Why is PCB Testing Important?
PCB testing is essential for several reasons:
- Ensures the reliability and functionality of the PCB
- Identifies defects and issues early in the manufacturing process
- Reduces the risk of product failures and recalls
- Helps maintain the quality and consistency of the final product
- Saves time and money by catching problems before the final assembly
Types of PCB Testing
There are various types of PCB tests that can be performed, depending on the specific requirements of the project. Some of the most common types of PCB tests include:
1. Visual Inspection
Visual inspection is the first step in PCB testing. It involves examining the PCB for any visible defects, such as:
- Incorrect component placement
- Solder bridges or shorts
- Damaged or missing components
- Incorrect labeling or markings
This inspection can be done manually or using automated optical inspection (AOI) systems.
2. Continuity Testing
Continuity testing is used to verify that all the connections on the PCB are intact and there are no open circuits. This test is performed using a multimeter or a dedicated Continuity Tester. The test involves:
- Placing probes on the two points of the circuit that need to be tested
- Checking the resistance between the two points
- Verifying that the resistance is within the acceptable range
3. Solder Paste Inspection (SPI)
Solder paste inspection is performed before the components are placed on the PCB. It ensures that the solder paste is applied correctly and in the right amount. SPI systems use 3D scanning technology to inspect the solder paste and provide feedback on any issues, such as:
- Insufficient or excess solder paste
- Incorrect solder paste placement
- Solder paste contamination
4. In-Circuit Testing (ICT)
In-circuit testing is a comprehensive test that verifies the functionality of individual components on the PCB. It involves:
- Placing the PCB in a test fixture with probes that contact the test points on the board
- Applying signals to the test points and measuring the response
- Comparing the measured values to the expected values to identify any issues
ICT can detect problems such as:
- Incorrect component values
- Shorted or open circuits
- Incorrect component orientation
- Missing or damaged components
5. Functional Testing
Functional testing is performed to verify that the PCB functions as intended in its final application. This test involves:
- Connecting the PCB to its intended system or a test jig that simulates the final application
- Applying power and input signals to the PCB
- Measuring the output signals and comparing them to the expected values
Functional testing can identify issues such as:
- Incorrect output signals
- Timing or synchronization problems
- Compatibility issues with other components or systems
PCB Testing Equipment
To perform the various types of PCB tests, specialized equipment is required. Some of the most common PCB testing equipment includes:
- Multimeters: Used for continuity testing and measuring voltage, current, and resistance
- Oscilloscopes: Used for measuring and analyzing electrical signals
- Logic Analyzers: Used for testing and debugging digital circuits
- In-Circuit Testers: Used for performing in-circuit testing
- Flying Probe Testers: Used for testing PCBs without the need for a custom test fixture
- Boundary Scan Testers: Used for testing complex PCBs with high component density
- Automated Optical Inspection (AOI) Systems: Used for visual inspection of PCBs
- X-Ray Inspection Systems: Used for inspecting solder joints and other internal structures of the PCB
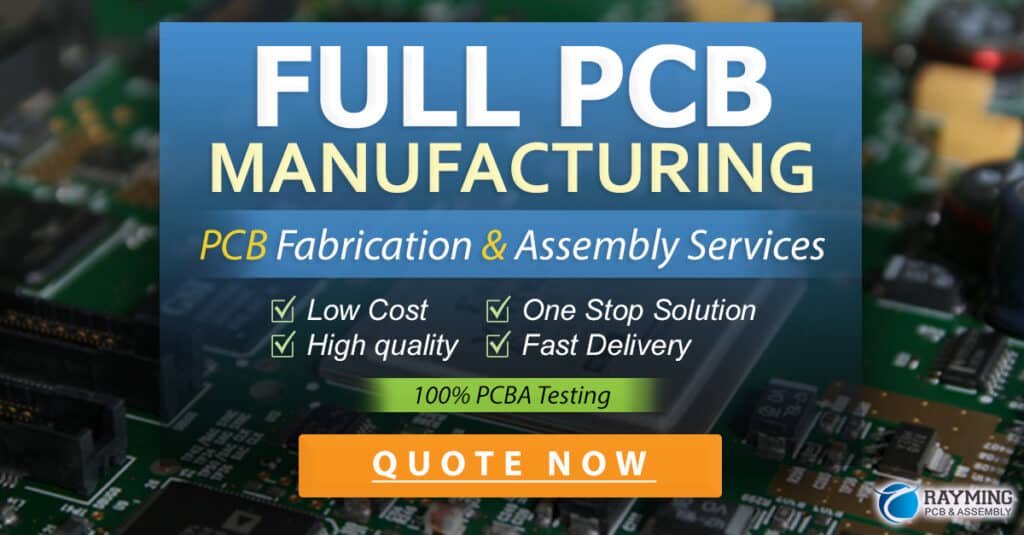
Best Practices for PCB Testing
To ensure that PCB testing is performed effectively and efficiently, it is important to follow some best practices:
- Develop a comprehensive test plan that covers all the required tests and specifications
- Use high-quality test equipment that is calibrated and maintained regularly
- Train the testing personnel on the proper use of the equipment and the test procedures
- Establish clear pass/fail criteria for each test and document the results
- Use statistical process control (SPC) techniques to monitor the testing process and identify any trends or issues
- Continuously review and update the testing process based on feedback and new requirements
PCB Testing Challenges and Solutions
Despite the importance of PCB testing, there are several challenges that can arise during the process. Some of the most common challenges and their solutions include:
Challenge | Solution |
---|---|
High component density | Use advanced testing techniques such as boundary scan testing or X-ray inspection |
Miniaturization of components | Use specialized test equipment with high precision and accuracy |
Complexity of PCB designs | Develop comprehensive test plans and use automated testing systems |
Time and cost constraints | Optimize the testing process and use parallel testing techniques |
Lack of skilled personnel | Provide training and development opportunities for testing personnel |
Frequently Asked Questions (FAQ)
- What is the difference between PCB testing and PCB inspection?
-
PCB testing involves verifying the functionality and performance of the PCB, while PCB inspection focuses on identifying any visual defects or issues with the PCB.
-
Can all types of PCBs be tested using the same equipment?
-
No, different types of PCBs may require specialized testing equipment depending on their complexity, component density, and other factors.
-
How often should PCB testing be performed?
-
PCB testing should be performed at various stages of the manufacturing process, including prototyping, production, and final assembly. The frequency of testing depends on the specific requirements of the project and the quality control standards.
-
What are the most common defects found during PCB testing?
-
Some of the most common defects found during PCB testing include open circuits, short circuits, incorrect component values, missing or damaged components, and soldering issues.
-
How can PCB testing be automated?
- PCB testing can be automated using various systems such as in-circuit testers, flying probe testers, and automated optical inspection systems. These systems can perform tests quickly and accurately, reducing the need for manual testing.
Conclusion
PCB testing is a critical step in the manufacturing process of electronic devices. It ensures that the PCBs are functioning correctly and meet the required specifications before they are assembled into the final product. By understanding the different types of tests, the equipment used, and the best practices for conducting these tests, manufacturers can ensure the quality and reliability of their products. While there are challenges associated with PCB testing, following the solutions and best practices outlined in this guide can help overcome these challenges and achieve successful PCB testing results.
No responses yet