Factors Affecting PCB Pricing
Several key factors contribute to the overall cost of a PCB. Understanding these factors can help you optimize your design and make cost-effective choices throughout the manufacturing process.
1. Board Size and Complexity
The size and complexity of a PCB have a significant impact on its pricing. Larger boards require more material and take longer to manufacture, resulting in higher costs. Additionally, complex designs with intricate layouts, multiple layers, and high component density will also drive up the price.
Consider the following table, which illustrates the relationship between board size and cost:
Board Size (mm) | Relative Cost |
---|---|
25 x 25 | 1x |
50 x 50 | 2x |
100 x 100 | 4x |
200 x 200 | 8x |
As the board size doubles, the relative cost increases exponentially. Therefore, it’s essential to optimize your design and keep the board size as small as possible while still meeting your functional requirements.
2. Number of Layers
The number of layers in a PCB directly affects its cost. Each additional layer requires more material, processing time, and labor, leading to higher manufacturing expenses. Here’s a comparison of the cost implications for different layer counts:
Number of Layers | Relative Cost |
---|---|
1 | 1x |
2 | 1.5x |
4 | 2x |
6 | 3x |
8 | 4x |
As a general rule, it’s best to use the minimum number of layers required for your design. However, in some cases, using more layers can help reduce the overall board size, which may offset the increased cost due to the additional layers.
3. Material Selection
The choice of materials for your PCB will also impact its pricing. The most common PCB materials are FR-4, which is a glass-reinforced epoxy laminate, and aluminum for metal core PCBs (MCPCBs). The cost of these materials can vary depending on their quality, thickness, and special properties such as high-temperature resistance or low dielectric constant.
In addition to the base material, the copper weight used for the conductive layers also affects the cost. Thicker copper layers (e.g., 2 oz) are more expensive than thinner ones (e.g., 1 oz) due to the increased amount of copper required.
4. Surface Finish
The surface finish applied to a PCB serves to protect the copper traces from oxidation and enhance the solderability of components. Common surface finishes include:
- Hot Air Solder Leveling (HASL)
- Organic Solderability Preservative (OSP)
- Electroless Nickel Immersion Gold (ENIG)
- Immersion Silver (IAg)
- Immersion Tin (ISn)
Each surface finish has its own advantages and cost implications. HASL is the most economical option, while ENIG and IAg offer superior flatness and durability at a higher cost. OSP and ISn provide a balance between cost and performance.
5. Quantity and Turnaround Time
The quantity of PCBs you order and the turnaround time you require will also affect the pricing. Manufacturers often offer volume discounts for larger orders, as the fixed costs associated with setting up the production run can be spread across more units. The following table shows an example of volume pricing:
Quantity | Price per Unit |
---|---|
1-50 | $10 |
51-100 | $8 |
101-500 | $6 |
501-1000 | $4 |
1000+ | $3 |
Faster turnaround times also generally incur higher costs, as manufacturers may need to prioritize your order and work overtime to meet the deadline. If your project timeline allows, opting for a standard turnaround time can help reduce costs.
Design Considerations for Cost Optimization
In addition to understanding the factors that affect PCB pricing, there are several design considerations that can help optimize costs:
1. Standardization
Using standard PCB sizes, layer counts, and materials can help reduce costs by allowing manufacturers to optimize their production processes. Custom sizes and materials may require special tooling or handling, which can increase costs.
2. Panelization
Panelizing your PCB design involves arranging multiple copies of the same board on a larger panel for production. This approach can help reduce costs by minimizing material waste and increasing manufacturing efficiency.
3. Via Optimization
Minimizing the number of vias and using standard via sizes can help reduce drilling costs and improve manufacturing yields. Buried and blind vias, while useful for certain designs, are more expensive than through-hole vias.
4. Component Selection
Choosing components that are readily available and have standard packaging can help reduce costs. Using exotic or hard-to-find components may increase procurement costs and lead times.
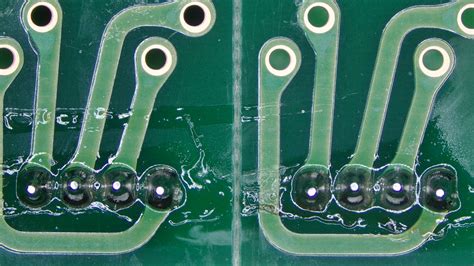
PCB Pricing Services and Tools
To help streamline the PCB pricing process, many manufacturers and service providers offer online tools and services that allow you to quickly generate quotes based on your design specifications. These tools often provide instant pricing feedback, enabling you to make informed decisions and optimize your design for cost.
