What is Prepreg?
Prepreg, short for pre-impregnated, is a type of composite material used in PCB manufacturing. It consists of a reinforcement fabric, typically made of glass fibers, that is pre-impregnated with a partially cured thermosetting resin, such as epoxy. The resin is in a semi-solid state, allowing the prepreg to be flexible and easy to handle during the PCB layup process.
Characteristics of Prepreg
- Resin content: Prepreg contains a precise amount of resin, ensuring consistent properties throughout the material.
- Flexibility: The partially cured state of the resin makes prepreg flexible, allowing it to conform to various shapes and contours during the layup process.
- Adhesive properties: When subjected to heat and pressure, the resin in prepreg melts and flows, acting as an adhesive to bond the layers of the PCB together.
Types of Prepreg
There are several types of prepreg available, each with different properties and applications:
Prepreg Type | Reinforcement Fabric | Resin System | Key Properties |
---|---|---|---|
FR-4 | E-glass | Epoxy | High strength, good insulation, cost-effective |
High Tg | E-glass or NE-glass | Epoxy | Higher glass transition temperature, improved thermal stability |
Polyimide | E-glass or S-glass | Polyimide | Excellent thermal and chemical resistance, high performance |
Teflon | Glass or ceramic | PTFE | Low dielectric constant, high-frequency applications |
What is Core?
Core, also known as copper-clad laminate (CCL), is a rigid, copper-clad substrate used in PCB manufacturing. It consists of a base material, typically made of glass-reinforced epoxy or other thermosetting resins, sandwiched between two layers of copper foil. The core provides the foundation for the PCB, offering mechanical support and electrical insulation between copper layers.
Characteristics of Core
- Rigidity: Core is a rigid material that maintains its shape and dimensions, providing a stable base for the PCB.
- Copper cladding: The copper foil layers on either side of the core allow for the creation of conductive traces and pads on the PCB.
- Insulation: The base material of the core offers excellent electrical insulation properties, preventing short circuits between copper layers.
Types of Core
Various types of core materials are available, each with different properties and applications:
Core Type | Base Material | Key Properties |
---|---|---|
FR-4 | Glass-reinforced epoxy | High strength, good insulation, cost-effective |
High Tg FR-4 | Glass-reinforced epoxy | Higher glass transition temperature, improved thermal stability |
Polyimide | Polyimide | Excellent thermal and chemical resistance, high performance |
Teflon | PTFE | Low dielectric constant, high-frequency applications |
Metal Core | Aluminum or copper | High thermal conductivity, improved heat dissipation |
The Role of Prepreg and Core in PCB Manufacturing
Prepreg and core play distinct but equally important roles in the PCB manufacturing process. Here’s a closer look at how these materials are used:
Prepreg
- Insulation between layers: Prepreg is used as an insulating layer between the conductive copper layers of the PCB. It prevents short circuits and ensures proper electrical isolation.
- Bonding layers together: When subjected to heat and pressure during the lamination process, the resin in prepreg melts and flows, bonding the layers of the PCB together. This creates a strong, cohesive structure.
- Filling voids and gaps: Prepreg helps to fill any voids or gaps between the layers, ensuring a consistent and uniform thickness throughout the PCB.
Core
- Foundation of the PCB: Core serves as the rigid foundation of the PCB, providing mechanical support and maintaining the board’s shape and dimensions.
- Conductive layers: The copper foil layers on either side of the core are used to create the conductive traces, pads, and planes of the PCB.
- Electrical insulation: The base material of the core provides electrical insulation between the copper layers, preventing short circuits and ensuring proper signal integrity.
