Introduction to PCB Packaging
Printed circuit board (PCB) packaging refers to the enclosure and protection of PCB assemblies and components. As electronics continue to advance and shrink in size, PCB packaging has become increasingly complex and critical to product performance, reliability, and cost.
PCB designers today have many advanced packaging options available, each with their own advantages and tradeoffs. Understanding the pros and cons of different PCB packaging technologies is essential for making informed design decisions and optimizing products for their intended applications.
Types of Advanced PCB Packaging
Some common types of advanced electronic packaging used for PCBs include:
Ball Grid Arrays (BGAs)
BGAs are surface-mount packaging with a grid of solder balls on the bottom for connection to a PCB. They enable high connection density in a small footprint.
Pros | Cons |
---|---|
High I/O density | Requires precise soldering |
Small size | Limited reworkability |
Good thermal and electrical performance | Higher cost |
Chip-Scale Packages (CSPs)
CSPs are a type of packaging where the package size is not much larger than the die itself. This minimizes package footprint and shortens the connection between the die and PCB.
Pros | Cons |
---|---|
Very small size | Challenging assembly and inspection |
Short interconnects | Requires advanced PCB fabrication |
Lower power consumption | Limited power and thermal dissipation |
Multi-Chip Modules (MCMs)
MCMs combine multiple bare die or packaged ICs into a single package. This improves performance by reducing interconnect lengths between components.
Pros | Cons |
---|---|
High packaging density | Complex and costly design/manufacturing |
Improved electrical performance | Reduced flexibility and upgradeability |
Shared power, ground, thermal | Challenging testing and rework |
System-in-Package (SiP)
SiPs take MCM-like packaging to the next level by integrating multiple die along with passives, MEMs, sensors, antennas or other components into a single package to create a complete system or subsystem.
Pros | Cons |
---|---|
Very high density and small size | Very high design complexity |
Optimized system performance | High development cost and risk |
Enables novel form factors | Supply chain challenges |
3D Packaging
3D packaging technologies like through-silicon vias (TSVs) and package-on-package (PoP) allow vertical stacking of multiple die or packages. This achieves higher density and performance than 2D packaging.
Pros | Cons |
---|---|
Highest density and smallest form factor | Cutting-edge manufacturing required |
Improved bandwidth and power efficiency | Design and simulation challenges |
Enables novel 3D architectures | Thermal and mechanical concerns |
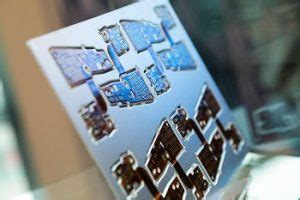
Considerations for Choosing a PCB Packaging Approach
With the variety of packaging options available, PCB designers must carefully weigh multiple factors when selecting the optimal approach for a given product. Key considerations include:
Size and Form Factor Requirements
The target size and shape of the end product is often a primary driver of packaging choice. Applications demanding the smallest possible footprint may require advanced options like CSPs or SiPs. More forgiving spatial requirements may enable lower-cost choices like standard SMT components.
Electrical Performance Needs
Bandwidth, power consumption, and signal integrity needs influence packaging selection. High-speed digital, RF/microwave, and low-power designs can benefit from the short interconnects and low parasitics of CSPs, MCMs, and SiPs. Lower-performance applications may not require such advanced packaging.
Thermal and Power Constraints
The power dissipation and thermal profile of components is a key factor in packaging decisions. High-power components may not be suitable for the dense packaging of MCMs and SiPs without sufficient thermal management. Low-power designs can take better advantage of small packaging.
Reliability and Ruggedness Demands
The operating environment and reliability requirements of a product must be considered in packaging selection. Harsh environments may necessitate the physical robustness of larger packaging options. Applications with extreme reliability needs may favor hermetic ceramic packages over plastic ones.
Manufacturing and Assembly Process
The complexity, precision, and special handling needs of advanced packaging places additional demands on PCB manufacturing and assembly. This can impact process yields, costs, and supplier options. Designers must consider the capabilities of their manufacturing partners when making packaging choices.
Cost Constraints
Advanced packaging options typically come at a higher cost than standard surface-mount. The cost impact of packaging must be weighed against the performance and size benefits it provides. Cost-sensitive products may need to avoid the most advanced packaging technologies.
