Introduction to Power Supply Filters and PSU Noise Reduction
Power supplies are a critical component in virtually all electronic devices, converting AC mains voltage into lower DC voltages required by the circuitry. However, power supplies can also introduce unwanted noise and ripple on their output which can negatively impact the performance and reliability of the powered device. Power supply filters are essential for reducing this noise and ensuring a clean, stable DC voltage is delivered.
A well-designed power supply filter can provide the following key benefits:
– Attenuates high frequency noise and ripple voltages
– Improves power supply efficiency
– Protects sensitive components from voltage spikes and transients
– Minimizes electromagnetic interference (EMI)
– Increases device reliability and longevity
In this article, we’ll dive into the fundamentals of power supply filter design, examine common topologies and component selection, and provide tips for optimizing filters for various applications.
Understanding Power Supply Noise Sources
To effectively design PSU filters, it’s important to first understand the origins and characteristics of power supply noise. The two primary categories of noise are:
-
Differential-mode noise
- Occurs between positive and negative power supply rails
- Caused by fast switching in power conversion (e.g. in switch-mode supplies)
- Typically high frequency (>100kHz)
-
Common-mode noise
- Appears on both rails relative to ground
- Often caused by capacitive coupling between components/wires and ground
- Can be low or high frequency
Other potential noise sources include:
– Ripple voltage from rectification stages
– Transients from sudden load changes
– External interference coupled into power lines
The specific frequencies and amplitudes of noise depend on factors like the power supply topology, switching frequencies, component parasitic elements, PCB layout, and loading conditions. Accurately characterizing the noise spectrum using tools like a spectrum analyzer or oscilloscope is an important first step.
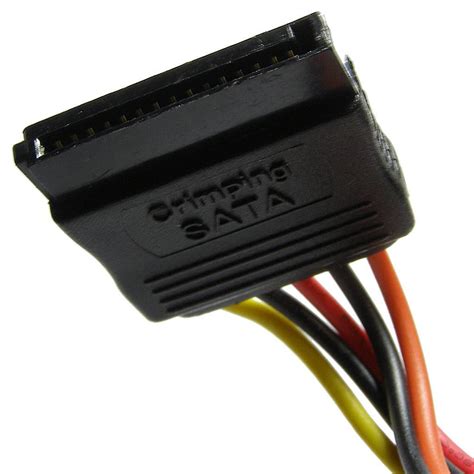
Key PSU Filter Components and Parameters
Power supply filters are constructed using various arrangements of four fundamental passive components:
Component | Symbol | Key Parameters | Function |
---|---|---|---|
Capacitor | C | Capacitance (F), Voltage Rating (V), ESR (Ω) | Provides low impedance path for AC currents, stores energy |
Inductor | L | Inductance (H), Current Rating (A), DCR (Ω) | Opposes changes in current, blocks high freq. |
Resistor | R | Resistance (Ω), Power Rating (W) | Limits current, dampens resonances |
Ferrite Bead | FB | Impedance (Ω), Current Rating (A) | Absorbs high freq., low DCR |
The key parameters to consider when selecting components for a PSU filter include:
- Voltage and current ratings – Must exceed maximum expected steady-state and transient levels
- Frequency response – Impedance vs. frequency curves determine filter attenuation
- Parasitic elements – ESR, ESL, and DCR impact filter performance and efficiency
- Temperature and environmental ratings – Ensure reliable operation in application conditions
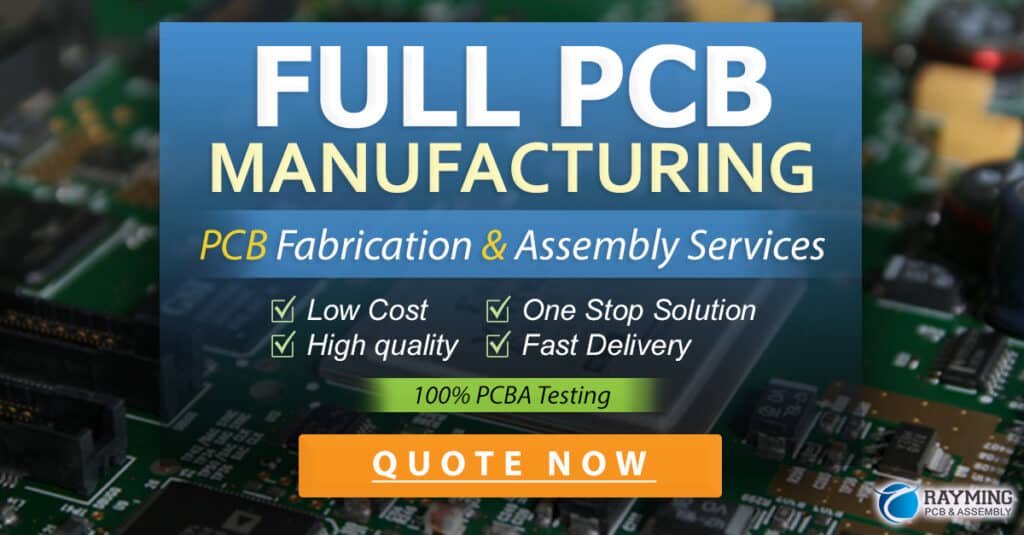
Common PSU Filter Topologies
Single-Stage LC Low-Pass Filters
One of the simplest and most common PSU filter topologies is the single-stage LC low-pass filter:
+---------+
------| Choke |------+------> Output
+---------+ |
=== Cin
|
GND
This second-order filter provides a roll-off of -40dB/decade above the cutoff frequency Fc, which is set by:
Fc = 1 / (2π√(LC))
Choosing a cutoff frequency at least 10x below the switching frequency and 10x above the control loop bandwidth provides effective attenuation of switching noise while maintaining stability. The output capacitance Cin should be sized to meet the voltage ripple and hold-up time requirements.
