Introduction to PCB Thermal Resistance
Printed Circuit Boards (PCBs) are the backbone of modern electronic devices, providing a platform for components to be mounted and interconnected. As electronic systems become more complex and power-dense, managing heat dissipation becomes increasingly critical. PCB thermal resistance plays a crucial role in determining a circuit board’s ability to effectively dissipate heat and maintain optimal operating temperatures for components.
What is PCB Thermal Resistance?
PCB thermal resistance is a measure of a circuit board’s ability to resist the flow of heat from a heat source to a heat sink. It quantifies the temperature difference between the heat source and the heat sink divided by the power dissipated. In simpler terms, it indicates how effectively a PCB can transfer heat away from hot components and prevent thermal buildup.
The thermal resistance of a PCB is influenced by several factors, including:
- PCB material properties
- Copper thickness and distribution
- Number of layers and their arrangement
- Thermal vias and heat spreaders
- Component placement and power dissipation
Understanding and optimizing PCB thermal resistance is essential for designing reliable and efficient electronic systems.
Importance of PCB Thermal Management
Effective thermal management is critical for ensuring the reliability, performance, and longevity of electronic devices. When components operate at high temperatures, they can experience several issues:
- Reduced reliability: High temperatures accelerate the aging process of components, leading to premature failures and shortened product lifespans.
- Performance degradation: Many electronic components, such as processors and power devices, exhibit reduced performance at elevated temperatures.
- Safety concerns: Overheating can pose safety risks, such as fire hazards or burns to users.
- Compliance issues: Electronic devices must comply with thermal safety standards and regulations to ensure user safety and avoid legal liabilities.
By minimizing PCB thermal resistance and implementing effective thermal management techniques, designers can mitigate these issues and create robust electronic systems.
Factors Affecting PCB Thermal Resistance
PCB Material Properties
The choice of PCB material significantly influences its thermal resistance. The two primary thermal properties to consider are thermal conductivity and thermal expansion coefficient.
Thermal Conductivity
Thermal conductivity is a measure of a material’s ability to conduct heat. Materials with higher thermal conductivity allow heat to flow more easily, resulting in lower thermal resistance. Common PCB materials and their thermal conductivities are listed in the table below:
Material | Thermal Conductivity (W/mK) |
---|---|
FR-4 | 0.3 – 0.4 |
Aluminum | 205 – 237 |
Copper | 385 – 401 |
Ceramic (Alumina) | 20 – 30 |
Polyimide | 0.1 – 0.35 |
Choosing materials with higher thermal conductivity, such as metal-core PCBs or ceramic substrates, can significantly reduce thermal resistance.
Thermal Expansion Coefficient
The thermal expansion coefficient (CTE) describes how much a material expands or contracts with changes in temperature. Mismatches in CTE between the PCB material and components can lead to mechanical stress and failures.
To minimize CTE mismatches, designers can:
- Select PCB materials with CTEs closely matching those of critical components.
- Use techniques like underfilling or conformal coating to provide mechanical support.
- Employ flexible interconnects or stress-relief features to accommodate thermal expansion.
Copper Thickness and Distribution
Copper is an excellent thermal conductor and plays a vital role in heat dissipation on PCBs. The thickness and distribution of copper on a PCB directly impact its thermal resistance.
Copper Thickness
Increasing the thickness of copper traces and planes reduces thermal resistance by providing a larger cross-sectional area for heat flow. Typical copper thicknesses range from 0.5 oz/ft² (17.5 μm) to 4 oz/ft² (140 μm) or more in high-power applications.
Thicker copper also allows for higher current-carrying capacity, which is essential for power delivery and minimizing voltage drops.
Copper Distribution
The distribution of copper on a PCB affects heat spreading and thermal resistance. Techniques to optimize copper distribution include:
- Using large, unbroken copper planes for power and ground layers to maximize heat spreading.
- Placing copper pours or fills in unused areas to increase thermal mass and conductivity.
- Strategically placing thermal vias to provide low-resistance paths for heat transfer between layers.
- Designing wide, short traces for high-current paths to minimize resistive heating.
Number of Layers and Their Arrangement
Multi-layer PCBs offer several advantages for thermal management compared to single-layer boards.
Benefits of Multi-Layer PCBs
- Increased thermal mass: Additional layers provide more copper for heat storage and dissipation.
- Improved heat spreading: Inner layers can be dedicated to power and ground planes, efficiently spreading heat across the board.
- Reduced thermal resistance: Multiple layers allow for more thermal vias and shorter heat paths between components and heat sinks.
Layer Arrangement
The arrangement of layers in a multi-layer PCB can be optimized for thermal performance:
- Place power and ground planes close to heat-generating components for efficient heat transfer.
