1. Visual Inspection
Visual inspection is the first and most basic form of PCB Testing. It involves examining the PCB for any visible defects or anomalies using the naked eye or magnification tools. Some of the aspects checked during visual inspection include:
- Proper alignment and spacing of components
- Correct placement of labels and markings
- Absence of scratches, cracks, or other physical damage
- Proper solder joint formation
- Cleanliness of the board
While visual inspection cannot detect all issues, it is an essential first step in identifying any obvious problems that may affect the PCB’s performance.
2. Automated Optical Inspection (AOI)
Automated Optical Inspection (AOI) is a more advanced form of visual inspection that uses cameras and image processing software to detect defects on the PCB. AOI systems can quickly scan the entire board and compare it to a reference image to identify any discrepancies. Some of the defects that AOI can detect include:
- Missing or misaligned components
- Incorrect component polarity
- Solder bridging or insufficient solder
- Lifted or tombstoned components
- Contamination or foreign objects on the board
AOI is a fast and efficient method of detecting surface-level defects, making it an essential tool in high-volume PCB manufacturing.
3. X-Ray Inspection
X-ray inspection is a non-destructive testing method that uses X-rays to create images of the internal structure of the PCB. This method is particularly useful for inspecting solder joints and other hidden features that are not visible from the surface. X-ray inspection can detect issues such as:
- Voids or cracks in solder joints
- Insufficient or excessive solder
- Misaligned or shifted components
- Broken or damaged traces or vias
X-ray inspection is especially important for testing high-density boards with ball grid array (BGA) or chip-scale package (CSP) components, where visual inspection is not possible.
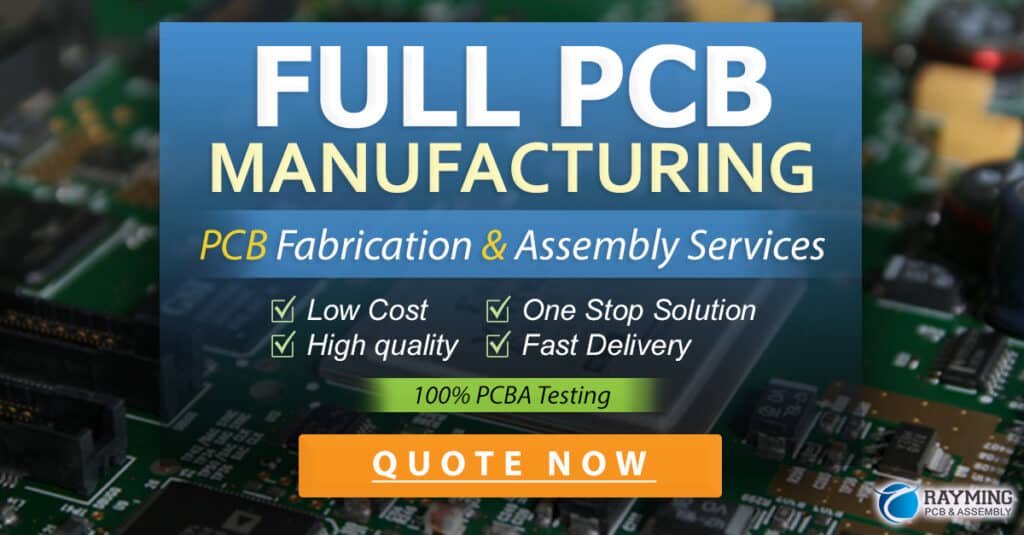
4. In-Circuit Testing (ICT)
In-Circuit Testing (ICT) is a method of testing the individual components on a PCB to ensure they are functioning correctly and are properly connected. ICT involves using a bed-of-nails fixture that makes contact with specific points on the board, allowing the tester to apply signals and measure the response of each component. ICT can detect issues such as:
- Open or short circuits
- Incorrect component values
- Missing or damaged components
- Incorrect component orientation
ICT is a comprehensive testing method that can identify a wide range of defects, but it requires the development of a custom test fixture for each PCB design.
