Understanding PCB Substrate Materials
PCB substrate materials, also known as PCB base materials or PCB Laminates, are the insulating layers that form the backbone of a printed circuit board. These materials provide mechanical support, electrical insulation, and a stable surface for the copper traces and components. The choice of substrate material depends on several factors, including the intended application, operating environment, frequency range, and cost constraints.
Key Properties of PCB Substrate Materials
When evaluating PCB substrate materials, several key properties should be considered:
-
Dielectric Constant (Dk): The dielectric constant is a measure of a material’s ability to store electrical energy. It affects the signal propagation speed and impedance of the PCB. Lower Dk values are preferred for high-frequency applications to minimize signal loss and distortion.
-
Dissipation Factor (Df): The dissipation factor, also known as loss tangent, represents the amount of energy dissipated as heat when an alternating electric field is applied to the material. Lower Df values are desirable to reduce signal attenuation and maintain signal integrity.
-
Thermal Conductivity: Thermal conductivity refers to a material’s ability to conduct heat. Higher thermal conductivity helps dissipate heat generated by electronic components, preventing thermal stress and ensuring reliable operation.
-
Coefficient of Thermal Expansion (CTE): The CTE indicates how much a material expands or contracts with changes in temperature. A low CTE is important to minimize thermal stress and prevent delamination or cracking of the PCB.
-
Mechanical Strength: The substrate material should have sufficient mechanical strength to withstand the stresses encountered during manufacturing, assembly, and operation. This includes properties such as flexural strength, tensile strength, and impact resistance.
-
Moisture Resistance: The ability of a substrate material to resist moisture absorption is crucial for maintaining the PCB’s electrical and mechanical integrity, especially in humid environments.
-
Flame Retardancy: Flame retardancy is an essential safety consideration, particularly for PCBs used in consumer electronics and industrial applications. The substrate material should meet the relevant flammability standards, such as UL 94V-0.
Common Types of PCB Substrate Materials
There are several types of PCB substrate materials available, each with its own set of properties and advantages. Let’s explore some of the most commonly used materials:
FR-4 (Flame Retardant 4)
FR-4 is the most widely used PCB substrate material, representing over 90% of the market. It is a composite material made of woven fiberglass fabric impregnated with an epoxy resin. FR-4 offers a good balance of electrical, mechanical, and thermal properties at a relatively low cost.
Property | Value |
---|---|
Dielectric Constant (Dk) | 4.2-4.6 @ 1 MHz |
Dissipation Factor (Df) | 0.02 @ 1 MHz |
Thermal Conductivity | 0.3-0.4 W/mK |
CTE (X-Y) | 12-16 ppm/°C |
CTE (Z) | 50-70 ppm/°C |
Tg (Glass Transition Temperature) | 130-140°C |
FR-4 is suitable for a wide range of applications, including consumer electronics, industrial controls, and telecommunications equipment. However, its relatively high Dk and Df values limit its use in high-frequency applications above a few gigahertz.
High-Tg FR-4
High-Tg FR-4 is a variant of standard FR-4 that offers improved thermal stability and higher glass transition temperature (Tg). The higher Tg allows the PCB to withstand higher temperatures during assembly and operation, reducing the risk of delamination and warping.
Property | Value |
---|---|
Dielectric Constant (Dk) | 4.2-4.6 @ 1 MHz |
Dissipation Factor (Df) | 0.02 @ 1 MHz |
Thermal Conductivity | 0.3-0.4 W/mK |
CTE (X-Y) | 12-16 ppm/°C |
CTE (Z) | 50-70 ppm/°C |
Tg (Glass Transition Temperature) | 170-180°C |
High-Tg FR-4 is commonly used in applications that require higher thermal stability, such as automotive electronics, aerospace systems, and high-power LED lighting.
Rogers PCB Materials
Rogers Corporation offers a range of high-performance PCB substrate materials designed for demanding RF/microwave and high-speed digital applications. These materials provide excellent electrical properties, low loss, and controlled dielectric constant.
