Introduction to PCB Interconnections
Printed Circuit Boards (PCBs) are the backbone of modern electronics, providing a platform for interconnecting various components to create complex circuits. One critical aspect of PCB design is the interconnection between transmitters and receivers, which is achieved through transmission lines. PCB transmission lines are essential for ensuring reliable and efficient signal transmission within a PCB.
What are PCB Transmission Lines?
PCB transmission lines are conductive traces on a PCB that are designed to carry high-frequency signals between components. These traces are carefully engineered to maintain signal integrity and minimize signal degradation caused by factors such as impedance mismatches, reflections, and crosstalk.
Types of PCB Transmission Lines
There are several types of PCB transmission lines, each with its own characteristics and applications. The most common types include:
-
Microstrip: A microstrip is a transmission line consisting of a conductive trace on one side of a dielectric substrate, with a ground plane on the other side. Microstrips are widely used in high-frequency applications due to their simplicity and ease of fabrication.
-
Stripline: A stripline is a transmission line that is sandwiched between two ground planes, with a dielectric material separating the trace from the ground planes. Striplines offer better isolation and reduced radiation compared to microstrips, making them suitable for applications requiring low noise and high isolation.
-
Coplanar Waveguide (CPW): A coplanar waveguide consists of a conductive trace with ground planes on either side, all on the same side of the dielectric substrate. CPWs offer lower dispersion and better impedance control compared to microstrips and striplines.
-
Grounded Coplanar Waveguide (GCPW): A grounded coplanar waveguide is similar to a CPW, but with an additional ground plane on the opposite side of the substrate. GCPWs provide better isolation and reduced radiation compared to CPWs.
Design Considerations for PCB Transmission Lines
Designing PCB transmission lines requires careful consideration of several factors to ensure optimal signal transmission and minimize signal degradation. Some of the key design considerations include:
Impedance Matching
Impedance matching is crucial for minimizing reflections and ensuring efficient power transfer between the transmitter and receiver. The characteristic impedance of a transmission line should match the output impedance of the transmitter and the input impedance of the receiver. Common characteristic impedances for PCB transmission lines are 50Ω, 75Ω, and 100Ω.
Trace Width and Thickness
The width and thickness of a transmission line trace affect its characteristic impedance and current-carrying capacity. Wider traces have lower impedance and higher current-carrying capacity, while narrower traces have higher impedance and lower current-carrying capacity. The optimal trace width and thickness depend on the desired characteristic impedance, the dielectric material, and the operating frequency.
Dielectric Material
The choice of dielectric material affects the propagation velocity, impedance, and loss of a transmission line. Common dielectric materials used in PCBs include FR-4, Rogers, and Teflon. Each material has its own dielectric constant (εr) and loss tangent (tanδ), which determine the transmission line’s performance.
Length Matching
Length matching is essential for ensuring that signals arrive at the receiver at the same time, particularly in high-speed digital systems. Mismatched trace lengths can cause signal skew, leading to timing errors and reduced system performance. Length matching can be achieved through careful PCB layout and the use of serpentine routing or meandering techniques.
Termination
Proper termination of transmission lines is necessary to minimize reflections and ensure signal integrity. There are several termination techniques, including:
- Series Termination: A series resistor is placed near the transmitter to match the transmission line’s impedance.
- Parallel Termination: A resistor is placed at the receiver end, parallel to the transmission line, to match the line’s impedance.
- AC Termination: A series resistor and a parallel capacitor are used to provide frequency-dependent termination, suitable for high-frequency applications.
The choice of termination technique depends on the specific application, signal characteristics, and design constraints.
Analyzing PCB Transmission Lines
Analyzing PCB transmission lines is essential for optimizing their performance and ensuring reliable signal transmission. Several tools and techniques are available for analyzing transmission lines, including:
Time-Domain Reflectometry (TDR)
Time-Domain Reflectometry (TDR) is a technique used to characterize transmission lines by sending a fast rise time pulse through the line and measuring the reflections. TDR can help identify impedance discontinuities, length mismatches, and other anomalies in the transmission line.
Frequency-Domain Analysis
Frequency-domain analysis involves measuring the transmission line’s scattering parameters (S-parameters) using a vector network analyzer (VNA). S-parameters provide information about the transmission line’s impedance, insertion loss, return loss, and crosstalk. This information can be used to optimize the Transmission Line Design and ensure compliance with performance specifications.
Electromagnetic Simulation
Electromagnetic simulation tools, such as HFSS, CST, and ADS, can be used to model and simulate PCB transmission lines. These tools solve Maxwell’s equations to predict the transmission line’s behavior, including impedance, propagation velocity, and field distributions. Simulation results can be used to optimize the transmission line design before fabrication, saving time and resources.
