What Are PCB Prototypes?
Before diving into the 12 insane facts, let’s first define what PCB prototypes are. PCB stands for Printed Circuit Board, which is a flat board made of insulating material with conductive tracks printed on its surface. These boards are used to mechanically support and electrically connect electronic components using conductive pathways, tracks, or signal traces etched from copper sheets laminated onto a non-conductive substrate.
PCB prototypes are the initial versions of these boards, created to test the design and functionality before mass production. They are typically made in small quantities and may undergo several iterations before the final design is approved.
The 12 Insane (But True) Things You Need To Know About PCB Prototypes
1. PCB Prototypes Can Be Made In Just 24 Hours
One of the most surprising facts about PCB prototypes is that they can be manufactured in as little as 24 hours. Thanks to advanced manufacturing techniques and rapid prototyping services, designers can have their prototype boards in hand within a day of submitting their design files. This quick turnaround time allows for faster testing and iteration, ultimately leading to a better final product.
2. PCB Prototypes Can Be Made In Unusual Shapes
While most PCBs are rectangular or square, prototypes can be made in virtually any shape imaginable. From circles to triangles to custom shapes that fit a specific enclosure, the possibilities are endless. This flexibility allows designers to create boards that are optimized for their specific application, whether it’s a wearable device or an industrial sensor.
3. PCB Prototypes Can Have Up To 50 Layers
Most PCBs have just a few layers, but prototypes can be made with up to 50 layers or more. These high-layer-count boards are used in complex applications such as aerospace and military equipment, where space is at a premium and signal integrity is critical. The more layers a board has, the more challenging it is to manufacture, but advanced PCB prototyping techniques make it possible.
4. PCB Prototypes Can Be Made With Flexible Materials
Not all PCBs are rigid. Flexible PCBs, also known as flex circuits, are made with flexible materials that allow the board to bend and twist without breaking. These boards are often used in applications where space is limited or where the board needs to conform to a specific shape, such as in wearable devices or automotive applications. PCB prototypes can be made with flexible materials, allowing designers to test their designs before committing to a full production run.
5. PCB Prototypes Can Have Embedded Components
Traditionally, electronic components are placed on the surface of a PCB and soldered in place. However, PCB prototypes can be made with embedded components, where the components are placed inside the layers of the board itself. This technique allows for smaller, more compact designs and can improve signal integrity by reducing the distance between components. Embedded components are more challenging to manufacture than surface-mounted components, but they offer significant benefits in certain applications.
6. PCB Prototypes Can Be Made With High-Temperature Materials
Most PCBs are made with standard FR-4 material, which has a maximum operating temperature of around 130°C. However, some applications require boards that can withstand much higher temperatures, such as in industrial or automotive environments. PCB prototypes can be made with high-temperature materials such as polyimide or ceramic, which can withstand temperatures up to 260°C or higher. These materials are more expensive than standard FR-4, but they offer superior performance in harsh environments.
7. PCB Prototypes Can Have Integrated Antennas
Wireless connectivity is becoming increasingly important in many applications, from IoT devices to wearables. PCB prototypes can be made with integrated antennas, eliminating the need for external antennas and reducing the overall size of the device. These antennas can be printed directly onto the board using conductive inks or can be embedded into the layers of the board itself. Integrated antennas offer a more compact and efficient solution than external antennas, but they require careful design and testing to ensure optimal performance.
8. PCB Prototypes Can Be Made With Conductive Inks
Traditional PCBs are made with copper traces, but prototypes can be made with conductive inks as well. These inks can be printed directly onto the board using inkjet or screen printing techniques, allowing for faster and more cost-effective prototyping. Conductive inks are not as durable or conductive as copper traces, but they offer a quick and easy way to test a design before committing to a full production run.
9. PCB Prototypes Can Have 3D-Printed Components
3D printing has revolutionized many industries, and the PCB industry is no exception. PCB prototypes can be made with 3D-printed components, such as enclosures or mechanical parts. These components can be printed directly onto the board or can be printed separately and attached later. 3D printing allows for rapid prototyping and customization, enabling designers to quickly test different designs and make changes on the fly.
10. PCB Prototypes Can Have Embedded Sensors
PCB prototypes can be made with embedded sensors, such as temperature sensors, accelerometers, or pressure sensors. These sensors can be placed directly onto the board or can be embedded into the layers of the board itself. Embedded sensors offer a more compact and integrated solution than external sensors, but they require careful design and calibration to ensure accurate readings.
11. PCB Prototypes Can Be Made With Biodegradable Materials
As concerns about electronic waste continue to grow, some manufacturers are exploring the use of biodegradable materials in PCBs. PCB prototypes can be made with materials such as paper or bioplastics, which can break down naturally in the environment. These materials are not as durable or reliable as traditional PCB materials, but they offer a more sustainable option for certain applications.
12. PCB Prototypes Can Have Integrated Lighting
Finally, PCB prototypes can be made with integrated lighting, such as LEDs or EL wire. These lighting elements can be placed directly onto the board or can be embedded into the layers of the board itself. Integrated lighting can be used for a variety of purposes, from indicating the status of a device to creating a unique aesthetic. PCB prototypes with integrated lighting require careful design and power management to ensure optimal performance and longevity.
