What is a PWM Inverter?
A Pulse Width Modulation (PWM) inverter is a power electronic device that converts direct current (DC) to alternating current (AC) by using a switching technique called Pulse Width Modulation. PWM inverters are widely used in various applications, such as solar power systems, motor drives, uninterruptible power supplies (UPS), and other power conversion systems.
The main function of a PWM inverter is to convert the DC power from sources like batteries, solar panels, or fuel cells into AC power that can be used to power electrical devices and appliances. The PWM technique allows the inverter to control the output voltage and frequency by adjusting the width of the pulses in the switching pattern.
How Does a PWM Inverter Work?
A PWM inverter consists of several key components, including power electronic switches (usually MOSFETs or IGBTs), a DC link capacitor, an output filter, and a control circuit. The basic working principle of a PWM inverter can be described in the following steps:
-
DC to DC Conversion: The input DC voltage is first converted to a higher or lower DC voltage using a DC-to-DC converter, depending on the requirements of the application.
-
Switching: The power electronic switches are turned on and off rapidly according to a specific PWM pattern generated by the control circuit. The PWM pattern determines the width of the pulses, which in turn controls the output voltage and frequency.
-
Filtering: The switched DC voltage is then filtered using an output filter, typically an LC filter, to remove the high-frequency components and produce a smooth AC waveform.
-
Voltage and Frequency Control: The control circuit monitors the output voltage and frequency and adjusts the PWM pattern accordingly to maintain the desired values.
PWM Techniques
There are several PWM techniques used in inverters, each with its own advantages and disadvantages. Some of the most common PWM techniques include:
-
Sinusoidal PWM (SPWM): In this technique, a sinusoidal reference signal is compared with a high-frequency triangular carrier signal to generate the PWM pattern. SPWM is widely used in inverters due to its simplicity and ability to produce a low-distortion output waveform.
-
Space Vector PWM (SVPWM): SVPWM is a more advanced technique that uses a mathematical model to represent the three-phase output voltages as a vector in a two-dimensional plane. This technique offers better DC bus utilization and reduces the harmonic content in the output waveform compared to SPWM.
-
Modified Sinusoidal PWM (MSPWM): MSPWM is a variation of SPWM that uses multiple carrier signals with different phase shifts to reduce the harmonic content in the output waveform. This technique is often used in multilevel inverters to improve the output power quality.
Advantages of PWM Inverters
PWM inverters offer several advantages over other types of inverters, such as square wave and modified square wave inverters. Some of the key benefits of PWM inverters include:
-
High Efficiency: PWM inverters can achieve high conversion efficiencies, typically in the range of 90-95%, due to the reduced switching losses and optimized power electronic components.
-
Low Harmonic Distortion: The output waveform of a PWM inverter closely resembles a pure sinusoidal waveform, with low harmonic distortion. This makes PWM inverters suitable for powering sensitive electronic devices and appliances.
-
Flexible Output Voltage and Frequency Control: PWM inverters allow for precise control over the output voltage and frequency, enabling them to adapt to various load requirements and grid conditions.
-
Compact Size and Light Weight: The high switching frequency used in PWM inverters allows for the use of smaller and lighter passive components, such as inductors and capacitors, resulting in a more compact and lightweight design compared to other types of inverters.
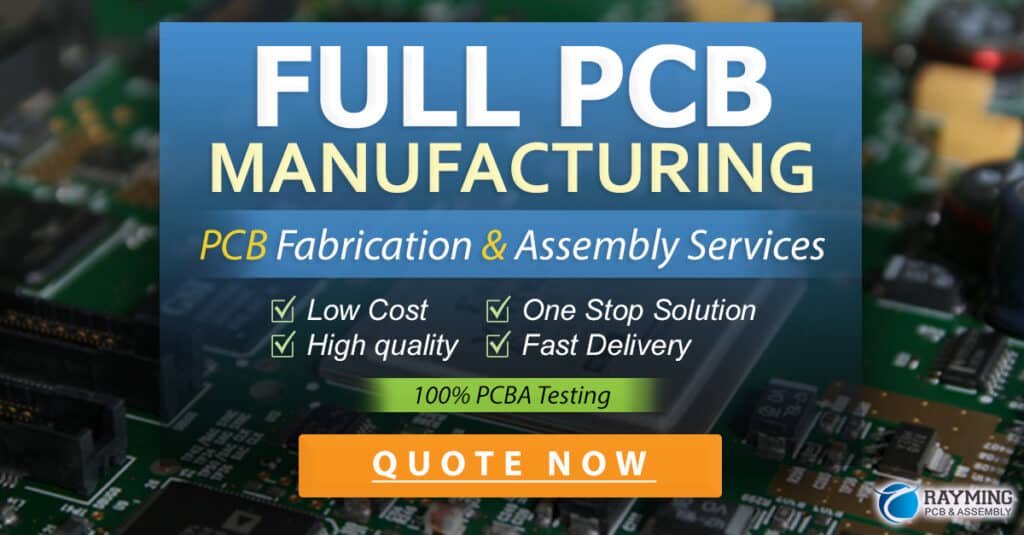
Applications of PWM Inverters
PWM inverters find applications in a wide range of industries and sectors, including:
-
Solar Power Systems: PWM inverters are commonly used in solar power systems to convert the DC power generated by solar panels into AC power that can be fed into the grid or used to power local loads.
