Introduction to Placer-camera machines
Placer camera-assisted manual pick and place machines have revolutionized the manufacturing industry by providing a cost-effective and efficient solution for assembly processes. These machines combine the precision of machine vision with the flexibility of manual operation, enabling operators to accurately place components on printed circuit boards (PCBs) or other substrates.
How Placer-Camera Machines Work
A placer-camera machine consists of several key components:
- Camera system: A high-resolution camera mounted above the work area captures images of the components and the substrate.
- Illumination: Proper lighting ensures clear and consistent images for accurate component recognition and placement.
- Image processing software: Algorithms analyze the captured images to identify components, determine their orientation, and guide the operator during placement.
- Crosshair display: A monitor or projection system displays a crosshair or other visual cues to assist the operator in aligning components with the substrate.
- Manual placement tool: The operator uses a hand-held tool, such as tweezers or a vacuum pen, to pick up components and place them on the substrate following the visual guidance.
Benefits of Placer-Camera Machines
Placer camera-assisted manual pick and place machines offer several advantages over fully automated systems:
- Cost-effectiveness: Manual systems are generally less expensive than fully automated solutions, making them accessible to a wider range of manufacturers.
- Flexibility: Operators can easily adapt to changes in product design or component types without extensive programming or machine reconfiguration.
- Scalability: Manual systems can be easily scaled up or down based on production requirements, allowing manufacturers to adjust their capacity as needed.
- Error reduction: The camera-assisted guidance helps operators place components accurately, reducing the risk of misalignment or incorrect placement.
Applications of Placer-Camera Machines
Placer camera-assisted manual pick and place machines find applications in various industries and manufacturing processes:
Electronics Assembly
One of the most common applications for placer-camera machines is in the assembly of electronic devices, particularly in the placement of surface-mount devices (SMDs) on PCBs. The camera system helps operators accurately position small components, such as resistors, capacitors, and integrated circuits, ensuring proper alignment and connection with the PCB Traces.
Medical Device Manufacturing
Placer-camera machines are also used in the production of medical devices, where precision and accuracy are critical. These machines assist in the assembly of small, intricate components in devices such as:
- Pacemakers
- Insulin pumps
- Surgical instruments
- Diagnostic equipment
Automotive Industry
In the automotive industry, placer-camera machines are employed in the assembly of various electronic components, such as sensors, control modules, and wiring harnesses. The camera-assisted guidance helps ensure the correct placement of components in safety-critical systems, such as airbag control modules and anti-lock braking systems.
Aerospace and Defense
Placer-camera machines are used in the assembly of electronic components for aerospace and defense applications, where reliability and durability are paramount. These machines assist in the production of:
- Avionics systems
- Satellite components
- Military communication devices
- Radar and surveillance equipment
Advancements in Placer-Camera Technology
As the demand for more efficient and accurate assembly processes grows, placer-camera technology continues to evolve:
High-Resolution Cameras
The introduction of high-resolution cameras, such as those with 4K or 8K resolution, enables placer-camera machines to capture even finer details of components and substrates. This improved image quality allows for more precise component recognition and placement, particularly for miniaturized components.
Advanced Image Processing Algorithms
Developments in image processing algorithms, such as deep learning and artificial intelligence, have enhanced the capabilities of placer-camera machines. These advanced algorithms can better identify and locate components, even in the presence of variations in lighting or component appearance.
Augmented Reality Guidance
Some placer-camera machines now incorporate augmented reality (AR) technology to provide more intuitive and interactive guidance for operators. AR systems can overlay digital information, such as component outlines or placement instructions, directly onto the operator’s view of the work area, streamlining the assembly process.
Integration with Other Technologies
Placer-camera machines can be integrated with other manufacturing technologies to create more comprehensive and efficient assembly solutions. For example:
- Robotic Arm Integration: Combining a placer-camera machine with a robotic arm can automate the component picking process, further reducing the risk of errors and increasing production speed.
- Automated Dispensing: Integrating a placer-camera machine with an automated dispensing system allows for the precise application of adhesives, solder paste, or other materials during the assembly process.
- Traceability and Data Collection: Connecting placer-camera machines to a factory’s data collection system enables real-time monitoring of production metrics, quality control, and traceability of components and finished products.
