What is PCB Surface Finish?
PCB surface finish is the final coating applied to the exposed copper traces and pads on a PCB. Its primary purpose is to protect the copper from oxidation and corrosion, which can occur due to exposure to air and moisture. Additionally, the surface finish enhances the solderability of the board, ensuring a reliable and strong connection between the components and the PCB.
There are several types of PCB Surface Finishes available, each with its own unique properties and benefits. Some of the most common surface finishes include:
- HASL (Hot Air Solder Leveling)
- Lead-Free HASL
- ENIG (Electroless Nickel Immersion Gold)
- OSP (Organic Solderability Preservative)
- Immersion Silver
- Immersion Tin
In this article, we will focus on two of the most widely used surface finishes: Lead-Free HASL and ENIG.
Lead-Free HASL (Hot Air Solder Leveling)
What is Lead-Free HASL?
Lead-Free HASL is a surface finish process that involves dipping the PCB into a molten lead-free solder bath and then using hot air to level the solder on the surface of the board. This process creates a thin, uniform layer of solder on the exposed copper traces and pads, protecting them from oxidation and enhancing solderability.
The lead-free solder used in this process typically consists of a tin-silver-copper (SnAgCu) alloy, which complies with the Restriction of Hazardous Substances (RoHS) directive. This directive aims to reduce the use of hazardous substances, such as lead, in electronic products.
Advantages of Lead-Free HASL
-
Cost-effective: Lead-Free HASL is one of the most economical surface finish options available, making it a popular choice for budget-conscious projects.
-
Excellent solderability: The solder coating provided by Lead-Free HASL ensures excellent solderability, resulting in strong and reliable connections between components and the PCB.
-
Durability: Lead-Free HASL offers good durability and resistance to oxidation and corrosion, protecting the copper traces and pads from environmental factors.
-
Compatibility: This surface finish is compatible with a wide range of soldering processes, including Wave Soldering, selective soldering, and hand soldering.
Disadvantages of Lead-Free HASL
-
Uneven surface: The hot air leveling process can sometimes result in an uneven surface, with variations in solder thickness across the board. This unevenness can cause issues with fine-pitch components and high-density designs.
-
Thermal shock: The high temperature of the molten solder bath can cause thermal shock to the PCB, potentially leading to warpage or damage to the board material.
-
Solder bridging: In some cases, the solder may bridge between closely spaced pads or traces, creating short circuits and affecting the functionality of the PCB.
-
Limited shelf life: The shelf life of Lead-Free HASL is relatively short compared to other surface finishes, as the solder surface can oxidize over time, reducing solderability.
ENIG (Electroless Nickel Immersion Gold)
What is ENIG?
ENIG is a two-layer surface finish that consists of an electroless nickel plating followed by a thin layer of immersion gold. The electroless nickel layer provides a barrier between the copper and the gold, preventing the formation of intermetallic compounds that can cause brittleness and reduced solderability. The immersion gold layer protects the nickel from oxidation and provides a solderable surface.
The ENIG process involves several steps:
-
Cleaning: The PCB is thoroughly cleaned to remove any contaminants or oxides from the copper surface.
-
Microetching: A mild etching solution is used to roughen the copper surface, promoting better adhesion of the nickel layer.
-
Electroless nickel plating: The PCB is immersed in an electroless nickel plating solution, which deposits a thin, uniform layer of nickel on the copper surface.
-
Immersion gold plating: The nickel-plated PCB is then immersed in an immersion gold solution, which deposits a thin layer of gold on top of the nickel.
Advantages of ENIG
-
Flat surface: ENIG provides a flat and uniform surface finish, making it ideal for fine-pitch components and high-density designs.
-
Excellent solderability: The gold layer on top of the nickel ensures excellent solderability, resulting in strong and reliable solder joints.
-
Corrosion resistance: The nickel layer acts as a barrier, protecting the copper from corrosion and oxidation, while the gold layer protects the nickel from oxidation.
-
Long shelf life: ENIG has a longer shelf life compared to Lead-Free HASL, as the gold surface does not oxidize easily, maintaining its solderability over time.
-
Wire Bonding compatibility: The gold surface of ENIG is suitable for wire bonding applications, making it a popular choice for packaging and assembly processes that require this technique.
Disadvantages of ENIG
-
Higher cost: ENIG is more expensive than Lead-Free HASL due to the use of gold and the additional processing steps involved.
-
Black pad syndrome: In some cases, the nickel layer may become excessively thick or poorly adhered to the copper, resulting in a condition known as “black pad syndrome.” This can lead to weak solder joints and reduced reliability.
-
Potential for gold embrittlement: If the gold layer is too thick, it can cause embrittlement of the solder joint, leading to reduced mechanical strength and reliability.
