What are Phototools in PCB Manufacturing?
Phototools are high-resolution, transparent films that carry the circuit pattern for a PCB. They are used in the photolithography process, where the circuit design is transferred onto the photoresist-coated copper layer of the PCB. The phototools act as a mask, allowing light to pass through the transparent areas while blocking it in the opaque regions. This selective exposure of the photoresist to light creates a precise replica of the circuit pattern on the PCB.
Types of Phototools
There are two main types of phototools used in PCB manufacturing:
-
Emulsion Phototools: Emulsion phototools are created by exposing a light-sensitive emulsion layer on a transparent film to the circuit pattern. The emulsion hardens in the exposed areas, creating an opaque mask. Emulsion phototools offer high resolution and are suitable for fine-pitch designs.
-
Ink-Jet Phototools: Ink-jet phototools are produced using high-resolution ink-jet printers. The circuit pattern is printed directly onto a transparent film using UV-blocking ink. Ink-jet phototools are cost-effective and offer quick turnaround times, making them ideal for prototyping and low-volume production.
Creating Phototools for PCB Image Transfer
The process of creating phototools involves several steps to ensure the accurate reproduction of the circuit pattern. Let’s explore each step in detail.
Step 1: PCB Design and Gerber File Generation
The first step in creating phototools is to design the PCB using Electronic Design automation (EDA) software. The design includes the component placement, routing, and all the necessary layers of the PCB. Once the design is finalized, Gerber files are generated. Gerber files are industry-standard formats that contain the information required to manufacture the PCB, including the copper layers, solder mask, and silkscreen.
Step 2: Phototool Preparation
With the Gerber files ready, the next step is to prepare the phototools. This involves the following sub-steps:
-
Film Selection: Choose a high-quality, transparent film suitable for the chosen phototool type (emulsion or ink-jet). The film should have good dimensional stability and optical clarity to ensure accurate image transfer.
-
Resolution and Aperture Setting: Set the appropriate resolution and aperture settings based on the PCB design requirements. Higher resolutions are necessary for fine-pitch designs and smaller features. The aperture setting determines the smallest feature size that can be reproduced on the phototool.
-
Polarity and Mirroring: Determine the polarity of the phototool based on the photoresist type used. Positive photoresists require a positive phototool, where the circuit pattern is opaque, while negative photoresists require a negative phototool, where the circuit pattern is transparent. Additionally, consider whether the phototool needs to be mirrored to account for the orientation of the PCB during exposure.
Step 3: Phototool Printing
Once the phototool preparation is complete, the actual printing process begins. The method of printing depends on the chosen phototool type:
-
Emulsion Phototools: For emulsion phototools, the film is coated with a light-sensitive emulsion and exposed to the circuit pattern using a high-resolution imagesetter. The exposed areas of the emulsion harden, creating an opaque mask. The unexposed areas are then washed away, leaving a transparent circuit pattern on the film.
-
Ink-Jet Phototools: Ink-jet phototools are printed using a high-resolution ink-jet printer. The Gerber files are processed by specialized software that converts them into a printable format. The printer deposits UV-blocking ink onto the transparent film, creating an opaque circuit pattern.
Step 4: Phototool Inspection and Quality Control
After printing, the phototools undergo a thorough inspection and quality control process to ensure their accuracy and consistency. This involves the following checks:
-
Dimensional Accuracy: Verify that the phototool dimensions match the PCB design specifications. Use precision measuring tools to check critical features and overall dimensions.
-
Image Quality: Inspect the phototool for any defects, such as pinholes, scratches, or incomplete coverage. Ensure that the circuit pattern is sharp, well-defined, and free from any distortions or artifacts.
-
Density and Opacity: Check the density and opacity of the opaque areas on the phototool. The opaque regions should have a high density to prevent light leakage during exposure. Use a densitometer to measure the optical density and ensure it meets the required standards.
-
Registration Marks: Verify the presence and accuracy of registration marks on the phototool. These marks are used to align the phototool with the PCB during exposure, ensuring precise image transfer.
Any phototools that fail to meet the quality standards are rejected, and the printing process is repeated until satisfactory results are achieved.
Best Practices for Phototool Creation and Handling
To ensure the best results when using phototools for PCB image transfer, consider the following best practices:
-
Use High-Quality Films: Invest in high-quality, transparent films specifically designed for phototool production. Look for films with good dimensional stability, optical clarity, and resistance to scratches and handling damage.
-
Maintain Clean Environments: Keep the phototool production area clean and free from dust, debris, and contaminants. Particles on the film surface can cause defects in the printed circuit pattern. Use clean room facilities or laminar flow hoods to minimize contamination.
-
Handle with Care: Handle phototools with care to prevent damage. Use gloves to avoid fingerprints and oils from transferring onto the film surface. Store phototools in protective sleeves or envelopes when not in use.
-
Calibrate Equipment: Regularly calibrate the imaging and printing equipment used for phototool creation. Ensure that the resolution, aperture settings, and alignment are accurate and consistent. Perform periodic maintenance to keep the equipment in optimal condition.
-
Verify Polarity and Mirroring: Double-check the polarity and mirroring requirements of the phototool before printing. Incorrect polarity or mirroring can lead to unusable phototools and wasted materials.
