What are 3D-Printed Electronics?
3D-printed electronics refer to electronic devices and components that are fabricated using additive manufacturing techniques. Unlike traditional electronics manufacturing, which involves subtractive processes like etching and drilling, 3D printing builds up objects layer by layer from digital models. This allows for the creation of complex, three-dimensional structures that would be difficult or impossible to make using conventional methods.
There are several different approaches to 3D printing electronics, including:
- Direct Write: This method involves extruding conductive inks or pastes through a nozzle to create circuit traces and interconnects directly on a substrate.
- Inkjet Printing: Similar to direct write, inkjet printing uses a printhead to deposit conductive inks onto a substrate in a precise pattern.
- Stereolithography (SLA): SLA 3D printers use a laser to selectively cure layers of photopolymer resin, which can be infused with conductive materials to create electronic components.
- Fused Deposition Modeling (FDM): FDM printers extrude thermoplastic filaments to build up objects layer by layer. Conductive filaments containing metal particles can be used to print circuit traces and other electronic features.
Method | Materials | Advantages | Disadvantages |
---|---|---|---|
Direct Write | Conductive inks, pastes | High resolution, multi-material | Slow, limited material options |
Inkjet Printing | Conductive inks | Fast, scalable | Lower resolution, limited materials |
Stereolithography | Photopolymer resins | High resolution, smooth surfaces | Expensive, limited conductivity |
Fused Deposition Modeling | Thermoplastic filaments | Low cost, widely available | Lower resolution, limited conductivity |
Advantages of 3D-Printed Electronics
Customization and Rapid Prototyping
One of the biggest advantages of 3D-printed electronics is the ability to quickly and easily customize designs. With traditional manufacturing methods, creating custom electronic components often requires expensive tooling and long lead times. 3D printing allows designers to iterate on their designs rapidly, testing out new ideas and making modifications on the fly.
This rapid prototyping capability is particularly valuable in fields like wearable technology and medical devices, where the ability to create personalized, form-fitting electronics is essential. For example, researchers have used 3D printing to create customized, flexible sensor arrays that can conform to the contours of the human body for applications like motion tracking and health monitoring.
New Form Factors and Functionalities
3D printing also opens up new possibilities for the form and function of electronic devices. Because additive manufacturing is not constrained by the same geometric limitations as subtractive methods, designers can create complex, three-dimensional structures that would be difficult or impossible to make using traditional techniques.
This design freedom has led to the development of novel electronic devices with unique capabilities. For instance, researchers have created 3D-printed antennas with optimized geometries for improved performance, as well as flexible, stretchable electronic circuits that can be integrated into clothing and other wearable items.
Sustainability and Waste Reduction
Another potential benefit of 3D-printed electronics is improved sustainability and reduced waste. Traditional electronics manufacturing often involves the use of hazardous chemicals and generates significant amounts of waste material, such as scrap metal and circuit board trim. In contrast, additive manufacturing processes like 3D printing are generally less wasteful, as they only use the material needed to create the final product.
Furthermore, the ability to 3D print electronics on demand could help to reduce overproduction and inventory waste. Rather than manufacturing large batches of components that may not all be used, companies could print parts as needed, reducing the risk of obsolescence and excess inventory.
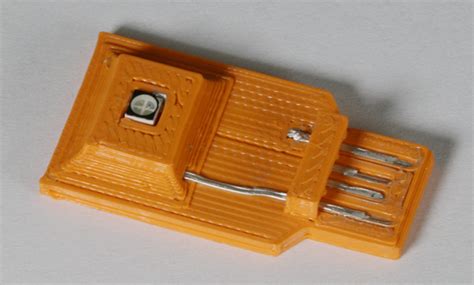
Challenges Facing 3D-Printed Electronics
Despite the many promising applications of 3D-printed electronics, the technology also faces several significant challenges that must be addressed to enable wider adoption and commercialization.
Material Limitations
One of the biggest challenges facing 3D-printed electronics is the limited availability of suitable materials. While there are a growing number of conductive inks, pastes, and filaments on the market, these materials often have lower conductivity and performance compared to traditional electronic materials like copper and gold.
Additionally, many 3D printing materials are not yet optimized for use in electronic applications. For example, some thermoplastic filaments used in FDM printing may have high dielectric constants or other properties that can interfere with electronic functionality.
