The Role of Precision MedTech in Advancing Healthcare
The medical device industry has been undergoing a significant transformation in recent years, driven by the increasing demand for more accurate, reliable, and personalized Healthcare Solutions. At the forefront of this revolution is precision manufacturing, a cutting-edge approach that combines advanced technologies, innovative materials, and stringent quality control processes to create medical devices of unparalleled precision and performance. This article delves into the world of precision MedTech, exploring how it is reshaping the landscape of medical device development and improving patient outcomes across the globe.
The Evolution of Precision Manufacturing in MedTech
Precision manufacturing has its roots in the aerospace and automotive industries, where tight tolerances and high-quality standards are essential for ensuring the safety and reliability of complex systems. As the medical device industry faced growing challenges, such as the need for miniaturization, biocompatibility, and enhanced functionality, it began to adopt precision manufacturing techniques to meet these demands.
The evolution of precision manufacturing in MedTech can be traced back to the introduction of computer-aided design (CAD) and computer-aided manufacturing (CAM) systems in the 1980s. These technologies allowed for the creation of highly detailed 3D models and the automated production of parts with incredible accuracy. As CAD/CAM systems became more sophisticated, medical device manufacturers could design and produce increasingly complex components, paving the way for a new generation of innovative devices.
In the 1990s and early 2000s, the advent of rapid prototyping and 3D printing technologies further accelerated the adoption of precision manufacturing in the medical device industry. These technologies enabled manufacturers to quickly create physical prototypes from digital designs, reducing development times and allowing for faster iterations and improvements. As 3D printing materials and techniques evolved, it became possible to produce fully functional medical devices using additive manufacturing processes.
Today, precision manufacturing in MedTech encompasses a wide range of technologies and processes, including:
- Advanced machining techniques, such as CNC milling and turning
- Laser cutting and welding
- Micro-molding and micro-injection molding
- Surface treatments and coatings
- Cleanroom assembly and packaging
By leveraging these technologies, medical device manufacturers can produce components and devices with micron-level precision, ensuring the highest levels of quality, reliability, and performance.
The Benefits of Precision Manufacturing in MedTech
Precision manufacturing offers numerous benefits to the medical device industry, ultimately leading to improved patient outcomes and reduced healthcare costs. Some of the key advantages include:
-
Enhanced device performance: Precision-manufactured medical devices exhibit superior accuracy, consistency, and reliability compared to traditionally produced devices. This translates into better diagnostic and therapeutic outcomes for patients, as devices can more effectively target specific areas of the body or perform their intended functions with minimal errors.
-
Miniaturization: Precision manufacturing techniques allow for the creation of extremely small and intricate components, enabling the development of miniaturized medical devices. These devices can be less invasive, causing less trauma to the patient during procedures and reducing recovery times. Miniaturization also enables the integration of multiple functions into a single device, improving efficiency and convenience.
-
Customization and personalization: With precision manufacturing, medical devices can be tailored to the specific needs and anatomy of individual patients. By using advanced imaging techniques, such as CT scans and MRIs, manufacturers can create patient-specific implants, prosthetics, and other devices that provide a perfect fit and optimal performance. This level of customization improves patient comfort, reduces the risk of complications, and enhances overall treatment outcomes.
-
Accelerated development cycles: Precision manufacturing technologies, such as rapid prototyping and 3D printing, enable medical device companies to quickly iterate on designs and test new concepts. This accelerated development process allows for faster time-to-market, giving patients access to the latest innovations sooner. Additionally, the ability to create highly accurate prototypes reduces the need for extensive testing and validation, further streamlining the development cycle.
-
Cost efficiency: While precision manufacturing technologies may require higher initial investments, they often lead to long-term cost savings for medical device companies. By reducing waste, minimizing errors, and improving yields, precision manufacturing processes can significantly lower production costs. Furthermore, the increased reliability and performance of precision-manufactured devices can reduce the need for replacements and revisions, resulting in cost savings for healthcare providers and patients.
Applications of Precision MedTech
Precision manufacturing has found applications across a wide range of medical device sectors, from cardiovascular and orthopedic implants to diagnostic equipment and drug delivery systems. Some notable examples include:
-
Cardiovascular devices: Precision manufacturing has revolutionized the development of cardiovascular implants, such as stents, heart valves, and pacemakers. By creating devices with ultra-fine features and highly controlled surface properties, manufacturers can improve the biocompatibility and long-term performance of these life-saving devices. For instance, precision-manufactured stents with optimized geometries and drug-eluting coatings have significantly reduced the risk of restenosis and improved patient outcomes in coronary artery disease treatment.
-
Orthopedic implants: Precision MedTech has transformed the field of orthopedics by enabling the creation of patient-specific implants and instrumentation. Using advanced imaging and 3D printing technologies, manufacturers can produce implants that precisely match the patient’s anatomy, ensuring optimal fit and function. This level of customization has been particularly beneficial in complex procedures, such as revision surgeries and the treatment of rare bone disorders. Additionally, precision manufacturing has allowed for the development of more durable and wear-resistant implant materials, extending the lifespan of joint replacements and reducing the need for revision surgeries.
