What is Photolithography?
Photolithography, also known as optical lithography or UV lithography, is a process used in microfabrication to pattern parts of a thin film or the bulk of a substrate. It uses light to transfer a geometric pattern from a photomask to a photosensitive chemical photoresist on the substrate. A series of chemical treatments then either engraves the exposure pattern into the material or enables deposition of a new material in the desired pattern upon the material underneath the photoresist.
Photolithography shares some fundamental principles with photography in that the pattern in the photresist is created by exposing it to light, either directly (without using a mask) or with a projected image using an optical mask. This procedure is comparable to a high precision version of the method used to make printed circuit boards. Subsequent stages in the process have more in common with etching than with lithographic printing. It is used because it affords exact control over the shape and size of the objects it creates and because it can create patterns over an entire surface simultaneously.
History of Photolithography
The origin of photolithography can be traced back to 1796 when Alois Senefelder invented lithography as a low-cost method of publishing theatrical works. However, the modern photolithography was developed in 1959 by the American physicist and engineer Mohamed M. Atalla and the Korean engineer Dawon Kahng at Bell Labs. They developed the metal-oxide-semiconductor (MOS) process, which used silicon dioxide as a dielectric layer and silicon as a semiconductor, and used photolithography to pattern the oxide layer.
In the early 1970s, the MOS process became the dominant manufacturing process for very-large-scale integration (VLSI) chips. Since then, photolithography has continued to evolve and has been widely used in the semiconductor industry for the fabrication of integrated circuits.
Photolithography Process
The photolithography process involves several steps, which are as follows:
Step 1: Substrate Preparation
The first step in the photolithography process is to clean and prepare the substrate, which is typically a silicon wafer. The wafer is cleaned using a series of chemical baths to remove any contaminants or particles on the surface.
Step 2: Photoresist Application
After the wafer is cleaned, a thin layer of photoresist is applied to the surface of the wafer using a spin-coating process. The wafer is placed on a spinner, and a small amount of photoresist is dispensed onto the center of the wafer. The spinner then rotates at high speed, distributing the photoresist evenly across the surface of the wafer.
Step 3: Soft Bake
After the photoresist is applied, the wafer is baked on a hotplate to drive off excess solvent and to improve adhesion of the photoresist to the wafer.
Step 4: Exposure
The next step is to expose the photoresist to light through a photomask. The photomask contains the desired pattern that will be transferred to the photoresist. The wafer and photomask are aligned in a exposure tool, and the photoresist is exposed to a specific wavelength of light, typically ultraviolet (UV) light.
Step 5: Development
After exposure, the wafer is placed in a developer solution that removes the exposed (positive) or unexposed (negative) areas of the photoresist, depending on the type of photoresist used. This step creates the desired pattern in the photoresist layer.
Step 6: Hard Bake
After development, the wafer is baked again to harden the remaining photoresist and improve its adhesion to the wafer.
Step 7: Etching
The next step is to transfer the pattern from the photoresist to the underlying layer, which is typically an oxide or metal layer. This is done using an etching process, which can be either wet or dry. Wet etching uses chemical solutions to remove the unprotected areas of the underlying layer, while dry etching uses plasma or ion beams.
Step 8: Photoresist Removal
After etching, the remaining photoresist is removed using a solvent or plasma ashing process, leaving behind the desired pattern in the underlying layer.
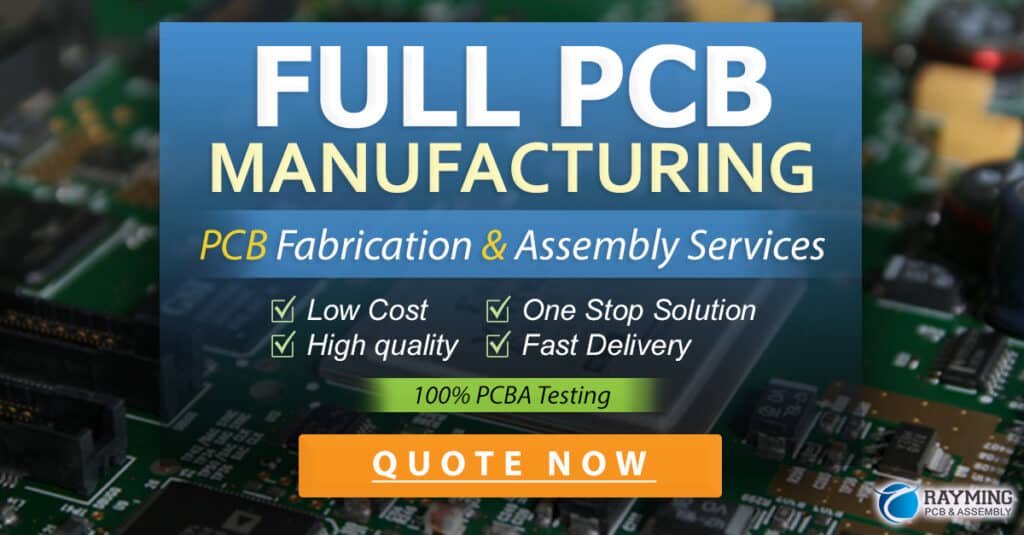
Types of Photolithography
There are two main types of photolithography: contact and projection.
Contact Photolithography
In contact photolithography, the photomask is placed in direct contact with the photoresist-coated wafer. The wafer and mask are then exposed to a uniform beam of light, typically from a mercury arc lamp. The light passes through the transparent areas of the mask and exposes the photoresist underneath.