-
Limited rework capability: Reworking ENIG boards can be more challenging compared to Lead-Free HASL, as the gold layer must be completely removed before resoldering.
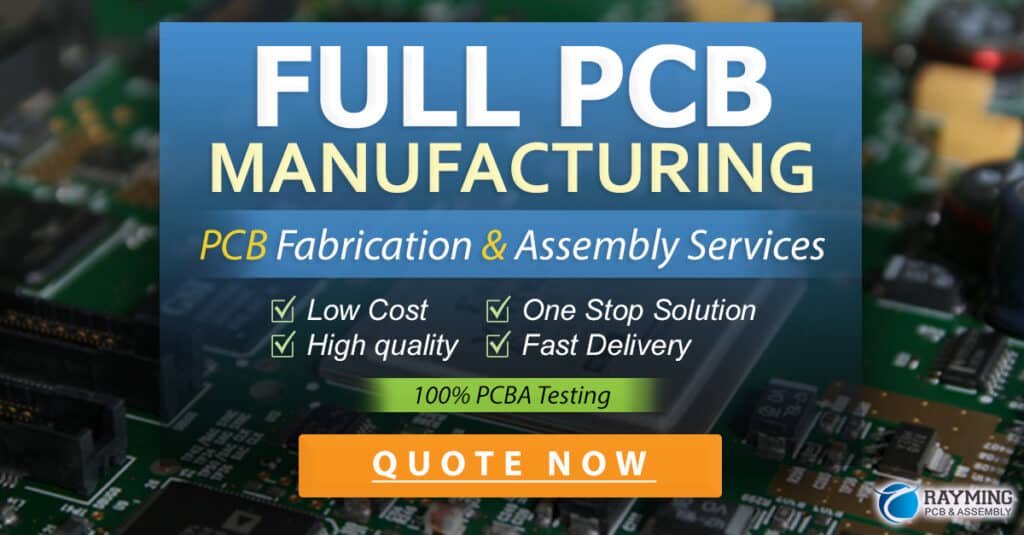
Comparison Table: Lead-Free HASL vs ENIG
Characteristic | Lead-Free HASL | ENIG |
---|---|---|
Cost | Low | High |
Surface Flatness | Uneven | Flat |
Solderability | Excellent | Excellent |
Shelf Life | Short | Long |
Fine-Pitch Compatibility | Limited | Excellent |
Corrosion Resistance | Good | Excellent |
Wire Bonding Compatibility | Limited | Excellent |
Rework Capability | Good | Limited |
Frequently Asked Questions (FAQ)
-
Q: Which surface finish is better for high-density designs, Lead-Free HASL or ENIG?
A: ENIG is generally considered better for high-density designs due to its flat and uniform surface, which allows for better placement and soldering of fine-pitch components. -
Q: Is Lead-Free HASL RoHS compliant?
A: Yes, Lead-Free HASL uses a tin-silver-copper (SnAgCu) alloy that complies with the Restriction of Hazardous Substances (RoHS) directive, making it a lead-free and environmentally friendly option. -
Q: Can ENIG be used for wire bonding applications?
A: Yes, the gold surface of ENIG is suitable for wire bonding applications, making it a popular choice for packaging and assembly processes that require this technique. -
Q: Which surface finish is more cost-effective, Lead-Free HASL or ENIG?
A: Lead-Free HASL is generally more cost-effective than ENIG due to the lower cost of materials and simpler processing steps involved. -
Q: What is the shelf life of Lead-Free HASL compared to ENIG?
A: ENIG has a longer shelf life compared to Lead-Free HASL, as the gold surface does not oxidize easily, maintaining its solderability over time. Lead-Free HASL, on the other hand, has a shorter shelf life due to the potential for oxidation of the solder surface.
Conclusion
Choosing the right PCB surface finish is crucial for ensuring the reliability, solderability, and longevity of your electronic devices. Lead-Free HASL and ENIG are two popular surface finish options, each with its own set of advantages and disadvantages.
Lead-Free HASL is a cost-effective solution that offers excellent solderability and good durability. However, it may result in an uneven surface and has a shorter shelf life compared to ENIG. On the other hand, ENIG provides a flat and uniform surface, excellent corrosion resistance, and a longer shelf life, making it ideal for high-density designs and applications that require wire bonding. However, ENIG comes at a higher cost and may be prone to issues like black pad syndrome and gold embrittlement.
Ultimately, the choice between Lead-Free HASL and ENIG depends on your specific project requirements, budget, and performance expectations. By understanding the characteristics and trade-offs of each surface finish, you can make an informed decision that best suits your needs.
No responses yet