Introduction to Purple PCBs
Purple PCBs, also known as purple printed circuit boards, have gained popularity in recent years due to their unique aesthetic appeal and potential benefits. In this comprehensive guide, we will explore the world of purple PCBs, their manufacturing process, advantages, applications, and frequently asked questions.
What are Purple PCBs?
Purple PCBs are printed circuit boards that feature a distinctive purple color, setting them apart from the traditional green or blue PCBs. The purple color is achieved through a special solder mask that is applied to the surface of the PCB during the manufacturing process.
Why Choose Purple PCBs?
There are several reasons why designers and manufacturers opt for purple PCBs:
- Aesthetic Appeal: Purple PCBs offer a unique and visually striking appearance, making them stand out from conventional PCBs.
- Improved Visibility: The purple color provides better contrast against components and labeling, enhancing visibility during assembly and inspection.
- Potential Performance Benefits: Some manufacturers claim that purple solder masks offer improved thermal and electrical properties compared to traditional solder masks.
Manufacturing Process of Purple PCBs
The manufacturing process of purple PCBs follows similar steps to that of standard PCBs, with the main difference being the application of the purple solder mask.
PCB Fabrication Steps
- Design and Layout: The PCB design is created using specialized software, defining the circuit layout, component placement, and routing.
- Copper Lamination: A thin layer of copper is laminated onto the insulating substrate material, typically FR-4.
- Etching: The unwanted copper areas are removed through a chemical etching process, leaving only the desired circuit traces.
- Drilling: Holes are drilled into the PCB to accommodate through-hole components and vias.
- Plating: The drilled holes are plated with copper to establish electrical connectivity between layers.
- Solder Mask Application: A purple solder mask is applied to the PCB surface, covering the copper traces while leaving the pads and other exposed areas uncovered.
- Silkscreen Printing: Text, symbols, and component indicators are printed onto the solder mask using white or black silkscreen ink.
- Surface Finish: A surface finish, such as HASL (Hot Air Solder Leveling) or ENIG (Electroless Nickel Immersion Gold), is applied to the exposed pads to improve solderability and protect the copper from oxidation.
Purple Solder Mask
The purple solder mask is a key component in the production of purple PCBs. Solder masks are polymer coatings that are applied to the PCB surface to protect the copper traces, prevent solder bridging, and provide electrical insulation.
The purple color is achieved by adding specific pigments to the solder mask material. The exact composition of the purple solder mask may vary depending on the manufacturer and the desired properties.
Advantages of Purple PCBs
Purple PCBs offer several advantages over traditional PCBs:
- Enhanced Visual Inspection: The purple color provides excellent contrast against components and labeling, making it easier to spot defects, solder bridges, or missing components during visual inspection.
- Improved Aesthetics: Purple PCBs have a distinct and attractive appearance, which can be particularly appealing for consumer electronics, gaming devices, or products where visual aesthetics are important.
- Potential Performance Enhancements: Some manufacturers claim that purple solder masks have better thermal and electrical properties, such as improved heat dissipation and reduced signal interference. However, these claims may vary and should be verified with the specific manufacturer.
- Differentiation: Using purple PCBs can help products stand out in the market and create a unique brand identity.
