Understanding the Power Requirements
Before starting the design process, it is essential to have a clear understanding of the power requirements of your system. This includes knowing the voltage and current levels required by each component, as well as the total power consumption of the system. You should also consider the power supply specifications, such as the input voltage range, output voltage, and current ratings.
Voltage Levels
Different components in your system may require different voltage levels to operate correctly. For example, digital logic circuits typically require 3.3V or 5V, while analog circuits may require higher voltages. It is important to ensure that your power PCB can provide the necessary voltage levels to all components.
Component Type | Typical Voltage Range |
---|---|
Digital Logic | 3.3V – 5V |
Analog Circuits | 5V – 15V |
Motors and Actuators | 12V – 24V |
Current Requirements
In addition to voltage levels, you must also consider the current requirements of each component. The current drawn by a component can vary depending on its operating state, so it is essential to determine the maximum current draw under worst-case conditions. This information will help you select the appropriate power supply and design the PCB traces to handle the required current.
Component Type | Typical Current Range |
---|---|
Microcontrollers | 10mA – 500mA |
Sensors | 1mA – 50mA |
Motors | 100mA – 10A |
Selecting the Right Components
Once you have determined the power requirements of your system, the next step is to select the appropriate components for your power PCB. This includes choosing the right voltage regulators, capacitors, inductors, and other power management components.
Voltage Regulators
Voltage regulators are critical components in power PCBs, responsible for maintaining a stable output voltage despite variations in the input voltage or load current. There are two main types of voltage regulators: linear regulators and switching regulators.
Linear regulators are simple and inexpensive but have lower efficiency and can only step down the voltage. Switching regulators, on the other hand, are more complex but offer higher efficiency and can step up or step down the voltage.
Regulator Type | Efficiency | Output Current | Complexity |
---|---|---|---|
Linear | 30% – 60% | < 1A | Low |
Switching | 70% – 95% | > 1A | High |
Capacitors and Inductors
Capacitors and inductors are essential components in power PCBs, used for filtering, smoothing, and storing energy. The selection of these components depends on factors such as the switching frequency, ripple current, and desired output voltage ripple.
Capacitors are used to reduce voltage ripple and provide local energy storage, while inductors are used to store energy and filter out high-frequency noise. The value and type of capacitors and inductors should be chosen based on the specific requirements of your power PCB.
Designing the PCB Layout
The PCB layout is a critical aspect of power PCB Design, as it directly impacts the performance and reliability of the system. When designing the layout, there are several key considerations to keep in mind.
Power and Ground Planes
Using dedicated power and ground planes is essential for maintaining a low-impedance power distribution network. These planes help minimize voltage drops, reduce electromagnetic interference (EMI), and improve overall system stability.
When designing the power and ground planes, it is important to ensure adequate copper coverage and thickness to handle the required current. You should also consider the placement of power and ground vias to minimize impedance and improve current flow.
Component Placement
Proper component placement is crucial for optimizing the performance of your power PCB. Power components, such as voltage regulators and inductors, should be placed close to the power input and output connectors to minimize trace lengths and reduce voltage drops.
Decoupling capacitors should be placed as close as possible to the power pins of digital ICs to minimize the effect of power supply noise. Analog and digital components should be separated to reduce cross-talk and interference.
Trace Widths and Spacing
The width and spacing of PCB traces directly impact the current carrying capacity and impedance of the power distribution network. Traces should be sized appropriately to handle the required current without excessive voltage drop or heating.
The spacing between traces should also be considered to minimize cross-talk and ensure adequate insulation. The following table provides general guidelines for trace widths based on current requirements:
Current (A) | Trace Width (mm) |
---|---|
0.5 | 0.25 |
1.0 | 0.5 |
2.0 | 1.0 |
5.0 | 2.5 |
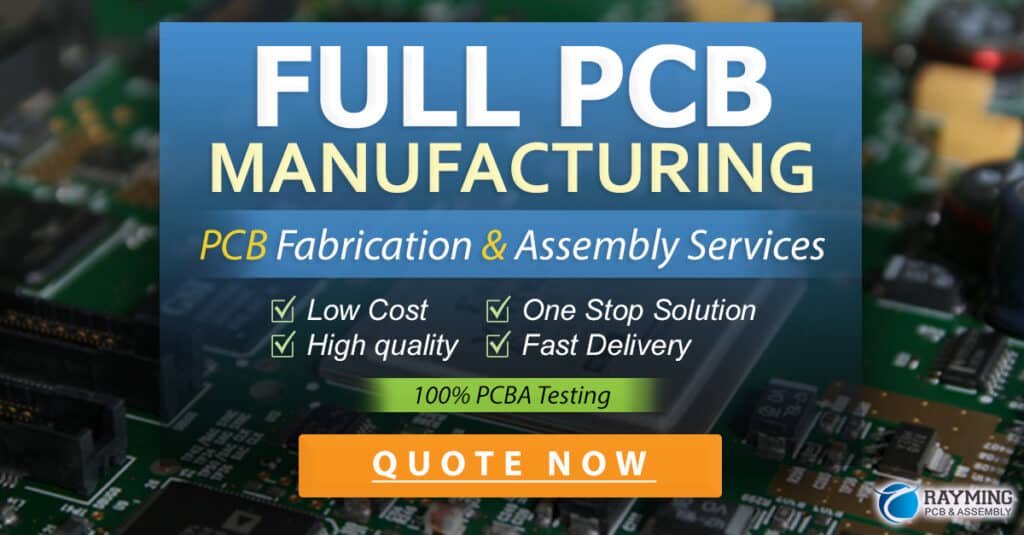
Thermal Management
Power PCBs often generate significant amounts of heat due to the high current flowing through the components and traces. Proper thermal management is essential to ensure the longevity and reliability of the system.
