Understanding the PCB Making Process
Before we delve into the specifics of how to improve your PCB making, it’s essential to understand the basic steps involved in the process. PCB fabrication typically follows these stages:
- Design: Create a schematic diagram and layout using PCB design software.
- Fabrication: Transfer the design onto a copper-clad board and etch away unwanted copper.
- Drilling: Drill holes for through-hole components and vias.
- Plating: Apply a thin layer of metal, usually copper, to the holes and exposed traces.
- Solder Mask Application: Apply a protective layer over the copper traces, leaving only the pads and holes exposed.
- Silkscreen: Print text and symbols on the board for easy identification of components and orientation.
- Surface Finishing: Apply a final finish, such as HASL, ENIG, or Immersion Silver, to protect the exposed copper and enhance solderability.
- Electrical Testing: Perform electrical tests to ensure the board functions as intended.
PCB Design Best Practices
The success of your PCB largely depends on the quality of your design. Here are some best practices to follow when designing your PCB:
Choose the Right Software
Using the right PCB design software can make a significant difference in the quality and efficiency of your design process. Popular options include:
Software | Vendor | Key Features |
---|---|---|
Altium Designer | Altium | Advanced routing, 3D visualization, simulation |
Eagle | Autodesk | User-friendly interface, extensive part libraries |
KiCad | Open Source | Free, cross-platform, growing community support |
OrCAD | Cadence | Schematic capture, PCB layout, signal integrity analysis |
Consider your specific needs, budget, and skill level when selecting a PCB design software.
Follow the Design Rules
Each PCB manufacturer has its own set of design rules that specify minimum trace widths, clearances, hole sizes, and other parameters. Adhering to these rules ensures that your board can be manufactured reliably and cost-effectively. Some common design rules include:
- Minimum trace width: 0.006″ (0.15mm)
- Minimum clearance between traces: 0.006″ (0.15mm)
- Minimum drill hole size: 0.020″ (0.5mm)
- Minimum annular ring: 0.005″ (0.13mm)
Optimize Component Placement
Proper component placement is crucial for minimizing signal interference, reducing trace lengths, and improving overall board performance. Consider the following when placing components:
- Group related components together to minimize trace lengths
- Place decoupling capacitors close to their associated ICs
- Separate analog and digital circuits to reduce noise coupling
- Provide adequate spacing for heat dissipation and mechanical stress relief
Route with Care
Routing is the process of creating the conductive paths that connect components on your PCB. Proper routing techniques can help minimize signal integrity issues and improve overall board reliability. Some routing best practices include:
- Use the shortest possible trace lengths to minimize signal loss and delay
- Avoid sharp corners and use 45° angles instead to reduce EMI
- Provide adequate trace widths for high-current paths
- Use ground planes to provide a low-impedance return path and reduce noise
PCB Fabrication Considerations
Once your design is complete, it’s time to send it off for fabrication. Here are some factors to consider when choosing a PCB manufacturer and specifying your fabrication requirements:
Material Selection
The choice of PCB substrate material can significantly impact your board’s performance, reliability, and cost. Common PCB materials include:
Material | Dielectric Constant | Dissipation Factor | Thermal Conductivity (W/mK) | Typical Applications |
---|---|---|---|---|
FR-4 | 4.5 | 0.02 | 0.3 | General-purpose, low-cost |
Rogers 4003C | 3.38 | 0.0027 | 0.71 | High-frequency, low-loss |
Polyimide | 3.5 | 0.002 | 0.12 | Flexible, high-temperature |
Aluminum | – | – | 205 | High-power, heat dissipation |
Consider your application’s specific requirements, such as frequency, temperature, and mechanical stress, when selecting a PCB material.
