What is PCB X-ray Inspection?
PCB X-ray inspection is a non-destructive testing method used to examine the internal structure of printed circuit boards (PCBs) and PCB assemblies (PCBAs). This technique utilizes X-rays to penetrate through the components and substrate, allowing for the detection of various defects and anomalies that may not be visible to the naked eye or other inspection methods.
How Does PCB X-ray Inspection Work?
X-ray inspection systems generate X-rays using an X-ray tube. The X-rays pass through the PCBA, and the resulting image is captured by a detector on the opposite side. The image is then processed and displayed on a screen for analysis. The level of absorption of X-rays depends on the density and thickness of the materials being inspected. Denser materials, such as metals, absorb more X-rays than less dense materials, such as plastics or air gaps.
Types of PCB X-ray Inspection Systems
There are two main types of PCB X-ray inspection systems:
- 2D X-ray Inspection Systems
- These systems provide a two-dimensional image of the PCBA.
-
They are suitable for detecting defects in the X-Y plane, such as component placement and solder joint quality.
-
3D X-ray Inspection Systems
- These systems use computed tomography (CT) technology to generate a three-dimensional representation of the PCBA.
- They can detect defects in the X-Y-Z plane, including internal defects, such as voids, cracks, and delamination.
The Importance of PCB X-ray Inspection in PCBA
PCB X-ray inspection plays a crucial role in ensuring the quality, reliability, and functionality of PCBAs. Here are some key reasons why X-ray inspection is essential:
1. Detecting Hidden Defects
X-ray inspection can reveal defects that are not visible through other inspection methods, such as automated optical inspection (AOI) or visual inspection. Some of the hidden defects that X-ray inspection can detect include:
- Voids: Air pockets or gaps within solder joints that can weaken the connection and lead to premature failure.
- Shorts: Unintended connections between two or more conductors, which can cause electrical malfunctions.
- Cracks: Fractures in components or solder joints that can result in intermittent or complete failure.
- Delamination: Separation of layers within the PCB substrate, which can cause signal integrity issues and reduced reliability.
2. Verifying Component Placement and Solder Joint Quality
X-ray inspection can confirm the correct placement of components on the PCBA, especially for devices with high component density or those using advanced packaging technologies, such as ball grid arrays (BGAs) or quad flat no-leads (QFNs). Additionally, X-ray inspection can assess the quality of solder joints, ensuring proper wetting, fillets, and the absence of bridging or insufficient solder.
3. Compliance with Industry Standards
Many industries, such as aerospace, defense, medical, and automotive, have strict quality requirements for PCBAs. X-ray inspection helps manufacturers meet these standards by providing objective evidence of the PCBA’s internal structure and quality. Standards organizations, such as IPC (Association Connecting Electronics Industries), have established acceptance criteria for X-ray inspection of solder joints and components.
4. Reducing Rework and Scrap Costs
By identifying defects early in the manufacturing process, X-ray inspection can help reduce rework and scrap costs. Catching defects before the PCBA is assembled into a final product can save time and resources that would otherwise be spent on troubleshooting and repairs. Additionally, X-ray inspection can provide valuable feedback to improve the manufacturing process, minimizing the occurrence of defects in future production runs.
5. Ensuring Product Reliability and Customer Satisfaction
The ultimate goal of PCB X-ray inspection is to ensure the reliability and functionality of the final product. By detecting and addressing defects, manufacturers can reduce the risk of field failures and product returns, leading to improved customer satisfaction and brand reputation. In industries where product reliability is critical, such as medical devices or aerospace systems, X-ray inspection is an essential tool for guaranteeing the safety and performance of the end product.
Applications of PCB X-ray Inspection
PCB X-ray inspection is used across various industries and applications, including:
- Aerospace and Defense
- PCBAs used in aircraft, satellites, and military equipment require the highest level of reliability and performance.
-
X-ray inspection ensures compliance with strict quality standards and helps prevent failures that could have catastrophic consequences.
-
Automotive Electronics
- Modern vehicles rely heavily on electronic systems for safety, navigation, and entertainment.
-
X-ray inspection is used to verify the quality of PCBAs in critical components, such as airbag control modules, engine control units, and advanced driver assistance systems (ADAS).
-
Medical Devices
- PCBAs in medical devices, such as pacemakers, insulin pumps, and diagnostic equipment, must function reliably to ensure patient safety and well-being.
-
X-ray inspection helps manufacturers meet stringent regulatory requirements and ensure the long-term performance of these life-critical devices.
-
Consumer Electronics
- The fast-paced consumer electronics industry demands high-volume production and rapid time-to-market.
-
X-ray inspection is used to quickly identify defects in PCBAs for smartphones, laptops, gaming consoles, and other consumer devices, reducing the risk of product recalls and customer returns.
-
Industrial Equipment
- PCBAs in industrial equipment, such as process control systems, robotics, and power electronics, must withstand harsh environments and continuous operation.
- X-ray inspection ensures the reliability and durability of these PCBAs, minimizing downtime and maintenance costs.
