Introduction to Printed Wiring Boards (PWB-AFI)
Printed Wiring Boards (PWBs), also known as Printed Circuit Boards (PCBs), are the backbone of modern electronics. They provide a platform for electrical components to be mounted and interconnected, enabling the creation of complex electronic circuits. PWBs have revolutionized the electronics industry by offering a reliable, compact, and cost-effective solution for electronIC Packaging.
What is a Printed Wiring Board?
A Printed Wiring Board is a flat board made of insulating material, such as fiberglass or plastic, with conductive copper traces printed on its surface. These traces form the electrical connections between components mounted on the board. PWBs can be single-sided (with traces on one side), double-sided (with traces on both sides), or multi-layered (with traces on multiple layers separated by insulating material).
Advantages of Printed Wiring Boards
PWBs offer several advantages over traditional point-to-point wiring:
- Compact size: PWBs allow for the miniaturization of electronic devices by providing a compact platform for component mounting and interconnection.
- Reliability: The copper traces on a PWB are more reliable than point-to-point wiring, as they are less susceptible to breakage or short-circuits.
- Cost-effective: PWBs can be mass-produced using automated processes, making them cost-effective for large-scale production.
- Consistency: PWBs ensure consistent electrical connections between components, reducing the risk of errors in assembly.
PWB Manufacturing Process
The manufacturing process of PWBs involves several steps, each requiring precision and accuracy to ensure the final product meets the desired specifications.
Design and Layout
The first step in PWB manufacturing is the design and layout of the circuit. This involves creating a schematic diagram of the electronic circuit and translating it into a physical layout on the PWB. The layout determines the placement of components and the routing of copper traces between them.
Fabrication
Once the design and layout are finalized, the PWB undergoes the fabrication process. This involves the following steps:
- Substrate preparation: The insulating substrate, typically fiberglass or plastic, is cut to the required size and shape.
- Copper Cladding: A thin layer of copper is bonded to the substrate using heat and pressure.
- Etching: The copper layer is selectively etched away using a photolithographic process to create the desired circuit pattern.
- Drilling: Holes are drilled through the PWB to accommodate through-hole components or to create vias for multi-layer boards.
- Plating: The holes are plated with copper to create electrical connections between layers.
- Solder mask application: A protective solder mask is applied to the PWB to prevent short-circuits and improve solderability.
- Silkscreen printing: Text and symbols are printed on the PWB using silkscreen printing for component identification and assembly instructions.
Assembly
After fabrication, the PWB is ready for component assembly. This involves the following steps:
- Component placement: Components are placed on the PWB either manually or using automated pick-and-place machines.
- Soldering: The components are soldered to the PWB using wave soldering, reflow soldering, or hand soldering techniques.
- Inspection: The assembled PWB is inspected for defects, such as solder bridges, cold solder joints, or missing components.
- Testing: The PWB undergoes functional testing to ensure it performs as intended.
PWB Materials
PWBs can be made from various materials, each with its own properties and advantages.
Substrate Materials
The most common substrate materials used in PWBs are:
- FR-4: A fiberglass-reinforced epoxy laminate, FR-4 is the most widely used substrate material due to its excellent mechanical and electrical properties, as well as its cost-effectiveness.
- Polyimide: Polyimide is a high-performance substrate material with excellent thermal stability and mechanical strength, making it suitable for high-temperature applications.
- Ceramic: Ceramic substrates, such as alumina or beryllia, offer excellent thermal conductivity and electrical insulation, making them suitable for high-power applications.
Conductor Materials
The most common conductor material used in PWBs is copper due to its excellent electrical conductivity and low cost. However, other materials, such as silver or gold, may be used for specialized applications requiring better conductivity or corrosion resistance.