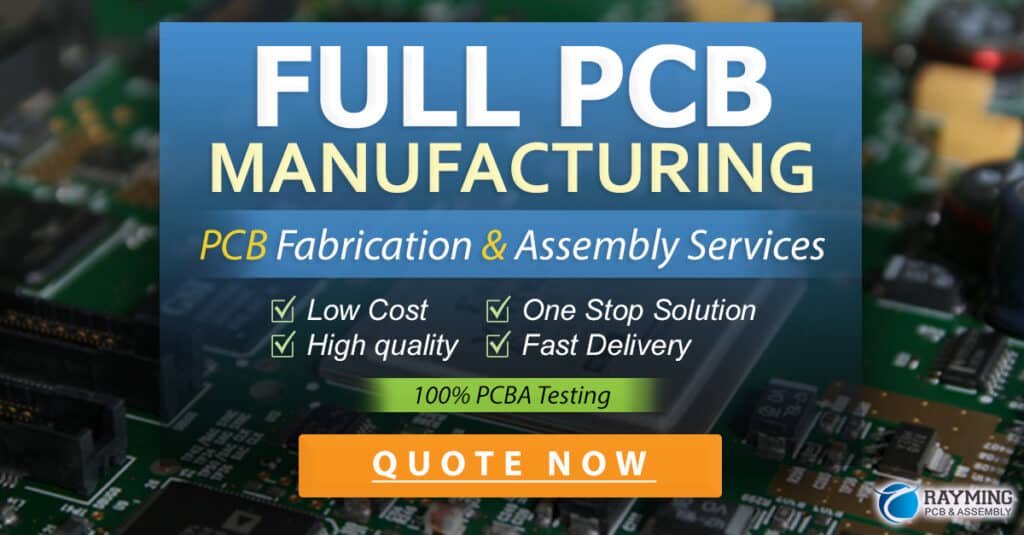
PCB Design Tips for Advanced Packaging
Designing PCBs for advanced component packaging requires meticulous attention to multiple factors beyond basic layout and routing. Some key design considerations include:
Precise Land Pattern Design
The high-density ball, bump, and lead patterns of BGAs, CSPs and other advanced packages leave little room for error in PCB land pattern design. Even slight inaccuracies can compromise assembly yields and reliability. Designers must work from vendor-supplied CAD data and follow strict land pattern design rules.
Escape Routing Strategies
Routing traces to and from fine-pitch advanced packages can be challenging, often requiring high-density HDI PCB technologies like microvias and multiple lamination cycles. Designers must carefully plan ball assignments and escape routing patterns to minimize layers and vias.
Thermal Management Design
The high I/O density of advanced packaging concentrates heat generation into a small area. Careful thermal management design is essential to conduct heat away from the package. Techniques like thermal vias, metal cores, and heat spreaders may be required.
Signal and Power Integrity
The fast edge rates and close proximity of signals in advanced packages make them prone to issues like crosstalk, simultaneous switching noise, and power delivery problems. Rigorous signal and power integrity simulation and design practices are a must.
Design for Manufacturability
Advanced packages are less tolerant of manufacturing process variations than standard SMT components. Designers must be mindful of manufacturability concerns like soldermask registration, via drilling tolerances, and final assembly precision to ensure successful fabrication and assembly.
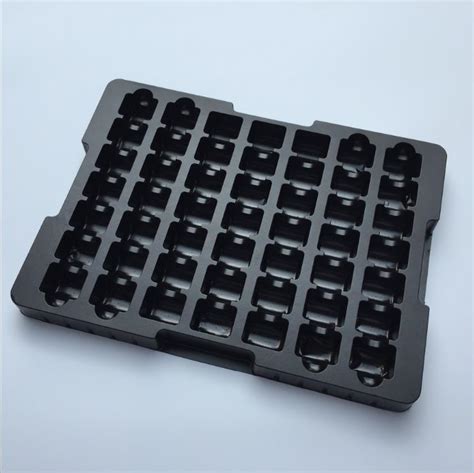
FAQ on Advanced PCB Packaging
What is the most important factor when selecting a PCB packaging approach?
There is no single factor that trumps all others in packaging selection. The optimal approach depends on balancing the specific size, performance, reliability, and cost needs of the application. Designers must weigh the relative importance of each factor for their particular product.
Are advanced packaging technologies suitable for all PCB applications?
No, advanced packaging is not necessary or appropriate for every PCB design. Simple, low-performance applications can often be realized most cost-effectively with standard SMT packaging. Advanced packaging is typically used when extreme constraints in size, performance, or functionality are required.
What are the cost implications of using advanced PCB packaging?
In general, using advanced packaging technologies will increase PCB costs compared to standard SMT assembly. The cost delta depends on the specific packaging used and the production volumes. Advanced packages cost more than standard ones and also require more precise and expensive PCB fabrication and assembly processes.
How do I select a PCB manufacturing partner for advanced packaging designs?
Selecting a manufacturing partner is a key success factor when using advanced packaging. Designers should look for a manufacturer with a proven track record in the specific packaging technologies being used. More advanced options like SiPs and 3D packaging may require a partner on the cutting edge of PCB fabrication capabilities. When in doubt, consult with manufacturers early in the design process to understand their capabilities and design requirements.
Will advanced packaging eliminate the need for PCBs in the future?
While packaging technologies continue to evolve and integrate more system functions, PCBs still play a critical role in most electronic products. Even highly-integrated advanced packages must be mounted to and interconnected with a PCB. Future innovations in packaging may change the nature of PCBs, but are unlikely to eliminate them entirely. Packaging and PCB technologies tend to evolve in tandem to meet the needs of new electronic products.
Conclusion
Advanced electronic packaging technologies offer PCB designers a variety of options for minimizing product size and maximizing performance. Each packaging approach has its own set of advantages and disadvantages that must be carefully considered in the context of a specific application.
Successful implementation of advanced packaging requires a deep understanding of the capabilities and tradeoffs of different technologies and meticulous attention to detail in the PCB design process. By weighing the pros and cons and following design best practices, PCB designers can harness the power of advanced packaging to optimize their products for cost, size, performance, and reliability.
No responses yet