Introduction to PCB Surface Finishes
Printed Circuit Boards (PCBs) are the backbone of modern electronics, providing a platform for electrical components to be mounted and interconnected. The surface finish of a PCB plays a crucial role in its performance, reliability, and longevity. PCB surface finishes protect the copper traces from oxidation, enhance solderability, and improve the overall appearance of the board.
In this comprehensive guide, we will explore seven common PCB surface finish types, discussing their pros and cons to help you make an informed decision when choosing the right surface finish for your project.
1. Hot Air Solder Leveling (HASL)
1.1 Overview
Hot Air Solder Leveling (HASL) is one of the most widely used PCB surface finishes. In this process, the PCB is dipped into a molten solder bath, and then hot air is used to level the solder on the surface, creating a uniform coating.
1.2 Pros
- Cost-effective and readily available
- Excellent solderability
- Good shelf life
- Suitable for both through-hole and surface mount components
1.3 Cons
- Uneven surface due to solder pooling
- Not suitable for fine-pitch components
- High thermal stress during the process
- Contains lead (Pb), which is subject to environmental regulations
2. Immersion Tin
2.1 Overview
Immersion tin is a lead-free surface finish that involves depositing a thin layer of tin on the copper surface through a chemical displacement reaction.
2.2 Pros
- Lead-free and RoHS compliant
- Flat surface suitable for fine-pitch components
- Good solderability
- Affordable and easy to apply
2.3 Cons
- Limited shelf life due to tin whiskers formation
- Prone to oxidation over time
- Not suitable for high-temperature applications
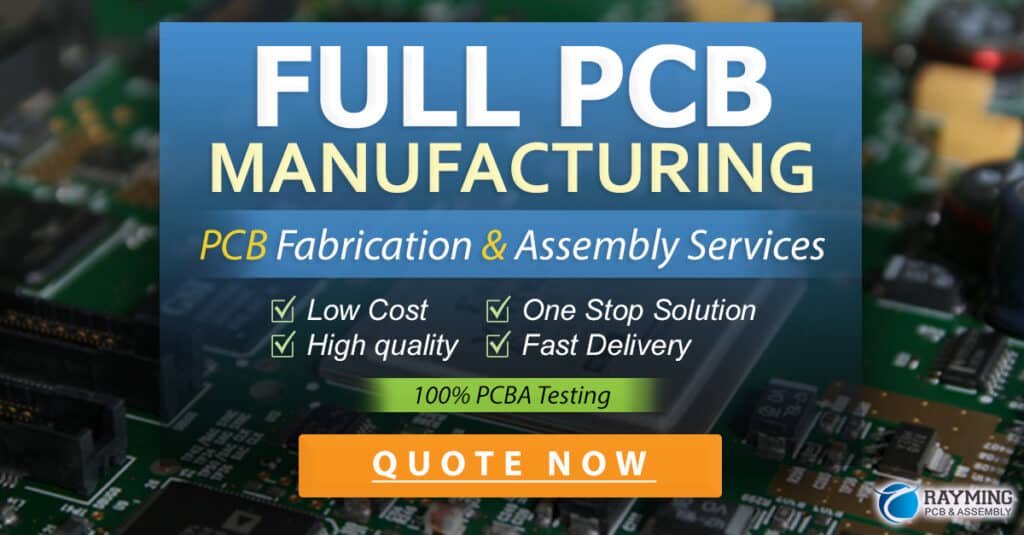
3. Electroless Nickel Immersion Gold (ENIG)
3.1 Overview
Electroless Nickel Immersion Gold (ENIG) is a two-layer surface finish that consists of a nickel underlayer and a thin gold topcoat. The nickel layer provides a barrier against copper diffusion, while the gold layer offers excellent solderability and oxidation resistance.
3.2 Pros
- Excellent solderability and wettability
- Long shelf life
- Suitable for fine-pitch components
- Good oxidation resistance
- Suitable for gold Wire Bonding
3.3 Cons
- Relatively expensive compared to other surface finishes
- Risk of “black pad” defect due to improper plating process
- Gold layer may dissolve into the solder during reflow
4. Immersion Silver
4.1 Overview
Immersion silver is a lead-free surface finish that involves depositing a thin layer of silver on the copper surface through a chemical displacement reaction.
