What is PCB Stackup?
PCB stackup refers to the arrangement of layers in a multi-layer PCB. It is the vertical structure of a PCB, consisting of alternating layers of conductive and insulating materials. The conductive layers are typically made of copper, while the insulating layers are made of materials such as FR-4, Rogers, or Polyimide.
The Importance of PCB Stackup
PCB stackup is crucial in determining the performance, reliability, and manufacturability of a PCB. A well-designed stackup ensures that the PCB meets the electrical, mechanical, and thermal requirements of the device. It also helps in reducing electromagnetic interference (EMI), crosstalk, and signal integrity issues.
Factors to Consider in PCB Stackup Design
When designing a PCB stackup, several factors need to be considered:
-
Number of Layers: The number of layers in a PCB stackup depends on the complexity of the circuit and the available space. More layers allow for higher component density and better signal integrity but also increase the cost and manufacturing complexity.
-
Layer Thickness: The thickness of each layer affects the electrical and mechanical properties of the PCB. Thinner layers allow for smaller vias and tighter tolerances but also increase the risk of manufacturing defects.
-
Material Selection: The choice of materials for the conductive and insulating layers depends on the electrical, mechanical, and thermal requirements of the device. FR-4 is the most common insulating material, while copper is the standard conductive material.
-
Via Structure: Vias are used to connect different layers in a PCB stackup. The size, shape, and placement of vias affect the signal integrity and manufacturability of the PCB.
-
Impedance Control: Controlling the impedance of the signal traces is essential for maintaining signal integrity and reducing EMI. This is achieved by adjusting the width and spacing of the traces and the thickness of the dielectric layers.
Types of PCB Stackup
There are three main types of PCB stackup:
-
Standard Stackup: This is the most common type of PCB stackup, consisting of alternating layers of copper and FR-4. It is suitable for most applications and is relatively inexpensive to manufacture.
-
High-Speed Stackup: This type of stackup is designed for high-speed applications, such as high-frequency RF circuits or high-speed digital circuits. It uses low-loss materials such as Rogers or Polyimide and has tightly controlled impedance and dielectric thickness.
-
HDI Stackup: High Density Interconnect (HDI) stackup is used for high-density circuits with a large number of components. It uses micro vias and thin dielectric layers to achieve high component density and signal integrity.
Standard PCB Stackup
A standard PCB stackup typically consists of the following layers:
Layer | Material | Thickness (mil) |
---|---|---|
Top Copper | Copper | 1.4 |
Prepreg | FR-4 | 4.0 |
Inner Copper 1 | Copper | 1.0 |
Core | FR-4 | 47.0 |
Inner Copper 2 | Copper | 1.0 |
Prepreg | FR-4 | 4.0 |
Bottom Copper | Copper | 1.4 |
The standard stackup provides a good balance between cost and performance and is suitable for most applications.
High-Speed PCB Stackup
A high-speed PCB stackup uses low-loss materials and tightly controlled impedance to achieve high signal integrity. A typical high-speed stackup consists of the following layers:
Layer | Material | Thickness (mil) |
---|---|---|
Top Copper | Copper | 1.2 |
Prepreg | Rogers 4350B | 3.6 |
Inner Copper 1 | Copper | 1.0 |
Core | Rogers 4350B | 8.0 |
Inner Copper 2 | Copper | 1.0 |
Prepreg | Rogers 4350B | 3.6 |
Bottom Copper | Copper | 1.2 |
The high-speed stackup uses Rogers material, which has a lower dielectric constant and dissipation factor than FR-4. This reduces signal loss and improves signal integrity.
HDI PCB Stackup
An HDI PCB stackup uses micro vias and thin dielectric layers to achieve high component density and signal integrity. A typical HDI stackup consists of the following layers:
Layer | Material | Thickness (mil) |
---|---|---|
Top Copper | Copper | 0.5 |
Prepreg | Polyimide | 1.0 |
Inner Copper 1 | Copper | 0.5 |
Core | FR-4 | 4.0 |
Inner Copper 2 | Copper | 0.5 |
Prepreg | Polyimide | 1.0 |
Bottom Copper | Copper | 0.5 |
The HDI stackup uses thin copper layers and Polyimide dielectric to achieve high density and signal integrity. The micro vias allow for shorter signal paths and reduced parasitic capacitance.
PCB Stackup Design Process
The PCB stackup design process involves the following steps:
-
Schematic Design: The first step is to create a schematic of the circuit, showing all the components and their connections.
-
Component Placement: The next step is to place the components on the PCB, taking into account the available space and the signal flow.
-
Layer Stack Definition: The layer stack is defined based on the number of layers, thickness, and material properties required for the design.
-
Signal Routing: The signal traces are routed on the appropriate layers, taking into account the impedance and crosstalk requirements.
-
Power and Ground Planes: The power and ground planes are added to the stackup to provide a low-impedance path for the power and ground signals.