FAQs
1. How much does it cost to make a PCB prototype?
The cost of making a PCB prototype can vary widely depending on factors such as the size and complexity of the board, the materials used, and the quantity ordered. In general, a simple two-layer board can cost anywhere from $50 to $500 or more, while a complex multi-layer board with embedded components and custom features can cost several thousand dollars. However, many PCB prototyping services offer discounts for larger orders or for repeat customers.
2. How long does it take to make a PCB prototype?
The turnaround time for a PCB prototype can range from 24 hours to several weeks, depending on the complexity of the design and the manufacturing process used. Simple two-layer boards can often be manufactured in just a few days, while more complex boards with multiple layers and custom features may take longer. Rush services are available from some manufacturers, but they typically come with a higher price tag.
3. What software is used to design PCB prototypes?
There are many software tools available for designing PCB prototypes, ranging from simple schematic capture tools to complex 3D modeling software. Some of the most popular tools include:
Software | Description |
---|---|
Altium Designer | A comprehensive PCB design tool with advanced features for high-speed design and multi-board projects. |
Eagle | A widely-used PCB design tool with a large library of components and a user-friendly interface. |
KiCad | A free, open-source PCB design tool with a growing community of users and developers. |
OrCAD | A powerful PCB design tool with advanced simulation and analysis capabilities. |
4. What are the most common materials used in PCB prototypes?
The most common material used in PCB prototypes is FR-4, a glass-reinforced epoxy laminate that offers good insulation properties and mechanical strength. Other common materials include:
Material | Description |
---|---|
Polyimide | A high-temperature material that can withstand temperatures up to 260°C or higher. |
Ceramic | A high-performance material that offers excellent thermal and electrical properties. |
Aluminum | A lightweight, heat-dissipating material that is often used in LED lighting applications. |
Copper | A highly conductive material that is used for traces and vias on most PCBs. |
5. What are the most common problems encountered when making PCB prototypes?
Some of the most common problems encountered when making PCB prototypes include:
Problem | Description |
---|---|
Design errors | Mistakes in the schematic or layout can lead to functionality issues or manufacturing defects. |
Manufacturing defects | Problems with the manufacturing process, such as incorrect hole sizes or misaligned layers, can result in non-functional boards. |
Component availability | Shortages or obsolescence of certain components can delay the prototyping process or require design changes. |
Signal integrity issues | High-speed designs can be susceptible to signal integrity problems such as crosstalk or electromagnetic interference. |
Power management issues | Incorrect power supply design or inadequate power management can lead to overheating or device failure. |
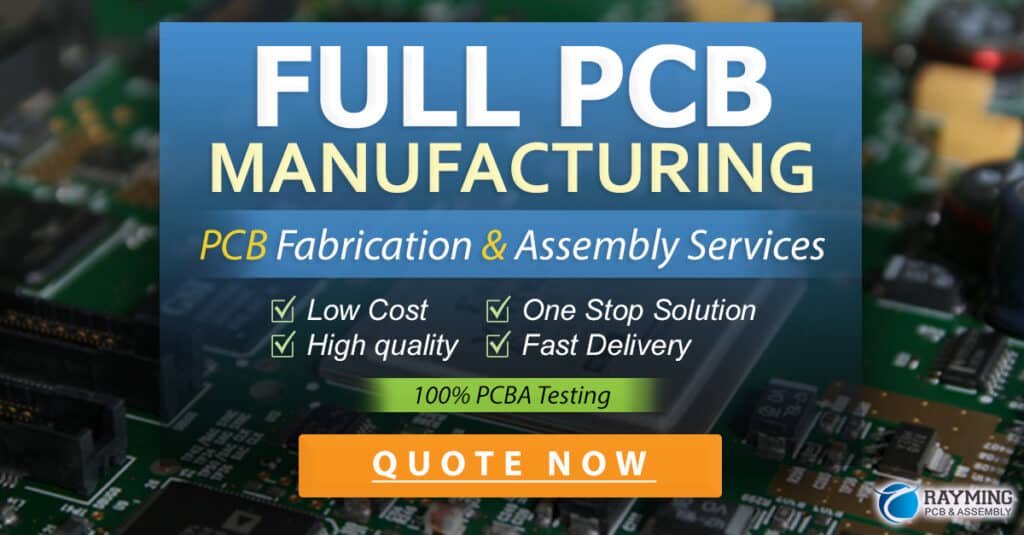
Conclusion
PCB prototypes are a critical step in the electronics design process, allowing designers to test and refine their designs before committing to a full production run. As we’ve seen in this article, there are many surprising and fascinating aspects to PCB prototyping, from the rapid turnaround times and unusual shapes to the advanced materials and embedded components.
By understanding these 12 insane (but true) facts about PCB prototypes, designers can make more informed decisions about their designs and take advantage of the latest technologies and techniques to create better, more reliable products. Whether you’re a seasoned engineer or a hobbyist just starting out, the world of PCB prototyping is full of exciting possibilities and endless potential.
No responses yet