Resolution and Accuracy
Another challenge for 3D-printed electronics is achieving the necessary resolution and accuracy for complex circuits and components. While some 3D printing methods like direct write and inkjet printing can produce features on the order of microns, this is still larger than the nanoscale features found in advanced integrated circuits.
Moreover, 3D printing processes can be subject to issues like material shrinkage, warping, and misalignment, which can affect the precision and reliability of printed electronic components. Achieving consistent, high-quality results requires careful control of printing parameters and post-processing steps.
Integration and Assembly
Integrating 3D-printed electronic components with other parts of a system can also be challenging. Because 3D-printed electronics often have unique form factors and material properties, they may not be compatible with standard connectors, enclosures, or assembly processes.
Furthermore, the multi-material nature of many 3D-printed electronic devices can make assembly and post-processing more complex. For example, conductive traces printed on a flexible substrate may need to be connected to rigid components like batteries or microcontrollers, requiring specialized bonding or welding techniques.
Scalability and Cost
Finally, the scalability and cost of 3D-printed electronics remain significant barriers to widespread adoption. While 3D printing can be cost-effective for small batches and prototypes, scaling up to mass production levels can be challenging due to slower print speeds and higher material costs compared to conventional manufacturing methods.
Additionally, the cost of 3D printing equipment and materials can be a significant upfront investment for companies looking to adopt the technology. While prices have come down in recent years, high-end 3D printers capable of producing complex electronic devices can still cost hundreds of thousands of dollars.
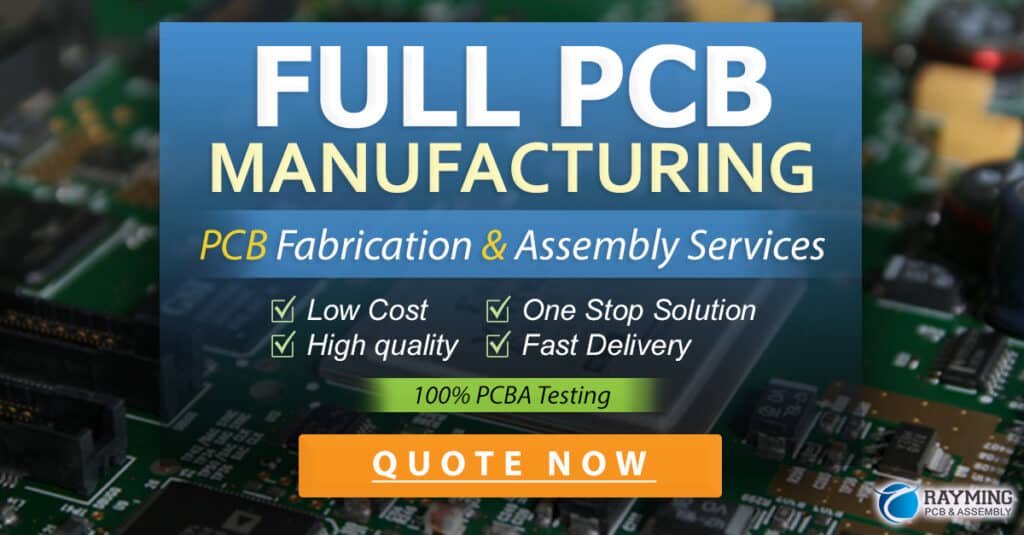
Future Prospects and Research Directions
Despite the challenges outlined above, the future of 3D-printed electronics looks bright. Researchers and companies around the world are working to develop new materials, processes, and applications that could revolutionize the way we design and manufacture electronic devices.
One promising area of research is the development of multi-material 3D printing techniques that can combine conductive and insulating materials in a single print job. This could enable the creation of complex, three-dimensional electronic structures with embedded circuits, sensors, and other components.
Another area of interest is the integration of 3D-printed electronics with other emerging technologies like flexible electronics, energy harvesting, and wireless power transfer. By combining these capabilities, researchers envision a future where electronic devices are not only customizable and adaptable, but also self-powered and able to communicate wirelessly with each other and with the cloud.