-
Via Definition: The vias are defined based on the signal requirements and the manufacturability constraints.
-
Design Rule Check: The design is checked against the manufacturing and assembly rules to ensure that it is feasible and reliable.
-
Prototyping and Testing: The PCB is prototyped and tested to verify its functionality and performance.
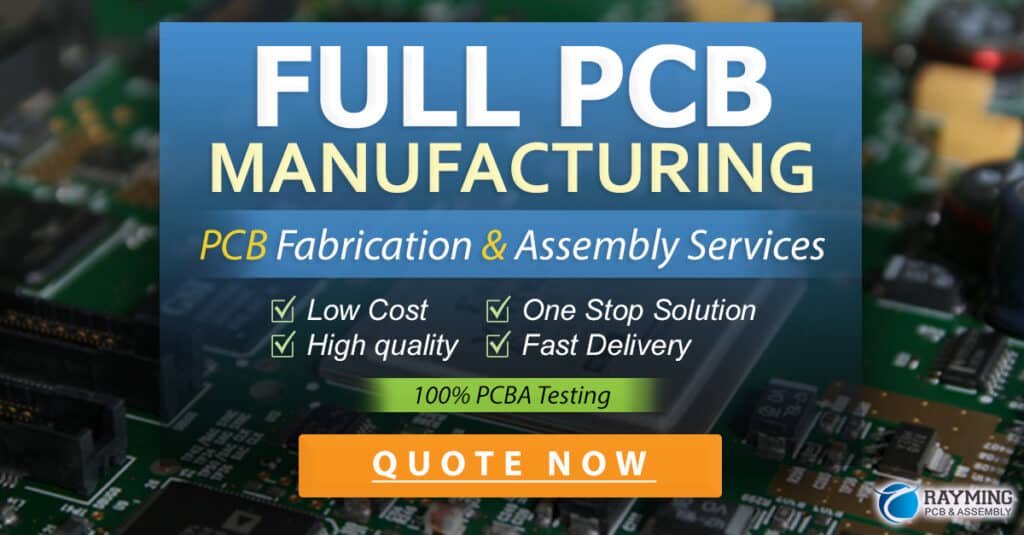
Best Practices for PCB Stackup Design
To ensure a successful PCB stackup design, follow these best practices:
-
Keep the layer count to a minimum: Use the minimum number of layers required for the design to reduce cost and complexity.
-
Use a symmetrical stackup: A symmetrical stackup helps in reducing warpage and improving manufacturability.
-
Minimize the use of vias: Vias add complexity and cost to the design. Use them only when necessary and keep their size and count to a minimum.
-
Use wide traces for power and ground: Wide traces help in reducing the impedance and improving the current carrying capacity of the power and ground planes.
-
Keep the signal traces short: Shorter signal traces reduce the parasitic capacitance and inductance, improving signal integrity.
-
Use ground planes to shield sensitive signals: Ground planes help in reducing crosstalk and EMI by providing a low-impedance return path for the signals.
-
Follow the manufacturer’s design rules: Each PCB manufacturer has its own set of design rules for manufacturability and reliability. Follow these rules to ensure a successful design.
FAQ
Q: What is the difference between a standard stackup and a high-speed stackup?
A: A standard stackup uses FR-4 material and is suitable for most applications, while a high-speed stackup uses low-loss materials such as Rogers or Polyimide and has tightly controlled impedance for high-speed applications.
Q: What is the purpose of micro vias in an HDI stackup?
A: Micro vias allow for shorter signal paths and reduced parasitic capacitance, enabling higher component density and signal integrity in an HDI stackup.
Q: How does the number of layers affect the cost and complexity of a PCB?
A: More layers allow for higher component density and better signal integrity but also increase the cost and manufacturing complexity of the PCB.
Q: What is the role of power and ground planes in a PCB stackup?
A: Power and ground planes provide a low-impedance path for the power and ground signals, helping to reduce noise and improve signal integrity.
Q: Why is it important to follow the manufacturer’s design rules when designing a PCB stackup?
A: Each PCB manufacturer has its own set of design rules for manufacturability and reliability. Following these rules ensures that the PCB can be manufactured successfully and will perform reliably in the intended application.
Conclusion
PCB stackup is a critical aspect of PCB design that affects the performance, reliability, and manufacturability of the circuit. A well-designed stackup takes into account the electrical, mechanical, and thermal requirements of the device and helps in reducing signal integrity issues such as EMI and crosstalk.
There are three main types of PCB stackup: standard, high-speed, and HDI. Each type has its own set of requirements and trade-offs in terms of cost, complexity, and performance.
To ensure a successful PCB stackup design, it is important to follow best practices such as keeping the layer count to a minimum, using a symmetrical stackup, minimizing the use of vias, and following the manufacturer’s design rules.
By understanding the principles of PCB stackup and applying them effectively, designers can create reliable and high-performance PCBs for even the most complex devices.
No responses yet