inspection results
– Seamless integration with other automated systems
However, AOI has some limitations:
– Inability to detect hidden or subsurface defects
– Potential for false positives or false negatives
– Need for accurate reference data and regular programming updates
– High initial investment cost
Manufacturers should consider the specific requirements of their products and processes when selecting an AOI system and developing inspection programs. Regular verification and validation of AOI performance are essential to ensure its effectiveness in catching defects.
Traceability and Documentation in Circuit Assembly
Traceability and documentation are essential aspects of quality circuit assembly. They help manufacturers:
– Track materials, components, and processes used in each assembly
– Identify the root cause of defects or failures
– Implement corrective actions and prevent recurrence
– Demonstrate compliance with customer or regulatory requirements
– Facilitate efficient product recalls or field service
Key elements of traceability and documentation in circuit assembly include:
– Unique identification of PCBs, components, and materials using barcodes, RFID tags, or serial numbers
– Recording of process parameters, equipment settings, and operator information for each assembly
– Maintaining certificates of conformance (COCs) and material certifications
– Documenting inspection and test results, including AOI data and functional test logs
– Implementing a robust data management system to store, retrieve, and analyze traceability data
Effective traceability and documentation practices require close collaboration between different departments, including manufacturing, quality, procurement, and customer service. Regular audits and reviews can help ensure the accuracy, completeness, and accessibility of traceability data.
Frequently Asked Questions (FAQ)
- What is the difference between through-hole and surface mount assembly?
-
Through-hole assembly involves inserting component leads into drilled holes on the PCB and soldering them on the opposite side. Surface mount assembly places components directly onto pads on the PCB surface and solders them in place. Surface mount assembly allows for smaller components, higher density, and faster assembly compared to through-hole.
-
What are the most common defects in circuit assembly?
-
Some of the most common defects in circuit assembly include solder bridges, tombstoning, cold solder joints, component shift or misalignment, and insufficient or excessive solder. These defects can be caused by various factors such as improper solder paste application, incorrect component placement, or non-optimal reflow profiles.
-
How can I ensure the quality of the components used in my PCB Assembly?
-
To ensure component quality, source from reputable suppliers, verify the authenticity of parts, and maintain traceability records. Establish incoming quality control procedures to inspect and test components before assembly. Monitor supplier performance and conduct regular audits to assess their quality management systems.
-
What is the role of automated optical inspection (AOI) in circuit assembly?
-
AOI is used to automatically detect assembly defects such as missing or misaligned components, solder defects, and orientation errors. It uses high-resolution cameras and image processing algorithms to compare the assembled PCB against a reference image or CAD data. AOI provides fast, consistent, and objective defect detection, reducing human error and improving quality control efficiency.
-
Why is traceability important in circuit assembly, and how can it be implemented?
- Traceability helps manufacturers track materials, components, and processes used in each assembly, identify the root cause of defects or failures, implement corrective actions, and demonstrate compliance with requirements. It can be implemented by using unique identifiers for PCBs and components, recording process parameters and operator information, maintaining material certifications, and documenting inspection and test results in a robust data management system.
Conclusion
Quality circuit assembly is essential for producing reliable and high-performing electronic products. By understanding the different assembly techniques, process flow, and key considerations, manufacturers can optimize their assembly operations and minimize defects.
Implementing best practices in component selection, PCB design, process control, contamination prevention, and training can significantly improve assembly quality. Automated optical inspection and traceability systems provide valuable tools for detecting defects and maintaining comprehensive records.
As the electronics industry continues to evolve, with increasing complexity and miniaturization of components, maintaining a focus on quality in circuit assembly will be crucial for staying competitive and meeting customer expectations. By continuously improving processes, investing in advanced technologies, and fostering a culture of quality, manufacturers can deliver reliable and innovative electronic products to the market.
No responses yet