Introduction to EMC in PCB Design
Electromagnetic Compatibility (EMC) is a critical aspect of designing printed circuit boards (PCBs) for RF and microwave communications systems. EMC ensures that electronic devices can operate without causing or being affected by electromagnetic interference (EMI). In the context of PCB design, EMC focuses on minimizing the generation, coupling, and reception of unwanted electromagnetic energy.
Proper EMC design practices are essential to maintain signal integrity, reduce crosstalk, and prevent interference with other electronic devices. This article will discuss practical EMC considerations and techniques for designing PCBs in RF and microwave communications systems.
Understanding EMI Sources and Coupling Mechanisms
Common EMI Sources
- Digital circuits with high-speed clocks and sharp transients
- Power supplies and voltage regulators
- High-frequency oscillators and mixers
- Electrostatic discharge (ESD) events
- External sources (e.g., nearby electronic devices, power lines)
EMI Coupling Mechanisms
- Conducted EMI
- Common-mode noise
- Differential-mode noise
- Radiated EMI
- Near-field coupling (capacitive and inductive)
- Far-field radiation
Understanding the various EMI sources and coupling mechanisms is crucial for implementing effective EMC measures in PCB design.
PCB Layer Stack-up and Grounding Strategies
Optimizing Layer Stack-up
- Use dedicated power and ground planes
- Maintain consistent dielectric thickness between layers
- Minimize the distance between signal layers and their reference planes
- Use high-frequency laminates for RF and microwave circuits
Grounding Strategies
- Implement a solid ground plane
- Use a star grounding topology for low-frequency circuits
- Employ a grid or mesh grounding strategy for high-frequency circuits
- Minimize ground loops and provide adequate ground stitching vias
A well-designed layer stack-up and proper grounding strategies help reduce EMI and maintain signal integrity.
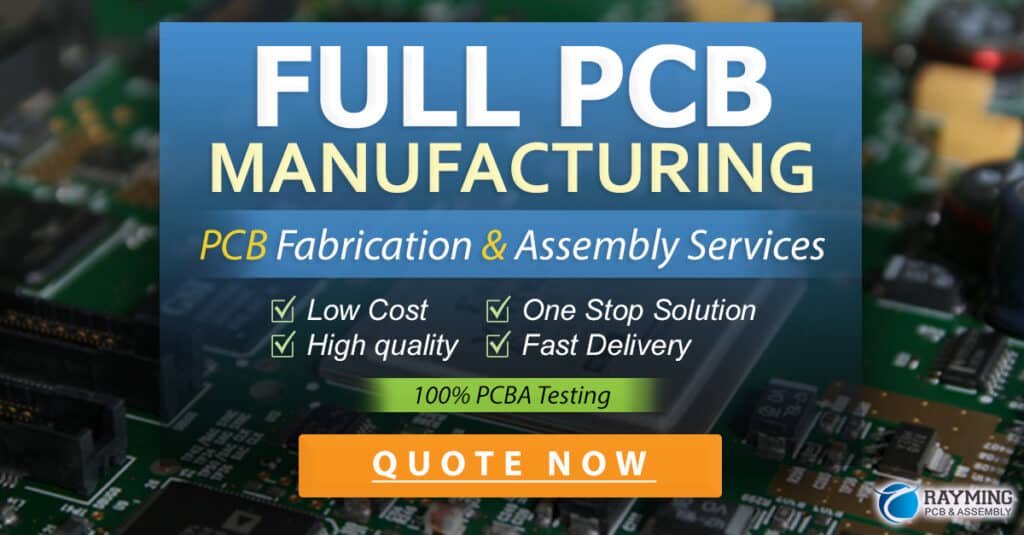
Signal Integrity and Routing Techniques
High-Speed Signal Routing
- Route high-speed traces over continuous reference planes
- Minimize trace length and avoid unnecessary bends
- Match trace impedances to the characteristic impedance of the system
- Use differential pair routing for high-speed differential signals
Crosstalk Reduction Techniques
- Increase spacing between adjacent traces
- Use guard traces or ground shields between sensitive signals
- Route sensitive signals on different layers with proper shielding
- Minimize parallel trace runs and avoid routing traces over split planes
Transmission Line Effects and Terminations
- Properly terminate transmission lines to prevent reflections
- Use series termination for source-end reflections
- Employ parallel termination for destination-end reflections
- Consider the use of AC terminations for high-frequency signals
Careful signal routing and proper termination techniques are essential for maintaining signal integrity and minimizing crosstalk.
Power Distribution Network (PDN) Design
Decoupling and Bypass Capacitors
- Place decoupling capacitors close to ICs and power pins
- Use a combination of bulk, ceramic, and low-ESL capacitors
- Minimize the loop area between capacitors and their reference planes
- Use the correct value and placement of capacitors based on frequency response
Power Plane Partitioning
- Partition power planes for different voltage levels and circuit blocks
- Use proper isolation techniques between power domains
- Implement adequate decoupling between power domains
- Consider the use of ferrite beads for high-frequency noise suppression
A well-designed PDN with proper decoupling and power plane partitioning helps maintain power integrity and reduce EMI.