Rogers 4003C
Rogers 4003C is a hydrocarbon ceramic laminate that offers low Dk and Df values, making it suitable for high-frequency applications up to 10 GHz.
Property | Value |
---|---|
Dielectric Constant (Dk) | 3.38 @ 10 GHz |
Dissipation Factor (Df) | 0.0027 @ 10 GHz |
Thermal Conductivity | 0.64 W/mK |
CTE (X-Y) | 11 ppm/°C |
CTE (Z) | 46 ppm/°C |
Tg (Glass Transition Temperature) | >280°C |
Rogers 4003C is commonly used in wireless communication systems, radar equipment, and satellite communications.
Rogers RO4350B
Rogers RO4350B is a glass-reinforced hydrocarbon ceramic laminate that provides a low Dk and Df, along with excellent thermal stability and mechanical properties.
Property | Value |
---|---|
Dielectric Constant (Dk) | 3.48 @ 10 GHz |
Dissipation Factor (Df) | 0.0037 @ 10 GHz |
Thermal Conductivity | 0.62 W/mK |
CTE (X-Y) | 11 ppm/°C |
CTE (Z) | 30 ppm/°C |
Tg (Glass Transition Temperature) | >280°C |
RO4350B is widely used in high-frequency applications, such as 5G networks, automotive radar systems, and aerospace communications.
Polyimide
Polyimide is a high-performance polymer that offers excellent thermal stability, mechanical strength, and chemical resistance. It has a higher Tg compared to FR-4 and can withstand temperatures up to 260°C.
Property | Value |
---|---|
Dielectric Constant (Dk) | 3.5 @ 1 MHz |
Dissipation Factor (Df) | 0.002 @ 1 MHz |
Thermal Conductivity | 0.2 W/mK |
CTE (X-Y) | 12-16 ppm/°C |
CTE (Z) | 50-60 ppm/°C |
Tg (Glass Transition Temperature) | 260°C |
Polyimide is commonly used in flexible and rigid-flex PCBs, high-temperature applications, and aerospace and military electronics.
PTFE (Polytetrafluoroethylene)
PTFE, also known as Teflon, is a fluoropolymer that offers exceptional electrical properties, including low Dk and Df values, making it suitable for high-frequency applications up to 100 GHz.
Property | Value |
---|---|
Dielectric Constant (Dk) | 2.1 @ 10 GHz |
Dissipation Factor (Df) | 0.0002 @ 10 GHz |
Thermal Conductivity | 0.2 W/mK |
CTE (X-Y) | 100-120 ppm/°C |
CTE (Z) | 200-250 ppm/°C |
Tg (Glass Transition Temperature) | 327°C |
PTFE is commonly used in RF/microwave circuits, radar systems, and high-speed digital applications. However, its high CTE and relatively low mechanical strength can pose challenges during manufacturing and assembly.
Selecting the Right PCB Substrate Material
Choosing the appropriate PCB substrate material depends on several factors specific to your application. Consider the following aspects when making your decision:
-
Frequency Range: If your PCB operates at high frequencies (above a few gigahertz), opt for materials with low Dk and Df values, such as Rogers or PTFE laminates, to minimize signal loss and distortion.
-
Thermal Requirements: Consider the operating temperature range and the heat generated by the components on your PCB. For high-temperature applications, choose materials with higher Tg, such as High-Tg FR-4 or polyimide.
-
Mechanical Demands: Evaluate the mechanical stresses your PCB will encounter during manufacturing, assembly, and operation. Select materials with sufficient strength and dimensional stability to withstand these stresses.
-
Cost Constraints: PCB substrate materials vary in cost, with high-performance materials generally being more expensive. Balance your performance requirements with your budget constraints to find the most cost-effective solution.
-
Manufacturing Compatibility: Ensure that the chosen substrate material is compatible with your PCB manufacturing process, including etching, drilling, and lamination. Some materials may require specialized equipment or processing techniques.
-
Regulatory Compliance: Consider any regulatory requirements, such as UL flammability ratings or RoHS compliance, that your PCB must meet. Choose substrate materials that comply with the relevant standards.