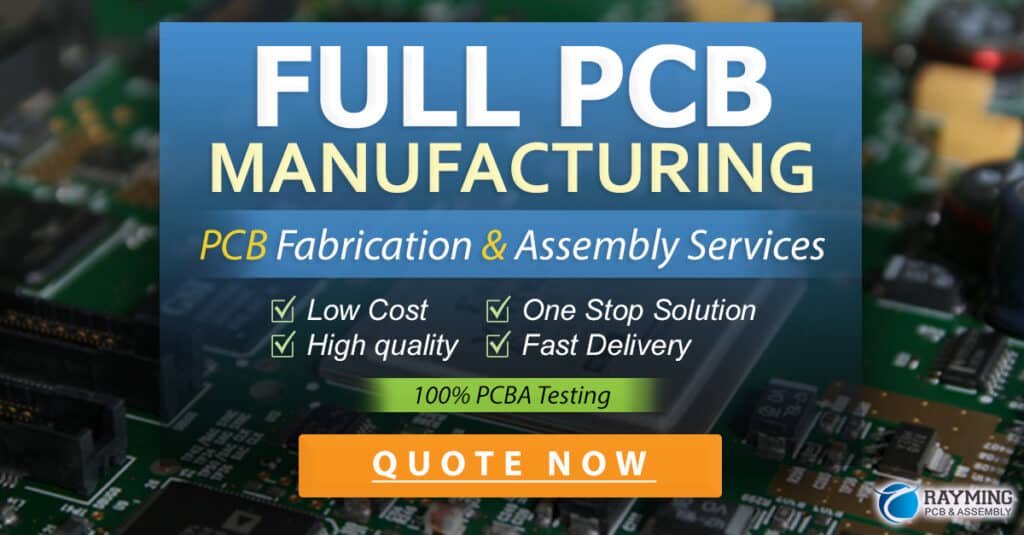
PCB Layup Process
The PCB layup process involves combining prepreg and core materials to create a multi-layer PCB. Here’s a simplified overview of the process:
- Inner layer processing: The core material is patterned and etched to create the inner conductive layers of the PCB.
- Layup: The patterned core layers are alternated with sheets of prepreg, and additional unpatterned core layers are added to the top and bottom of the stack.
- Lamination: The layup stack is subjected to heat and pressure in a lamination press. The resin in the prepreg melts and flows, bonding the layers together and creating a solid, unified structure.
- Drilling: Holes are drilled through the laminated board to create vias and component mounting holes.
- Outer layer processing: The outer layers of the PCB are patterned and etched to create the final conductive traces and pads.
- Surface finish and solder mask application: A surface finish, such as HASL or ENIG, is applied to the exposed copper to prevent oxidation and improve solderability. A solder mask is then applied to protect the copper traces and prevent short circuits.
Choosing the Right Prepreg and Core Materials
Selecting the appropriate prepreg and core materials is crucial for ensuring the performance, reliability, and manufacturability of a PCB. Several factors should be considered when making this choice:
- Electrical requirements: Consider the dielectric constant, dissipation factor, and insulation resistance of the materials to ensure they meet the electrical requirements of the PCB.
- Thermal requirements: Evaluate the thermal conductivity, coefficient of thermal expansion (CTE), and glass transition temperature (Tg) of the materials to ensure they can withstand the expected operating temperatures and thermal stresses.
- Mechanical requirements: Assess the strength, stiffness, and dimensional stability of the materials to ensure they can support the PCB’s mechanical requirements, such as vibration resistance and shock absorption.
- Cost and availability: Consider the cost and availability of the materials, as well as their impact on the overall manufacturing process and lead times.
FAQ
- What is the difference between prepreg and core in PCB manufacturing?
-
Prepreg is a flexible, partially cured composite material used as an insulating layer between copper layers, while core is a rigid, copper-clad substrate that serves as the foundation of the PCB.
-
Can prepreg be used as a standalone material in PCB manufacturing?
-
No, prepreg is typically used in combination with core materials to create a multi-layer PCB. It is not suitable for use as a standalone material due to its flexible nature and lack of copper cladding.
-
What is the purpose of the copper foil layers on core materials?
-
The copper foil layers on core materials are used to create the conductive traces, pads, and planes of the PCB. They provide the electrical connectivity necessary for the PCB to function.
-
How does the lamination process work in PCB manufacturing?
-
During the lamination process, the layup stack, consisting of alternating layers of patterned core and prepreg, is subjected to heat and pressure in a lamination press. The resin in the prepreg melts and flows, bonding the layers together and creating a solid, unified structure.
-
What factors should be considered when selecting prepreg and core materials for a PCB?
- When choosing prepreg and core materials, consider the electrical, thermal, and mechanical requirements of the PCB, as well as the cost and availability of the materials. It is essential to select materials that meet the specific needs of the application while also being cost-effective and readily available.
In conclusion, prepreg and core are two essential materials in PCB manufacturing, each serving a unique purpose. Prepreg acts as an insulating layer between copper layers and bonds the layers together during the lamination process, while core provides the rigid foundation and conductive layers of the PCB. Understanding the characteristics, types, and roles of these materials is crucial for designing and manufacturing high-quality, reliable PCBs. By carefully considering the electrical, thermal, mechanical, and cost requirements of a project, designers and manufacturers can select the most appropriate prepreg and core materials to ensure the success of their PCB applications.
No responses yet