Multi-Stage LC Filters
For applications requiring greater noise attenuation, multiple LC stages can be cascaded:
+---------+ +---------+
Input ---+----| Choke |---+---+----| Choke |---+---+---> Output
| +---------+ | | +---------+ | |
=== Cin1 === Cin2 === Cin3
| | |
GND GND GND
Each additional LC stage introduces another -40dB/decade of attenuation. Component values should be scaled to appropriately divide the filtering action across the bandwidth of interest. Damping resistors are often added across each inductor to control resonances.
Pi Filters
The capacitor-input pi filter is another common variant providing -60dB/decade attenuation:
+-------------------+
+----| |----+
+-----+ | | +------+------> Output
| | | |
=== Cin1 === === Cin2 === Cout
| | Choke | |
Input-+ +-+ +-+ +
| |
GND GND
The two shunt capacitors Cin1/Cin2 and series choke form a pi-shaped filter. Additional output capacitance Cout further reduces noise. Pi filters are often used in applications sensitive to differential-mode noise.
LC with Ferrite Beads
At very high frequencies (>10MHz), inductors can lose effectiveness due to parasitic capacitance. Ferrite beads are an attractive alternative, providing increasing impedance with frequency. A typical ferrite bead filter schematic is:
+----FB----+
------| |------+------> Output
+----FB----+ |
=== Cin
|
GND
Ferrite beads are available in various impedance and current ratings. For optimal filtering, the bead impedance at the noise frequency should be at least 3x the power supply output impedance.
Common-Mode Chokes
To target common-mode noise, common-mode chokes can be employed:
+-------+
Live ---| || |---+
| | |
| CMC | === CX
| | |
Neutral--| |---+
+-------+
The common-mode choke (CMC) appears as a large impedance to common-mode currents, while differential currents pass through unimpeded. A shunt capacitor CX returns the common-mode current to the source. CMCs are frequently used in combination with other differential-mode filters.
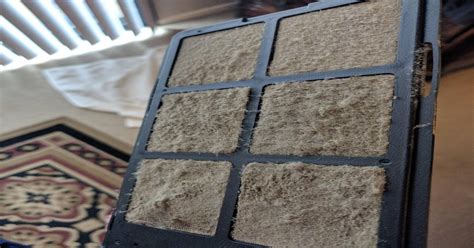
PSU Filter Design Process and Best Practices
Designing an optimized power supply filter involves the following steps:
- Characterize the power supply noise spectrum
- Define target noise attenuation levels across frequency
- Select a filter topology based on noise types and attenuation requirements
- Calculate preliminary component values based on filter equations
- Simulate or prototype filter to verify performance
- Iterate component selection and layout to optimize size, cost, and efficiency
Some key best practices to follow during the design process include:
- Minimize filter input and output impedances to reduce interaction with power supply control loop
- Use components with adequate Voltage Derating and low parasitic elements
- Place filter close to power supply output and use short, wide PCB traces
- Use ground planes to minimize loop area and provide shielding
- Consider impact of component tolerances, temperature, and aging on filter response
- Verify filter stability across all operating conditions, including startup and load transients
Optimizing Filters for Different Applications
The optimal filter design depends heavily on the end application and its unique requirements. Some common application areas and considerations include:
Analog/RF Circuits
- Prioritize low noise in sensitive frequency bands
- Use multistage filters for high attenuation
- Pay attention to filter output impedance and potential resonances
- Consider shielding filters to minimize radiated EMI
Digital Circuits
- Focus on power bus noise at clock frequencies and harmonics
- Use adequate bulk capacitance for transient currents
- Place filters close to noise sources like FPGAs, processors
- Consider impact of trace impedance on high-speed transient response
Automotive Systems
- Select components rated for wide temperature ranges and vibration
- Design for transient suppression during load dumps, starts/stops
- Ensure filters meet conducted EMC requirements
- Consider filter reliability and potential failure modes
Switching Amplifiers/Inverters
- Use filters rated for high peak voltages and currents
- Design for low DCR to minimize losses
- Optimize for low differential-mode noise in audible bands
- Consider potential for mechanical resonances/hum
Troubleshooting Common PSU Filter Issues
Even with careful design, power supply filters can encounter various issues in real-world operation. Some common problems and troubleshooting tips include:
Problem | Potential Causes | Solutions |
