What is Press Fit?
Press fit, also known as interference fit or friction fit, is a fastening method that relies on the friction between two mating parts to create a secure joint without the use of additional fasteners or adhesives. This technique is widely used in various industries, including automotive, aerospace, electronics, and manufacturing, due to its simplicity, reliability, and cost-effectiveness.
In a press fit assembly, the mating parts are designed with slightly different dimensions, such that the outer diameter of one part (the shaft or pin) is slightly larger than the inner diameter of the other part (the hole or bore). When the parts are forced together under high pressure, the interference between the surfaces creates a strong, permanent joint that can withstand significant mechanical stress and vibration.
Advantages of Press Fit
Press fit offers several advantages over other fastening methods, such as welding, riveting, or bolting:
- Simplicity: Press fit assemblies require no additional fasteners or adhesives, reducing the number of components and simplifying the assembly process.
- Cost-effectiveness: By eliminating the need for extra parts and reducing assembly time, press fit can significantly lower production costs.
- Reliability: When designed and executed correctly, press fit joints are highly reliable and can withstand harsh operating conditions, such as high temperatures, vibrations, and mechanical stresses.
- Compact design: Press fit allows for more compact and lightweight designs, as there is no need for flanges, bolts, or other protruding features.
- Excellent conductivity: Press fit joints provide excellent electrical and thermal conductivity, making them ideal for applications in electronics and heat transfer.
Types of Press Fit
There are several types of press fit, each suited for different applications and materials:
Cylindrical Press Fit
Cylindrical press fit is the most common type, involving a cylindrical shaft or pin being inserted into a circular hole. The interference between the parts is typically between 0.001 to 0.003 inches (0.025 to 0.076 mm) per inch of diameter, depending on the materials and desired strength of the joint.
Tapered Press Fit
In a tapered press fit, the shaft and hole have a slight taper, typically between 1:50 and 1:200. This allows for easier assembly and disassembly compared to cylindrical press fit, as the parts can be gradually engaged or separated. Tapered press fit is often used in applications where occasional disassembly is required, such as in machine tool spindles.
Splined Press Fit
Splined press fit involves a shaft with multiple equally spaced teeth (splines) that mesh with corresponding grooves in the hole. This type of press fit provides additional resistance to rotational forces and is commonly used in power transmission applications, such as gears and shafts.
Knurled Press Fit
Knurled press fit uses a shaft with a textured surface, featuring a pattern of raised diamond-shaped or straight-line protrusions. These protrusions dig into the surface of the hole during assembly, creating a strong, permanent joint. Knurled press fit is often used in applications where high torque resistance is required, such as in automotive steering columns.
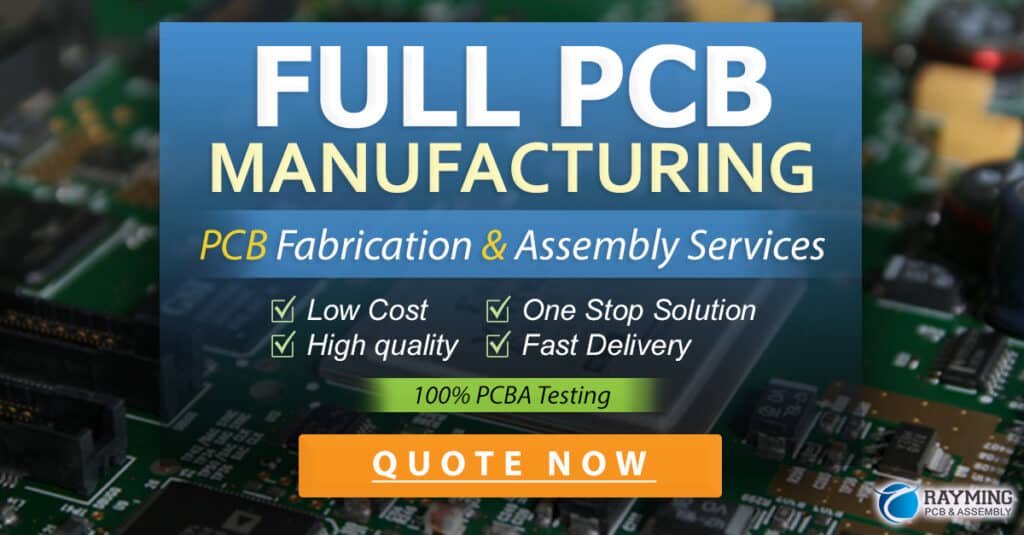
Designing for Press Fit
To ensure a successful press fit assembly, several key factors must be considered during the design process:
Material Selection
The materials chosen for the mating parts should have compatible mechanical properties, such as hardness, elasticity, and thermal expansion. Common material combinations for press fit include:
- Steel shaft and aluminum hole
- Stainless steel shaft and plastic hole
- Brass shaft and steel hole
The shaft material should be harder than the hole material to ensure that the shaft can deform the hole during assembly without being permanently damaged itself.