Some popular PCB pricing services and tools include:
- PCBWay: https://www.pcbway.com/quote.aspx
- JLCPCB: https://jlcpcb.com/quote
- ALLPCB: https://www.allpcb.com/quote
- EasyEDA: https://easyeda.com/order
These services typically allow you to upload your PCB design files (e.g., Gerber files) and specify your requirements, such as quantity, layer count, and surface finish. They then provide an instant quote based on your inputs.
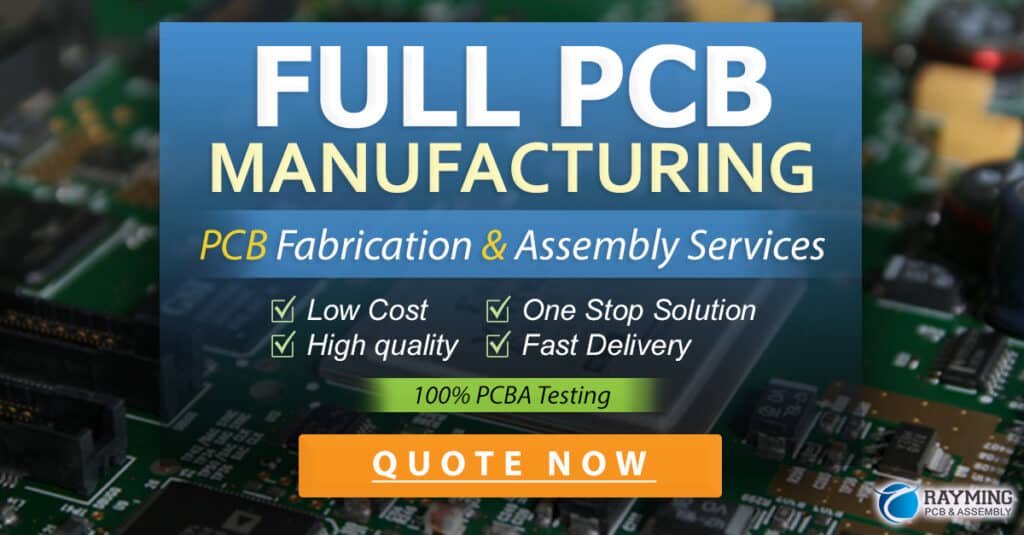
FAQ
1. What is the most cost-effective PCB material?
FR-4 is the most commonly used and cost-effective PCB material for general-purpose applications. It offers a good balance of mechanical and electrical properties at a reasonable price point.
2. How can I reduce the cost of my PCB design?
To reduce the cost of your PCB design, consider the following strategies:
- Minimize board size and layer count
- Use standard materials and components
- Optimize via placement and sizing
- Panelize your design for production
- Choose a cost-effective surface finish
3. What is the minimum order quantity for PCBs?
The minimum order quantity (MOQ) for PCBs varies among manufacturers. Some may have no MOQ, while others may require a minimum of 5, 10, or even 100 pieces. It’s essential to check with your chosen manufacturer for their specific MOQ requirements.
4. How does the aspect ratio affect PCB pricing?
The aspect ratio of a PCB refers to the ratio of its length to its width. PCBs with high aspect ratios (e.g., long and narrow) can be more challenging to manufacture and may require special handling, leading to increased costs. Aim for aspect ratios close to 1:1 for optimal pricing.
5. Can I get a discount for ordering large quantities of PCBs?
Yes, most PCB manufacturers offer volume discounts for larger orders. The specific discount structure varies among manufacturers, but generally, the price per unit decreases as the order quantity increases. It’s always a good idea to request quotes for different quantities to determine the most cost-effective option for your needs.
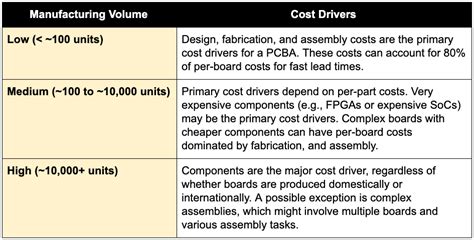
Conclusion
PCB pricing is a critical aspect of electronic product development, and understanding the factors that influence costs can help you make informed decisions throughout the design and manufacturing process. By considering board size, layer count, material selection, surface finish, and order quantity, you can optimize your PCB design for cost-effectiveness.
Additionally, utilizing PCB pricing services and tools can streamline the quoting process and provide instant feedback on your design choices. By carefully balancing your technical requirements with cost considerations, you can ensure that your PCB-based projects are both functional and economically viable.
No responses yet