Shielding and Filtering Techniques
Shielding Enclosures and Gaskets
- Use metallic enclosures to provide shielding against radiated EMI
- Ensure proper grounding and bonding of the enclosure to the PCB
- Implement EMI gaskets and conductive coatings for seams and openings
- Consider the use of absorbing materials for cavity resonance suppression
Filtering and Suppression Components
- Use EMI/RFI filters for power lines and I/O connections
- Implement ferrite beads and common-mode chokes for noise suppression
- Use TVS diodes and MOVs for transient protection
- Consider the use of shielded connectors and cables
Shielding and filtering techniques help attenuate EMI and protect sensitive circuits from external interference.
EMC Testing and Compliance
Pre-Compliance Testing
- Perform in-house pre-compliance testing to identify potential EMC issues
- Use spectrum analyzers, oscilloscopes, and near-field probes for EMI measurements
- Conduct both conducted and radiated emissions tests
- Iterate on the design based on pre-compliance test results
EMC Standards and Regulations
- Familiarize yourself with relevant EMC standards (e.g., FCC, CE, IEC)
- Understand the specific requirements for your target market and application
- Engage with an accredited EMC testing lab for compliance certification
- Maintain proper documentation and records for EMC compliance
Pre-compliance testing and adherence to EMC standards and regulations ensure that your PCB design meets the necessary EMC requirements.
Frequently Asked Questions (FAQ)
-
Q: What is the difference between EMI and EMC?
A: EMI (Electromagnetic Interference) refers to the unwanted electromagnetic energy that can disrupt the operation of electronic devices. EMC (Electromagnetic Compatibility) is the ability of electronic devices to operate without causing or being affected by EMI. -
Q: Why is EMC important in PCB design for RF and microwave systems?
A: RF and microwave systems operate at high frequencies and are particularly susceptible to EMI. Proper EMC design practices help maintain signal integrity, reduce crosstalk, and prevent interference with other electronic devices, ensuring reliable operation of the system. -
Q: What are the main EMI coupling mechanisms in PCBs?
A: The main EMI coupling mechanisms in PCBs are conducted EMI (common-mode and differential-mode noise) and radiated EMI (near-field coupling and far-field radiation). Understanding these mechanisms is crucial for implementing effective EMC measures. -
Q: How does proper grounding help in EMC PCB Design?
A: Proper grounding strategies, such as implementing a solid ground plane, using appropriate grounding topologies, and minimizing ground loops, help reduce EMI and maintain signal integrity. A well-designed grounding system provides a low-impedance return path for high-frequency currents and minimizes the coupling of unwanted signals. -
Q: What are some common shielding and filtering techniques used in EMC PCB design?
A: Common shielding and filtering techniques include the use of metallic enclosures, EMI gaskets, conductive coatings, EMI/RFI filters, ferrite beads, common-mode chokes, and transient protection devices. These techniques help attenuate EMI and protect sensitive circuits from external interference.
Conclusion
Designing PCBs for RF and microwave communications systems requires careful consideration of EMC principles and practices. By understanding EMI sources and coupling mechanisms, optimizing layer stack-up and grounding strategies, implementing proper signal integrity and routing techniques, designing a robust power distribution network, and employing shielding and filtering techniques, designers can effectively mitigate EMI and ensure the reliable operation of their systems.
Pre-compliance testing and adherence to relevant EMC standards and regulations are essential for verifying the EMC performance of the PCB design and achieving compliance certification. By following the practical EMC considerations discussed in this article, designers can create PCBs that meet the stringent EMC requirements of RF and microwave communications systems.
EMC Design Aspect | Key Considerations |
---|---|
EMI Sources and Coupling | – Identify common EMI sources – Understand conducted and radiated EMI coupling mechanisms |
Layer Stack-up and Grounding | – Use dedicated power and ground planes – Implement appropriate grounding strategies – Minimize ground loops and provide adequate ground stitching |
Signal Integrity and Routing | – Route high-speed traces over continuous reference planes – Use differential pair routing for high-speed signals – Employ crosstalk reduction techniques – Properly terminate transmission lines |
Power Distribution Network | – Place decoupling capacitors close to ICs and power pins – Use a combination of capacitor types – Partition power planes and implement proper isolation |
Shielding and Filtering | – Use metallic enclosures and EMI gaskets – Implement EMI/RFI filters and noise suppression components – Consider shielded connectors and cables |
EMC Testing and Compliance | – Perform pre-compliance testing – Familiarize yourself with relevant EMC standards and regulations – Engage with an accredited EMC testing lab for compliance certification |
By considering these key aspects of EMC PCB design, designers can create robust and reliable RF and microwave communications systems that meet the necessary EMC requirements.
No responses yet