What are PCB Shields?
PCB shields, also known as electromagnetic interference (EMI) shields or radio frequency interference (RFI) shields, are metal enclosures or barriers that are designed to protect electronic components on a PCB from external electromagnetic interference. They also prevent the electronic components from emitting electromagnetic radiation that could interfere with other devices.
PCB shields are typically made from conductive materials such as aluminum, steel, or copper, and are designed to fit securely over the components on a PCB. They can be custom-made to fit specific PCB layouts or purchased as off-the-shelf solutions for common PCB sizes and configurations.
Types of PCB Shields
There are several types of PCB shields available, each with its own unique characteristics and applications. Let’s take a closer look at some of the most common types of PCB shields:
1. One-Piece Shields
One-piece shields are the simplest and most cost-effective type of PCB shield. They are made from a single piece of metal and are designed to fit over the entire PCB or a specific section of the board. One-piece shields are typically used in applications where the PCB does not require frequent access or maintenance.
2. Two-Piece Shields
Two-piece shields consist of a frame and a removable cover, allowing for easy access to the PCB components when necessary. The frame is usually soldered onto the PCB, while the cover can be attached using screws, snap-fits, or other fastening methods. Two-piece shields are ideal for applications that require occasional maintenance or debugging.
3. Custom Shields
Custom shields are designed and manufactured to fit specific PCB layouts and configurations. They offer the highest level of protection and can be tailored to accommodate unique component placements, heights, and shapes. Custom shields are often used in high-end electronic devices or applications with stringent EMI/RFI requirements.
4. Ventilated Shields
Ventilated shields feature perforations or mesh patterns that allow for better airflow and heat dissipation. These shields are particularly useful in applications where the PCB components generate significant amounts of heat, as the ventilation helps prevent overheating and ensures optimal performance.
Applications of PCB Shields
PCB shields find applications in a wide range of industries and electronic devices. Some common applications include:
- Consumer electronics (smartphones, tablets, laptops)
- Automotive electronics (infotainment systems, engine control units)
- Medical devices (patient monitors, imaging equipment)
- Industrial equipment (process controllers, sensors)
- Aerospace and defense systems (avionics, communication devices)
- Internet of Things (IoT) devices (smart home appliances, wearables)
In each of these applications, PCB shields help ensure the proper functioning of electronic components by protecting them from electromagnetic interference and preventing the emission of unwanted radiation.
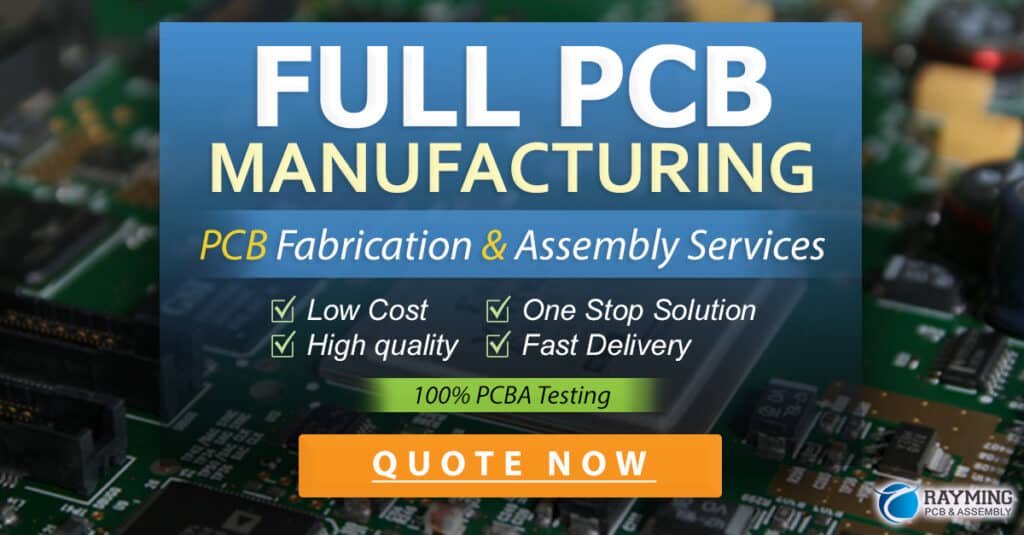
Design Considerations for PCB Shields
When designing or selecting PCB shields, there are several key factors to consider to ensure optimal performance and protection. These include:
1. Material Selection
The choice of material for a PCB shield depends on the specific application and the level of EMI/RFI protection required. Aluminum is a popular choice due to its low cost, lightweight, and good shielding effectiveness. Steel offers higher strength and better magnetic shielding properties, while copper provides excellent conductivity and shielding effectiveness but is more expensive.
2. Shielding Effectiveness
Shielding effectiveness refers to the ability of a shield to attenuate electromagnetic radiation. It is measured in decibels (dB) and is dependent on factors such as the material, thickness, and frequency of the radiation. When selecting a PCB shield, it is essential to choose one with the appropriate shielding effectiveness for your application.
3. Grounding
Proper grounding is crucial for the effective functioning of PCB shields. The shield must be electrically connected to the PCB’s ground plane to provide a low-impedance path for electromagnetic interference to be diverted away from the sensitive components. Grounding can be achieved through various methods, such as conductive gaskets, spring fingers, or direct soldering.
4. Mechanical Design
The mechanical design of a PCB shield should take into account factors such as component clearance, ease of assembly, and thermal management. The shield should be designed to fit securely over the components without interfering with their functioning or causing physical damage. Additionally, the shield should allow for adequate airflow and heat dissipation to prevent overheating.