- Alternate signal and plane layers to minimize thermal coupling and crosstalk.
- Use thermally conductive dielectric materials between layers to enhance heat transfer.
Thermal Vias and Heat Spreaders
Thermal vias and heat spreaders are essential tools for managing heat flow on PCBs.
Thermal Vias
Thermal vias are plated through-holes that provide low-resistance paths for heat transfer between layers. They are typically placed under or near heat-generating components to conduct heat to inner layers or the opposite side of the board.
Guidelines for effective thermal via design include:
- Use a sufficient number of vias to provide adequate heat transfer.
- Place vias as close to the heat source as possible to minimize thermal resistance.
- Select appropriate via sizes and pitches based on the component and PCB layout.
- Consider using filled or capped vias to enhance thermal conductivity and prevent solder wicking.
Heat Spreaders
Heat spreaders are metal structures, such as copper or aluminum plates, that are attached to the PCB to improve heat dissipation. They work by increasing the surface area for heat exchange and conducting heat away from hot components.
Heat spreaders can be integrated into the PCB design in several ways:
- Metal-core PCBs: The PCB substrate is replaced with a metal core, such as aluminum, which acts as a built-in heat spreader.
- Copper coins or slugs: Thick copper pieces are embedded in the PCB under high-power components to enhance local heat spreading.
- External heat spreaders: Metal plates are attached to the PCB surface using thermal adhesives or mechanical fasteners.
Component Placement and Power Dissipation
The placement of components on a PCB and their power dissipation significantly influence thermal resistance.
Component Placement
Proper component placement can minimize thermal resistance and prevent hot spots:
- Place high-power components near the edge of the board or close to heat sinks for better heat dissipation.
- Separate heat-generating components to avoid thermal coupling and local temperature rises.
- Orient components to maximize heat transfer to thermal vias or planes.
- Consider airflow patterns when placing components to optimize convective cooling.
Power Dissipation
Understanding the power dissipation of components is crucial for effective thermal management. Designers should:
- Calculate the expected power dissipation of each component based on its electrical characteristics and operating conditions.
- Use power dissipation data to guide component selection and placement decisions.
- Verify the maximum allowable temperature rise for each component to ensure reliable operation.
- Consider using power management techniques, such as dynamic power scaling or sleep modes, to reduce overall power dissipation.
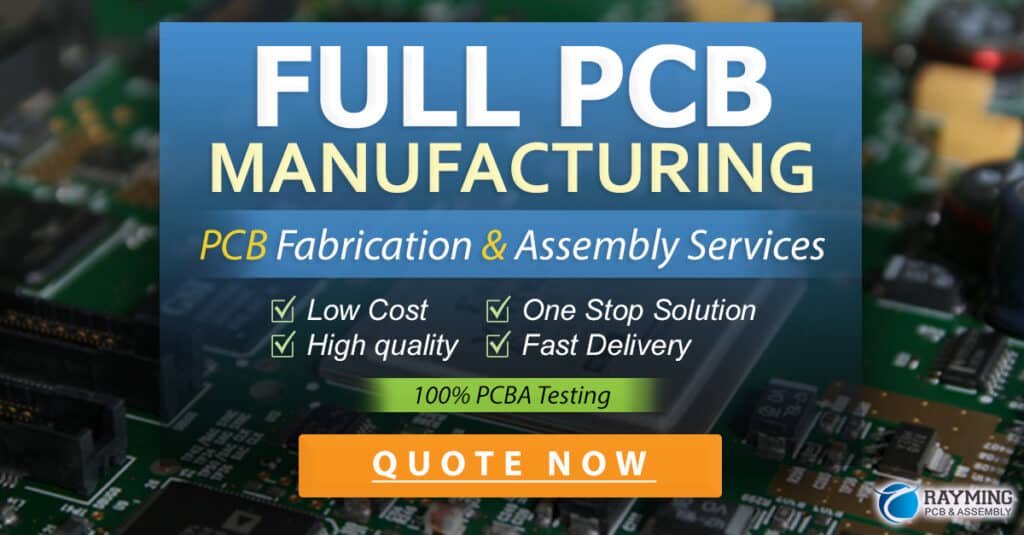
Thermal Resistance Calculation and Modeling
To optimize PCB thermal resistance, designers need to calculate and model the thermal behavior of the board.
Thermal Resistance Calculation
The thermal resistance of a PCB can be calculated using the following equation:
Rth = (Tcase - Tambient) / P
Where:
– Rth is the thermal resistance in °C/W
– Tcase is the temperature of the component case in °C
– Tambient is the ambient temperature in °C
– P is the power dissipated by the component in W
This equation provides a simplified estimate of thermal resistance, assuming steady-state conditions and one-dimensional heat flow.
