Introduction to PCB Plating Simulation
Printed Circuit Board (PCB) design is a complex process that involves multiple steps, from schematic design to component placement, routing, and finally, manufacturing. One critical aspect of PCB manufacturing is the plating process, which involves depositing a thin layer of metal onto the surface of the PCB to improve its conductivity, durability, and solderability. Plating is essential for ensuring the reliability and performance of the final product.
However, plating can also be a source of problems if not done correctly. Issues such as uneven plating thickness, voids, and cracks can lead to poor electrical connections, reduced durability, and even complete failure of the PCB. To avoid these problems, it is essential to carefully design and simulate the plating process before manufacturing begins.
This is where PCB plating simulation comes in. Plating simulation is a powerful tool that allows PCB Designers to virtually test and optimize the plating process before committing to manufacturing. By simulating the plating process, designers can identify potential issues early on and make necessary adjustments to ensure a high-quality final product.
Benefits of PCB Plating Simulation
PCB plating simulation offers several benefits for PCB designers and manufacturers alike. Some of the key benefits include:
-
Cost Savings: By identifying potential issues early on, plating simulation can help avoid costly manufacturing errors and rework. This can lead to significant cost savings in the long run.
-
Improved Quality: Plating simulation allows designers to optimize the plating process for maximum quality and reliability. By identifying and addressing potential issues before manufacturing begins, designers can ensure a higher-quality final product.
-
Faster Time-to-Market: By streamlining the design and manufacturing process, plating simulation can help reduce overall development time and bring products to market faster.
-
Enhanced Collaboration: Plating simulation tools often include collaboration features that allow team members to work together more effectively. This can lead to better communication, faster problem-solving, and ultimately, a more efficient design process.
How PCB Plating Simulation Works
PCB plating simulation typically involves creating a virtual model of the PCB and simulating the plating process using specialized software. The simulation takes into account various factors such as the type of metal being deposited, the thickness of the plating, the current density, and the geometry of the PCB.
The simulation process typically involves the following steps:
-
Creating the PCB Model: The first step is to create a 3D model of the PCB using CAD software. This model should include all the relevant features such as traces, vias, and pads.
-
Defining the Plating Parameters: Next, the designer specifies the plating parameters such as the type of metal, the thickness of the plating, and the current density. These parameters will depend on the specific requirements of the PCB and the intended application.
-
Running the Simulation: Once the model and parameters are defined, the designer runs the simulation. The software will simulate the flow of the plating solution over the surface of the PCB and calculate the resulting plating thickness and distribution.
-
Analyzing the Results: After the simulation is complete, the designer can analyze the results to identify any potential issues such as uneven plating thickness, voids, or cracks. The designer can then make adjustments to the design or plating parameters as needed.
-
Optimizing the Design: Based on the simulation results, the designer can optimize the PCB design and plating process for maximum quality and reliability. This may involve adjusting trace widths, via sizes, or pad shapes to ensure even plating distribution.