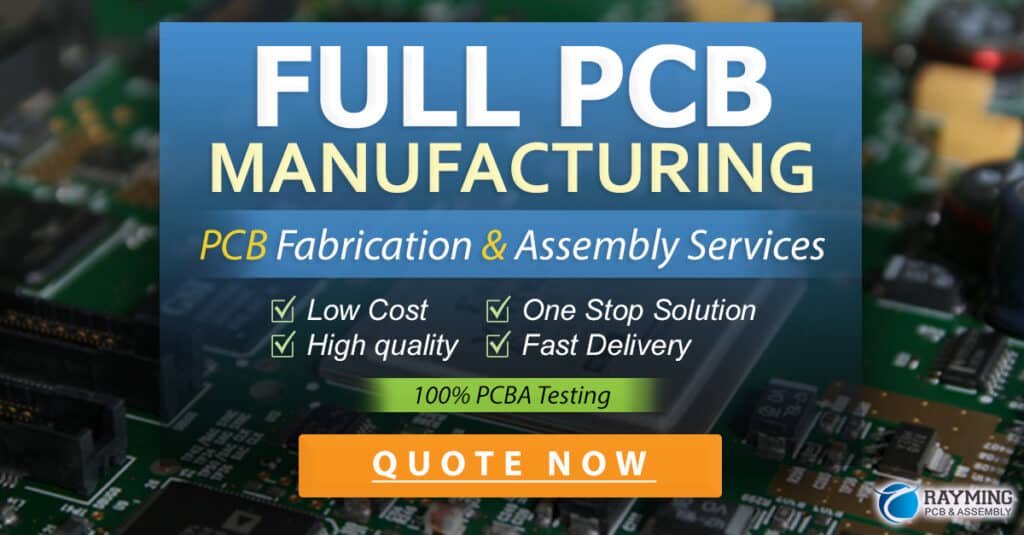
PCB Transmission Line Examples
Here are a few examples of PCB transmission lines and their applications:
High-Speed Digital Interfaces
High-speed digital interfaces, such as USB, PCIe, and HDMI, rely on well-designed transmission lines to ensure signal integrity and minimize bit errors. These interfaces typically use differential signaling, where a pair of transmission lines carry complementary signals. Proper impedance matching, length matching, and termination are critical for achieving the desired performance.
RF and Microwave Circuits
RF and microwave circuits, such as filters, amplifiers, and antennas, often use transmission lines to interconnect components and achieve the desired frequency response. Microstrip and coplanar waveguide transmission lines are commonly used in these applications due to their ease of fabrication and compatibility with surface-mount components.
Automotive and Industrial Applications
PCB transmission lines are also used in automotive and industrial applications, where reliability and robustness are paramount. For example, Controller Area Network (CAN) buses in vehicles use twisted-pair transmission lines to communicate between various electronic control units (ECUs). In industrial settings, RS-485 and Profibus communication protocols rely on well-designed transmission lines to ensure reliable data transmission in noisy environments.
FAQ
Q1: What is the difference between a microstrip and a stripline?
A1: A microstrip is a transmission line with a conductive trace on one side of a dielectric substrate and a ground plane on the other side. In contrast, a stripline is a transmission line that is sandwiched between two ground planes, with a dielectric material separating the trace from the ground planes. Striplines offer better isolation and reduced radiation compared to microstrips.
Q2: Why is impedance matching important in PCB transmission lines?
A2: Impedance matching is crucial for minimizing reflections and ensuring efficient power transfer between the transmitter and receiver. When the characteristic impedance of a transmission line matches the output impedance of the transmitter and the input impedance of the receiver, signal reflections are minimized, and maximum power transfer is achieved.
Q3: What is the purpose of length matching in PCB transmission lines?
A3: Length matching ensures that signals arrive at the receiver at the same time, particularly in high-speed digital systems. Mismatched trace lengths can cause signal skew, leading to timing errors and reduced system performance. By carefully matching the lengths of transmission lines, designers can minimize signal skew and ensure proper system operation.
Q4: How can electromagnetic simulation tools help in designing PCB transmission lines?
A4: Electromagnetic simulation tools, such as HFSS, CST, and ADS, can be used to model and simulate PCB transmission lines before fabrication. These tools solve Maxwell’s equations to predict the transmission line’s behavior, including impedance, propagation velocity, and field distributions. By simulating the transmission line design, engineers can optimize its performance and identify potential issues early in the design process, saving time and resources.
Q5: What are some common applications of PCB transmission lines?
A5: PCB transmission lines are used in a wide range of applications, including:
– High-speed digital interfaces, such as USB, PCIe, and HDMI
– RF and microwave circuits, such as filters, amplifiers, and antennas
– Automotive and industrial communication protocols, such as CAN and RS-485
In each of these applications, well-designed transmission lines are essential for ensuring reliable signal transmission and maintaining system performance.
Conclusion
PCB transmission lines play a crucial role in interconnecting transmitters and receivers in a PCB, ensuring reliable and efficient signal transmission. By understanding the types of transmission lines, their design considerations, and analysis techniques, engineers can create robust and high-performance PCBs for a wide range of applications.
Proper impedance matching, trace geometry, dielectric material selection, length matching, and termination are all essential aspects of transmission line design. Time-domain reflectometry, frequency-domain analysis, and electromagnetic simulation are powerful tools for analyzing and optimizing transmission line performance.
As the demand for high-speed, high-frequency, and high-reliability electronic systems continues to grow, the importance of well-designed PCB transmission lines will only increase. By mastering the principles and techniques of transmission line design, engineers can create PCBs that meet the evolving needs of modern electronics.
No responses yet