What is a PCB Stiffener?
A PCB stiffener is a mechanical support component that is attached to a flexible or rigid-flex printed circuit board (PCB) to provide additional strength, stability, and protection. It helps to prevent the PCB from bending, twisting, or vibrating excessively during handling, assembly, and operation. PCB stiffeners are typically made from rigid materials such as aluminum, stainless steel, or fiberglass-reinforced epoxy laminate (FR-4).
Types of PCB Stiffeners
There are two main types of PCB stiffeners:
-
Flat Stiffeners: These are simple, flat pieces of rigid material that are attached to the surface of the PCB using adhesive or mechanical fasteners. Flat stiffeners are suitable for applications where the PCB needs to be kept flat and stable, but does not require significant protection from mechanical stress or environmental factors.
-
Formed Stiffeners: These are shaped or contoured pieces of rigid material that are designed to conform to the specific shape and layout of the PCB. Formed stiffeners can provide more comprehensive support and protection than flat stiffeners, especially for PCBs with complex geometries or high-stress areas. They can also be used to create enclosures, shields, or heat sinks for the PCB.
Why Use a PCB Stiffener?
There are several reasons why a PCB stiffener may be necessary or beneficial for a flexible or rigid-flex PCB design:
-
Mechanical Strength: Flexible PCBs are inherently less rigid than traditional rigid PCBs, which makes them more susceptible to bending, twisting, and vibration. A PCB stiffener can provide the necessary mechanical support to keep the PCB flat and stable, especially in applications where the PCB is subject to physical handling or movement.
-
Dimensional Stability: Flexible PCBs can expand, contract, or warp due to changes in temperature, humidity, or mechanical stress. This can cause issues with component placement, solder joint reliability, and overall circuit performance. A PCB stiffener can help to maintain the dimensional stability of the PCB, ensuring that critical components remain properly aligned and connected.
-
Connector Support: Flexible PCBs often require connectors or other mechanical interfaces to connect to other parts of the system. These connectors can put significant stress on the PCB, especially if they are subject to repeated insertion and removal. A PCB stiffener can provide additional support around the connector area, preventing the PCB from bending or breaking under the stress.
-
Component Protection: Some components on a flexible PCB may be sensitive to mechanical stress or environmental factors such as moisture, dust, or electromagnetic interference (EMI). A PCB stiffener can be used to create a protective enclosure or shield around these components, helping to ensure their long-term reliability and performance.
-
Thermal Management: In some cases, a PCB stiffener can also serve as a heat sink or thermal conductor, helping to dissipate heat away from critical components on the PCB. This can be especially important for high-power or high-frequency applications where thermal management is a key concern.
How to Design a PCB Stiffener
Designing a PCB stiffener requires careful consideration of the specific requirements and constraints of the PCB and its application. Here are some key steps and considerations in the PCB stiffener design process:
-
Identify the Critical Areas: The first step is to identify the areas of the PCB that require additional support or protection. This may include areas around connectors, high-stress components, or regions of the PCB that are subject to significant bending or twisting.
-
Choose the Stiffener Material: The choice of stiffener material will depend on the specific requirements of the application, such as mechanical strength, thermal conductivity, electrical insulation, and cost. Common materials include aluminum, stainless steel, and FR-4.
-
Determine the Stiffener Thickness: The thickness of the stiffener will depend on the required level of support and the available space within the PCB assembly. Thicker stiffeners provide more rigidity but may increase the overall thickness of the PCB assembly.
-
Design the Stiffener Shape: The shape of the stiffener should be designed to conform to the specific layout and geometry of the PCB. This may involve creating cutouts, holes, or other features to accommodate components, connectors, or other mechanical interfaces.
-
Consider Attachment Methods: The stiffener must be securely attached to the PCB to provide effective support. Common attachment methods include adhesive bonding, mechanical fasteners (screws, rivets, etc.), or snap-fit features.
-
Analyze the Mechanical and Thermal Performance: It is important to analyze the mechanical and thermal performance of the PCB assembly with the stiffener in place, using tools such as finite element analysis (FEA) or thermal simulation. This can help to identify any potential issues or areas for optimization.
-
Prototype and Test: Before finalizing the design, it is recommended to create a prototype of the PCB assembly with the stiffener and perform physical testing to validate the mechanical and thermal performance. This can help to identify any issues or areas for improvement before moving to production.