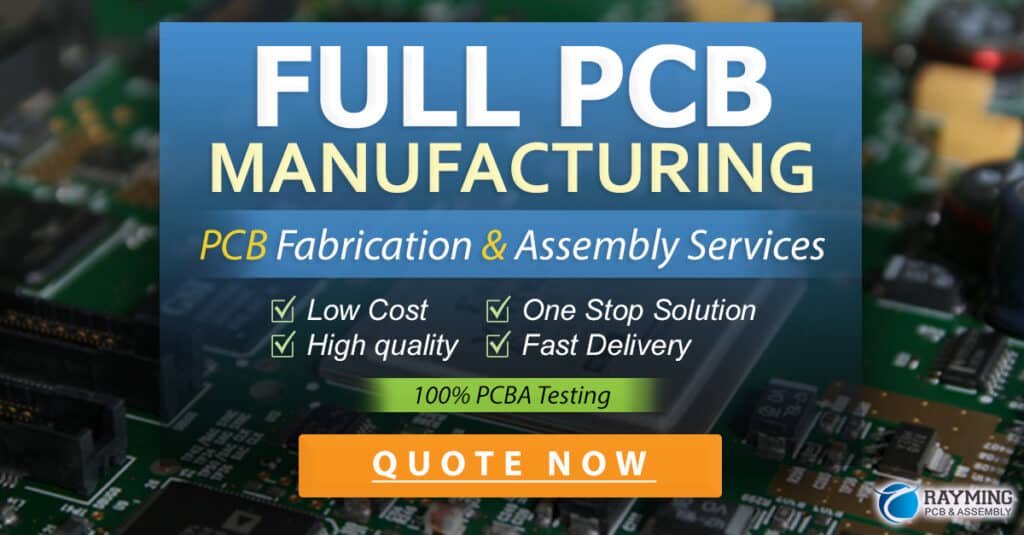
Types of PCB Plating
There are several types of PCB plating commonly used in the industry, each with its own unique properties and applications. Some of the most common types of PCB plating include:
-
Copper Plating: Copper is the most commonly used metal for PCB plating due to its excellent conductivity and low cost. Copper plating is typically used for creating the conductive traces and pads on the PCB.
-
Gold Plating: Gold plating is often used for high-reliability applications such as military and aerospace electronics. Gold is an excellent conductor and is highly resistant to corrosion and oxidation.
-
Nickel Plating: Nickel plating is often used as an underlayer for gold plating to improve adhesion and prevent diffusion. Nickel is also used as a barrier layer to prevent copper migration.
-
Silver Plating: Silver plating is sometimes used for high-frequency applications due to its excellent conductivity. However, silver is prone to tarnishing and is not as durable as other plating metals.
-
Tin Plating: Tin plating is often used for solderability and to protect exposed copper surfaces from oxidation. Tin is also used as a final finish for some PCBs.
Plating Type | Properties | Applications |
---|---|---|
Copper | Excellent conductivity, low cost | Conductive traces, pads |
Gold | Excellent conductivity, corrosion resistance | High-reliability applications, connectors |
Nickel | Good adhesion, barrier layer | Underlayer for gold plating, diffusion barrier |
Silver | Excellent conductivity | High-frequency applications |
Tin | Good solderability, oxidation protection | Final finish, solderability |
Challenges in PCB Plating
While PCB plating is essential for ensuring the quality and reliability of the final product, it can also present several challenges for designers and manufacturers. Some of the most common challenges in PCB plating include:
-
Uneven Plating Thickness: Uneven plating thickness can lead to poor electrical connections and reduced durability. This can be caused by factors such as incorrect current density, poor solution flow, or surface contamination.
-
Voids and Cracks: Voids and cracks in the plating can lead to poor electrical connections and reduced durability. These defects can be caused by factors such as incorrect plating parameters, surface contamination, or mechanical stress.
-
Copper Migration: Copper migration can occur when copper ions diffuse through the plating and cause short circuits or other reliability issues. This can be prevented by using barrier layers such as nickel.
-
Whiskers: Whiskers are small, hair-like growths that can form on the surface of the plating. These whiskers can cause short circuits and other reliability issues. Whiskers can be prevented by using matte tin finishes or by adding lead to the plating.
-
Environmental Concerns: Some plating processes use hazardous chemicals that can pose environmental and health risks. Designers and manufacturers must carefully consider the environmental impact of their plating processes and take steps to minimize harm.
Best Practices for PCB Plating
To ensure the highest quality and reliability in PCB plating, designers and manufacturers should follow these best practices:
-
Use Plating Simulation: Plating simulation is a powerful tool for identifying potential issues early on and optimizing the plating process. Designers should use plating simulation software to test and refine their designs before committing to manufacturing.
-
Choose the Right Plating Metal: The choice of plating metal will depend on the specific requirements of the PCB and the intended application. Designers should carefully consider the properties of each plating metal and choose the one that best meets their needs.
-
Control the Plating Parameters: Plating parameters such as current density, solution temperature, and agitation must be carefully controlled to ensure even plating thickness and avoid defects. Manufacturers should use advanced process control systems to monitor and adjust these parameters in real-time.
