Introduction to PCB Warpage
Printed Circuit Board (PCB) warpage is a critical issue in the electronics manufacturing industry. It refers to the unintended alteration of a circuit board’s shape, resulting in a non-flat or distorted board. PCB warpage can occur during various stages of the manufacturing process, such as lamination, soldering, or even during the product’s usage. This phenomenon can lead to several problems, including difficulty in component assembly, reduced reliability, and even complete failure of the electronic device.
Causes of PCB Warpage
Several factors can contribute to PCB warpage, including:
Material Properties
The choice of materials used in PCB fabrication plays a significant role in determining the likelihood of warpage. The thermal expansion coefficients of the different layers in a PCB, such as the copper foil, prepreg, and core materials, can vary significantly. When exposed to heat during the manufacturing process or during use, these layers may expand or contract at different rates, leading to warpage.
Manufacturing Process
The manufacturing process itself can introduce stresses that lead to PCB warpage. For example, during the lamination process, where the layers of the PCB are pressed together under high temperature and pressure, uneven heating or cooling can cause the board to warp. Similarly, during the soldering process, the high temperatures involved can cause the board to distort if not properly controlled.
Environmental Factors
Environmental factors, such as humidity and temperature changes, can also contribute to PCB warpage. Moisture absorption by the PCB materials can cause swelling, while temperature fluctuations can lead to thermal expansion and contraction, both of which can result in warpage.
Effects of PCB Warpage
PCB warpage can have several detrimental effects on the functionality and reliability of electronic devices:
Component Assembly Difficulties
When a PCB is warped, it can be challenging to place and solder components accurately. Surface mount components, in particular, require a flat surface for proper placement and soldering. Warpage can lead to misaligned or poorly soldered components, which can cause short circuits, open connections, or other defects.
Reduced Reliability
Warped PCBs can experience increased mechanical stress, particularly at the solder joints. This stress can lead to cracks or fractures in the solder, resulting in intermittent or complete failure of the electronic device. Additionally, warpage can cause components to detach from the board, further reducing the reliability of the product.
Impaired Thermal Management
Proper thermal management is crucial for the performance and longevity of electronic devices. A warped PCB can hinder the efficient dissipation of heat, as it may not make proper contact with heatsinks or other cooling solutions. This can lead to increased component temperatures, which can accelerate the degradation of the device and shorten its lifespan.
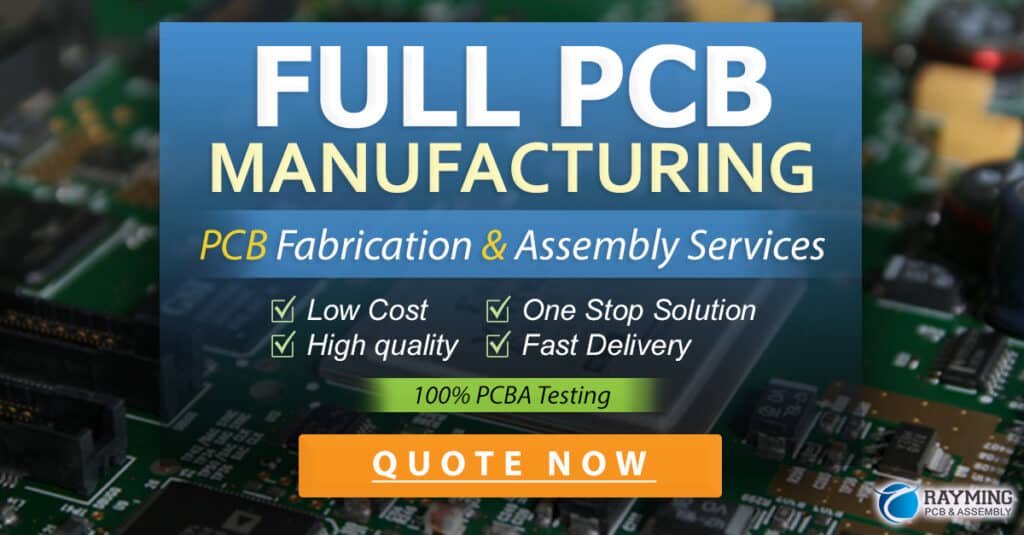
Mitigating PCB Warpage
To minimize the occurrence and impact of PCB warpage, several strategies can be employed:
Material Selection
Choosing materials with similar thermal expansion coefficients can help reduce the likelihood of warpage. For example, using a core material with a coefficient of thermal expansion (CTE) that closely matches that of the copper foil can minimize the stress caused by differential expansion.
