Introduction
Printed Circuit Boards (PCBs) are the backbone of modern electronics, found in almost every electronic device we use today. They provide a platform for electronic components to be mounted and interconnected, enabling the device to function as intended. However, one of the most critical factors that can affect the performance and lifespan of a PCB is its temperature. High temperatures can cause a range of issues, from reduced efficiency to complete failure of the board.
In this comprehensive guide, we will explore the topic of PCB Temperature in detail. We will discuss what causes high temperatures, how they affect the performance of the board, and what steps can be taken to manage and mitigate these issues. Whether you are an electronics engineer, a PCB designer, or simply someone interested in learning more about this crucial aspect of electronics, this guide will provide you with the knowledge and tools you need to ensure your PCBs operate at optimal temperatures.
What Causes High Temperatures in PCBs?
There are several factors that can contribute to high temperatures in PCBs. Some of the most common causes include:
Power Dissipation
One of the primary causes of high temperatures in PCBs is power dissipation. When electronic components on the board consume power, they generate heat as a byproduct. The more power a component consumes, the more heat it will generate. If this heat is not effectively dissipated, it can lead to high temperatures on the board.
Ambient Temperature
The ambient temperature of the environment in which the PCB is operating can also have a significant impact on its temperature. If the surrounding air is already hot, it will be more difficult for the board to dissipate heat effectively. This is particularly important in applications where the PCB is housed in an enclosure with limited airflow.
Component Placement
The placement of components on the PCB can also affect its temperature. If components that generate a lot of heat are placed too close together, it can create hot spots on the board. Similarly, if components are placed too close to the edge of the board, it can limit the board’s ability to dissipate heat effectively.
Trace Width and Thickness
The width and thickness of the traces on the PCB can also have an impact on its temperature. Thinner traces have higher resistance, which can lead to increased power dissipation and heat generation. Similarly, traces that are too narrow may not be able to handle the amount of current flowing through them, leading to overheating.
How High Temperatures Affect PCB Performance
High temperatures can have a range of negative effects on the performance of a PCB. Some of the most significant impacts include:
Reduced Component Lifespan
One of the most significant effects of high temperatures on PCBs is reduced component lifespan. Electronic components are designed to operate within a specific temperature range, and exposure to high temperatures can cause them to degrade more quickly. This can lead to reduced reliability and increased failure rates over time.
Increased Power Consumption
High temperatures can also cause electronic components to consume more power than they would at lower temperatures. This is because the resistance of the components increases with temperature, leading to higher power dissipation. This can reduce the overall efficiency of the device and lead to increased energy costs.
Reduced Signal Integrity
High temperatures can also affect the signal integrity of the PCB. As the temperature of the board increases, the dielectric constant of the PCB material can change, leading to changes in the impedance of the traces. This can cause signal reflections and distortions, which can negatively impact the performance of the device.
Warping and Delamination
In extreme cases, high temperatures can cause the PCB to warp or delaminate. This occurs when the different layers of the board expand at different rates due to the heat, causing them to separate or bend. This can lead to broken connections and complete failure of the board.
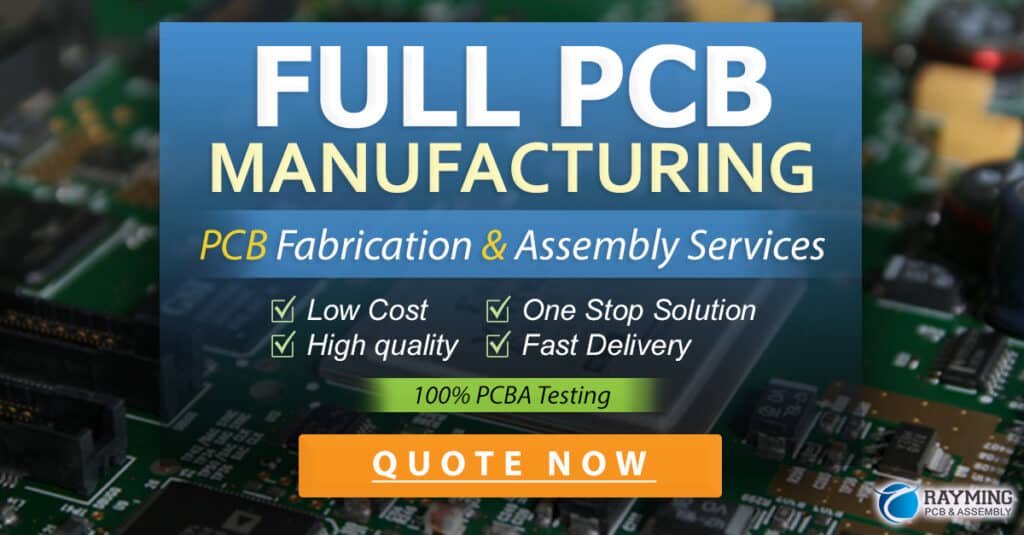
Managing High Temperatures in PCBs
Given the significant negative impacts of high temperatures on PCBs, it is crucial to take steps to manage and mitigate these issues. Some of the most effective strategies for managing high temperatures in PCBs include:
Proper Component Selection
One of the most important steps in managing high temperatures in PCBs is proper component selection. When choosing components for your board, it is important to consider their power dissipation and temperature ratings. Components with lower power dissipation will generate less heat, while components with higher temperature ratings will be more resilient to high temperatures.
Effective Thermal Management
Effective thermal management is another crucial aspect of managing high temperatures in PCBs. This can involve a range of strategies, such as using heatsinks or fans to dissipate heat away from the board, using thermal interface materials to improve heat transfer between components and the board, and designing the board with adequate spacing between components to allow for proper airflow.