Interference and Tolerance
The interference between the mating parts is the key to a strong press fit joint. The optimal interference depends on the materials, dimensions, and desired strength of the joint. Too little interference may result in a weak or loose fit, while too much interference can cause excessive stress and damage to the parts during assembly.
Typical interference values range from 0.0005 to 0.003 inches (0.013 to 0.076 mm) per inch of diameter, with higher values used for softer materials and lower values for harder materials. The tolerance on the interference should be carefully controlled to ensure consistent joint strength across multiple assemblies.
Surface Finish and Lubrication
The surface finish of the mating parts can significantly affect the strength and reliability of the press fit joint. A smooth, polished surface can reduce friction and galling during assembly, while a rougher surface can increase the holding power of the joint.
Lubrication can also be used to facilitate assembly and reduce galling, especially for harder materials or larger interference values. Common lubricants include oil, grease, and dry film lubricants, such as molybdenum disulfide.
Assembly Process
The assembly process for press fit joints typically involves the use of a hydraulic or mechanical press to apply a controlled, uniform force to the mating parts. The press should be sized appropriately for the parts being assembled, with sufficient capacity to overcome the interference and seat the parts fully.
The assembly should be performed in a clean, controlled environment to prevent contamination of the mating surfaces. The parts should be properly aligned before pressing to ensure a straight, concentric fit. In some cases, heating the hole or cooling the shaft can be used to temporarily expand or contract the parts, making assembly easier.
Quality Control and Testing
To ensure the reliability and consistency of press fit assemblies, proper quality control and testing procedures should be implemented:
Visual Inspection
Visual inspection of the mating parts before assembly can help identify any defects or irregularities that may affect the quality of the joint, such as burrs, nicks, or surface contamination.
Dimensional Verification
The dimensions of the mating parts should be verified before assembly to ensure that the interference and tolerance requirements are met. This can be done using precision measuring tools, such as micrometers, calipers, or coordinate measuring machines (CMMs).
Pull-Out and Push-Out Testing
Pull-out and push-out tests can be performed on sample assemblies to evaluate the strength and holding power of the press fit joint. In a pull-out test, an axial force is applied to the shaft until it separates from the hole, while in a push-out test, the shaft is forced out of the hole using a hydraulic or mechanical press. The force required to separate the parts is recorded and compared to the design specifications.
Non-Destructive Testing
Non-destructive testing methods, such as ultrasonic inspection or X-ray imaging, can be used to evaluate the integrity of press fit joints without damaging the parts. These methods can detect internal defects, such as cracks, voids, or incomplete seating, that may not be visible through visual inspection.