Design Considerations
Incorporating design features that promote flatness can help mitigate warpage. For example, using symmetrical layer stackups, where the copper layers are balanced on either side of the board, can help distribute the stresses evenly. Additionally, using copper pours or other reinforcing structures can help stiffen the board and reduce warpage.
Process Control
Strict control over the manufacturing process parameters can help minimize warpage. For example, ensuring even heating and cooling during lamination, as well as maintaining proper temperature profiles during soldering, can reduce the stresses that lead to warpage. Implementing quality control measures, such as flatness inspections, can help identify and address warpage issues early in the manufacturing process.
Measuring and Quantifying PCB Warpage
To effectively address PCB warpage, it is essential to have methods for measuring and quantifying the extent of the distortion. Several techniques can be used for this purpose:
3D Scanning
3D scanning technologies, such as structured light or laser scanning, can create a detailed digital model of the PCB surface. These scans can provide precise measurements of the board’s flatness, allowing for the identification of warped areas and the quantification of the distortion.
Shadow Moiré
Shadow moiré is an optical measurement technique that uses the interference patterns created by a grating and a light source to visualize surface contours. By projecting a grating onto the PCB surface and observing the resulting moiré fringes, the flatness of the board can be assessed and quantified.
Coordinate Measuring Machines (CMMs)
CMMs are precision measurement devices that use a probe to collect data points on the surface of an object. By scanning the PCB surface with a CMM, a detailed map of the board’s topography can be created, allowing for the identification and quantification of warpage.
Standards and Specifications for PCB Flatness
To ensure the quality and reliability of electronic products, several industry standards and specifications have been established to define acceptable levels of PCB flatness. Some of the most widely used standards include:
IPC-TM-650 2.4.22
This standard, developed by the Association Connecting Electronics Industries (IPC), provides a method for measuring the flatness of PCBs using a dial indicator or other suitable measurement device. It defines the maximum allowable deviation from flatness for various board sizes and thicknesses.
IPC-6012
IPC-6012 is a generic performance specification for rigid printed boards. It includes requirements for board flatness, with different allowable deviations based on the board’s class (Class 1, 2, or 3) and the stage of manufacturing (before or after solder mask application).
JEDEC JESD22-B112A
This standard, developed by the Joint Electron Device Engineering Council (JEDEC), provides a method for measuring the coplanarity of surface mount pads on a PCB. While not directly measuring flatness, coplanarity is related to the overall flatness of the board and is crucial for successful component assembly.
FAQ
1. What is PCB warpage?
PCB warpage is the unintended distortion or deviation from flatness that occurs in a printed circuit board. It can manifest as a twist, bow, or other non-flat shape.
2. What causes PCB warpage?
PCB warpage can be caused by several factors, including differences in the thermal expansion coefficients of the materials used, stresses introduced during the manufacturing process, and environmental factors such as humidity and temperature changes.
3. How does PCB warpage affect electronic devices?
PCB warpage can lead to difficulties in component assembly, reduced reliability due to increased mechanical stress on solder joints, and impaired thermal management. These issues can result in short circuits, open connections, component detachment, and premature device failure.
4. What can be done to mitigate PCB warpage?
Strategies for mitigating PCB warpage include careful selection of materials with similar thermal expansion coefficients, incorporating design features that promote flatness (such as symmetrical layer stackups and reinforcing structures), and implementing strict process controls during manufacturing.
5. How is PCB warpage measured and quantified?
PCB warpage can be measured and quantified using various techniques, such as 3D scanning, shadow moiré, and coordinate measuring machines (CMMs). These methods allow for the creation of detailed surface maps and the precise measurement of flatness deviations.
Conclusion
PCB warpage is a significant challenge in the electronics manufacturing industry, with the potential to cause a range of problems that can compromise the functionality and reliability of electronic devices. By understanding the causes and effects of warpage, as well as the strategies for mitigation and the methods for measurement and quantification, manufacturers can take proactive steps to ensure the production of high-quality, reliable PCBs. Adherence to industry standards and specifications, coupled with continuous improvement in materials, design, and process control, will be essential for minimizing the impact of PCB warpage and delivering electronic products that meet the ever-increasing demands of the market.
No responses yet