-
Motor Drives: PWM inverters are used in motor drive systems to control the speed and torque of AC motors, such as induction motors and permanent magnet synchronous motors (PMSM).
-
Uninterruptible Power Supplies (UPS): PWM inverters are a key component in UPS systems, providing backup power to critical loads during power outages or disturbances.
-
Electric Vehicles (EVs): PWM inverters are used in EV powertrains to convert the DC power from the battery pack into AC power for the electric motor.
-
Renewable Energy Systems: In addition to solar power, PWM inverters are also used in other renewable energy systems, such as wind turbines and fuel cells, to convert the generated DC power into AC power.
Designing a PWM Inverter
Designing a PWM inverter involves several key considerations, including:
-
Power Rating: The first step in designing a PWM inverter is to determine the required power rating based on the intended application and load requirements. This will dictate the choice of power electronic components, such as switches and passive components.
-
Topology Selection: There are several inverter topologies to choose from, such as full-bridge, half-bridge, and multilevel topologies. The choice of topology depends on factors such as power rating, efficiency, cost, and complexity.
-
PWM Technique: The selection of the PWM technique (e.g., SPWM, SVPWM, or MSPWM) will depend on the desired output power quality, control complexity, and efficiency requirements.
-
Component Selection: The power electronic switches, DC link capacitor, output filter components, and control circuitry must be carefully selected based on the power rating, switching frequency, and other design parameters.
-
Thermal Management: Proper thermal management is crucial to ensure the reliable operation and longevity of the PWM inverter. This involves the design of appropriate heatsinks, cooling systems, and thermal interfaces for the power electronic components.
-
Control System Design: The control system for the PWM inverter must be designed to ensure stable and accurate output voltage and frequency control under various operating conditions. This involves the development of control algorithms, feedback systems, and protection mechanisms.
PWM Inverter Market and Future Trends
The global PWM inverter market is expected to grow significantly in the coming years, driven by the increasing adoption of renewable energy systems, electric vehicles, and energy-efficient power conversion solutions. Some of the key market trends and drivers include:
-
Growth in Solar Power: The increasing deployment of solar power systems, both in residential and utility-scale applications, is driving the demand for PWM inverters that can efficiently convert the DC power from solar panels into AC power.
-
Electric Vehicle Adoption: The rapid growth of the electric vehicle market is creating a significant demand for PWM inverters used in EV powertrains, as they play a crucial role in converting the DC power from the battery pack into AC power for the electric motor.
-
Energy Efficiency Regulations: Stringent energy efficiency regulations and standards are driving the adoption of high-efficiency power conversion solutions, such as PWM inverters, in various industries and applications.
-
Advances in Power Electronics: Ongoing advancements in power electronic technologies, such as wide bandgap semiconductors (e.g., SiC and GaN), are enabling the development of more efficient, compact, and reliable PWM inverters.
-
IoT and Smart Grid Integration: The integration of PWM inverters with Internet of Things (IoT) technologies and smart grid systems is enabling remote monitoring, control, and optimization of power conversion systems, leading to improved efficiency and reliability.
Frequently Asked Questions (FAQ)
-
What is the difference between a PWM inverter and a square wave inverter?
A PWM inverter produces an output waveform that closely resembles a pure sinusoidal waveform, with low harmonic distortion. In contrast, a square wave inverter generates a square wave output, which contains higher harmonic content and may not be suitable for powering sensitive electronic devices and appliances. -
Can a PWM inverter be used to power any type of load?
PWM inverters are suitable for powering a wide range of loads, including resistive, inductive, and capacitive loads. However, it is essential to ensure that the inverter’s power rating and output characteristics match the requirements of the specific load to ensure optimal performance and safety. -
What is the typical efficiency of a PWM inverter?
PWM inverters can achieve high conversion efficiencies, typically in the range of 90-95%, depending on the specific design, power rating, and operating conditions. -
How does a PWM inverter control the output voltage and frequency?
A PWM inverter controls the output voltage and frequency by adjusting the width of the pulses in the switching pattern generated by the control circuit. By varying the pulse width, the inverter can regulate the output voltage and maintain a constant frequency. -
What are the main applications of PWM inverters?
PWM inverters find applications in various industries and sectors, including solar power systems, motor drives, uninterruptible power supplies (UPS), electric vehicles (EVs), and renewable energy systems.
Conclusion
PWM inverters are essential power electronic devices that play a crucial role in converting DC power to AC power in various applications. By using advanced switching techniques and control methods, PWM inverters offer high efficiency, low harmonic distortion, and flexible output voltage and frequency control. As the demand for renewable energy systems, electric vehicles, and energy-efficient power conversion solutions continues to grow, the PWM inverter market is expected to witness significant growth in the coming years. With ongoing advancements in power electronic technologies and the integration of IoT and smart grid systems, PWM inverters are poised to become even more efficient, reliable, and versatile in meeting the diverse power conversion needs of the future.
No responses yet