-
Implement Quality Control Measures: Establish a robust quality control process for phototool inspection. Define clear acceptance criteria and use standardized measuring and testing methods. Maintain detailed records of quality control results for traceability and continuous improvement.
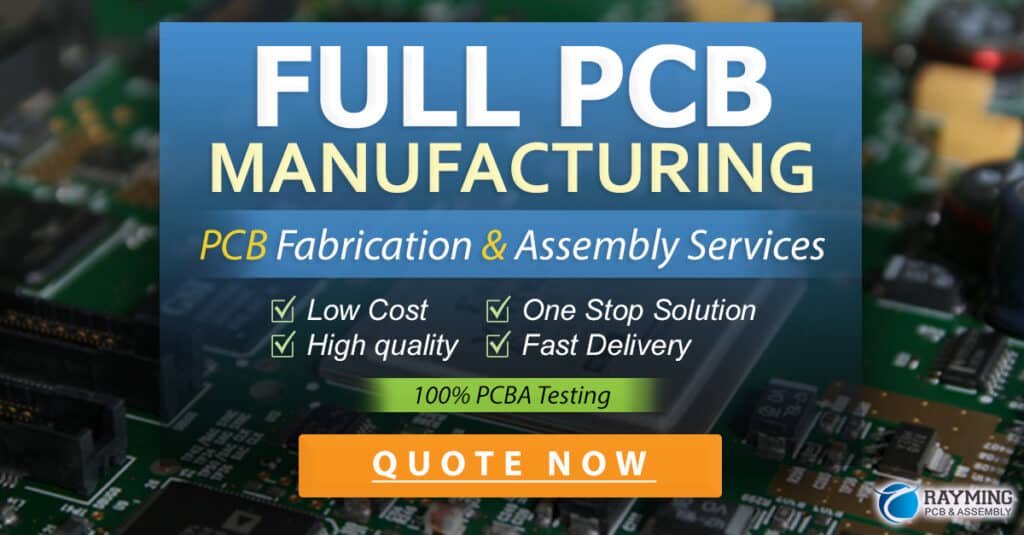
Frequently Asked Questions (FAQ)
-
What is the difference between emulsion and ink-jet phototools?
Emulsion phototools are created by exposing a light-sensitive emulsion layer on a transparent film to the circuit pattern, while ink-jet phototools are produced using high-resolution ink-jet printers that deposit UV-blocking ink onto the film. Emulsion phototools offer higher resolution but require more processing steps, whereas ink-jet phototools are faster and more cost-effective for prototyping and low-volume production. -
Can phototools be reused for multiple PCB exposures?
Yes, phototools can be reused for multiple PCB exposures as long as they remain in good condition. However, it is essential to handle phototools carefully to prevent damage, such as scratches or contamination, which can affect the quality of subsequent exposures. Regularly inspect phototools for any signs of wear or degradation and replace them when necessary. -
How do I choose the right resolution for my phototool?
The choice of resolution for a phototool depends on the PCB design requirements. Higher resolutions are necessary for fine-pitch designs and smaller features. Consult with your PCB Manufacturer or phototool provider to determine the appropriate resolution based on your specific design needs. They can provide guidance on the minimum feature size and pitch that can be reliably reproduced using their phototool production process. -
What causes pinholes in phototools, and how can they be prevented?
Pinholes in phototools are small, transparent spots in the opaque areas of the film. They can be caused by dust, debris, or contaminants on the film surface during the printing process. To prevent pinholes, maintain a clean production environment, handle phototools with care, and use high-quality films. Implementing strict quality control measures and inspecting phototools for pinholes before use can help identify and reject defective phototools. -
How should I store phototools to ensure their longevity?
Proper storage of phototools is crucial to maintain their quality and extend their lifespan. Store phototools in a cool, dry place away from direct sunlight and extreme temperatures. Use protective sleeves or envelopes to shield them from dust, moisture, and handling damage. Avoid folding or creasing the phototools, as this can cause permanent distortions in the film. When handling phototools, use gloves to prevent fingerprints and oils from transferring onto the surface.
Conclusion
Phototools play a vital role in the PCB manufacturing process, enabling the accurate transfer of circuit patterns onto the copper-clad board. By understanding the types of phototools, the creation process, and best practices for handling and quality control, PCB manufacturers can ensure high-quality image transfer and reliable PCB production. Whether using emulsion or ink-jet phototools, attention to detail and adherence to industry standards are essential for achieving optimal results.
As PCB designs continue to evolve, with smaller features and higher densities, the importance of phototools in PCB image transfer remains paramount. By staying up to date with the latest phototool technologies and best practices, PCB manufacturers can meet the ever-increasing demands of the electronics industry and deliver high-quality, reliable printed circuit boards.
Aspect | Emulsion Phototools | Ink-Jet Phototools |
---|---|---|
Resolution | High | Moderate |
Cost | Higher | Lower |
Turnaround Time | Longer | Shorter |
Suitable for | Fine-pitch designs | Prototyping and low-volume production |
Processing Steps | More complex | Simpler |
In summary, phototools are essential tools in the PCB manufacturing process, allowing for the precise transfer of circuit patterns onto the PCB substrate. By selecting the appropriate phototool type, following best practices for creation and handling, and implementing rigorous quality control measures, PCB manufacturers can ensure accurate and reliable image transfer, ultimately leading to high-quality printed circuit boards that meet the demands of today’s electronics industry.
No responses yet