-
Diagnostic equipment: Precision manufacturing plays a crucial role in the development of advanced diagnostic equipment, such as microfluidic chips, biosensors, and lab-on-a-chip devices. These miniaturized systems require highly precise components and intricate fluid channels to accurately detect and analyze biological samples. Precision manufacturing techniques, such as micro-molding and laser machining, enable the creation of these complex structures, allowing for the development of more sensitive, specific, and cost-effective diagnostic tools. These advances have the potential to revolutionize point-of-care testing, enabling earlier detection of diseases and more personalized treatment approaches.
-
Drug delivery systems: Precision MedTech has also had a significant impact on the development of innovative drug delivery systems. By creating highly controlled release mechanisms and targeting specific areas of the body, precision-manufactured drug delivery devices can improve the efficacy and safety of medications. For example, microneedle arrays, which are fabricated using precision manufacturing techniques, can painlessly deliver drugs through the skin, offering a more patient-friendly alternative to traditional injections. Similarly, precision-manufactured implantable pumps can provide controlled and localized drug delivery, reducing systemic side effects and improving patient compliance.
-
Surgical instruments: Precision manufacturing has enabled the development of more sophisticated and ergonomic surgical instruments, improving the accuracy and efficiency of surgical procedures. By creating instruments with optimized designs and advanced materials, manufacturers can enhance the tactile feedback and control for surgeons, ultimately leading to better surgical outcomes. Additionally, precision manufacturing has allowed for the miniaturization of surgical tools, enabling less invasive procedures and faster patient recovery times.
The Future of Precision MedTech
As precision manufacturing technologies continue to evolve, the future of MedTech looks increasingly promising. Some of the key trends and developments that are expected to shape the industry in the coming years include:
-
Increased adoption of 3D printing: As 3D printing technologies become more accessible and cost-effective, their use in medical device manufacturing is set to expand rapidly. This will enable the creation of even more complex and customized devices, as well as the on-demand production of medical supplies and equipment. The development of new printable biomaterials, such as biocompatible polymers and metals, will further drive the adoption of 3D printing in precision MedTech.
-
Integration of smart technologies: The incorporation of smart technologies, such as sensors, electronics, and artificial intelligence, into medical devices is expected to become more prevalent in the future. Precision manufacturing will play a crucial role in enabling this integration, as it allows for the creation of highly miniaturized and sophisticated components. Smart medical devices will be able to continuously monitor patient health, provide real-time feedback, and even adjust treatment automatically, leading to more personalized and effective care.
-
Collaborative partnerships: As the complexity of medical devices increases, collaboration between various stakeholders in the MedTech ecosystem will become increasingly important. Precision manufacturers will need to work closely with medical device companies, healthcare providers, and research institutions to develop innovative solutions that meet the evolving needs of patients. These collaborations will foster knowledge sharing, accelerate the development process, and ensure that precision-manufactured devices are clinically relevant and commercially viable.
-
Regulatory adaptations: As precision manufacturing technologies continue to advance, regulatory bodies will need to adapt their guidelines and approval processes to keep pace with the industry. This may involve the development of new standards and testing protocols specifically tailored to precision-manufactured medical devices. Regulators will also need to work closely with manufacturers to ensure that the benefits of precision MedTech are realized while maintaining the highest levels of patient safety and device quality.
-
Workforce development: The growing adoption of precision manufacturing in MedTech will require a skilled workforce capable of operating and maintaining advanced manufacturing technologies. This will necessitate investments in education and training programs to develop the next generation of precision MedTech professionals. Collaboration between industry, academia, and government will be essential in creating curricula and apprenticeship programs that equip workers with the necessary knowledge and skills to thrive in this rapidly evolving field.
Frequently Asked Questions (FAQ)
1. What is precision manufacturing in the context of medical devices?
Precision manufacturing in the context of medical devices refers to the use of advanced technologies, processes, and materials to create components and devices with extremely high levels of accuracy, consistency, and quality. This approach enables the production of medical devices with tight tolerances, complex geometries, and enhanced functionality, ultimately leading to improved patient outcomes and reduced healthcare costs.
2. What are some examples of precision manufacturing technologies used in the medical device industry?
Some examples of precision manufacturing technologies used in the medical device industry include:
- Computer-aided design (CAD) and computer-aided manufacturing (CAM) systems
- Advanced machining techniques, such as CNC milling and turning
- Laser cutting and welding
- Micro-molding and micro-injection molding
- Surface treatments and coatings
- 3D printing and additive manufacturing
These technologies allow manufacturers to create highly precise and intricate components, enabling the development of innovative and customized medical devices.
