Introduction to PCB Material Selection
Printed Circuit Boards (PCBs) are the backbone of modern electronics, providing a platform for components to be mounted and interconnected. The choice of PCB material is crucial as it directly impacts the performance, reliability, and cost of the final product. This article delves into the world of PCB material selection, exploring the various options available and the factors to consider when choosing the right material for your PCB project.
Factors Influencing PCB Material Selection
When selecting a PCB material, several key factors come into play:
-
Electrical Properties: The dielectric constant (Dk) and dissipation factor (Df) of the material determine its ability to insulate and minimize signal loss.
-
Thermal Properties: The material’s thermal conductivity and coefficient of thermal expansion (CTE) affect its ability to dissipate heat and maintain structural integrity under temperature fluctuations.
-
Mechanical Properties: The material’s strength, flexibility, and dimensional stability are important considerations, especially for applications subject to physical stress or vibration.
-
Frequency and Signal Integrity: Different materials exhibit varying performance at high frequencies, impacting signal integrity and electromagnetic compatibility (EMC).
-
Environmental Factors: The material’s resistance to moisture, chemicals, and extreme temperatures is crucial for reliable operation in harsh environments.
-
Cost and Availability: The price and availability of the material should align with the project’s budget and timeline.
Common PCB Materials
Several materials are commonly used in PCB Fabrication, each with its own set of properties and advantages:
FR-4
FR-4 is the most widely used PCB material, consisting of a glass-reinforced epoxy laminate. It offers good mechanical strength, dimensional stability, and electrical insulation properties. FR-4 is suitable for a wide range of applications, from low-cost consumer electronics to industrial control systems.
Property | Value |
---|---|
Dielectric Constant (Dk) | 4.2 – 4.5 |
Dissipation Factor (Df) | 0.02 |
Thermal Conductivity | 0.3 W/m·K |
CTE (Z-axis) | 50-70 ppm/°C |
Tg (Glass Transition) | 130 – 140°C |
High Tg FR-4
High Tg FR-4 is a variant of standard FR-4 with improved thermal properties. It features a higher glass transition temperature (Tg), making it suitable for applications requiring better heat resistance and stability, such as automotive and aerospace electronics.
Property | Value |
---|---|
Dielectric Constant (Dk) | 4.2 – 4.5 |
Dissipation Factor (Df) | 0.02 |
Thermal Conductivity | 0.3 W/m·K |
CTE (Z-axis) | 50-70 ppm/°C |
Tg (Glass Transition) | 170 – 180°C |
Polyimide
Polyimide is a high-performance polymer known for its excellent thermal stability, chemical resistance, and mechanical strength. It is often used in applications requiring operation at elevated temperatures or exposure to harsh environments, such as aerospace, military, and oil and gas industries.
Property | Value |
---|---|
Dielectric Constant (Dk) | 3.5 |
Dissipation Factor (Df) | 0.002 |
Thermal Conductivity | 0.2 W/m·K |
CTE (Z-axis) | 30-60 ppm/°C |
Tg (Glass Transition) | >250°C |
PTFE (Teflon)
PTFE, also known as Teflon, is a fluoropolymer with outstanding electrical properties, including a low dielectric constant and dissipation factor. It is an excellent choice for high-frequency applications, such as microwave and RF circuits, due to its low signal loss and stable performance over a wide frequency range.
Property | Value |
---|---|
Dielectric Constant (Dk) | 2.1 |
Dissipation Factor (Df) | 0.0002 |
Thermal Conductivity | 0.25 W/m·K |
CTE (Z-axis) | 100-200 ppm/°C |
Tg (Glass Transition) | 327°C |
Rogers Materials
Rogers Corporation offers a range of high-performance PCB materials tailored for specific applications. Some popular Rogers materials include:
-
RO4000 Series: A hydrocarbon ceramic laminate with low dielectric constant and dissipation factor, suitable for high-frequency and microwave applications.
-
RT/duroid: A PTFE-based laminate with low dielectric constant and excellent thermal stability, ideal for demanding RF and microwave designs.
-
RO3000 Series: A ceramic-filled PTFE composite offering a balance of good electrical properties and ease of fabrication, suitable for a wide range of high-frequency applications.
PCB Material Selection Process
Choosing the right PCB material involves a systematic approach, considering the specific requirements of your application:
-
Define the Application: Clearly identify the intended use, operating environment, and performance expectations of your PCB.
-
Determine Electrical Requirements: Specify the desired dielectric constant, dissipation factor, and other electrical properties based on the frequency range and signal integrity needs.
-
Consider Thermal and Mechanical Demands: Evaluate the thermal management requirements and mechanical stresses the PCB will encounter, and select a material with appropriate thermal conductivity, CTE, and mechanical strength.