PCB Material Selection
The material used to construct the PCB can also have a significant impact on its ability to manage high temperatures. Some materials, such as FR-4, have higher thermal conductivity than others, allowing them to dissipate heat more effectively. In applications where high temperatures are a significant concern, it may be necessary to use specialized materials such as metal-core PCBs or ceramic substrates.
Proper Trace Design
Proper trace design is another important factor in managing high temperatures in PCBs. Traces should be designed with adequate width and thickness to handle the amount of current flowing through them without overheating. In addition, traces should be routed in a way that minimizes the amount of heat generated by the board, such as by avoiding sharp angles or placing high-power traces too close together.
Active Cooling
In some cases, passive thermal management strategies may not be sufficient to keep PCB temperatures within acceptable limits. In these situations, active cooling methods such as forced air cooling or liquid cooling may be necessary. These methods involve using external devices to actively remove heat from the board, allowing it to operate at lower temperatures.
PCB Temperature Monitoring
In addition to taking steps to manage high temperatures in PCBs, it is also important to monitor the temperature of the board during operation. This can help identify potential issues before they lead to failure, as well as provide valuable data for optimizing the design of the board. Some common methods for monitoring PCB temperature include:
Thermocouples
Thermocouples are simple, inexpensive devices that can be used to measure the temperature of a PCB at a specific point. They consist of two dissimilar metals that generate a voltage when exposed to a temperature gradient. By placing thermocouples at key points on the board, designers can monitor the temperature of critical components and identify potential hot spots.
Resistance Temperature Detectors (RTDs)
RTDs are another type of temperature sensor that can be used to monitor PCB temperature. They work by measuring the change in resistance of a metal element as its temperature changes. RTDs are generally more accurate than thermocouples but are also more expensive.
Infrared Cameras
Infrared cameras can be used to create a thermal map of the entire PCB, allowing designers to identify hot spots and temperature gradients across the board. This can be particularly useful for identifying issues with component placement or trace routing that may not be apparent from point measurements alone.
PCB Temperature Standards and Regulations
There are several industry standards and regulations that govern the acceptable temperature ranges for PCBs in various applications. Some of the most common standards include:
IPC-2221
IPC-2221 is a standard for the design of PCBs that includes guidelines for managing high temperatures. It specifies maximum allowable temperatures for various classes of PCBs based on their intended application and the materials used in their construction.
IEC 61189-3
IEC 61189-3 is an international standard that specifies test methods for determining the thermal properties of PCB materials. It includes guidelines for measuring the thermal conductivity, thermal resistance, and other key parameters of PCB materials.
UL 94
UL 94 is a safety standard that specifies flammability requirements for PCBs and other electronic components. It includes guidelines for testing the flammability of PCB materials and specifies maximum allowable temperatures for various classes of materials.
FAQs
-
Q: What is the ideal operating temperature range for a PCB?
A: The ideal operating temperature range for a PCB depends on the specific application and the materials used in its construction. In general, most PCBs are designed to operate between -40°C and 85°C, although some specialized applications may require higher or lower temperature ranges. -
Q: How can I tell if my PCB is overheating?
A: There are several signs that a PCB may be overheating, including reduced performance, increased power consumption, and physical damage such as discoloration or warping. If you suspect that your PCB is overheating, you can use temperature monitoring methods such as thermocouples or infrared cameras to measure its temperature directly. -
Q: What are some common causes of PCB overheating?
A: Some common causes of PCB overheating include inadequate thermal management, improper component selection, and design issues such as inadequate trace widths or spacing between components. Environmental factors such as high ambient temperatures or inadequate airflow can also contribute to overheating. -
Q: Can high temperatures cause permanent damage to a PCB?
A: Yes, exposure to high temperatures can cause permanent damage to a PCB, including component degradation, delamination of the board layers, and even complete failure of the board. It is important to take steps to manage high temperatures and ensure that the board operates within its specified temperature range to avoid these issues. -
Q: How can I improve the thermal management of my PCB design?
A: There are several steps you can take to improve the thermal management of your PCB design, including: -
Selecting components with lower power dissipation and higher temperature ratings
- Using thermal interface materials to improve heat transfer between components and the board
- Designing the board with adequate spacing between components to allow for proper airflow
- Using heatsinks or other passive cooling methods to dissipate heat away from the board
- Considering active cooling methods such as forced air or liquid cooling for high-temperature applications
By taking a proactive approach to thermal management in your PCB design, you can help ensure that your board operates reliably and efficiently even in challenging environmental conditions.
Conclusion
Managing high temperatures is a critical aspect of PCB design and operation. By understanding the causes and effects of high temperatures, as well as the strategies for mitigating these issues, designers can create PCBs that are more reliable, efficient, and long-lasting.
From proper component selection and thermal management to active cooling and temperature monitoring, there are a range of tools and techniques available for managing PCB temperatures. By staying up to date with industry standards and best practices, and by taking a proactive approach to thermal management in their designs, PCB designers can help ensure that their boards are able to operate safely and effectively in even the most demanding environments.
Parameter | Value |
---|---|
Ideal Operating Temperature Range | -40°C to 85°C |
Common Causes of Overheating | Inadequate thermal management, improper component selection, design issues |
Strategies for Improving Thermal Management | Component selection, thermal interface materials, adequate component spacing, heatsinks, active cooling |
Industry Standards for PCB Temperatures | IPC-2221, IEC 61189-3, UL 94 |
By following the guidelines and best practices outlined in this guide, PCB designers can help ensure that their boards are able to operate reliably and efficiently, even in challenging environmental conditions. With a focus on thermal management and a commitment to staying up to date with industry standards and best practices, designers can create PCBs that are able to meet the demands of even the most complex and demanding applications.
No responses yet