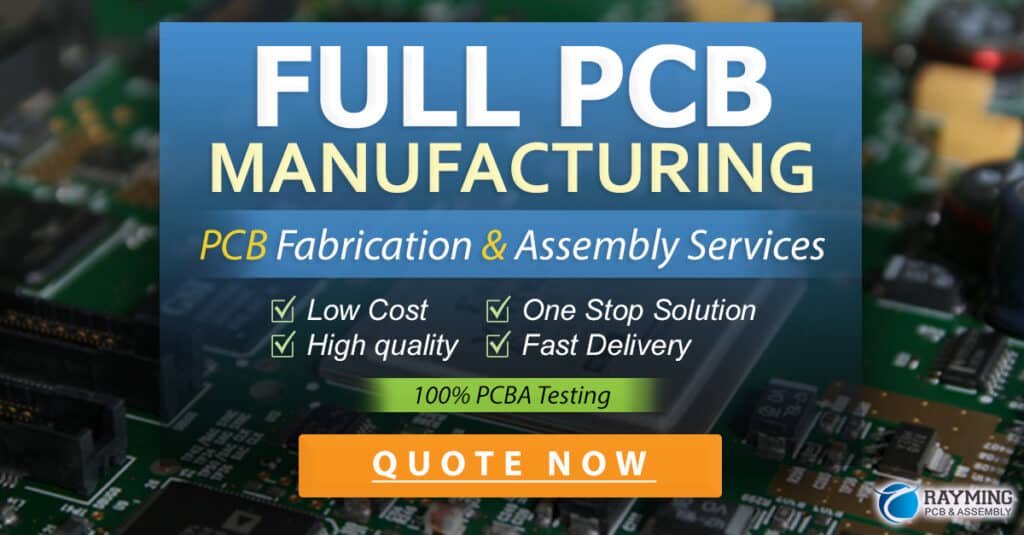
Advantages of PCB X-ray Inspection
- Non-destructive testing: X-ray inspection allows for the examination of PCBAs without damaging or altering the components or substrate.
- Comprehensive coverage: X-ray inspection can reveal defects in areas that are difficult or impossible to access with other inspection methods, such as hidden solder joints or internal layers of the PCB.
- High resolution: Advanced X-ray inspection systems can provide high-resolution images, enabling the detection of even the smallest defects.
- Automated analysis: Many X-ray inspection systems include software tools for automated defect detection and classification, reducing the need for manual interpretation and increasing inspection throughput.
- Traceability: X-ray inspection images can be stored and used as documentation for quality control and failure analysis purposes.
Limitations of PCB X-ray Inspection
- Cost: X-ray inspection systems can be expensive, especially 3D CT systems, which may limit their adoption by smaller manufacturers or those with tight budgets.
- Complexity: Interpreting X-ray images requires specialized knowledge and training, and setting up inspection programs for complex PCBAs can be time-consuming.
- Radiation safety: X-ray inspection systems emit ionizing radiation, which requires proper safety protocols and shielding to protect operators and nearby personnel.
- Limited material detection: X-ray inspection may have difficulty detecting defects in materials with similar densities, such as distinguishing between different types of plastics or organic compounds.
Best Practices for PCB X-ray Inspection
- Establish inspection criteria: Define clear acceptance criteria for X-ray inspection based on industry standards, customer requirements, and product specifications.
- Optimize inspection parameters: Adjust X-ray system settings, such as voltage, current, and magnification, to achieve the best image quality for the specific PCBA being inspected.
- Implement a multi-stage inspection approach: Combine X-ray inspection with other inspection methods, such as AOI and electrical testing, to create a comprehensive quality control process.
- Train operators: Ensure that X-ray inspection operators are properly trained in system operation, image interpretation, and safety protocols.
- Regularly calibrate and maintain equipment: Perform periodic calibration and maintenance of X-ray inspection systems to ensure consistent and accurate results.
FAQ
-
Q: Is X-ray inspection safe for the components and PCBAs being inspected?
A: Yes, X-ray inspection is a non-destructive testing method that does not damage or alter the components or PCBAs being inspected. However, proper safety protocols must be followed to protect operators from X-ray exposure. -
Q: Can X-ray inspection detect all types of defects?
A: While X-ray inspection is a powerful tool for detecting hidden defects, it may have limitations in detecting defects in materials with similar densities or very small defects below the system’s resolution. -
Q: How long does X-ray inspection take?
A: The inspection time depends on the complexity of the PCBA, the type of X-ray system used, and the inspection coverage required. 2D X-ray inspection can be relatively fast, while 3D CT inspection may take longer due to the need for multiple projections and image reconstruction. -
Q: Can X-ray inspection be automated?
A: Yes, many X-ray inspection systems include software tools for automated defect detection and classification, which can increase inspection throughput and reduce the need for manual interpretation. -
Q: Is X-ray inspection required for all PCBAs?
A: The need for X-ray inspection depends on the specific industry, product requirements, and quality standards. Some industries, such as aerospace and medical devices, have strict requirements for X-ray inspection, while others may use it selectively based on product complexity or risk.
Conclusion
PCB X-ray inspection is a vital tool for ensuring the quality, reliability, and functionality of PCBAs across various industries. By providing a non-destructive means of examining the internal structure of PCBAs, X-ray inspection can detect hidden defects, verify component placement and solder joint quality, and help manufacturers meet strict industry standards. Implementing X-ray inspection as part of a comprehensive quality control process can reduce rework and scrap costs, improve product reliability, and enhance customer satisfaction. As electronic products continue to become more complex and miniaturized, the importance of PCB X-ray inspection will only continue to grow, making it an essential technology for manufacturers striving to deliver high-quality, reliable products to their customers.
No responses yet