Heat Sinks
Heat sinks are commonly used to dissipate heat from power components, such as voltage regulators and power transistors. The selection of the heat sink depends on factors such as the power dissipation of the component, the ambient temperature, and the available space on the PCB.
When designing the PCB layout, it is important to provide adequate space for heat sinks and ensure proper thermal coupling between the component and the heat sink.
Thermal Vias
Thermal vias are used to transfer heat from the components to the PCB copper planes, which act as heat spreaders. By placing thermal vias under power components, you can effectively dissipate heat and reduce the component’s operating temperature.
The number and size of thermal vias depend on the power dissipation of the component and the desired thermal resistance. As a general rule, more vias and larger via diameters provide better thermal performance.
Testing and Validation
Once your power PCB design is complete, it is essential to thoroughly test and validate the system to ensure it meets the desired performance and reliability requirements.
Prototype Testing
Building a prototype of your power PCB allows you to test the system under real-world conditions and identify any potential issues early in the design process. During prototype testing, you should measure key parameters such as voltage levels, current consumption, and thermal performance.
It is also important to test the system under various operating conditions, such as different input voltages, load currents, and ambient temperatures, to ensure robust performance.
Compliance Testing
Depending on the application and target market, your power PCB may need to comply with various safety and EMC standards. Compliance testing ensures that your system meets the necessary regulatory requirements and can be safely used in the intended environment.
Some common standards for power PCBs include:
- UL 60950: Safety of Information Technology Equipment
- IEC 62368-1: Audio/Video, Information and Communication Technology Equipment – Part 1: Safety Requirements
- FCC Part 15: Radio Frequency Devices
- EN 55032: Electromagnetic Compatibility of Multimedia Equipment – Emission Requirements
It is important to familiarize yourself with the relevant standards and plan for compliance testing early in the design process to avoid costly redesigns later on.
Frequently Asked Questions (FAQ)
-
What is the difference between linear and switching voltage regulators?
Linear regulators are simple and inexpensive but have lower efficiency and can only step down the voltage. Switching regulators are more complex but offer higher efficiency and can step up or step down the voltage. -
Why is proper component placement important in power PCB design?
Proper component placement is crucial for optimizing the performance of your power PCB. Power components should be placed close to the power input and output connectors to minimize trace lengths and reduce voltage drops. Decoupling capacitors should be placed close to the power pins of digital ICs to minimize the effect of power supply noise. -
How do I select the right heat sink for my power components?
The selection of the heat sink depends on factors such as the power dissipation of the component, the ambient temperature, and the available space on the PCB. You can use online heat sink calculators or consult with the component manufacturer to determine the appropriate heat sink for your application. -
What are thermal vias, and why are they important?
Thermal vias are used to transfer heat from the components to the PCB copper planes, which act as heat spreaders. By placing thermal vias under power components, you can effectively dissipate heat and reduce the component’s operating temperature, improving the overall reliability of your power PCB. -
What are some common safety and EMC standards for power PCBs?
Some common standards for power PCBs include UL 60950 (Safety of Information Technology Equipment), IEC 62368-1 (Audio/Video, Information and Communication Technology Equipment – Part 1: Safety Requirements), FCC Part 15 (Radio Frequency Devices), and EN 55032 (Electromagnetic Compatibility of Multimedia Equipment – Emission Requirements). It is important to familiarize yourself with the relevant standards and plan for compliance testing early in the design process.
In conclusion, designing a power PCB can be a challenging task for beginners, but by understanding the key considerations discussed in this article, you can create reliable and efficient power systems. Remember to carefully assess your power requirements, select the right components, design an optimized PCB layout, manage thermal performance, and thoroughly test and validate your system. By following these guidelines and continually learning from your experiences, you’ll be well on your way to becoming a proficient power PCB designer.
No responses yet