Introduction to QFN Packaging
Quad Flat No-lead (QFN) packaging is a surface-mount technology (SMT) package that has gained significant popularity in the electronics industry due to its numerous advantages over traditional packaging methods. QFN packages are characterized by their small size, excellent thermal and electrical performance, and cost-effectiveness. In this article, we will explore the various types of QFN packaging, the assembly process, and the benefits they offer.
Types of QFN Packaging
Standard QFN Packages
Standard QFN packages are the most common type of QFN packaging. They feature a square or rectangular body with a flat lead frame and exposed die pad on the bottom surface. The leads are typically located on all four sides of the package, hence the term “quad.” Standard QFN packages come in various sizes, ranging from 1x1mm to 12x12mm, with lead counts ranging from 4 to 100 or more.
Dual-Row QFN Packages
Dual-row QFN packages, also known as DFN (Dual Flat No-lead) packages, are similar to standard QFN packages but feature two rows of leads on each side of the package instead of one. This allows for a higher lead count within the same package footprint, making them suitable for more complex devices with higher I/O requirements.
Punch-Type QFN Packages
Punch-type QFN packages, also referred to as SMT-type QFN packages, differ from standard QFN packages in their manufacturing process. Instead of using a molded lead frame, punch-type QFN packages employ a stamped or etched lead frame, which is then punched out to form the leads. This process allows for tighter tolerances and finer lead pitches, enabling even smaller package sizes.
Wettable Flank QFN Packages
Wettable flank QFN packages are designed to improve solder joint reliability and inspection. In these packages, the sides of the leads are plated with a solderable material, such as tin or nickel/palladium/gold (NiPdAu). This enables solder to wet up the sides of the leads during the reflow process, creating a stronger and more reliable solder joint. Wettable flank QFN packages also allow for better visual inspection of the solder joints.
QFN Assembly Process
The QFN assembly process involves several steps to ensure proper attachment and functionality of the package on the printed circuit board (PCB). The following table outlines the typical steps in the QFN assembly process:
Step | Description |
---|---|
1. Solder Paste Application | Solder paste is applied to the PCB pads using a stencil printing process. |
2. Component Placement | The QFN package is placed onto the PCB using a pick-and-place machine, aligning the leads with the solder paste-covered pads. |
3. Reflow Soldering | The PCB with the placed QFN package undergoes a reflow soldering process, where the solder paste melts and forms a strong mechanical and electrical connection between the package leads and the PCB pads. |
4. Inspection | After the reflow soldering process, the solder joints are inspected using automated optical inspection (AOI) or X-ray inspection to ensure proper joint formation and detect any defects. |
5. Underfill Application (Optional) | In some cases, an underfill material may be applied between the QFN package and the PCB to improve mechanical strength and thermal performance. |
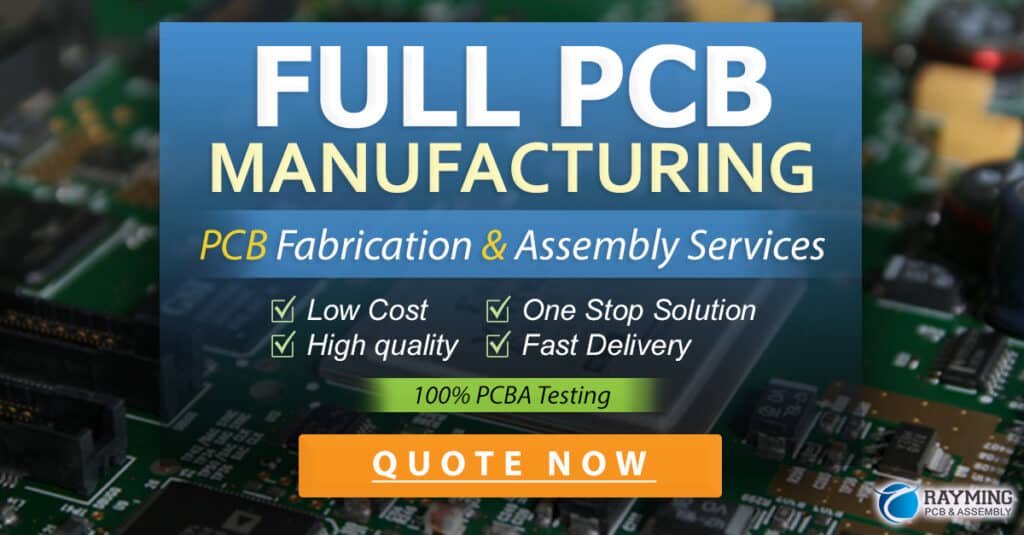
Benefits of QFN Packaging
QFN packaging offers numerous benefits over traditional packaging methods, making it an attractive choice for many electronic devices. Some of the key benefits include:
-
Reduced Package Size: QFN packages have a smaller footprint compared to other SMT packages, such as QFP (Quad Flat Package) or SOP (Small Outline Package). This allows for higher component density on the PCB, enabling the design of more compact and lightweight electronic devices.
