Understanding the Basics of PCB Design
Before diving into advanced PCBHacks, it’s essential to have a solid foundation in PCB design basics. Let’s review some key concepts:
PCB Layers and Their Functions
A typical PCB consists of multiple layers, each serving a specific purpose:
Layer | Function |
---|---|
Copper Layers | Conductive pathways for electrical signals |
Substrate | Insulating material separating copper layers |
Solder Mask | Protective coating to prevent short circuits |
Silkscreen | Text and symbols for component identification |
Component Placement and Orientation
Proper component placement and orientation are crucial for a successful PCB design:
- Place components logically, considering signal flow and functionality
- Minimize the distance between related components to reduce signal integrity issues
- Orient components for optimal routing and manufacturing ease
Trace Routing and Width Considerations
When routing traces on your PCB, keep these factors in mind:
- Choose appropriate trace widths based on current requirements and manufacturing constraints
- Maintain consistent trace widths to avoid impedance mismatches
- Use smooth corners and avoid sharp angles to minimize signal reflections
Advanced PCBHacks for Improved Signal Integrity
Signal integrity is a critical aspect of PCB design, especially in high-speed and sensitive applications. Here are some advanced PCBHacks to optimize your design for better signal integrity:
Impedance Matching Techniques
Proper impedance matching ensures that signals propagate smoothly without reflections or distortions:
- Calculate and maintain consistent characteristic impedance for critical traces
- Use termination resistors to match source and load impedances
- Implement differential pair routing for high-speed signals
Ground Plane Strategies
A well-designed ground plane is essential for minimizing noise and providing a stable reference for signals:
- Use a solid ground plane to minimize loop areas and provide shielding
- Implement ground plane stitching vias to maintain low-impedance return paths
- Avoid splitting the ground plane unnecessarily, as it can create ground loops
Decoupling and Bypass Capacitors
Decoupling and bypass capacitors help stabilize power supply voltages and reduce high-frequency noise:
- Place decoupling capacitors close to power pins of ICs
- Use a combination of bulk and ceramic capacitors for effective noise suppression
- Minimize the loop area between the capacitor and the power/ground pins
PCBHacks for Electromagnetic Compatibility (EMC)
Ensuring your PCB design is electromagnetically compatible is crucial to prevent interference and comply with regulations. Consider these PCBHacks for better EMC performance:
Shielding Techniques
Shielding helps contain electromagnetic fields and prevents interference between components:
- Use shielding cans or enclosures for sensitive components
- Implement guard traces or ground planes around critical signals
- Utilize shielded connectors and cables for external interfaces
Grounding and Isolation
Proper grounding and isolation techniques minimize electromagnetic coupling and noise:
- Implement separate analog and digital ground planes, connected at a single point
- Use isolation techniques, such as optocouplers or transformers, for sensitive signals
- Maintain adequate spacing between high-speed signals and sensitive components
Filtering and Suppression
Filtering and suppression components help attenuate unwanted frequencies and transients:
- Use ferrite beads or common-mode chokes to suppress high-frequency noise
- Implement LC filters for power supply lines
- Include transient voltage suppressors (TVS) for protection against voltage spikes
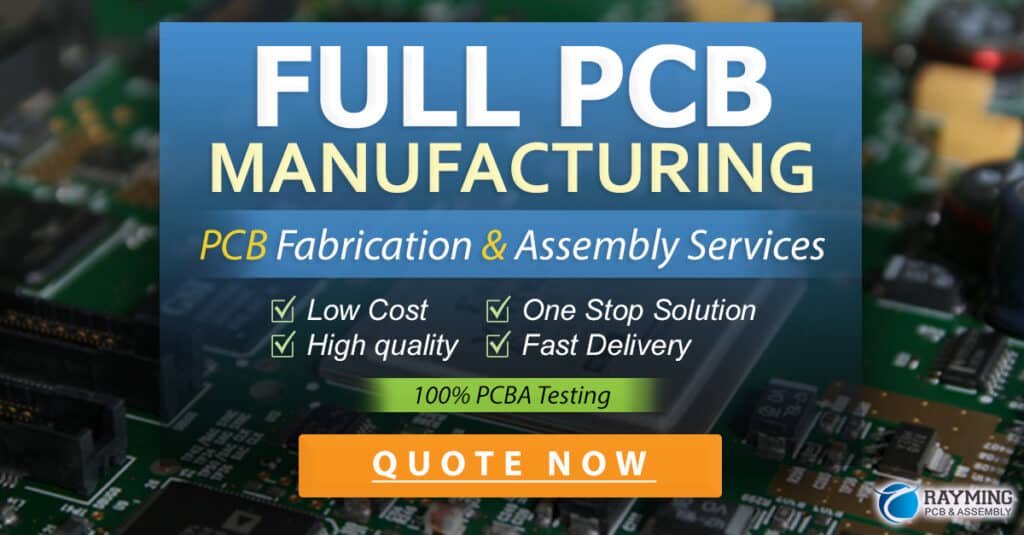
PCBHacks for Thermal Management
Effective thermal management is essential to ensure your PCB operates reliably and within safe temperature limits. Consider these PCBHacks for better heat dissipation:
Thermal Vias and Pads
Thermal vias and pads provide efficient heat transfer from components to the PCB:
- Use thermal vias to conduct heat from component pads to internal or bottom layers
- Increase the size of Thermal Pads for better heat spreading
- Use thermal interface materials (TIM) between components and heatsinks
Copper Pours and Planes
Copper pours and planes help distribute heat evenly across the PCB:
- Utilize large copper pours on the top and bottom layers for better heat dissipation