-
Assess Environmental Factors: Consider the exposure to moisture, chemicals, and extreme temperatures, and choose a material with suitable resistance properties.
-
Evaluate Cost and Availability: Compare the cost and lead times of different materials, and select one that aligns with your budget and project timeline.
-
Consult with PCB Manufacturers: Engage with experienced PCB manufacturers to discuss your requirements and obtain recommendations based on their expertise and capabilities.
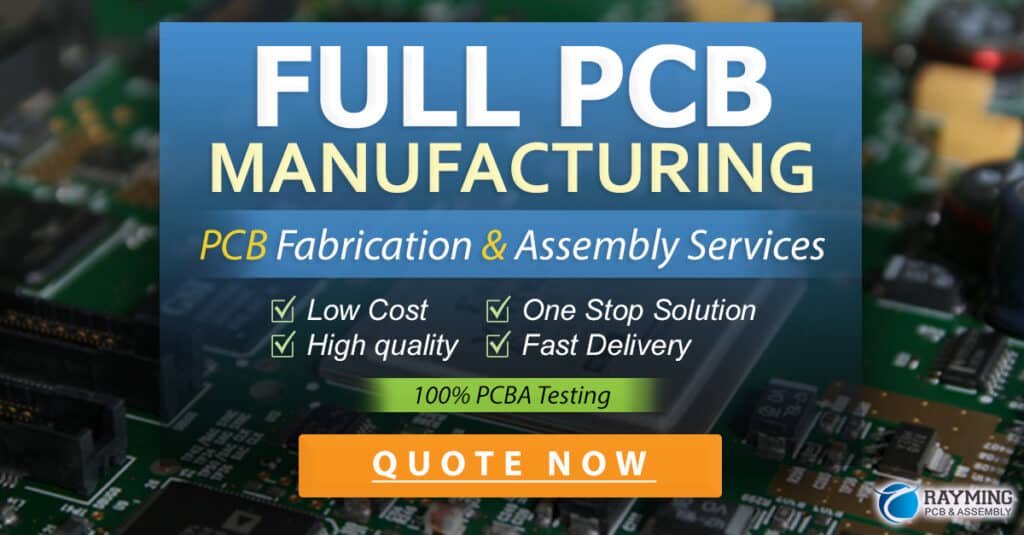
Conclusion
PCB material selection is a critical aspect of PCB Design and manufacturing, directly impacting the performance, reliability, and cost of the final product. By understanding the various material options available and considering the specific requirements of your application, you can make an informed decision and choose the most suitable material for your PCB project. Engaging with experienced PCB manufacturers and leveraging their expertise can further streamline the material selection process and ensure the success of your PCB design.
Frequently Asked Questions (FAQ)
1. What is the most common PCB material?
FR-4 is the most widely used PCB material, offering a good balance of electrical, mechanical, and thermal properties at a reasonable cost. It is suitable for a wide range of applications, from consumer electronics to industrial control systems.
2. What PCB material is best for high-frequency applications?
For high-frequency applications, such as RF and microwave circuits, PTFE (Teflon) and Rogers materials like RO4000 and RT/duroid are excellent choices. These materials have low dielectric constants and dissipation factors, minimizing signal loss and ensuring stable performance over a wide frequency range.
3. How does the glass transition temperature (Tg) affect PCB material selection?
The glass transition temperature (Tg) is the temperature at which the PCB material transitions from a rigid, glassy state to a softer, rubbery state. Materials with higher Tg, such as High Tg FR-4 and polyimide, are better suited for applications requiring operation at elevated temperatures or exposure to harsh environments.
4. What factors should I consider when selecting a PCB material?
When selecting a PCB material, consider the following factors:
– Electrical properties (dielectric constant, dissipation factor)
– Thermal properties (thermal conductivity, CTE)
– Mechanical properties (strength, flexibility, dimensional stability)
– Frequency and signal integrity requirements
– Environmental factors (moisture, chemical, and temperature resistance)
– Cost and availability
5. How can I ensure I choose the right PCB material for my application?
To ensure you choose the right PCB material, follow these steps:
1. Clearly define your application requirements and operating conditions.
2. Evaluate the electrical, thermal, mechanical, and environmental demands of your PCB.
3. Compare the properties of different PCB materials and select one that best meets your requirements.
4. Consult with experienced PCB manufacturers to discuss your needs and obtain recommendations based on their expertise.
5. Consider the cost and availability of the material to align with your budget and project timeline.
By carefully considering these factors and engaging with knowledgeable PCB manufacturers, you can make an informed decision and select the most suitable PCB material for your specific application.
No responses yet