-
Improved Thermal Performance: The exposed die pad on the bottom of the QFN package provides a direct thermal path from the die to the PCB, allowing for efficient heat dissipation. This is particularly beneficial for power-sensitive devices, such as power management ICs or high-performance processors.
-
Enhanced Electrical Performance: The shorter lead lengths and reduced package parasitics in QFN packages result in improved electrical performance, including lower inductance, capacitance, and resistance. This makes QFN packages suitable for high-frequency and high-speed applications.
-
Cost-Effectiveness: QFN packages are generally more cost-effective than other SMT packages due to their simpler manufacturing process and reduced material usage. The smaller package size also allows for more units to be produced on a single wafer or lead frame strip, further reducing production costs.
-
Robustness and Reliability: QFN packages exhibit excellent mechanical robustness and reliability due to their low profile and leadless design. The absence of external leads minimizes the risk of lead damage during handling and assembly, while the solder joint strength is enhanced by the exposed die pad and wettable flanks (if present).
Frequently Asked Questions (FAQ)
1. What is the difference between QFN and QFP packages?
QFN (Quad Flat No-lead) and QFP (Quad Flat Package) are both surface-mount package types, but they differ in their lead configuration. QFN packages have leads that are flush with the package body and do not extend outward, while QFP packages have gull-wing leads that extend from the package body. QFN packages are generally smaller and have better thermal and electrical performance compared to QFP packages.
2. Can QFN packages be soldered using through-hole technology?
No, QFN packages are designed specifically for surface-mount technology (SMT) and cannot be soldered using through-hole technology. The leads on a QFN package are flush with the package body and do not have the necessary length or shape to be inserted into through-holes on a PCB.
3. What is the purpose of the exposed die pad in QFN packages?
The exposed die pad in QFN packages serves two main purposes. First, it provides a direct thermal path from the die to the PCB, allowing for efficient heat dissipation. Second, it enhances the mechanical strength of the solder joint by providing additional contact area between the package and the PCB.
4. Are underfill materials always necessary for QFN packages?
No, underfill materials are not always necessary for QFN packages. The decision to use an underfill depends on the specific application requirements, such as mechanical stress, thermal cycling, and reliability expectations. Underfills are more commonly used in applications with high thermal or mechanical stress, or in cases where additional mechanical reinforcement is desired.
5. What are the challenges associated with QFN assembly?
Some of the challenges associated with QFN assembly include:
- Proper alignment of the package leads with the PCB pads during placement
- Ensuring adequate solder paste volume and coverage on the small PCB pads
- Controlling the reflow soldering process to achieve optimal solder joint formation
- Inspecting the solder joints, as they are hidden under the package body
- Reworking or replacing QFN packages, which can be difficult due to their small size and lack of external leads
Conclusion
QFN packaging has become an increasingly popular choice in the electronics industry due to its numerous advantages, including reduced package size, improved thermal and electrical performance, and cost-effectiveness. With various types of QFN packages available, designers can choose the most suitable option for their specific application requirements. Understanding the QFN assembly process and the associated challenges is crucial for ensuring proper assembly and reliability of the end product. As electronic devices continue to shrink in size and increase in functionality, QFN packaging is expected to play a vital role in enabling these advancements.
No responses yet