Introduction to Printed and Flexible Electronics
Printed and flexible electronics, also known as Printed-Flexible-Electronics, represent a groundbreaking technology that has revolutionized the way we think about electronic devices. This innovative field combines the principles of traditional electronics with the versatility of printing techniques, enabling the creation of lightweight, flexible, and cost-effective electronic components and devices.
What are Printed and Flexible Electronics?
Printed and flexible electronics refer to the process of creating electronic devices and circuits using printing methods, such as screen printing, inkjet printing, and gravure printing, on flexible substrates like plastic, paper, or fabric. This technology allows for the fabrication of thin, bendable, and stretchable electronic components that can be integrated into a wide range of applications.
Advantages of Printed and Flexible Electronics
Compared to conventional rigid electronics, printed and flexible electronics offer several key advantages:
-
Flexibility and Stretchability: Printed Electronics can be fabricated on flexible substrates, allowing for the creation of bendable, rollable, and stretchable devices that can conform to various shapes and surfaces.
-
Lightweight and Thin: Printed electronic components are typically much thinner and lighter than their rigid counterparts, making them ideal for portable and wearable applications.
-
Cost-Effective: The use of printing techniques and readily available substrates enables the mass production of printed electronics at a lower cost compared to traditional manufacturing methods.
-
Large-Area Fabrication: Printing methods allow for the fabrication of electronic devices over large areas, opening up new possibilities for applications such as smart packaging, large-area sensors, and flexible displays.
Materials and Fabrication Techniques
Conductive Inks and Materials
One of the key components in printed and flexible electronics is the use of conductive inks and materials. These inks contain conductive particles, such as silver, copper, or carbon nanotubes, dispersed in a liquid medium. When printed onto a substrate and cured, the ink forms conductive traces and patterns that enable the flow of electricity.
Types of Conductive Inks
-
Silver Inks: Silver-based inks are widely used in printed electronics due to their high conductivity and stability. They can be formulated for various printing methods and offer excellent electrical performance.
-
Copper Inks: Copper inks provide a cost-effective alternative to silver inks while maintaining good conductivity. However, they require additional processing steps to prevent oxidation.
-
Carbon-Based Inks: Carbon-based inks, such as carbon nanotubes and graphene, offer unique properties like flexibility, transparency, and high mechanical strength. They are suitable for applications that require these specific characteristics.
Printing Techniques
Several printing techniques have been adapted for the fabrication of printed and flexible electronics:
-
Screen Printing: Screen printing involves pushing ink through a patterned mesh screen onto the substrate. It is a versatile method that can deposit thick layers of ink and is suitable for printing on various substrates.
-
Inkjet Printing: Inkjet printing uses a digital-controlled printhead to deposit tiny droplets of ink onto the substrate. It offers high resolution and allows for precise patterning of conductive traces.
-
Gravure Printing: Gravure printing utilizes an engraved cylinder to transfer ink onto the substrate. It is a high-speed printing method that enables the production of large volumes of printed electronics.
-
Flexographic Printing: Flexographic printing employs a flexible relief plate to transfer ink onto the substrate. It is well-suited for printing on flexible substrates and can achieve high printing speeds.
Substrate Materials
The choice of substrate material is crucial in printed and flexible electronics, as it determines the flexibility, durability, and compatibility with the printing process. Common substrate materials include:
-
Plastic Films: Plastic films, such as polyethylene terephthalate (PET) and polyimide (PI), are widely used substrates due to their flexibility, transparency, and thermal stability.
-
Paper: Paper-based substrates offer biodegradability and low cost, making them attractive for disposable and eco-friendly applications.
-
Textiles: Printing electronics on textiles enables the integration of electronic functionality into clothing and wearable devices.
-
Elastomers: ElastomerIC Substrates, such as polydimethylsiloxane (PDMS), provide stretchability and conformability, allowing for the creation of stretchable electronic devices.
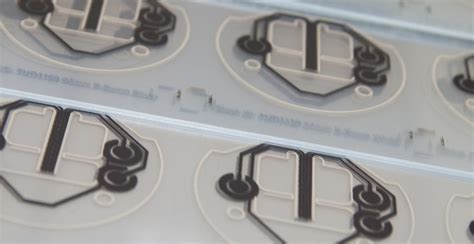
Applications of Printed and Flexible Electronics
Printed and flexible electronics find applications in various domains, ranging from consumer electronics to healthcare and beyond.