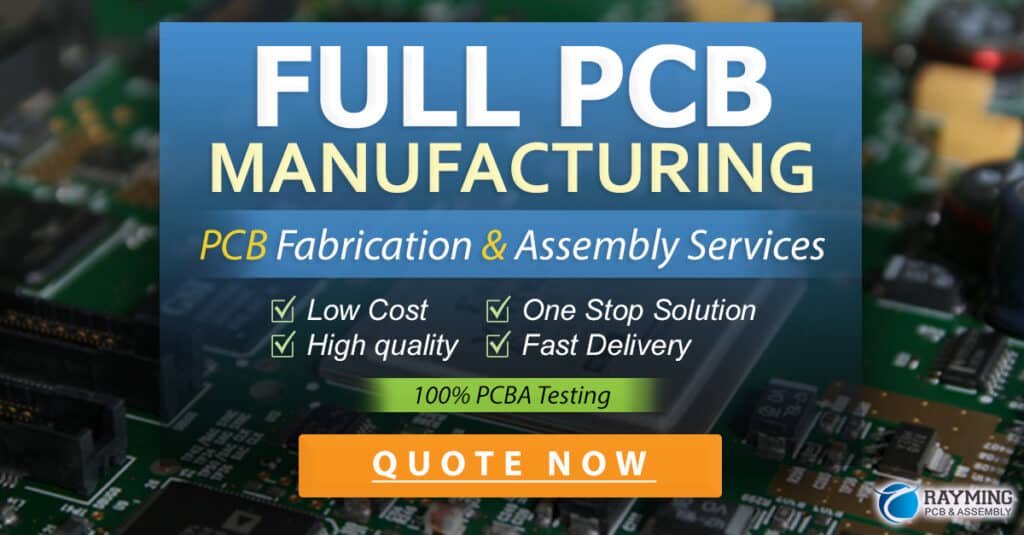
PCB Stiffener Material Comparison
Here is a table comparing the properties of common PCB stiffener materials:
Material | Mechanical Strength | Thermal Conductivity | Electrical Insulation | Cost |
---|---|---|---|---|
Aluminum | High | High | Low | Low |
Stainless Steel | Very High | Low | Low | High |
FR-4 | Moderate | Low | High | Low |
Polyimide | Low | Low | High | High |
Acrylic | Moderate | Low | High | Low |
PCB Stiffener Application Examples
Here are some examples of applications where PCB stiffeners are commonly used:
-
Automotive Electronics: Flexible PCBs are increasingly used in automotive applications such as instrument clusters, infotainment systems, and camera modules. PCB stiffeners are used to provide mechanical support and protection for these PCBs, which are subject to vibration, temperature extremes, and other harsh environmental conditions.
-
Wearable Devices: Flexible PCBs are a key enabler for wearable devices such as smartwatches, fitness trackers, and medical monitors. PCB stiffeners are used to provide structure and support for these PCBs, which must conform to the shape of the human body while still providing reliable electronic functionality.
-
Aerospace and Defense: Flexible PCBs are used in a variety of aerospace and defense applications, such as avionics, satellites, and military communications equipment. PCB stiffeners are used to provide mechanical support and protection for these PCBs, which must operate reliably in harsh environments and under extreme conditions.
-
Industrial Automation: Flexible PCBs are used in industrial automation applications such as robotics, machine vision, and process control. PCB stiffeners are used to provide mechanical support and protection for these PCBs, which are subject to vibration, shock, and other mechanical stresses in the industrial environment.
-
Medical Devices: Flexible PCBs are used in a variety of medical devices, such as implantable sensors, surgical instruments, and diagnostic equipment. PCB stiffeners are used to provide mechanical support and protection for these PCBs, which must be biocompatible, reliable, and able to withstand sterilization processes.
PCB Stiffener Frequently Asked Questions (FAQ)
1. What is the difference between a flat stiffener and a formed stiffener?
A flat stiffener is a simple, flat piece of rigid material that is attached to the surface of the PCB, while a formed stiffener is a shaped or contoured piece of material that is designed to conform to the specific shape and layout of the PCB. Formed stiffeners provide more comprehensive support and protection than flat stiffeners.
2. Can a PCB stiffener be used as a heat sink?
Yes, in some cases, a PCB stiffener can be designed to serve as a heat sink or thermal conductor, helping to dissipate heat away from critical components on the PCB. This is especially important for high-power or high-frequency applications where thermal management is a key concern.
3. How is a PCB stiffener attached to the PCB?
PCB stiffeners can be attached to the PCB using various methods, including adhesive bonding, mechanical fasteners (screws, rivets, etc.), or snap-fit features. The choice of attachment method depends on the specific requirements of the application, such as mechanical strength, ease of assembly, and cost.
4. What materials are commonly used for PCB stiffeners?
Common materials for PCB stiffeners include aluminum, stainless steel, FR-4, polyimide, and acrylic. The choice of material depends on the specific requirements of the application, such as mechanical strength, thermal conductivity, electrical insulation, and cost.
5. How can I determine the appropriate thickness for a PCB stiffener?
The appropriate thickness for a PCB stiffener depends on the required level of mechanical support and the available space within the PCB assembly. Thicker stiffeners provide more rigidity but may increase the overall thickness of the assembly. Finite element analysis (FEA) can be used to analyze the mechanical performance of the PCB assembly with different stiffener thicknesses and help determine the optimal thickness for the application.
Conclusion
PCB stiffeners are a critical component in the design of flexible and rigid-flex PCBs, providing the necessary mechanical support, stability, and protection to ensure reliable electronic performance. By carefully considering the specific requirements and constraints of the application, designers can select the appropriate stiffener material, shape, and attachment method to create a robust and reliable PCB assembly. With the increasing use of flexible PCBs in a variety of industries, from automotive and wearables to aerospace and medical devices, the importance of effective PCB stiffener design will only continue to grow in the future.
No responses yet