Introduction to PLCC Packages
PLCC, which stands for Plastic Leaded Chip Carrier, is a surface-mount integrated circuit package used for housing and protecting electronic chips and providing electrical connections between the chip and a printed circuit board (PCB). PLCC packages are square or rectangular in shape and have “J”-shaped leads extending from all four sides of the package body.
PLCC packages offer several advantages over other IC package types:
- Compact size and high lead density
- Good thermal and electrical performance
- Easy to handle and place on PCBs
- Lower cost than some other SMT packages
- Available in a variety of sizes and lead counts
Because of these benefits, PLCC packages are widely used in many electronics applications, especially those requiring high interconnect density in a small footprint at a reasonable cost. Common applications include:
- Microcontrollers and microprocessors
- Memory chips
- Interface and I/O devices
- ASICs and FPGAs
- Analog and mixed-signal ICs
- Optoelectronic devices
In the following sections, we’ll take a closer look at the construction, types, and usage of PLCC packages to help you better understand and utilize these versatile IC packages in your designs.
PLCC Package Construction and Dimensions
A PLCC package consists of a plastic housing that encapsulates the silicon die and provides mechanical protection. The chip is wire bonded to a leadframe, which is then molded into the plastic housing. The outer J-leads are part of this leadframe and provide the electrical connections to the PCB.
The package dimensions are specified by the JEDEC (Joint Electron Device Engineering Council) standard MS-018. The key dimensions include:
- E1: Body width
- E: Overall width (including leads)
- B: Lead width
- L: Foot length
- A2: Body thickness
- A: Overall height (including standoff)
Here is a table summarizing the typical dimensions for some common PLCC package sizes:
Pins | E1 (mm) | E (mm) | B (mm) | L (mm) | A2 (mm) | A (mm) |
---|---|---|---|---|---|---|
20 | 8.89 | 11.43 | 0.36 | 0.81 | 3.05 | 4.57 |
28 | 11.43 | 13.97 | 0.36 | 0.81 | 3.05 | 4.57 |
44 | 16.51 | 19.05 | 0.36 | 0.81 | 3.56 | 5.08 |
52 | 19.05 | 21.59 | 0.36 | 0.81 | 3.56 | 5.08 |
68 | 24.13 | 26.67 | 0.36 | 0.81 | 3.56 | 5.08 |
84 | 29.21 | 31.75 | 0.36 | 0.81 | 3.56 | 5.08 |
It’s important to note that there can be slight variations in dimensions between manufacturers, so always consult the specific datasheet for the exact package dimensions and tolerances.
Types of PLCC Packages
There are a few different types of PLCC packages, each with its own characteristics and applications.
Standard PLCC
The standard PLCC is the most common type, with the J-leads extending from all four sides of the square or rectangular package. It is available in a wide range of sizes and lead counts, from as few as 20 pins to over 100 pins.
Standard PLCCs are used in a variety of general-purpose applications, such as microcontrollers, memory chips, and interface devices. They offer a good balance of size, performance, and cost.
Shrink PLCC (SPLCC)
Shrink PLCC packages are similar to standard PLCCs but with reduced package dimensions and tighter lead spacing. This allows for higher-density PCB layouts and smaller overall device sizes.
SPLCCs are commonly used in applications where space is at a premium, such as mobile devices, wearables, and IoT nodes. They are available in sizes from 20 to 84 pins.
Leadless PLCC (LPLCC)
Leadless PLCC packages do not have the external J-leads. Instead, they have metal pads on the bottom of the package that are soldered directly to the PCB. This results in a more compact package with a smaller footprint.
LPLCCs are often used in high-frequency applications, as the absence of leads reduces inductance and improves signal integrity. They are also used in space-constrained designs and are available in sizes up to 84 pins.
Thermally Enhanced PLCC
Thermally enhanced PLCC packages feature a metal heat spreader or heat sink attached to the top of the package. This improves heat dissipation and allows the chip to operate at higher power levels without overheating.
These packages are used for power-hungry devices such as microprocessors, FPGAs, and motor drivers. They are available in various sizes and configurations, with the heat spreader material and geometry optimized for the specific application.
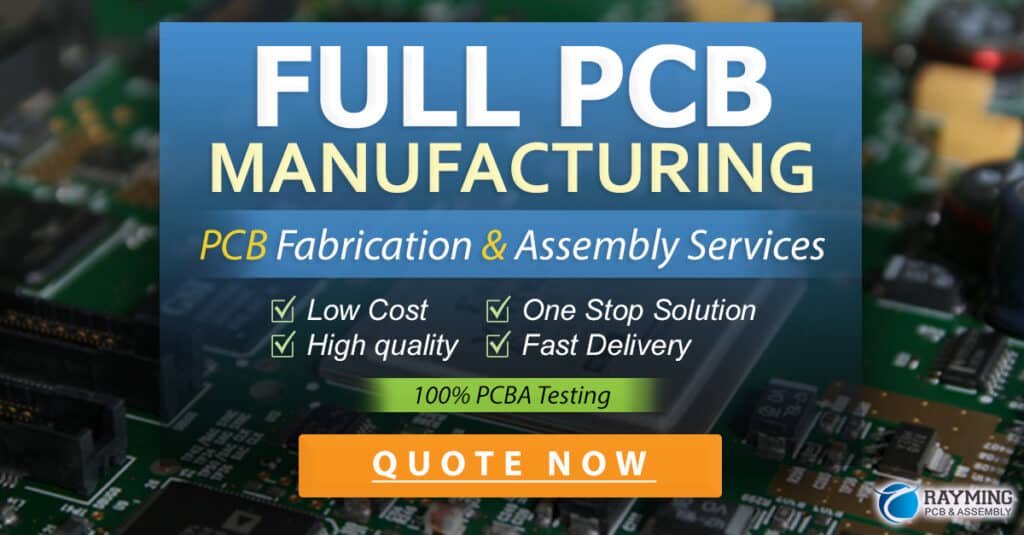
PCB Design Considerations for PLCC Packages
When designing a PCB for a PLCC package, there are several factors to consider to ensure proper assembly and reliable operation.