- Consider using thicker copper layers for improved thermal conductivity
- Maintain adequate spacing between heat-generating components
Heatsinks and Cooling Solutions
Heatsinks and other cooling solutions provide additional heat dissipation capabilities:
- Select appropriate heatsinks based on component power dissipation and thermal resistance
- Consider using forced air cooling, such as fans, for high-power applications
- Implement liquid cooling solutions for extreme thermal demands
PCBHacks for Manufacturing and Assembly
Designing your PCB with manufacturing and assembly in mind can save time, reduce costs, and improve overall quality. Here are some PCBHacks to optimize your design for production:
Design for Manufacturing (DFM)
DFM guidelines ensure your PCB can be manufactured reliably and cost-effectively:
- Adhere to minimum trace width and spacing requirements for your chosen manufacturing process
- Use standard hole sizes and pad dimensions for easy drilling and soldering
- Avoid acute angles and maintain minimum annular ring sizes for vias
Panelization and Breakouts
Panelization and breakouts allow for efficient mass production of PCBs:
- Group multiple PCBs into a single panel for cost-effective manufacturing
- Include breakout tabs or mousebites for easy separation of individual boards
- Incorporate fiducial marks and tooling holes for accurate alignment during assembly
Pick-and-Place (PnP) Considerations
Designing your PCB with PnP assembly in mind streamlines the manufacturing process:
- Provide adequate clearance around components for pick-and-place machine access
- Use standard component packages and orientations for compatibility with PnP equipment
- Include polarity marks and reference designators for accurate component placement
Frequently Asked Questions (FAQ)
-
What is the importance of a well-designed ground plane in a PCB?
A well-designed ground plane is crucial for maintaining signal integrity, reducing noise, and providing a stable reference for electrical signals. It helps minimize loop areas, provides shielding, and ensures low-impedance return paths for currents. -
How can I ensure proper impedance matching in my PCB design?
To ensure proper impedance matching, calculate and maintain consistent characteristic impedance for critical traces. Use termination resistors to match source and load impedances, and implement differential pair routing for high-speed signals. Consult your PCB manufacturer for specific impedance requirements and design guidelines. -
What are some effective techniques for minimizing electromagnetic interference (EMI) in a PCB?
To minimize EMI, consider shielding sensitive components using shielding cans or enclosures. Implement guard traces or ground planes around critical signals, and utilize shielded connectors and cables for external interfaces. Proper grounding, isolation, filtering, and suppression techniques also help reduce electromagnetic coupling and noise. -
How can I optimize my PCB design for better thermal management?
To optimize thermal management, use thermal vias to conduct heat from component pads to internal or bottom layers, and increase the size of thermal pads for better heat spreading. Utilize large copper pours on the top and bottom layers for even heat distribution, and consider using thicker copper layers for improved thermal conductivity. Select appropriate heatsinks and cooling solutions based on component power dissipation and thermal resistance. -
What are some key considerations when designing a PCB for manufacturing and assembly?
When designing a PCB for manufacturing and assembly, adhere to design for manufacturing (DFM) guidelines, such as minimum trace width and spacing requirements, standard hole sizes, and pad dimensions. Consider panelization and breakouts for efficient mass production, and include fiducial marks and tooling holes for accurate alignment during assembly. Design your PCB with pick-and-place (PnP) assembly in mind by providing adequate clearance around components and using standard component packages and orientations.
By implementing these PCBHacks and best practices, you’ll be well on your way to creating robust, reliable, and high-performance PCBs. Remember, continuous learning and staying up-to-date with the latest techniques and technologies is key to mastering the art of PCB design.
No responses yet