---|---|---|
Instability | Filter resonance with power supply control loop | Adjust filter cutoff, add damping, check compensation |
Overheating | Excessive ripple current, undersized components | Increase component ratings, reduce filter attenuation |
Noise spikes | Insufficient high-frequency attenuation | Add ferrite beads, increase filter order |
Ground loops | Improper grounding, shield connections | Revisit grounding scheme, use common-mode chokes |
If noise issues persist, it can be helpful to:
– Measure filter response in-situ using a network analyzer
– Inspect PCB layout and component placement for potential issues
– Verify integrity of component solder joints and trace connections
– Compare measured noise spectrum to expected/simulated results
– Selectively remove filter stages to isolate problem areas
Conclusion
Designing effective power supply filters is critical to achieving optimal power integrity and overall system performance. By understanding noise sources, common filter topologies, and component selection principles, designers can craft filters tailored to their application needs.
Through careful simulation, prototyping, and verification, filters can be optimized to provide high noise attenuation while maintaining efficiency, stability, and reliability. With a methodical design approach and attention to best practices, power supply filter design can be a powerful tool in maximizing electronic system performance.
FAQ
Q1: What are the most important parameters when selecting capacitors for a PSU filter?
A1: The key parameters for PSU filter capacitors are the capacitance value (sufficient for low impedance at noise frequencies), voltage rating (higher than peak voltages seen, typically 2x nominal), and equivalent series resistance or ESR (lower is better for minimizing losses). Other important factors include temperature stability, ripple current rating, and physical size.
Q2: How do you determine the cutoff frequency for an LC low-pass PSU filter?
A2: The cutoff frequency Fc for an LC low-pass filter is calculated as:
Fc = 1 / (2π√(LC))
Where L is the inductance in henries and C is the capacitance in farads. A good rule of thumb is to set Fc at least a decade below the power supply switching frequency to provide sufficient noise attenuation, and at least a decade above the control loop bandwidth to maintain stability.
Q3: What are the benefits of using ferrite beads in PSU filters?
A3: Ferrite beads offer several advantages over regular inductors in PSU filters, especially at high frequencies (>10MHz). Their impedance increases with frequency, providing excellent high-frequency noise attenuation. They also have lower DC resistance than comparable inductors, minimizing power loss. Ferrite beads are non-resonant devices, avoiding stability issues common with high-Q inductors. Finally, their compact size is beneficial in space-constrained designs.
Q4: How do you select the appropriate common-mode choke for a PSU filter?
A4: When selecting a common-mode choke (CMC) for a PSU filter, the most important parameters are the common-mode impedance at the target noise frequencies (higher is better for attenuation), and the rated current (must exceed the maximum expected common-mode current). The choke should also have low DC resistance to minimize voltage drop and power loss. Other factors include the choke’s self-resonant frequency, voltage rating, and physical size. It’s also important to ensure the choke is properly matched with shunt capacitors to provide a low-impedance path for common-mode noise.
Q5: What are some common mistakes to avoid when laying out PSU filters on a PCB?
A5: Some key mistakes to avoid when laying out PSU filters include:
- Placing the filter too far from the power supply output, allowing noise to couple onto long traces
- Using narrow, high-impedance traces that negate the low-impedance benefits of the filter
- Creating large loop areas that can radiate or pick up EMI
- Improperly grounding filter components, causing ground loops or noise coupling
- Neglecting component pad sizes and thermal relief, leading to overheating or reliability issues
To minimize these issues, best practices include placing filters close to the power supply, using short wide traces, providing solid ground planes, using appropriate via stitching, and carefully considering component placement and orientation. Paying attention to these layout details can help ensure optimal filter performance and reliability.
No responses yet