-
Maintain a Clean Environment: Surface contamination can lead to poor plating adhesion and other defects. Manufacturers should maintain a clean and controlled environment to minimize contamination risk.
-
Use Barrier Layers: Barrier layers such as nickel can help prevent copper migration and improve plating adhesion. Designers should consider using barrier layers where appropriate.
-
Consider Environmental Impact: Designers and manufacturers should carefully consider the environmental impact of their plating processes and take steps to minimize harm. This may involve using environmentally friendly plating chemistries or implementing waste reduction strategies.
Choosing the Right PCB Plating Simulation Tool
When choosing a PCB plating simulation tool, designers should consider several key factors:
-
Accuracy: The simulation tool should provide accurate results that closely match real-world plating behavior. Look for tools that have been validated against experimental data.
-
Speed: The simulation tool should be fast enough to provide results in a timely manner. This is especially important for complex designs or large batches of simulations.
-
Ease of Use: The simulation tool should be easy to use and integrate into existing design workflows. Look for tools with intuitive interfaces and good documentation.
-
Features: The simulation tool should offer a range of features to support different types of plating simulations. This may include support for different plating metals, advanced boundary conditions, and post-processing tools.
-
Cost: The cost of the simulation tool should be weighed against its features and benefits. Look for tools that offer good value for money and fit within your budget.
Some popular PCB plating simulation tools include:
- Ansys SIwave: A comprehensive simulation tool for PCB and IC package design, including plating simulation.
- Cadence Sigrity: A suite of tools for signal and power integrity analysis, including plating simulation.
- Mentor Graphics HyperLynx: A high-speed PCB design tool with integrated plating simulation capabilities.
- Altium Designer: A PCB design tool with built-in plating simulation features.
Conclusion
PCB plating simulation is a powerful tool for optimizing the plating process and ensuring the highest quality and reliability in PCB manufacturing. By using plating simulation, designers can identify potential issues early on, refine their designs, and ultimately save time and money in the manufacturing process.
To get the most out of plating simulation, designers should follow best practices such as choosing the right plating metal, controlling plating parameters, and maintaining a clean environment. They should also carefully consider the environmental impact of their plating processes and take steps to minimize harm.
When choosing a plating simulation tool, designers should look for tools that offer good accuracy, speed, ease of use, and features. By investing in the right tools and following best practices, designers can unlock the full potential of plating simulation and create high-quality, reliable PCBs that meet the demands of today’s electronics industry.
FAQs
-
What is PCB plating simulation?
PCB plating simulation is a virtual process that allows designers to test and optimize the plating process before manufacturing begins. It involves creating a 3D model of the PCB and simulating the flow of the plating solution over the surface to calculate the resulting plating thickness and distribution. -
Why is PCB plating simulation important?
PCB plating simulation is important because it allows designers to identify potential issues early on and make necessary adjustments to ensure a high-quality final product. This can lead to cost savings, improved quality, faster time-to-market, and enhanced collaboration. -
What are some common challenges in PCB plating?
Some common challenges in PCB plating include uneven plating thickness, voids and cracks, copper migration, whiskers, and environmental concerns. These challenges can lead to poor electrical connections, reduced durability, and other reliability issues. -
What are some best practices for PCB plating?
Some best practices for PCB plating include using plating simulation, choosing the right plating metal, controlling plating parameters, maintaining a clean environment, using barrier layers, and considering environmental impact. By following these best practices, designers can ensure the highest quality and reliability in their PCB designs. -
How do I choose the right PCB plating simulation tool?
When choosing a PCB plating simulation tool, designers should consider factors such as accuracy, speed, ease of use, features, and cost. Some popular tools include Ansys SIwave, Cadence Sigrity, Mentor Graphics HyperLynx, and Altium Designer. By choosing the right tool and following best practices, designers can unlock the full potential of plating simulation and create high-quality, reliable PCBs.
No responses yet