3. How does precision manufacturing contribute to the miniaturization of medical devices?
Precision manufacturing techniques, such as micro-molding and laser machining, allow for the creation of extremely small and intricate components with micron-level accuracy. This enables the development of miniaturized medical devices that are less invasive, cause less trauma to patients, and can be more easily integrated into the body. Miniaturization also allows for the integration of multiple functions into a single device, improving efficiency and convenience for both patients and healthcare providers.
4. What role does precision manufacturing play in the customization and personalization of medical devices?
Precision manufacturing enables the creation of patient-specific medical devices that are tailored to the unique anatomy and needs of individual patients. By using advanced imaging techniques, such as CT scans and MRIs, manufacturers can create custom implants, prosthetics, and other devices that provide a perfect fit and optimal performance. This level of customization improves patient comfort, reduces the risk of complications, and enhances overall treatment outcomes.
5. How is precision manufacturing expected to shape the future of the medical device industry?
As precision manufacturing technologies continue to advance, they are expected to drive significant innovation and growth in the medical device industry. Some key trends and developments that are likely to shape the future of precision MedTech include:
- Increased adoption of 3D printing and additive manufacturing
- Integration of smart technologies, such as sensors, electronics, and artificial intelligence
- Collaborative partnerships between manufacturers, healthcare providers, and research institutions
- Regulatory adaptations to keep pace with the evolving landscape of precision-manufactured medical devices
- Workforce development to ensure a skilled labor pool capable of operating and maintaining advanced manufacturing technologies
By embracing these trends and investing in precision manufacturing capabilities, the medical device industry will be well-positioned to deliver innovative, personalized, and high-quality healthcare solutions that improve patient outcomes and drive long-term success.
Conclusion
Precision manufacturing is revolutionizing the medical device industry, enabling the development of innovative, personalized, and high-performance solutions that are transforming patient care. By leveraging advanced technologies, materials, and processes, precision MedTech is pushing the boundaries of what is possible in medical device design and production, ultimately leading to improved patient outcomes and reduced healthcare costs.
As the demand for more sophisticated and customized medical devices continues to grow, the adoption of precision manufacturing techniques will become increasingly critical for companies looking to stay competitive in the market. By investing in these technologies and fostering collaborative partnerships across the MedTech ecosystem, manufacturers can accelerate innovation, streamline development cycles, and deliver cutting-edge solutions that meet the evolving needs of patients and healthcare providers.
Looking ahead, the future of precision MedTech is bright, with exciting opportunities for growth, innovation, and meaningful impact on global healthcare. As the industry continues to evolve, it will be essential for all stakeholders – manufacturers, healthcare providers, researchers, regulators, and educators – to work together to unlock the full potential of precision manufacturing and ensure that its benefits are realized by patients around the world.
In conclusion, precision manufacturing is not just a technological advancement, but a powerful force for change in the medical device industry. By embracing this approach and committing to ongoing innovation and collaboration, the MedTech sector can play a pivotal role in shaping the future of healthcare, improving lives, and creating a healthier, more equitable world for all.
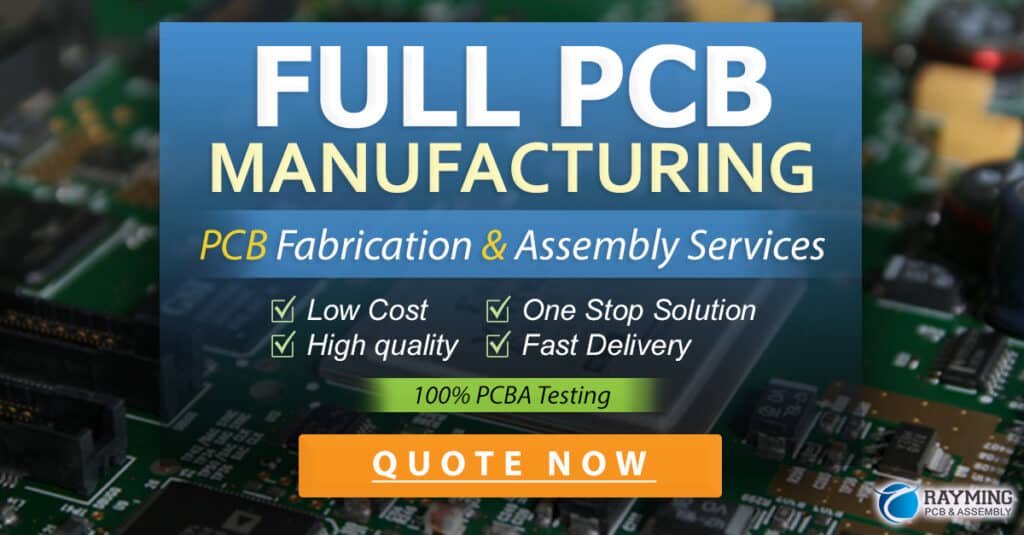
No responses yet