4.2 Pros
- Lead-free and RoHS compliant
- Excellent solderability
- Flat surface suitable for fine-pitch components
- Good electrical conductivity
- Affordable compared to ENIG
4.3 Cons
- Limited shelf life due to silver tarnishing
- Not suitable for high-temperature applications
- Risk of silver migration in high-humidity environments
5. Organic Solderability Preservative (OSP)
5.1 Overview
Organic Solderability Preservative (OSP) is a lead-free surface finish that involves applying a thin, organic compound layer on the copper surface to prevent oxidation.
5.2 Pros
- Lead-free and RoHS compliant
- Cost-effective
- Flat surface suitable for fine-pitch components
- Excellent solderability
- Easy to apply
5.3 Cons
- Limited shelf life (typically 6-12 months)
- Not suitable for multiple reflow cycles
- Sensitive to handling and storage conditions
- Not suitable for gold wire bonding
6. Electroless Nickel Electroless Palladium Immersion Gold (ENEPIG)
6.1 Overview
Electroless Nickel Electroless Palladium Immersion Gold (ENEPIG) is a three-layer surface finish that consists of a nickel underlayer, a palladium middle layer, and a thin gold topcoat. This surface finish combines the benefits of ENIG and the reliability of palladium.
6.2 Pros
- Excellent solderability and wettability
- Long shelf life
- Suitable for fine-pitch components
- Good oxidation resistance
- Suitable for gold wire bonding and press-fit connections
- Reduces the risk of “black pad” defect compared to ENIG
6.3 Cons
- Most expensive surface finish option
- Complex and time-consuming process
- Gold layer may dissolve into the solder during reflow
7. Direct Immersion Gold (DIG)
7.1 Overview
Direct Immersion Gold (DIG) is a surface finish that involves depositing a thin layer of gold directly on the copper surface without a nickel underlayer.
7.2 Pros
- Excellent solderability
- Flat surface suitable for fine-pitch components
- Good oxidation resistance
- Suitable for gold wire bonding
7.3 Cons
- Expensive compared to other surface finishes
- Limited shelf life due to copper diffusion through the gold layer
- Not suitable for multiple reflow cycles
- Risk of brittle solder joints due to copper-tin intermetallic formation
Comparison Table
Surface Finish | Solderability | Shelf Life | Fine-Pitch Suitability | Cost | RoHS Compliant |
---|---|---|---|---|---|
HASL | Excellent | Good | Limited | Low | No |
Immersion Tin | Good | Limited | Suitable | Low | Yes |
ENIG | Excellent | Long | Suitable | High | Yes |
Immersion Silver | Excellent | Limited | Suitable | Medium | Yes |
OSP | Excellent | Limited | Suitable | Low | Yes |
ENEPIG | Excellent | Long | Suitable | Very High | Yes |
DIG | Excellent | Limited | Suitable | High | Yes |
FAQ
1. Which PCB surface finish is the most cost-effective?
Hot Air Solder Leveling (HASL) and Organic Solderability Preservative (OSP) are the most cost-effective PCB surface finishes.
2. Which surface finish is best suited for fine-pitch components?
ENIG, Immersion Silver, OSP, ENEPIG, and DIG are all suitable for fine-pitch components due to their flat surface.
3. Which surface finish has the longest shelf life?
ENIG and ENEPIG have the longest shelf life among the discussed surface finishes.
4. Which surface finish is suitable for gold wire bonding?
ENIG, ENEPIG, and DIG are suitable for gold wire bonding.
5. Which surface finish is RoHS compliant?
All surface finishes except HASL are RoHS compliant, as HASL contains lead (Pb).
Conclusion
Choosing the right PCB surface finish depends on various factors such as cost, solderability, shelf life, component compatibility, and environmental requirements. By understanding the pros and cons of each surface finish type, you can make an informed decision that best suits your project’s needs.
Remember to consider the specific requirements of your application, such as fine-pitch components, gold wire bonding, or multiple reflow cycles, when selecting a surface finish. Additionally, consult with your PCB manufacturer to ensure that the chosen surface finish is compatible with their fabrication process and meets your quality standards.
No responses yet