Introduction to Prepreg and PCB Core
In the world of printed circuit board (PCB) manufacturing, two essential materials play a crucial role in determining the quality, reliability, and performance of the final product: prepreg and PCB core. These materials form the foundation of Multilayer PCBs, providing the necessary insulation, mechanical strength, and dimensional stability. Understanding the differences between prepreg and PCB core is crucial for designers, engineers, and manufacturers to make informed decisions when creating high-quality PCBs.
What is Prepreg?
Prepreg, short for pre-impregnated, is a composite material consisting of a reinforcement fabric, such as glass fiber, impregnated with a partially cured thermosetting resin, typically epoxy. The resin is partially cured, or “B-staged,” which means it is in a semi-solid state, allowing for easy handling and storage. Prepreg is used as an insulating layer between the conductive layers of a multilayer PCB, providing both electrical insulation and mechanical bonding.
What is PCB Core?
PCB core, also known as the substrate or base material, is a fully cured, rigid material that serves as the foundation for the conductive layers of a PCB. It is typically made of a glass fiber reinforced epoxy laminate, such as FR-4, which offers excellent mechanical and electrical properties. The core provides the necessary stability and support for the copper traces and other components that make up the functional part of the PCB.
Prepreg vs. Core: Key Differences
Composition and Structure
One of the main differences between prepreg and PCB core lies in their composition and structure. Prepreg is a composite material consisting of a reinforcement fabric impregnated with a partially cured resin, while PCB core is a fully cured, rigid laminate material.
Material | Composition | Structure |
---|---|---|
Prepreg | Reinforcement fabric (e.g., glass fiber) impregnated with partially cured resin (e.g., epoxy) | Partially cured, semi-solid state |
PCB Core | Glass fiber reinforced epoxy laminate (e.g., FR-4) | Fully cured, rigid laminate |
Curing State
Another key difference between prepreg and PCB core is their curing state. Prepreg is partially cured, or “B-staged,” which means the resin is in a semi-solid state. This allows for easy handling, storage, and flexibility during the PCB manufacturing process. On the other hand, PCB core is fully cured, resulting in a rigid and stable material that serves as the foundation for the conductive layers.
Function in PCB Manufacturing
Prepreg and PCB core serve different functions in the PCB manufacturing process. Prepreg is used as an insulating layer between the conductive layers of a multilayer PCB, providing both electrical insulation and mechanical bonding. It also helps to fill any gaps or voids between the layers, ensuring a strong and reliable connection.
PCB core, on the other hand, serves as the base material for the conductive layers. It provides the necessary stability and support for the copper traces and other components, ensuring the overall integrity of the PCB.
Electrical and Mechanical Properties
Prepreg and PCB core also differ in their electrical and mechanical properties. Prepreg, being a partially cured material, has a lower dielectric constant and loss tangent compared to PCB core. This makes it an excellent choice for high-frequency applications where signal integrity is critical.
PCB core, such as FR-4, offers a balance of good electrical properties and mechanical strength. It has a higher dielectric constant and loss tangent compared to prepreg, but it provides the necessary rigidity and stability for the PCB.
Property | Prepreg | PCB Core (FR-4) |
---|---|---|
Dielectric Constant | Lower | Higher |
Loss Tangent | Lower | Higher |
Mechanical Strength | Lower | Higher |
Thermal Stability | Lower | Higher |
Thickness and Availability
Prepreg and PCB core also differ in terms of their thickness and availability. Prepreg is typically available in thinner sheets, ranging from 0.002″ to 0.006″ (0.05mm to 0.15mm), which allows for the creation of thinner multilayer PCBs. It is also available in a variety of glass styles and resin systems, providing designers with more options to meet specific application requirements.
PCB core is available in a wider range of thicknesses, typically starting at 0.006″ (0.15mm) and going up to 0.125″ (3.18mm) or more. It is also available in different grades and materials, such as FR-4, high-Tg FR-4, and other specialty laminates, catering to various application needs.
The Role of Prepreg and PCB Core in Multilayer PCBs
Multilayer PCB Construction
Multilayer PCBs are constructed by stacking alternating layers of prepreg and PCB core, with conductive layers (copper foil) on either side of each core. The number of layers in a multilayer PCB can vary from 4 to 50 or more, depending on the complexity of the design and the application requirements.
