Types of PCBA Equipment
Solder Paste Printer
A solder paste printer is used to apply solder paste onto the PCB pads before component placement. It ensures precise and consistent application of solder paste, which is essential for achieving reliable solder joints.
Solder Paste Printer Type | Features | Advantages |
---|---|---|
Stencil Printer | Uses a stencil to apply solder paste | High accuracy, suitable for high-volume production |
Jet Printer | Uses a jet dispenser to apply solder paste | Flexibility in applying solder paste on different pad sizes and shapes |
Dispensing Printer | Uses a dispensing needle to apply solder paste | Suitable for low-volume production or prototypes |
Pick and Place Machine
A pick and place machine is used to automatically place electronic components onto the PCB. It picks up components from feeders and places them accurately on the designated pads.
Pick and Place Machine Type | Features | Advantages |
---|---|---|
High-Speed Machine | High placement speed (>50,000 CPH) | Suitable for high-volume production |
Mid-Speed Machine | Moderate placement speed (20,000-50,000 CPH) | Cost-effective for medium-volume production |
Desktop Machine | Low placement speed (<10,000 CPH) | Suitable for low-volume production or prototypes |
Reflow Oven
A reflow oven is used to melt the solder paste and form permanent solder joints between the components and the PCB. It follows a specific temperature profile to ensure proper solder joint formation.
Reflow Oven Type | Features | Advantages |
---|---|---|
Convection Oven | Uses hot air convection for heating | Uniform heating, suitable for most PCBs |
Infrared Oven | Uses infrared radiation for heating | Fast heating, suitable for PCBs with high thermal mass |
Vapor Phase Oven | Uses vapor phase for heating | Uniform heating, minimal thermal stress on components |
Inspection Equipment
Inspection equipment is used to verify the quality of the assembled PCBs. It helps identify defects such as misaligned components, solder bridging, or missing components.
Inspection Equipment Type | Features | Advantages |
---|---|---|
Automated Optical Inspection (AOI) | Uses cameras and image processing algorithms | High-speed inspection, suitable for high-volume production |
X-Ray Inspection | Uses X-ray imaging to inspect hidden solder joints | Suitable for inspecting BGA and QFN packages |
Manual Inspection | Visual inspection by operators | Suitable for low-volume production or prototypes |
Soldering Equipment
Soldering equipment is used for manual soldering tasks, such as rework, repairs, or soldering through-hole components.
Soldering Equipment Type | Features | Advantages |
---|---|---|
Soldering Iron | Handheld tool for soldering | Versatile, suitable for various soldering tasks |
Soldering Station | Includes soldering iron and temperature control | Precise temperature control, suitable for sensitive components |
Desoldering Station | Includes desoldering tools for component removal | Suitable for rework and repairs |
Considerations When Selecting PCBA Equipment
When selecting PCBA equipment, consider the following factors:
-
Production Volume: Choose equipment that matches your production volume requirements. High-speed machines are suitable for high-volume production, while desktop machines are better for low-volume or prototype work.
-
PCB Complexity: Consider the complexity of your PCBs, such as component density, package types, and board size. Ensure that the equipment can handle the specific requirements of your PCBs.
-
Accuracy and Precision: Look for equipment with high accuracy and precision to ensure reliable and consistent assembly results.
-
Flexibility: If you have a diverse range of PCBs, choose equipment that offers flexibility in handling different component types, sizes, and shapes.
-
Cost: Consider your budget and the return on investment when selecting PCBA equipment. Balance the initial cost with the long-term benefits and productivity gains.
-
Maintenance and Support: Choose equipment from reputable manufacturers that offer reliable technical support and maintenance services to minimize downtime and ensure smooth operation.
Frequently Asked Questions (FAQ)
1. What is the difference between SMT and THT assembly?
SMT (Surface Mount Technology) assembly involves placing components directly onto the surface of the PCB, while THT (Through-Hole Technology) assembly involves inserting component leads through holes in the PCB and soldering them on the opposite side. SMT is more common in modern electronics due to its higher component density and faster assembly process.
2. Can I use the same solder paste for all components?
Different components may require different solder paste formulations based on their size, shape, and metallurgy. It is important to select the appropriate solder paste for each component type to ensure reliable solder joint formation.
3. How often should I calibrate my PCBA equipment?
Calibration frequency depends on the specific equipment and the manufacturer’s recommendations. Generally, it is recommended to calibrate equipment at regular intervals (e.g., every 6 months or annually) or whenever there are signs of performance degradation.
4. Can I mix and match equipment from different manufacturers?
While it is possible to use equipment from different manufacturers, it is important to ensure compatibility and smooth integration between the various machines. It is often more convenient and efficient to choose equipment from the same manufacturer or from manufacturers that have established partnerships.
5. How can I ensure the long-term reliability of my assembled PCBs?
To ensure long-term reliability, follow best practices such as using high-quality components, adhering to proper assembly procedures, implementing effective quality control measures, and conducting thorough testing and inspection. Additionally, consider factors such as thermal management, vibration resistance, and environmental protection during the design and assembly process.
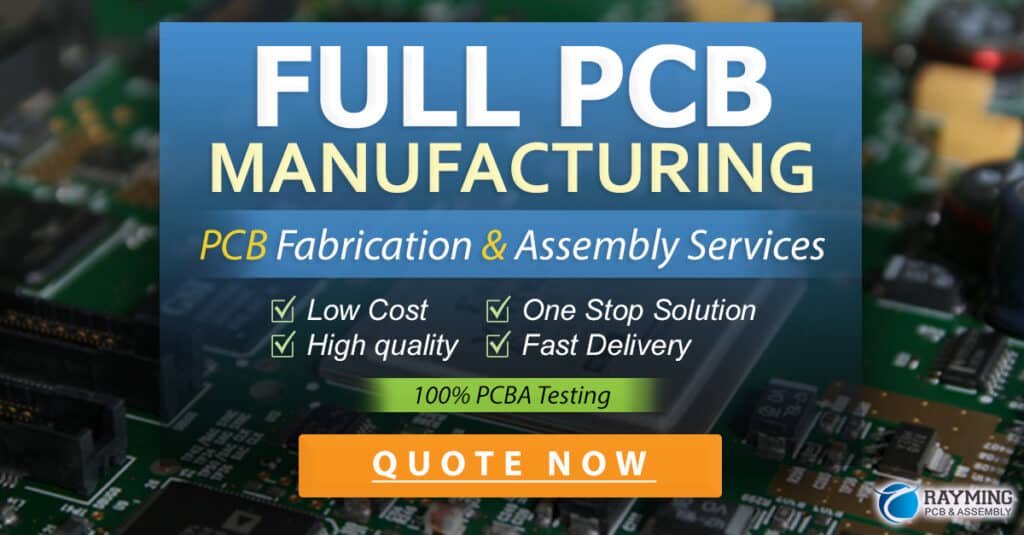
Conclusion
PCBA equipment plays a vital role in the efficient and reliable assembly of electronic devices. By understanding the different types of equipment and their functions, you can make informed decisions when selecting the right tools for your PCBA process. Consider factors such as production volume, PCB complexity, accuracy, flexibility, cost, and maintenance support when choosing equipment. With the right PCBA equipment and best practices in place, you can ensure high-quality assembly results and long-term reliability of your electronic products.
No responses yet