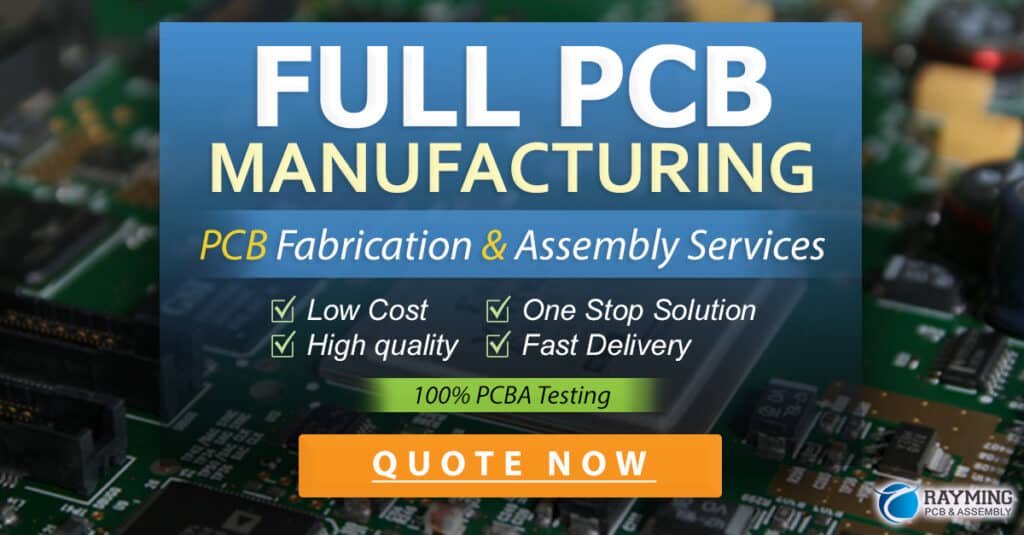
Applications of Purple PCBs
Purple PCBs find applications in various industries and products:
- Consumer Electronics: Purple PCBs are popular in consumer electronics, such as smartphones, tablets, laptops, and gaming devices, where aesthetics and visual appeal are important.
- Automotive Industry: Purple PCBs can be used in automotive electronics, such as infotainment systems, instrument clusters, and advanced driver assistance systems (ADAS).
- Industrial Equipment: Purple PCBs are used in industrial control systems, power electronics, and automation equipment.
- Medical Devices: Purple PCBs can be found in medical devices, such as monitoring systems, diagnostic equipment, and wearable devices.
- Aerospace and Defense: Purple PCBs are used in aerospace and defense applications, including avionics, radar systems, and communication equipment.
Designing with Purple PCBs
When designing a PCB that will be manufactured with a purple solder mask, there are a few considerations to keep in mind:
- Solder Mask Clearance: Ensure that there is sufficient clearance between the solder mask and the exposed pads to allow for proper soldering and component placement.
- Silkscreen Legibility: Choose a silkscreen color (white or black) that provides good contrast against the purple background for optimal legibility.
- Component Selection: Consider the color of the components and how they will appear against the purple PCB. Some components may have a better visual contrast than others.
- Design Rules: Follow the manufacturer’s design guidelines and rules for purple PCBs, including minimum trace width, spacing, and hole sizes.
Frequently Asked Questions (FAQ)
-
Are purple PCBs more expensive than traditional PCBs?
Generally, purple PCBs may have a slightly higher cost compared to standard green or blue PCBs due to the specific solder mask material used. However, the cost difference is usually minimal and varies depending on the manufacturer and order quantity. -
Can purple PCBs be used for all types of applications?
Yes, purple PCBs can be used for a wide range of applications, including consumer electronics, automotive, industrial, medical, and aerospace. They offer the same functionality as traditional PCBs while providing a unique visual appearance. -
Are there any limitations or challenges with purple PCBs?
Purple PCBs may have slightly different processing requirements compared to standard PCBs, such as specific curing temperatures or exposure times for the solder mask. However, experienced PCB manufacturers are well-equipped to handle these requirements and ensure high-quality results. -
Can I mix purple PCBs with other colors in the same product?
Yes, you can use purple PCBs in combination with other color PCBs within the same product. This can create an interesting visual contrast and enhance the overall aesthetics of the device. -
How do I specify the purple color when ordering PCBs?
When placing an order for purple PCBs, you need to specify the desired solder mask color. Most manufacturers have a specific color code or name for their purple solder mask. Communicate your requirements clearly to the manufacturer, and they will guide you through the ordering process.
Conclusion
Purple PCBs offer a unique and visually appealing alternative to traditional green or blue PCBs. With their enhanced aesthetics, improved visibility, and potential performance benefits, purple PCBs have gained popularity across various industries.
By understanding the manufacturing process, advantages, and design considerations of purple PCBs, designers and manufacturers can leverage their benefits and create products that stand out in the market.
As the demand for differentiation and visual appeal continues to grow, purple PCBs are likely to become an increasingly popular choice for a wide range of applications.
No responses yet