Lamination Process
The lamination process is a critical step in the manufacturing of multilayer PCBs, where the prepreg and PCB core layers are bonded together under high pressure and temperature. During lamination, the partially cured prepreg resin flows and fills any gaps or voids between the layers, while also bonding the conductive layers to the core.
The lamination process typically involves the following steps:
1. Stacking: The layers of prepreg, PCB core, and copper foil are stacked in the desired sequence.
2. Alignment: The stacked layers are aligned using registration holes or pins to ensure precise positioning.
3. Pressing: The stacked layers are placed in a lamination press, where they are subjected to high pressure and temperature.
4. Curing: The heat and pressure applied during the pressing stage fully cure the prepreg resin, bonding the layers together.
The Importance of Prepreg in Multilayer PCBs
Prepreg plays a crucial role in the construction of multilayer PCBs, providing several key benefits:
- Insulation: Prepreg acts as an insulating layer between the conductive layers, preventing electrical short circuits and ensuring proper signal integrity.
- Mechanical bonding: The partially cured prepreg resin flows and bonds the layers together during the lamination process, creating a strong and reliable mechanical connection.
- Filling gaps and voids: Prepreg helps to fill any gaps or voids between the layers, ensuring a consistent and uniform lamination.
- Controlling thickness: The use of prepreg allows for precise control over the thickness of the insulating layers, enabling the creation of thinner and more compact multilayer PCBs.
The Importance of PCB Core in Multilayer PCBs
PCB core serves as the foundation for the conductive layers in a multilayer PCB, providing several essential functions:
- Stability: The rigid and fully cured PCB core provides the necessary stability and support for the copper traces and other components.
- Mechanical strength: PCB core offers excellent mechanical strength, ensuring the overall integrity of the PCB and protecting it from physical stress and damage.
- Thermal management: The PCB core material, such as FR-4, has good thermal properties, allowing for efficient heat dissipation and preventing thermal stress on the components.
- Dimensional stability: PCB core maintains its dimensions and shape during the manufacturing process and in various environmental conditions, ensuring the accuracy and reliability of the final product.
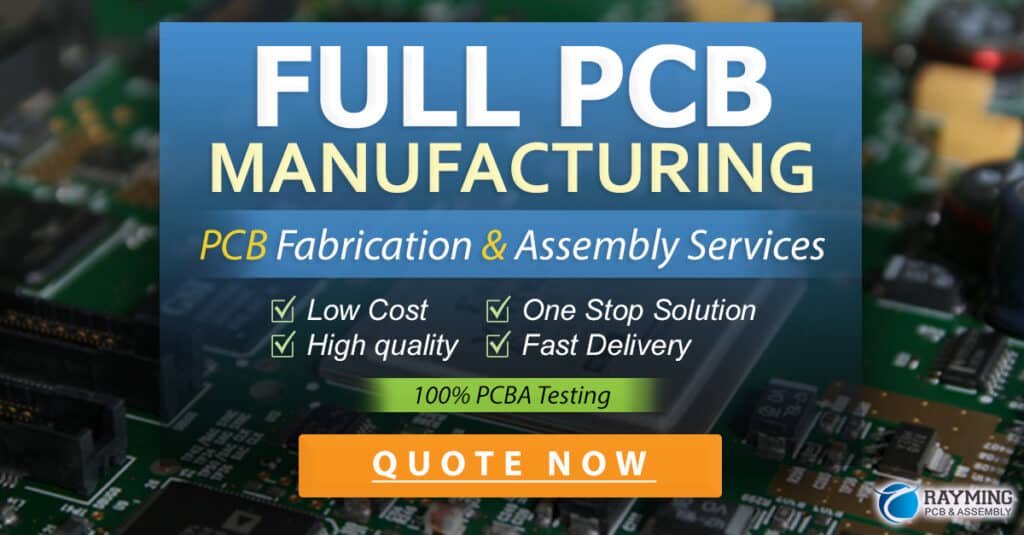
Selecting the Right Prepreg and PCB Core
Factors to Consider
When selecting prepreg and PCB core for a specific application, several factors should be considered:
- Electrical requirements: Consider the dielectric constant, loss tangent, and insulation resistance needed for the application.