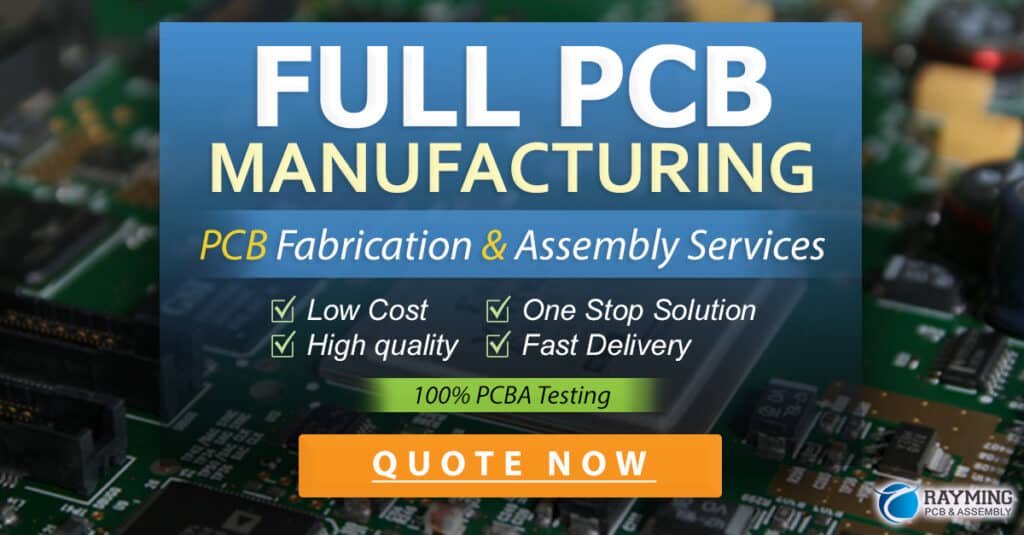
PWB Types
PWBs can be classified based on their construction and intended application.
Single-sided PWBs
Single-sided PWBs have conductive traces on only one side of the substrate. They are the simplest and most cost-effective type of PWB, suitable for low-complexity circuits.
Double-sided PWBs
Double-sided PWBs have conductive traces on both sides of the substrate, allowing for higher component density and more complex circuits. The two sides are connected using through-hole vias.
Multi-layer PWBs
Multi-layer PWBs have conductive traces on multiple layers separated by insulating material. They offer the highest component density and are suitable for complex circuits with high interconnect requirements.
Flexible PWBs
Flexible PWBs use flexible substrate materials, such as polyimide, to create circuits that can bend or fold. They are suitable for applications requiring flexibility or conformity to irregular shapes.
Rigid-Flex PWBs
Rigid-Flex PWBs combine rigid and flexible sections in a single board, offering the benefits of both types. They are suitable for applications requiring both stability and flexibility.
PWB Design Considerations
Designing a PWB involves several considerations to ensure optimal performance, reliability, and manufacturability.
Signal Integrity
Signal integrity refers to the quality of the electrical signals transmitted through the PWB. Factors affecting signal integrity include:
- Trace width and spacing: Traces should be wide enough to carry the required current without excessive resistance, and spaced far enough apart to minimize crosstalk.
- Impedance control: Traces should be designed to have a specific characteristic impedance to minimize reflections and ensure proper signal termination.
- Grounding and shielding: Proper grounding and shielding techniques should be used to minimize electromagnetic interference (EMI) and ensure signal integrity.
Thermal Management
PWBs generate heat during operation, which can affect the performance and reliability of the circuit. Thermal management techniques include:
- Copper pours: Large areas of copper can be used to dissipate heat from high-power components.
- Thermal vias: Vias can be used to transfer heat from one layer to another or to an external heat sink.
- Component placement: Components should be placed in a way that minimizes thermal interactions and allows for adequate cooling.
Manufacturing Considerations
PWB design should take into account the limitations and capabilities of the manufacturing process to ensure manufacturability and minimize costs. Considerations include:
- Minimum feature size: The minimum trace width, spacing, and hole size should be within the capabilities of the manufacturing process.
- Aspect ratio: The ratio of hole depth to diameter should be within the limits of the drilling and plating processes.
- Panelization: PWBs should be designed to fit efficiently on a manufacturing panel to minimize waste and reduce costs.
PWB Testing and Inspection
PWBs undergo various testing and inspection procedures to ensure quality and reliability.
Visual Inspection
Visual inspection is the first step in PWB testing and involves examining the board for obvious defects, such as:
- Solder bridges: Unintended connections between adjacent solder joints.
- Cold solder joints: Solder joints that have not been heated sufficiently, resulting in a weak or unreliable connection.
- Component placement: Incorrect or misaligned component placement.
Automated Optical Inspection (AOI)
AOI uses cameras and image processing software to automatically inspect PWBs for defects. It can detect issues such as missing components, incorrect component placement, and solder defects.
X-ray Inspection
X-ray inspection is used to examine the internal structure of PWBs, particularly for multi-layer boards or boards with hidden components. It can detect issues such as voids in solder joints, broken traces, or misaligned vias.
Electrical Testing
Electrical testing involves applying electrical signals to the PWB and measuring its response to ensure it functions as intended. Types of electrical testing include:
- Continuity testing: Verifying that electrical connections between points on the PWB are intact.