Press Fit Applications
Press fit is used in a wide range of applications across various industries, including:
Automotive
- Transmission gears
- Steering columns
- Suspension components
- Brake system components
Aerospace
- Turbine engine components
- Landing gear assemblies
- Structural fasteners
- Hydraulic system components
Electronics
- Connector pins
- Heat sink assemblies
- Transformer cores
- Electric motor components
Manufacturing
- Machine tool spindles
- Bearing assemblies
- Shaft couplings
- Pulleys and sprockets
Troubleshooting Press Fit Issues
Despite careful design and quality control, issues can sometimes arise with press fit assemblies. Common problems and their solutions include:
Incomplete Seating
If the shaft is not fully seated in the hole, it may result in a weak or loose joint. This can be caused by insufficient assembly force, misalignment, or contamination of the mating surfaces. To resolve this issue, the parts should be disassembled, cleaned, and reassembled with proper alignment and force.
Galling or Seizure
Galling or seizure can occur when the mating surfaces experience excessive friction during assembly, causing localized welding or tearing of the material. This can be prevented by using appropriate lubrication, reducing the interference, or improving the surface finish of the parts.
Crack Formation
Excessive interference or improper material selection can cause cracks to form in the hole during assembly, weakening the joint and potentially leading to failure. To prevent cracking, the interference should be carefully selected based on the material properties, and the parts should be inspected for defects before assembly.
Relaxation or Creep
Over time, the holding power of a press fit joint may decrease due to relaxation or creep of the materials, especially in applications with high temperatures or sustained mechanical stress. This can be mitigated by using materials with good creep resistance, such as certain grades of stainless steel or titanium, and by designing the joint with sufficient initial interference to compensate for potential relaxation.
Frequently Asked Questions
1. What is the difference between press fit and shrink fit?
Press fit and shrink fit are similar in that they both rely on interference between mating parts to create a secure joint. However, in a shrink fit, the hole is heated to expand its diameter before assembly, allowing the shaft to be inserted easily. As the hole cools and contracts, it creates a strong interference fit. Press fit, on the other hand, relies on mechanical force to assemble the parts at room temperature.
2. Can press fit be used with dissimilar materials?
Yes, press fit can be used with dissimilar materials, as long as the materials are compatible in terms of their mechanical properties and thermal expansion coefficients. Common dissimilar material combinations include steel shafts with aluminum or plastic holes, and brass shafts with steel holes.
3. How do I calculate the interference for a press fit assembly?
The optimal interference for a press fit assembly depends on several factors, including the materials, dimensions, and desired strength of the joint. As a general rule of thumb, the interference should be between 0.001 to 0.003 inches (0.025 to 0.076 mm) per inch of diameter for most applications. More precise calculations can be made using specialized software or by consulting engineering references, such as the Machinery’s Handbook.
4. Can press fit joints be disassembled?
Press fit joints are typically designed to be permanent and are not intended for disassembly. However, in some cases, controlled heating of the hole or cooling of the shaft can be used to temporarily expand or contract the parts, allowing for disassembly without damage. Tapered press fits are also easier to disassemble than cylindrical press fits, as the parts can be gradually separated by applying an axial force.
5. What is the typical press fit assembly process?
The typical press fit assembly process involves the following steps:
- Clean and inspect the mating parts to ensure they are free of defects and contamination.
- Apply lubrication to the mating surfaces, if necessary.
- Align the parts in a hydraulic or mechanical press, ensuring they are concentric and perpendicular.
- Apply a controlled, uniform force to the parts until the shaft is fully seated in the hole.
- Verify the quality of the assembly through visual inspection, dimensional checks, and/or non-destructive testing.
Conclusion
Press fit is a versatile and reliable fastening method that offers numerous advantages over other joining techniques, including simplicity, cost-effectiveness, and excellent mechanical and thermal properties. By carefully designing the mating parts, selecting appropriate materials and lubricants, and controlling the assembly process, engineers can create strong, durable press fit joints for a wide range of applications.
As with any manufacturing process, proper quality control and testing are essential to ensure the consistency and reliability of press fit assemblies. Visual inspection, dimensional verification, pull-out and push-out testing, and non-destructive evaluation can help identify and prevent potential issues before they lead to failures in the field.
By understanding the principles, techniques, and best practices associated with press fit, engineers and manufacturers can leverage this powerful joining method to create high-quality, reliable products that meet the demands of today’s complex and challenging applications.
No responses yet