Wearable Electronics
Wearable electronics, such as smartwatches, fitness trackers, and smart clothing, benefit greatly from printed and flexible electronics technology. By integrating thin and flexible sensors, circuits, and displays into wearable devices, manufacturers can create comfortable and unobtrusive products that seamlessly integrate with the human body.
Examples of Wearable Electronics
-
Smart Textiles: Printed electronics can be integrated into fabrics to create smart textiles that can monitor vital signs, track physical activity, or provide interactive functionality.
-
Flexible Sensors: Flexible sensors, such as strain gauges and Temperature Sensors, can be printed directly onto clothing or skin, enabling continuous monitoring of physiological parameters.
-
Wearable Displays: Flexible displays, such as organic light-emitting diode (OLED) displays, can be integrated into wearable devices, providing a thin and lightweight visual interface.
Healthcare and Medical Devices
Printed and flexible electronics have significant potential in the healthcare and medical device industry. By leveraging the flexibility and biocompatibility of printed electronics, researchers and manufacturers can develop innovative medical devices and diagnostic tools.
Examples of Healthcare Applications
-
Flexible Biosensors: Printed biosensors can be used for non-invasive monitoring of various biomarkers, such as glucose, lactate, or electrolytes, enabling continuous health monitoring and early disease detection.
-
Wearable Drug Delivery Systems: Flexible drug delivery patches can be designed using printed electronics, allowing for controlled and localized drug release.
-
Implantable Devices: Printed and flexible electronics can be used to create thin and conformable implantable devices, such as neural interfaces or retinal implants, that can interact with biological tissues.
Consumer Electronics and Displays
Printed and flexible electronics are transforming the consumer electronics landscape by enabling the development of innovative and user-friendly devices.
Examples of Consumer Electronics Applications
-
Flexible Displays: Printed and flexible displays, such as OLED and electrophoretic displays, offer thin, lightweight, and bendable alternatives to traditional rigid displays. They find applications in smartphones, tablets, and wearable devices.
-
Printed RFID Tags: Printed radio-frequency identification (RFID) tags can be used for item tracking, Inventory Management, and smart packaging applications.
-
Flexible Solar Cells: Printed and flexible solar cells can be integrated into consumer electronics, providing a portable and renewable power source for devices.
Automotive and Transportation
Printed and flexible electronics are finding their way into the automotive and transportation industries, enabling the integration of electronic functionality into various components and surfaces.
Examples of Automotive Applications
-
In-Vehicle Displays: Flexible displays can be integrated into car interiors, providing interactive and conformable user interfaces for infotainment systems and instrument clusters.
-
Smart Sensors: Printed sensors can be used for monitoring various parameters in vehicles, such as tire pressure, temperature, and strain, enhancing safety and performance.
-
Lightweight Wiring: Printed conductive traces can replace traditional wiring harnesses, reducing weight and improving fuel efficiency in vehicles.
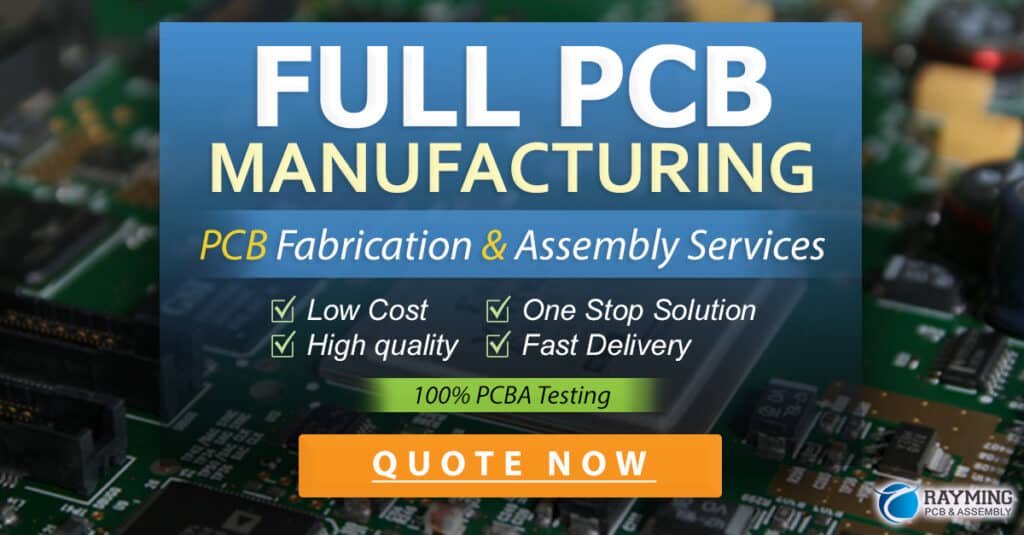
Challenges and Future Outlook
While printed and flexible electronics offer numerous advantages and applications, there are still challenges to be addressed for widespread adoption:
-
Material Development: Continued research and development of conductive inks, substrates, and other materials are necessary to improve performance, stability, and compatibility with various printing techniques.