Contact photolithography has several advantages, including high resolution and low cost. However, it also has some disadvantages, such as the potential for mask damage due to contact with the wafer and the difficulty in achieving uniform contact across the entire wafer surface.
Projection Photolithography
In projection photolithography, the photomask is placed between the light source and the wafer, and the pattern on the mask is projected onto the wafer using a lens system. This allows for a larger gap between the mask and the wafer, reducing the risk of mask damage.
Projection photolithography can be further divided into two main types: 1x projection and reduction projection.
1x Projection Photolithography
In 1x projection photolithography, the mask pattern is projected onto the wafer at a 1:1 ratio, meaning that the size of the pattern on the wafer is the same as the size of the pattern on the mask. This type of photolithography is typically used for larger feature sizes and less critical layers.
Reduction Projection Photolithography
In reduction projection photolithography, the mask pattern is projected onto the wafer at a reduced size, typically 4:1 or 5:1. This allows for smaller feature sizes and higher resolution than 1x projection photolithography. Reduction projection photolithography is widely used in the semiconductor industry for the fabrication of advanced integrated circuits.
Advantages of Photolithography
Photolithography has several advantages over other patterning techniques, such as electron beam lithography or nanoimprint lithography. Some of the main advantages of photolithography are:
-
High throughput: Photolithography can pattern large areas of a wafer simultaneously, allowing for high throughput and low cost per device.
-
High resolution: With advances in photolithography technology, feature sizes as small as a few nanometers can be achieved.
-
Versatility: Photolithography can be used to pattern a wide range of materials, including metals, semiconductors, and dielectrics.
-
Repeatability: Photolithography is a highly repeatable process, allowing for consistent results across multiple wafers and lots.
Challenges in Photolithography
Despite its many advantages, photolithography also faces several challenges, particularly as feature sizes continue to shrink. Some of the main challenges in photolithography are:
-
Diffraction: As feature sizes approach the wavelength of the exposure light, diffraction effects can limit the resolution and fidelity of the patterned features.
-
Overlay: As multiple layers are patterned on top of each other, precise alignment between layers becomes increasingly critical to ensure proper device functionality.
-
Defects: Photolithography is sensitive to defects, such as particles or scratches on the mask or wafer, which can cause yield loss and device failure.
-
Cost: As feature sizes continue to shrink, the cost of photolithography equipment and masks continues to increase, making it challenging to maintain profitability in the semiconductor industry.
Future of Photolithography
Despite the challenges facing photolithography, it remains the dominant patterning technique in the semiconductor industry and is expected to continue to be so for the foreseeable future. Several new technologies and techniques are being developed to extend the capabilities of photolithography and enable the continued scaling of semiconductor devices.
One promising approach is extreme ultraviolet (EUV) lithography, which uses light with a wavelength of 13.5 nm to achieve higher resolution and smaller feature sizes than conventional optical lithography. EUV lithography has been in development for many years and is now being used in high-volume manufacturing for the most advanced semiconductor devices.
Another approach is directed self-assembly (DSA), which uses block copolymers that self-assemble into periodic nanostructures to augment the resolution of conventional photolithography. DSA has the potential to enable the patterning of features smaller than what is achievable with photolithography alone.
Frequently Asked Questions (FAQ)
1. What is the difference between positive and negative photoresist?
Positive photoresist becomes soluble in the developer solution when exposed to light, while negative photoresist becomes insoluble in the developer solution when exposed to light. Positive photoresist is more commonly used in the semiconductor industry due to its higher resolution and better process control.
2. What is the role of the photomask in photolithography?
The photomask is a glass or quartz plate with a patterned opaque layer, typically chromium, that defines the desired pattern to be transferred to the photoresist. The photomask acts as a stencil, allowing light to pass through the transparent areas and expose the photoresist underneath.
3. What is the difference between wet and dry etching?
Wet etching uses liquid chemical solutions to remove material, while dry etching uses plasma or ion beams. Wet etching is typically isotropic, meaning that it etches in all directions equally, while dry etching can be anisotropic, meaning that it etches in a specific direction. Dry etching is more commonly used in the semiconductor industry due to its higher resolution and better process control.
4. What is the role of the hard bake step in photolithography?
The hard bake step is used to improve the adhesion of the photoresist to the wafer and to increase its resistance to the subsequent etching process. During the hard bake, the wafer is heated to a high temperature, typically around 120-180°C, which causes the photoresist to crosslink and become more stable.
5. What is the difference between contact and projection photolithography?
In contact photolithography, the photomask is placed in direct contact with the photoresist-coated wafer, while in projection photolithography, the photomask is placed between the light source and the wafer, and the pattern on the mask is projected onto the wafer using a lens system. Projection photolithography allows for a larger gap between the mask and the wafer, reducing the risk of mask damage and enabling higher resolution and smaller feature sizes.
Conclusion
Photolithography is a critical technology in the semiconductor industry, enabling the fabrication of complex integrated circuits with billions of transistors on a single chip. It has evolved over the years to keep pace with the demands for smaller feature sizes and higher device density, and continues to be the dominant patterning technique for the foreseeable future.
Despite the challenges facing photolithography, such as diffraction, overlay, defects, and cost, new technologies and techniques are being developed to extend its capabilities and enable the continued scaling of semiconductor devices. These include extreme ultraviolet (EUV) lithography and directed self-assembly (DSA), among others.
As the semiconductor industry continues to push the boundaries of what is possible with photolithography, it is clear that this technology will remain a key enabler of innovation and progress in the field of microelectronics for years to come.
No responses yet