Technology | Description | Potential Applications |
---|---|---|
Multi-material 3D printing | Combining conductive and insulating materials in a single print | Embedded sensors, antennas, and circuits |
Flexible electronics | Electronic devices that can bend, stretch, and conform to surfaces | Wearable devices, medical implants, soft robotics |
Energy harvesting | Capturing ambient energy from sources like light, heat, or motion | Self-powered sensors and devices |
Wireless power transfer | Transmitting electrical power wirelessly over short distances | Contactless charging, battery-free devices |
As these technologies mature and converge, we can expect to see a wide range of innovative applications emerge, from smart packaging and interactive displays to biomedical implants and space exploration hardware.
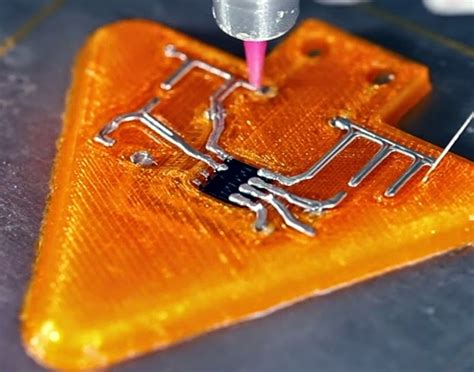
Frequently Asked Questions (FAQ)
Q1: What types of electronic components can be 3D printed?
A1: A variety of electronic components can be 3D printed, including circuit traces, antennas, sensors, batteries, and even simple semiconductor devices like diodes and transistors. However, the complexity and performance of 3D-printed components are generally lower than those produced using traditional manufacturing methods.
Q2: Can 3D-printed electronics be used in high-performance applications?
A2: Currently, 3D-printed electronics are mostly used in low-power, low-frequency applications where high performance is not critical. While researchers are working to improve the conductivity, resolution, and reliability of 3D-printed electronic components, they are not yet suitable for most high-performance applications like computing or telecommunications.
Q3: How do the costs of 3D-printed electronics compare to traditional manufacturing?
A3: The cost of 3D-printed electronics depends on factors like the printing method, materials, and production volume. For small batches and prototypes, 3D printing can be more cost-effective than traditional manufacturing methods that require expensive tooling and setup costs. However, for large-scale production, conventional manufacturing techniques are generally more economical due to faster production speeds and lower material costs.
Q4: What are some of the most promising applications for 3D-printed electronics?
A4: Some of the most promising applications for 3D-printed electronics include:
- Wearable devices and smart clothing
- Medical implants and prosthetics
- Aerospace and defense hardware
- Internet of Things (IoT) sensors and devices
- Robotics and automation components
In these areas, the customization, flexibility, and rapid prototyping capabilities of 3D printing could enable new devices and use cases that are not possible with traditional manufacturing methods.
Q5: What are some of the biggest challenges facing the adoption of 3D-printed electronics?
A5: Some of the biggest challenges facing the adoption of 3D-printed electronics include:
- Limited material options and performance
- Difficulty achieving high resolution and accuracy
- Integration and assembly challenges
- Scalability and cost barriers
- Lack of standardization and design tools
Overcoming these challenges will require ongoing research and development in areas like materials science, process control, and software tools, as well as collaboration between industry, academia, and government stakeholders.
Conclusion
3D-printed electronics represent a promising and rapidly evolving field with the potential to transform the way we design, manufacture, and use electronic devices. From customized wearables to sustainable, on-demand production, 3D printing could enable a wide range of innovative applications and use cases.
However, realizing this potential will require overcoming significant technical, economic, and logistical challenges. Material limitations, resolution and accuracy issues, integration and assembly difficulties, and scalability and cost barriers all pose significant hurdles to the widespread adoption of 3D-printed electronics.
Despite these challenges, the future of 3D-printed electronics looks bright. With ongoing research and development in areas like multi-material printing, flexible electronics, and wireless power transfer, we can expect to see continued progress and innovation in the years ahead.
As the technology matures and becomes more accessible, 3D-printed electronics could help to democratize electronics design and manufacturing, enabling a new generation of inventors, entrepreneurs, and makers to bring their ideas to life. While there is still much work to be done, the promise of 3D-printed electronics is too great to ignore. By investing in this exciting field today, we can lay the foundation for a more innovative, sustainable, and customizable electronic future.
No responses yet