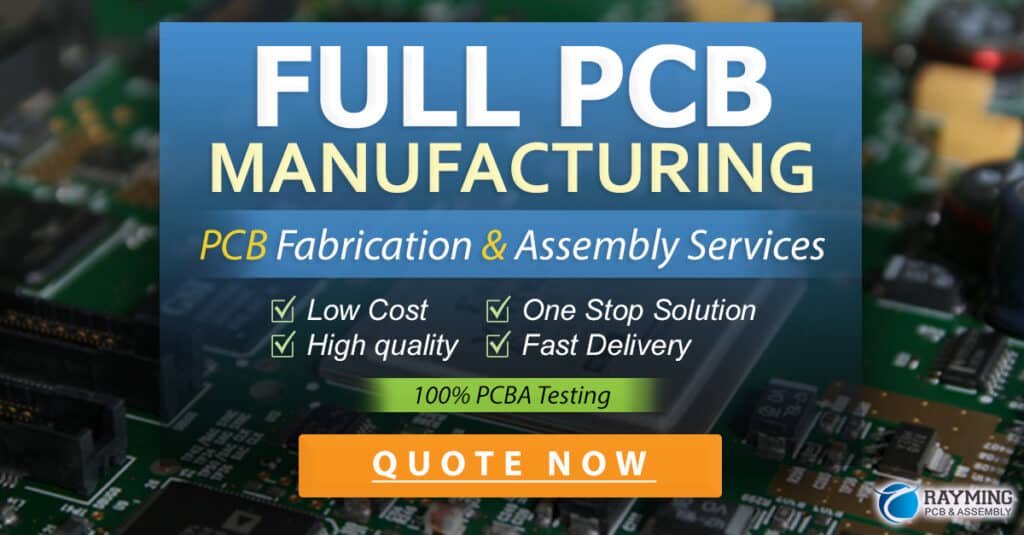
FAQ
1. What is the most commonly used PCB substrate material?
FR-4 (Flame Retardant 4) is the most widely used PCB substrate material, accounting for over 90% of the market. It offers a good balance of electrical, mechanical, and thermal properties at a relatively low cost.
2. What are the key properties to consider when selecting a PCB substrate material?
The key properties to consider include dielectric constant (Dk), dissipation factor (Df), thermal conductivity, coefficient of thermal expansion (CTE), mechanical strength, moisture resistance, and flame retardancy.
3. Which PCB substrate materials are suitable for high-frequency applications?
For high-frequency applications, materials with low Dk and Df values are preferred, such as Rogers laminates (e.g., Rogers 4003C, RO4350B) and PTFE (Polytetrafluoroethylene). These materials minimize signal loss and distortion at high frequencies.
4. What is the difference between standard FR-4 and High-Tg FR-4?
High-Tg FR-4 has a higher glass transition temperature (Tg) compared to standard FR-4. This allows High-Tg FR-4 to withstand higher temperatures during assembly and operation, reducing the risk of delamination and warping.
5. How does the cost of PCB substrate materials vary?
The cost of PCB substrate materials varies depending on their performance characteristics and availability. High-performance materials like Rogers laminates and polyimide are generally more expensive than standard FR-4. It is important to balance performance requirements with cost constraints when selecting a substrate material.
Conclusion
Selecting the right PCB substrate material is crucial for ensuring the optimal performance, reliability, and cost-effectiveness of your printed circuit board. By understanding the key properties and characteristics of various substrate materials, such as FR-4, High-Tg FR-4, Rogers laminates, polyimide, and PTFE, you can make an informed decision based on your specific application requirements.
Consider factors such as the frequency range, thermal demands, mechanical stresses, cost constraints, manufacturing compatibility, and regulatory compliance when choosing the most suitable PCB substrate material. By carefully evaluating these aspects and consulting with experienced PCB manufacturers, you can ensure that your PCB meets its intended performance goals while maintaining a cost-effective solution.
No responses yet