5. Cost and Manufacturing
Cost is an essential consideration when designing or selecting PCB shields. The choice of material, manufacturing process, and complexity of the design all contribute to the overall cost of the shield. It is important to strike a balance between cost and performance, ensuring that the shield provides the necessary protection while remaining within budget constraints.
PCB Shield Manufacturing Processes
PCB shields can be manufactured using various processes, depending on the material, design complexity, and production volume. Some common manufacturing processes include:
1. Stamping
Stamping is a cost-effective manufacturing process for high-volume production of simple PCB shield designs. In this process, a sheet of metal is placed between two dies, and a press is used to cut and shape the metal into the desired shield geometry.
2. Forming
Forming involves bending and shaping a sheet of metal into the desired shield geometry using specialized tools and machines. This process is suitable for more complex shield designs and lower production volumes.
3. Casting
Casting is a manufacturing process in which molten metal is poured into a mold cavity and allowed to solidify. This process is suitable for complex shield geometries and materials that are difficult to stamp or form, such as aluminum alloys with high magnesium content.
4. 3D Printing
3D printing is an additive manufacturing process that builds up the shield geometry layer by layer using a digital model. This process is ideal for rapid prototyping and low-volume production of custom PCB shields.
Testing and Certification of PCB Shields
To ensure that PCB shields meet the necessary EMI/RFI protection requirements, they must undergo rigorous testing and certification processes. Some common testing and certification standards include:
- FCC Part 15 (USA)
- CE Marking (Europe)
- IEC 61000-4-2 (ESD)
- IEC 61000-4-3 (Radiated Immunity)
- IEC 61000-4-6 (Conducted Immunity)
- MIL-STD-461 (Military Standard)
These standards specify the test methods, limits, and criteria for evaluating the electromagnetic compatibility (EMC) of electronic devices and their components, including PCB shields.
Best Practices for Implementing PCB Shields
To ensure the optimal performance and effectiveness of PCB shields, consider the following best practices:
- Conduct thorough EMI/RFI testing to identify potential interference issues early in the design process.
- Select the appropriate shielding material and manufacturing process based on the specific application requirements and budget constraints.
- Ensure proper grounding and bonding of the shield to the PCB ground plane.
- Minimize gaps and seams in the shield design to prevent leakage of electromagnetic radiation.
- Consider the thermal management implications of the shield design, ensuring adequate airflow and heat dissipation.
- Follow industry standards and guidelines for shield design, testing, and certification.
By adhering to these best practices, you can ensure that your PCB shields provide the necessary protection against electromagnetic interference and contribute to the overall reliability and performance of your electronic devices.
Frequently Asked Questions (FAQ)
1. What is the difference between EMI and RFI?
EMI (electromagnetic interference) and RFI (radio frequency interference) are often used interchangeably, but they refer to slightly different phenomena. EMI encompasses a broader range of electromagnetic disturbances, including both conducted and radiated interference, across the entire electromagnetic spectrum. RFI specifically refers to electromagnetic interference in the radio frequency range, typically from 3 kHz to 300 GHz.
2. Can PCB shields completely eliminate EMI/RFI?
While PCB shields can significantly reduce the impact of EMI/RFI on electronic components, they cannot completely eliminate it. The effectiveness of a shield depends on factors such as the shielding material, design, and frequency of the interference. In some cases, additional measures such as filters, grounding, and proper PCB layout may be necessary to achieve the desired level of protection.
3. How do I select the right PCB shield for my application?
When selecting a PCB shield, consider factors such as the required shielding effectiveness, the frequency range of the interference, the mechanical design constraints, and the budget. Consult with shield manufacturers or EMC experts to determine the most appropriate shield solution for your specific application.
4. Can I use a PCB shield for heat dissipation?
While the primary function of PCB shields is to provide EMI/RFI protection, they can also contribute to heat dissipation. Ventilated shields, in particular, allow for better airflow and can help dissipate heat generated by electronic components. However, for applications with significant heat generation, additional thermal management solutions such as heatsinks or fans may be necessary.
5. Are there any alternatives to PCB shields for EMI/RFI protection?
In some cases, alternative methods can be used to mitigate EMI/RFI issues, such as:
- Proper PCB layout and grounding
- Filtering and suppression components (e.g., capacitors, ferrites)
- Shielded cables and connectors
- Conductive coatings and paints
However, PCB shields remain one of the most effective and widely used solutions for protecting electronic components from electromagnetic interference.
Conclusion
PCB shields play a crucial role in ensuring the proper functioning and reliability of electronic devices by protecting sensitive components from electromagnetic interference. By understanding the types, applications, design considerations, and best practices associated with PCB shields, engineers and designers can make informed decisions when developing electronic products.
As the complexity and density of electronic devices continue to increase, the importance of effective EMI/RFI shielding solutions will only grow. By staying up-to-date with the latest advancements in PCB shield technology and adhering to industry standards and best practices, manufacturers can deliver high-quality, reliable electronic products that meet the evolving needs of their customers.
Type of PCB Shield | Advantages | Disadvantages |
---|---|---|
One-Piece Shields | Simple, cost-effective, suitable for applications without frequent maintenance | Limited access to PCB components |
Two-Piece Shields | Easy access to PCB components, ideal for applications requiring occasional maintenance | More complex design, higher cost compared to one-piece shields |
Custom Shields | Tailored to specific PCB layouts, highest level of protection | Higher cost, longer lead times |
Ventilated Shields | Improved airflow and heat dissipation | Potential for reduced shielding effectiveness due to perforations |
No responses yet