Layer Stack-up
The number and arrangement of layers in your PCB can affect signal integrity, EMI, and manufacturability. When specifying your layer stack-up, consider:
- Using dedicated power and ground planes to reduce noise and improve signal integrity
- Alternating signal layers with ground planes to minimize crosstalk
- Using symmetrical stack-ups to reduce warpage and improve reliability
- Specifying controlled impedance for high-speed signals
Solder Mask and Silkscreen
Solder mask and silkscreen are essential for protecting your PCB and providing clear component identification. When specifying these features, keep in mind:
- Choose a solder mask color that provides good contrast with your silkscreen
- Ensure silkscreen text is legible and properly aligned
- Specify solder mask openings that are slightly larger than the pads to ensure good solder coverage
- Consider using a matte finish solder mask to reduce glare and improve readability
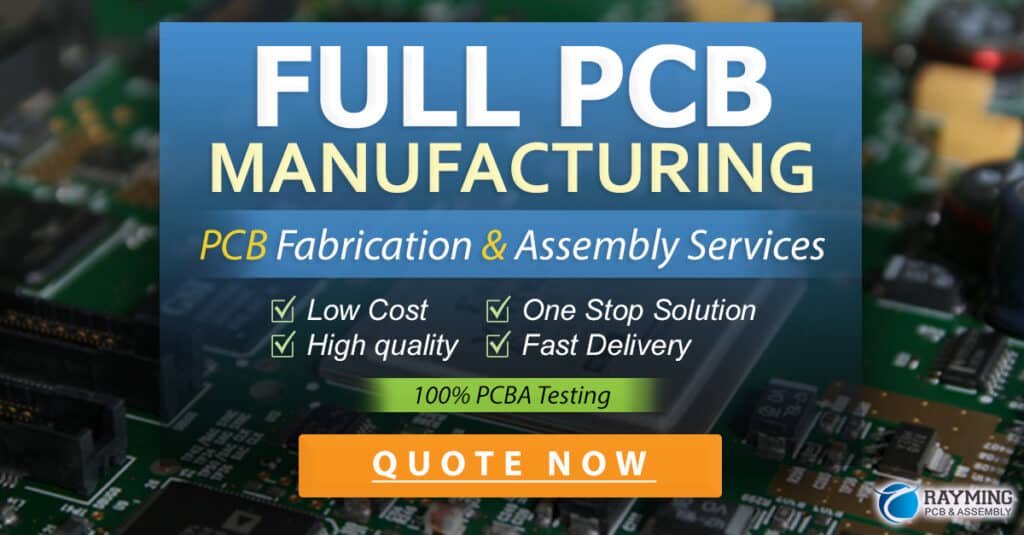
Testing and Verification
Before putting your PCB into production, it’s crucial to thoroughly test and verify its functionality. Some testing methods include:
Visual Inspection
Visually inspect your PCB for any obvious defects, such as:
- Incorrect component placement or orientation
- Solder bridges or shorts
- Incomplete or damaged solder joints
- Damaged or missing components
Electrical Testing
Perform electrical tests to ensure your PCB functions as intended. Common tests include:
- Continuity testing to verify that all connections are intact
- Resistance testing to check for shorts or opens
- Voltage testing to ensure proper power distribution
- Functional testing to verify that the board performs its intended function
In-Circuit Testing (ICT)
ICT involves using a bed-of-nails fixture to access test points on your PCB and verify the presence, orientation, and value of components. ICT can help catch assembly defects early in the production process, reducing costs and improving quality.
Frequently Asked Questions (FAQ)
-
What is the difference between a single-layer and multi-layer PCB?
A single-layer PCB has conductive traces on only one side of the substrate, while a multi-layer PCB has traces on both sides and often includes internal layers for power and ground planes. Multi-layer PCBs offer better signal integrity and higher component density but are more complex and expensive to manufacture. -
How do I choose the right trace width for my PCB?
Trace width depends on several factors, including the current carrying requirements, the desired impedance, and the PCB manufacturing capabilities. As a general rule, use wider traces for high-current paths and narrower traces for high-speed signals. Consult your PCB manufacturer’s design rules and use a trace width calculator to determine the optimal width for your application. -
What is the purpose of a ground plane in a PCB?
A ground plane is a large area of copper that provides a low-impedance return path for electrical currents. Ground planes help reduce electromagnetic interference (EMI), improve signal integrity, and provide shielding between layers. They also help distribute heat evenly across the PCB, improving thermal performance. -
How can I reduce crosstalk between traces on my PCB?
Crosstalk occurs when signals on adjacent traces interfere with each other, causing signal integrity issues. To reduce crosstalk: -
Increase the spacing between traces
- Use guard traces or ground planes between sensitive signals
- Route signals on different layers with ground planes in between
-
Use differential signaling for high-speed signals
-
What is the difference between HASL and ENIG surface finishes?
Hot Air Solder Leveling (HASL) and Electroless Nickel Immersion Gold (ENIG) are two common PCB surface finishes. HASL involves dipping the PCB in molten solder, while ENIG applies a thin layer of nickel and gold to the exposed copper. ENIG provides better planarity and a longer shelf life but is more expensive than HASL. HASL is more suitable for through-hole components and is less expensive, but can result in uneven surfaces and shorter shelf life.
Conclusion
Creating high-quality, reliable PCBs requires a combination of careful design, appropriate material selection, and thorough testing. By following best practices in PCB design, fabrication, and assembly, you can minimize errors, reduce costs, and improve the overall performance of your electronic devices.
Remember to choose the right PCB design software, adhere to design rules, optimize component placement and routing, select appropriate materials and manufacturing specifications, and thoroughly test your boards before putting them into production.
As technology continues to advance, staying up-to-date with the latest PCB design and manufacturing techniques will be essential for creating better, more innovative electronic products. By continuously learning and adapting to new challenges, you can stay ahead of the curve and create PCBs that push the boundaries of what’s possible in the world of electronics.
No responses yet