- Mechanical requirements: Evaluate the required mechanical strength, flexibility, and dimensional stability.
- Thermal requirements: Assess the thermal conductivity and thermal expansion properties needed for proper heat dissipation and stability.
- Thickness and layer count: Determine the required thickness of the insulating layers and the number of layers needed in the multilayer PCB.
- Cost and availability: Consider the cost and availability of the materials, as well as any minimum order quantities or lead times.
Common Prepreg and PCB Core Materials
There are several common prepreg and PCB core materials used in the industry, each with its own set of properties and benefits:
Material | Description | Key Properties |
---|---|---|
FR-4 | Glass fiber reinforced epoxy laminate | Good electrical and mechanical properties, widely available, cost-effective |
High-Tg FR-4 | FR-4 with higher glass transition temperature | Improved thermal stability, better performance in high-temperature environments |
Polyimide | High-performance polymer | Excellent thermal and chemical resistance, low dielectric constant and loss tangent |
PTFE | Polytetrafluoroethylene (Teflon) | Very low dielectric constant and loss tangent, superior high-frequency performance |
Ceramic | Ceramic-based materials | Excellent thermal conductivity, low CTE, high dielectric constant |
Working with PCB Manufacturers
When selecting prepreg and PCB core materials, it is essential to work closely with experienced PCB manufacturers. They can provide valuable insights and recommendations based on your specific application requirements, design constraints, and budget. PCB manufacturers can also help with material selection, stackup design, and lamination process optimization to ensure the best possible results.
FAQ
- What is the main difference between prepreg and PCB core?
-
The main difference between prepreg and PCB core is their curing state. Prepreg is partially cured, or “B-staged,” while PCB core is fully cured. Prepreg is used as an insulating layer between conductive layers, while PCB core serves as the foundation for the conductive layers.
-
Can prepreg be used as a standalone material for PCBs?
-
No, prepreg cannot be used as a standalone material for PCBs. It is used in combination with PCB core to create multilayer PCBs, where prepreg acts as an insulating layer between the conductive layers.
-
What is the purpose of the lamination process in multilayer PCBs?
-
The purpose of the lamination process in multilayer PCBs is to bond the layers of prepreg, PCB core, and copper foil together under high pressure and temperature. During lamination, the partially cured prepreg resin flows and fills any gaps or voids between the layers, while also bonding the conductive layers to the core.
-
How does the thickness of prepreg and PCB core affect the design of a multilayer PCB?
-
The thickness of prepreg and PCB core affects the overall thickness of the multilayer PCB, as well as the spacing between the conductive layers. Thinner prepreg sheets allow for the creation of thinner multilayer PCBs, while thicker PCB cores provide greater mechanical strength and stability.
-
What should I consider when selecting prepreg and PCB core materials for my application?
- When selecting prepreg and PCB core materials, consider factors such as electrical requirements (dielectric constant, loss tangent), mechanical requirements (strength, flexibility), thermal requirements (conductivity, expansion), thickness and layer count, and cost and availability. It is also essential to work closely with experienced PCB manufacturers for guidance and recommendations.
Conclusion
Prepreg and PCB core are two fundamental materials in the construction of multilayer PCBs, each serving a unique purpose. Prepreg acts as an insulating layer between conductive layers, providing electrical insulation and mechanical bonding, while PCB core serves as the foundation for the conductive layers, offering stability, mechanical strength, and thermal management.
Understanding the differences between prepreg and PCB core, their roles in multilayer PCBs, and the factors to consider when selecting these materials is crucial for designers, engineers, and manufacturers. By working closely with experienced PCB manufacturers and making informed decisions based on application requirements, it is possible to create high-quality, reliable, and performance-driven multilayer PCBs.
As technology advances and the demand for more complex and compact electronic devices grows, the importance of prepreg and PCB core in PCB manufacturing will only continue to increase. By staying informed about these essential materials and their properties, designers and manufacturers can stay ahead of the curve and develop innovative PCB solutions for a wide range of applications.
No responses yet