5. Flying Probe Testing
Flying probe testing is an alternative to ICT that uses movable test probes instead of a fixed bed-of-nails fixture. The probes can be programmed to contact specific points on the PCB to perform electrical tests similar to ICT. Flying probe testing offers several advantages over ICT, including:
- No need for custom test fixtures
- Ability to test multiple PCB designs with the same equipment
- Faster setup and changeover times
- Better accessibility for testing high-density boards
However, flying probe testing is generally slower than ICT and may not be suitable for high-volume production.
6. Boundary Scan Testing
Boundary scan testing, also known as JTAG (Joint Test Action Group) testing, is a method of testing the interconnections between digital components on a PCB. It involves using a special test access port (TAP) built into the components to control and monitor their inputs and outputs. Boundary scan testing can detect issues such as:
- Open or short circuits between components
- Stuck-at faults (inputs or outputs stuck at a fixed value)
- Delay faults (signal timing issues)
Boundary scan testing is particularly useful for testing complex digital circuits with many interconnected components, such as microprocessors and FPGAs.
7. Functional Testing
Functional testing involves testing the PCB as a complete system to ensure it performs its intended function correctly. This may involve applying inputs to the board and measuring the outputs, or running software tests to verify the functionality of the board’s firmware or software. Functional testing can detect issues such as:
- Incorrect or missing functionality
- Performance issues or bottlenecks
- Compatibility problems with other components or systems
- Software bugs or glitches
Functional testing is typically performed after the PCB has passed all other tests and is ready for final assembly or integration into a larger system.
8. Environmental Testing
Environmental testing involves subjecting the PCB to various environmental conditions to ensure it can operate reliably in its intended environment. Some common environmental tests include:
- Temperature cycling: Exposing the PCB to alternating high and low temperatures to simulate thermal stress
- Humidity testing: Exposing the PCB to high humidity levels to test its resistance to moisture
- Vibration testing: Subjecting the PCB to mechanical vibrations to test its resistance to shock and vibration
- Electromagnetic compatibility (EMC) testing: Testing the PCB’s ability to operate without causing or being affected by electromagnetic interference
Environmental testing is crucial for PCBs that will be used in harsh or demanding environments, such as automotive, aerospace, or industrial applications.
Summary
In summary, the eight essential PCB testing methods are:
- Visual Inspection
- Automated Optical Inspection (AOI)
- X-Ray Inspection
- In-Circuit Testing (ICT)
- Flying Probe Testing
- Boundary Scan Testing
- Functional Testing
- Environmental Testing
Each of these methods plays a critical role in ensuring the quality, reliability, and functionality of PCBs. By employing a combination of these testing methods, manufacturers can identify and rectify defects early in the production process, reducing the risk of costly failures or recalls later on.
FAQ
-
Q: What is the difference between ICT and flying probe testing?
A: ICT uses a fixed bed-of-nails test fixture to make contact with specific points on the PCB, while flying probe testing uses movable test probes. Flying probe testing offers more flexibility and faster setup times but is slower than ICT for high-volume production. -
Q: Can X-ray inspection detect all types of solder joint defects?
A: X-ray inspection is very effective at detecting hidden solder joint defects such as voids, cracks, and insufficient or excessive solder. However, it may not detect some surface-level defects such as cold joints or contamination. -
Q: Is boundary scan testing only applicable to digital components?
A: Yes, boundary scan testing is specifically designed for testing the interconnections between digital components that have a built-in test access port (TAP). It is not applicable to analog components or simple digital components without a TAP. -
Q: How do I choose the right combination of PCB testing methods for my product?
A: The choice of PCB testing methods depends on factors such as the complexity of the board, the production volume, the intended application, and the cost and time constraints. It is best to consult with an experienced PCB testing provider to develop a comprehensive testing plan that meets your specific needs. -
Q: Can functional testing alone guarantee the quality of a PCB?
A: While functional testing is an essential part of ensuring the overall performance of a PCB, it is not sufficient on its own. Functional testing should be performed in addition to other testing methods that can detect defects or issues at the component or board level, such as AOI, ICT, or X-ray inspection.
No responses yet