- Insulation testing: Verifying that there are no unintended electrical connections between points on the PWB.
- Functional testing: Verifying that the PWB performs its intended function under various operating conditions.
PWB Applications
PWBs are used in a wide range of applications across various industries.
Consumer Electronics
PWBs are the foundation of most consumer electronic devices, such as:
- Smartphones: PWBs in smartphones house the processors, memory, sensors, and other components that enable the device’s functionality.
- Laptops: PWBs in laptops interconnect the processor, memory, storage, and peripheral devices.
- Televisions: PWBs in televisions control the display, audio, and input/output functions.
Automotive Electronics
PWBs are increasingly used in automotive electronics for applications such as:
- Engine control units: PWBs in engine control units manage the fuel injection, ignition timing, and emission control systems.
- Infotainment systems: PWBs in infotainment systems provide audio, video, and navigation functions.
- Advanced driver assistance systems: PWBs in ADAS enable features such as adaptive cruise control, lane departure warning, and automatic emergency braking.
Medical Electronics
PWBs are used in various medical electronic devices, such as:
- Patient monitors: PWBs in patient monitors acquire, process, and display vital signs such as heart rate, blood pressure, and oxygen saturation.
- Imaging equipment: PWBs in medical imaging equipment, such as X-ray machines or MRI scanners, control the image acquisition and processing functions.
- Implantable devices: PWBs in implantable devices, such as pacemakers or neurostimulators, provide the electrical stimulation and sensing functions.
Industrial Electronics
PWBs are used in industrial electronic applications for control, monitoring, and automation purposes, such as:
- Programmable logic controllers: PWBs in PLCs provide the processing and input/output functions for controlling industrial processes.
- Motor drives: PWBs in motor drives control the speed and torque of electric motors used in industrial machinery.
- Sensors and transducers: PWBs in sensors and transducers convert physical quantities, such as pressure, temperature, or flow, into electrical signals for monitoring and control purposes.
Future Trends in PWB Technology
PWB technology continues to evolve to meet the demands of advancing electronic applications. Some of the future trends in PWB technology include:
High-Density Interconnect (HDI)
HDI PWBs offer higher interconnect density than traditional PWBs, enabling the miniaturization of electronic devices. They use techniques such as microvias, buried vias, and fine-pitch traces to achieve higher component density and improved signal integrity.
Embedded Components
Embedded component technology involves placing passive components, such as resistors or capacitors, inside the PWB substrate rather than on the surface. This saves space, improves reliability, and reduces the number of solder joints required.
3D Printing
3D printing technology is being explored for PWB fabrication, offering the potential for rapid prototyping, customization, and the creation of complex, non-planar structures.
Frequently Asked Questions (FAQ)
- What is the difference between a PWB and a PCB?
-
PWB and PCB are often used interchangeably, but strictly speaking, a PWB refers to the bare board without components, while a PCB refers to the board with components assembled.
-
What is the typical lifespan of a PWB?
-
The lifespan of a PWB depends on factors such as the materials used, the operating environment, and the application. In general, a well-designed and manufactured PWB can last for several years or even decades.
-
Can PWBs be repaired?
-
Yes, PWBs can be repaired, but the feasibility and cost-effectiveness of repair depend on the extent of the damage and the complexity of the board. Common repair techniques include soldering, trace repair, and component replacement.
-
What is the environmental impact of PWB manufacturing?
-
PWB manufacturing involves the use of chemicals and materials that can have an environmental impact if not properly managed. However, the industry is increasingly adopting eco-friendly practices, such as the use of lead-free solders and the recycling of waste materials.
-
How do I choose the right PWB manufacturer?
- When choosing a PWB manufacturer, consider factors such as their experience, capabilities, quality control processes, and customer support. Look for manufacturers with relevant certifications, such as ISO 9001, and ask for references or samples of their work.
Conclusion
Printed Wiring Boards are essential components in modern electronics, providing a reliable and efficient means of interconnecting electronic components. Understanding the fundamentals of PWBs, including their manufacturing process, materials, types, design considerations, testing, and applications, is crucial for anyone involved in electronic product development.
As electronic devices continue to evolve, so too will PWB technology. Advancements in materials, manufacturing processes, and design tools will enable the creation of ever-more complex and miniaturized electronic products.
By staying informed about PWB technology and working with experienced PWB manufacturers, electronic product developers can ensure the reliability, performance, and cost-effectiveness of their products.
No responses yet