-
Standardization: Establishing industry standards for materials, processes, and performance metrics is crucial for ensuring consistency and reliability in printed and flexible electronics manufacturing.
-
Integration with Conventional Electronics: Seamless integration of printed and flexible electronics with conventional rigid electronics is essential for creating hybrid systems that leverage the strengths of both technologies.
-
Scalability and Manufacturing: Scaling up printed electronics manufacturing to industrial levels while maintaining quality and reliability remains a challenge. Advancements in printing techniques and process control are necessary for mass production.
Despite these challenges, the future outlook for printed and flexible electronics is promising. As research progresses and new materials and techniques emerge, we can expect to see an increasing number of applications and products that leverage the unique properties of printed and flexible electronics.
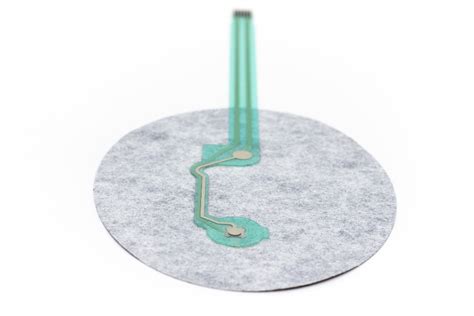
Frequently Asked Questions (FAQ)
-
What are the key benefits of printed and flexible electronics compared to traditional rigid electronics?
Printed and flexible electronics offer several advantages, including flexibility, stretchability, lightweight, thinness, cost-effectiveness, and the ability to fabricate large-area devices. -
What are some common printing techniques used in printed and flexible electronics?
Common printing techniques used in printed and flexible electronics include screen printing, inkjet printing, gravure printing, and flexographic printing. Each technique has its own advantages and is suitable for different applications. -
What are the main application areas for printed and flexible electronics?
Printed and flexible electronics find applications in various domains, such as wearable electronics, healthcare and medical devices, consumer electronics, displays, automotive, and transportation. They enable the development of innovative and user-friendly products. -
What are the challenges in the widespread adoption of printed and flexible electronics?
Some of the challenges in the widespread adoption of printed and flexible electronics include material development, standardization, integration with conventional electronics, and scalability and manufacturing. Continued research and advancements are necessary to overcome these challenges. -
What is the future outlook for printed and flexible electronics?
The future outlook for printed and flexible electronics is promising. As research progresses and new materials and techniques emerge, we can expect to see an increasing number of applications and products that leverage the unique properties of printed and flexible electronics. The technology has the potential to revolutionize various industries and create new opportunities for innovation.
Conclusion
Printed and flexible electronics represent a transformative technology that is reshaping the way we design, manufacture, and interact with electronic devices. By combining the principles of traditional electronics with the versatility of printing techniques and flexible substrates, printed and flexible electronics enable the creation of lightweight, conformable, and cost-effective electronic components and devices.
From wearable electronics and healthcare devices to consumer electronics and automotive applications, printed and flexible electronics are finding their way into various domains, offering unique advantages and possibilities. As research advances and challenges are addressed, we can anticipate a future where printed and flexible electronics become an integral part of our daily lives, enabling innovative products and solutions that enhance our experiences and improve our quality of life.
Application Domain | Examples |
---|---|
Wearable Electronics | Smart textiles, flexible sensors, wearable displays |
Healthcare and Medical Devices | Flexible biosensors, wearable drug delivery systems, implantable devices |
Consumer Electronics and Displays | Flexible displays, printed RFID tags, flexible solar cells |
Automotive and Transportation | In-vehicle displays, smart sensors, lightweight wiring |
As the field of printed and flexible electronics continues to evolve, it is essential for researchers, manufacturers, and stakeholders to collaborate and address the challenges associated with material development, standardization, integration, and scalability. By doing so, we can unlock the full potential of this exciting technology and pave the way for a future where printed and flexible electronics become a ubiquitous part of our technology landscape.
No responses yet