Thermal Modeling and Simulation
For more accurate and detailed thermal analysis, designers use thermal modeling and simulation tools. These tools allow for the creation of virtual prototypes and the prediction of temperature distributions and heat flow paths on PCBs.
Common thermal modeling and simulation techniques include:
- Finite Element Analysis (FEA): FEA tools discretize the PCB into small elements and solve heat transfer equations to predict temperature distributions.
- Computational Fluid Dynamics (CFD): CFD tools model the airflow and convective heat transfer around the PCB, considering factors such as fan placement and enclosure design.
- Compact Thermal Models (CTMs): CTMs are simplified thermal models that represent components and the PCB as a network of thermal resistances and capacitances.
Thermal modeling and simulation enable designers to:
- Identify hot spots and thermal bottlenecks early in the design process.
- Evaluate the effectiveness of different thermal management strategies.
- Optimize component placement, copper distribution, and thermal via layout.
- Ensure the PCB operates within acceptable temperature limits.
Best Practices for Minimizing PCB Thermal Resistance
To minimize PCB thermal resistance and ensure effective heat dissipation, designers should follow these best practices:
- Choose PCB materials with high thermal conductivity and closely matched CTEs.
- Use thick copper layers and optimize copper distribution for efficient heat spreading.
- Employ multi-layer PCB designs with dedicated power and ground planes.
- Incorporate thermal vias and heat spreaders strategically to enhance heat transfer.
- Optimize component placement to minimize thermal coupling and leverage airflow.
- Understand component power dissipation and select components with appropriate thermal ratings.
- Use thermal modeling and simulation to validate and optimize the thermal design.
- Consider active cooling solutions, such as fans or heatsinks, for high-power applications.
- Adhere to thermal safety standards and regulations.
- Perform thorough thermal testing and validation to ensure the PCB operates within acceptable temperature limits.
By following these best practices, designers can create PCBs with lower thermal resistance, improved reliability, and enhanced performance.
Conclusion
PCB thermal resistance is a critical factor in the design of reliable and efficient electronic systems. By understanding the factors that influence thermal resistance and implementing effective thermal management techniques, designers can minimize thermal issues and ensure optimal performance.
Key considerations for minimizing PCB thermal resistance include:
- Material selection
- Copper thickness and distribution
- Multi-layer PCB design
- Thermal vias and heat spreaders
- Component placement and power dissipation
- Thermal modeling and simulation
By following best practices and leveraging advanced thermal management solutions, designers can create PCBs that effectively dissipate heat, maintain acceptable operating temperatures, and deliver robust performance in demanding applications.
Frequently Asked Questions (FAQ)
1. What is PCB thermal resistance, and why is it important?
PCB thermal resistance is a measure of a circuit board’s ability to resist the flow of heat from a heat source to a heat sink. It is important because it determines how effectively a PCB can dissipate heat and maintain optimal operating temperatures for components. High thermal resistance can lead to reliability issues, performance degradation, and safety concerns.
2. What factors influence PCB thermal resistance?
Several factors influence PCB thermal resistance, including:
- PCB material properties, such as thermal conductivity and thermal expansion coefficient
- Copper thickness and distribution
- Number of layers and their arrangement
- Thermal vias and heat spreaders
- Component placement and power dissipation
3. How can I reduce thermal resistance in my PCB design?
To reduce thermal resistance in your PCB design, you can:
- Choose PCB materials with high thermal conductivity and closely matched CTEs
- Use thick copper layers and optimize copper distribution
- Employ multi-layer PCB designs with dedicated power and ground planes
- Incorporate thermal vias and heat spreaders strategically
- Optimize component placement to minimize thermal coupling and leverage airflow
4. What are thermal vias, and how do they help with heat dissipation?
Thermal vias are plated through-holes that provide low-resistance paths for heat transfer between layers. They are typically placed under or near heat-generating components to conduct heat to inner layers or the opposite side of the board. Thermal vias help to reduce thermal resistance by providing efficient pathways for heat to flow away from hot components.
5. How can thermal modeling and simulation help in PCB thermal management?
Thermal modeling and simulation tools allow designers to create virtual prototypes and predict temperature distributions and heat flow paths on PCBs. These tools enable designers to identify hot spots and thermal bottlenecks early in the design process, evaluate the effectiveness of different thermal management strategies, and optimize component placement, copper distribution, and thermal via layout. By using thermal modeling and simulation, designers can ensure that the PCB operates within acceptable temperature limits and minimize the need for costly design iterations.
No responses yet