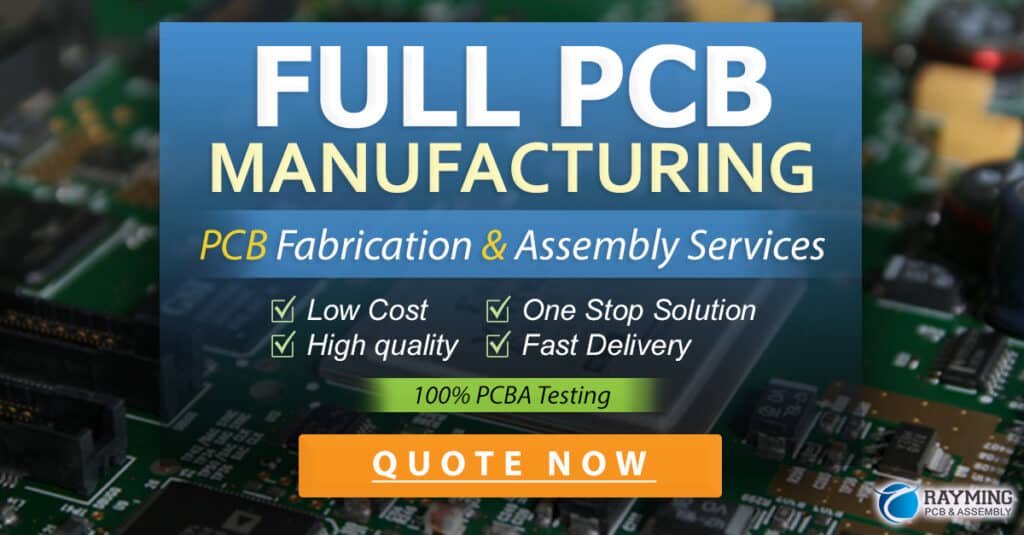
Best Practices for Implementing Placer-Camera Machines
To ensure the successful implementation and operation of placer-camera machines, consider the following best practices:
Proper Training
Provide thorough training for operators on the use of the placer-camera machine, including:
- Machine setup and calibration
- Component recognition and handling
- Interpretation of visual guidance
- Troubleshooting common issues
Regular refresher training can help maintain operator skills and ensure consistent performance.
Optimize Workspace Ergonomics
Design the workspace around the placer-camera machine to promote operator comfort and efficiency:
- Adjust the work surface height to reduce strain on the operator’s back, neck, and shoulders
- Provide adequate lighting to minimize eye strain and improve visual acuity
- Organize components and tools within easy reach to minimize excessive reaching or twisting
Regular Maintenance and Calibration
Establish a regular maintenance and calibration schedule for the placer-camera machine to ensure optimal performance:
- Clean camera lenses and illumination sources to maintain image quality
- Calibrate the camera system to ensure accurate component recognition and placement guidance
- Inspect and replace worn or damaged components, such as placement tools or machine fixtures
Continuous Improvement
Monitor the performance of the placer-camera machine and seek opportunities for continuous improvement:
- Analyze production data to identify bottlenecks or areas for optimization
- Encourage operator feedback to identify potential improvements in machine setup, component handling, or workflow
- Stay informed about advancements in placer-camera technology and evaluate their potential benefits for your specific application
Frequently Asked Questions (FAQ)
-
What is the typical accuracy of a placer-camera machine?
Placer-camera machines can achieve placement accuracies of ±50 microns or better, depending on the specific machine model, camera resolution, and component size. -
How does a placer-camera machine compare to a fully automated pick and place machine in terms of speed?
While placer-camera machines are generally slower than fully automated systems, they offer a balance between speed and flexibility. Manual placement allows for easier adaptation to changes in product design or component types, which can be more time-consuming with fully automated systems. -
Can a placer-camera machine handle different component sizes and shapes?
Yes, placer-camera machines can typically handle a wide range of component sizes and shapes, from small SMDs to larger through-hole components. The machine’s software can be programmed to recognize and provide guidance for different component types. -
How much training is required for operators to use a placer-camera machine effectively?
The amount of training required depends on the complexity of the machine and the operator’s existing skills. Generally, a few hours to a few days of training are sufficient for operators to become proficient in using a placer-camera machine. -
What is the typical cost of a placer-camera machine compared to a fully automated system?
Placer-camera machines are generally less expensive than fully automated pick and place systems. The exact cost difference depends on factors such as machine features, camera resolution, and software capabilities. In many cases, a placer-camera machine can provide a cost-effective solution for low-to-medium volume production runs.
Conclusion
Placer camera-assisted manual pick and place machines offer a versatile and efficient solution for component assembly in various industries. By combining the precision of machine vision with the flexibility of manual operation, these machines help manufacturers achieve accurate component placement while maintaining cost-effectiveness and adaptability.
As technology advances, placer-camera machines continue to evolve, incorporating high-resolution cameras, advanced image processing algorithms, and augmented reality guidance to further enhance their capabilities. By implementing best practices for machine setup, operator training, and continuous improvement, manufacturers can maximize the benefits of placer-camera machines and streamline their assembly processes.
Aspect | Placer-Camera Machine | Fully Automated Machine |
---|---|---|
Cost | Lower | Higher |
Speed | Moderate | High |
Flexibility | High | Lower |
Operator Skill Required | Moderate | Low |
Scalability | High | Moderate |
In conclusion, placer camera-assisted manual pick and place machines provide a reliable and efficient solution for component assembly, offering a balance between precision, flexibility, and cost-effectiveness. As manufacturers continue to seek ways to optimize their assembly processes, placer-camera machines will likely play an increasingly important role in the future of manufacturing.
No responses yet