Footprint and Land Pattern
The PCB footprint for a PLCC package should match the package dimensions and lead spacing. The land pattern consists of the copper pads on the PCB that the package leads are soldered to.
The land pattern dimensions are typically specified in the package datasheet and should include:
- Pad width and length
- Pad spacing
- Pad-to-pad pitch
- Soldermask opening size
- Courtyard and assembly clearances
It’s important to follow these recommended dimensions to ensure good solder joints and prevent shorts or opens due to misalignment.
Thermal Relief and Via Stitching
For packages with high power dissipation, it’s important to provide adequate thermal relief on the PCB. This can be done by connecting the pad(s) to a large copper pour or plane with multiple thermal vias.
Via stitching is another technique used to improve heat transfer and mechanical strength. It involves placing a grid of small vias under the package body to conduct heat to the inner layers of the PCB.
Routing and Signal Integrity
When routing traces to a PLCC package, it’s important to consider signal integrity and crosstalk. High-speed signals should be routed with controlled impedance and proper termination to minimize reflections and ensure clean waveforms.
Differential pairs should be closely matched in length and have good common-mode rejection. Crosstalk can be minimized by providing adequate spacing between traces and using ground guard bands where necessary.
Assembly and Soldering
PLCC packages are typically assembled using surface-mount technology (SMT) processes. The package is placed on the PCB and soldered using reflow or wave soldering methods.
To ensure good solder joints, it’s important to control the solder paste volume, placement accuracy, and reflow profile. Inspection techniques such as X-ray or automated optical inspection (AOI) can be used to verify the solder joint quality.
FAQ
1. What is the difference between a PLCC and a QFP package?
PLCC and QFP (Quad Flat Pack) are both surface-mount packages, but they have some key differences:
- Shape: PLCCs are square or rectangular, while QFPs are rectangular with leads on all four sides.
- Lead style: PLCCs have J-shaped leads, while QFPs have gull-wing or straight leads.
- Lead pitch: PLCCs typically have a larger lead pitch (0.05″) compared to QFPs (down to 0.4mm).
- Thermal performance: PLCCs generally have better thermal performance due to the larger lead size and pitch.
2. Can PLCC packages be socketed?
Yes, PLCC packages can be socketed using specialized PLCC sockets. These sockets allow the package to be inserted and removed without soldering, which is useful for prototyping, testing, or field replacements.
PLCC sockets are available in various sizes and styles, including through-hole, surface-mount, and zero-insertion force (ZIF) types.
3. How do I choose the right PLCC package for my application?
When selecting a PLCC package for your application, consider the following factors:
- Pin count: Choose a package with enough pins to accommodate your device’s I/O and power requirements.
- Size: Consider the available board space and select a package size that fits within those constraints.
- Thermal performance: If your device dissipates significant power, choose a package with good thermal characteristics or consider a thermally enhanced version.
- Frequency: For high-speed applications, consider a leadless or low-inductance package to minimize parasitics.
- Cost: PLCCs are generally cost-effective, but larger sizes or specialized versions may have higher prices.
4. What are the common failure modes for PLCC packages?
Some common failure modes for PLCC packages include:
- Solder joint cracking or fatigue due to thermal stress or mechanical shock
- Lead breakage or deformation during handling or assembly
- Moisture ingress or corrosion due to poor sealing or exposure to harsh environments
- Electrical overstress or ESD damage to the internal circuitry
- Thermal overstress or overheating due to inadequate heat dissipation
Proper design, handling, and assembly practices can help mitigate these failure risks.
5. Are PLCC packages suitable for high-reliability applications?
Yes, PLCC packages can be used in high-reliability applications such as automotive, aerospace, and medical devices. However, it’s important to select packages that are qualified for the specific environmental and reliability requirements of the application.
Factors such as temperature range, humidity, vibration, and shock should be considered when choosing a PLCC package and defining the assembly and test processes. Additional screening or qualification tests may be necessary to ensure the package meets the required reliability levels.
Conclusion
PLCC packages are a versatile and cost-effective solution for a wide range of electronics applications. By understanding the different types, dimensions, and design considerations for PLCC packages, engineers can make informed decisions when selecting and using these packages in their designs.
When designing with PLCC packages, it’s important to follow best practices for PCB layout, thermal management, and signal integrity to ensure reliable operation and long-term performance. Proper handling and assembly processes are also critical to avoid damage and ensure good solder joint quality.
As technology continues to advance, PLCC packages will likely evolve to meet the changing needs of the electronics industry. However, their fundamental benefits of compact size, good performance, and reasonable cost will continue to make them a popular choice for many applications.
No responses yet