Table of Contents
- Introduction to PCB Pricing
- PCB-Design-complexity”>PCB design Complexity
- Number of Layers
- Board Size
- Trace Width and Spacing
- Vias and Holes
- PCB material selection
- Substrate Materials
- Copper Thickness
- Solder Mask and Silkscreen
- Surface Finish
- Manufacturing Process
- Fabrication Techniques
- Batch Size and Turnaround Time
- Quality Control and Testing
- Additional Factors Affecting PCB Pricing
- Design Support and Prototyping
- Certifications and Compliance
- Shipping and Logistics
- Cost Optimization Strategies
- Design for Manufacturability (DFM)
- Material Selection and Standardization
- Batch Size Optimization
- Supplier Negotiations and Long-Term Contracts
- PCB Pricing Trends and Market Dynamics
- Frequently Asked Questions (FAQ)
- Conclusion
Introduction to PCB Pricing
PCB pricing is a complex topic that involves multiple variables and considerations. Understanding the factors that influence PCB pricing is crucial for electronics manufacturers, designers, and buyers to make informed decisions and optimize their costs. In this article, we will delve into the various aspects that contribute to the price composition of PCBs, including design complexity, material selection, manufacturing processes, and additional factors.
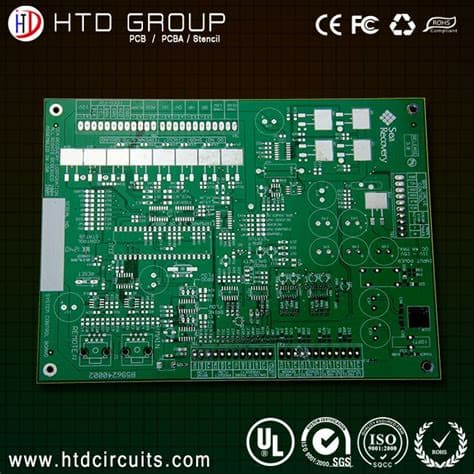
PCB Design Complexity
The complexity of a PCB design is one of the primary factors that affect its pricing. The following elements play a significant role in determining the overall design complexity:
Number of Layers
PCBs can be classified based on the number of layers they contain, such as single-sided, double-sided, or multi-layer boards. As the number of layers increases, so does the complexity of the design and the manufacturing process, resulting in higher costs.
Number of Layers | Relative Cost |
---|---|
Single-sided | Low |
Double-sided | Medium |
4-layer | High |
6-layer and above | Very High |
Board Size
The physical dimensions of the PCB, including length, width, and thickness, impact the pricing. Larger boards require more material and may necessitate specialized handling during manufacturing, leading to increased costs.
Trace Width and Spacing
The width of the conductive traces on the PCB and the spacing between them affect the manufacturing complexity. Narrower traces and tighter spacing require more precise fabrication techniques, which can drive up the cost.
Vias and Holes
Vias are conductive pathways that connect different layers of the PCB, while holes are used for mounting components or providing electrical connections. The number, size, and type of vias and holes influence the manufacturing process and, consequently, the pricing.
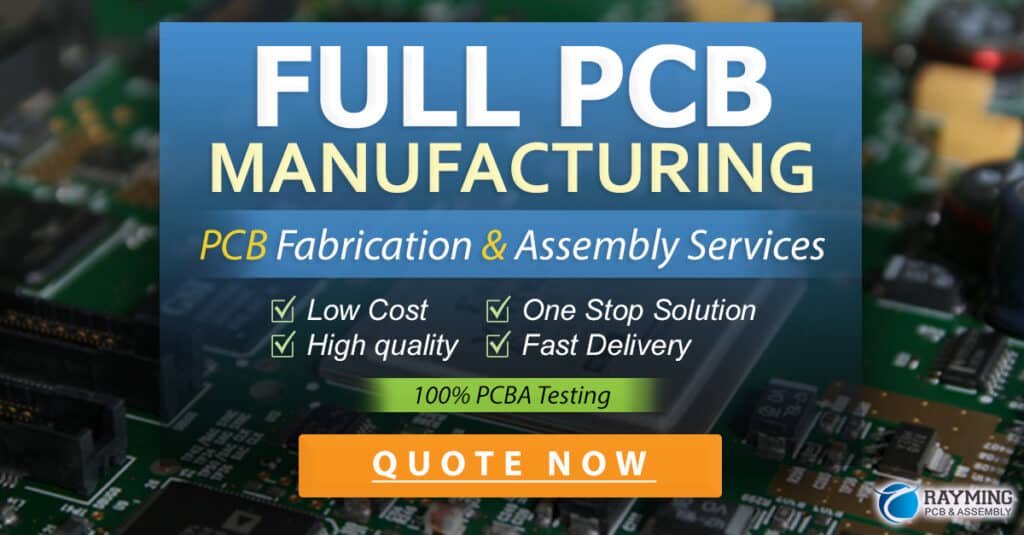
PCB Material Selection
The choice of materials used in PCB fabrication has a significant impact on the price. The following factors should be considered:
Substrate Materials
The substrate is the insulating material that forms the base of the PCB. Common substrate materials include FR-4, Rogers, and polyimide. Each material has different properties, such as dielectric constant, thermal stability, and cost.
Substrate Material | Relative Cost |
---|---|
FR-4 | Low to Medium |
Rogers | High |
Polyimide | Very High |
Copper Thickness
The thickness of the copper layer on the PCB affects its electrical properties and current-carrying capacity. Thicker copper layers are more expensive due to the increased material usage and processing requirements.
Solder Mask and Silkscreen
Solder mask is a protective coating applied to the PCB to prevent short circuits and improve solderability. Silkscreen is used for labeling and marking components on the board. The choice of colors and the complexity of the solder mask and silkscreen designs can impact the pricing.
Surface Finish
The surface finish on the PCB protects the exposed copper and enhances solderability. Common surface finishes include Hot Air Solder Leveling (HASL), Organic Solderability Preservative (OSP), and Electroless Nickel Immersion Gold (ENIG). Each surface finish has different properties and associated costs.
Surface Finish | Relative Cost |
---|---|
HASL | Low |
OSP | Low to Medium |
ENIG | High |
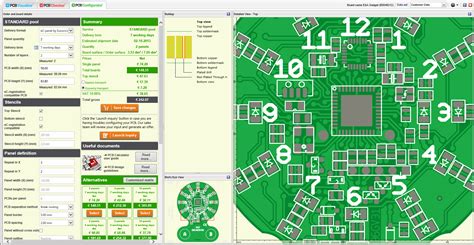
Manufacturing Process
The manufacturing process employed in PCB fabrication plays a crucial role in determining the pricing. The following aspects should be considered:
Fabrication Techniques
PCBs can be manufactured using various techniques, such as subtractive (e.g., etching) or additive (e.g., inkjet printing) processes. The choice of fabrication technique depends on the design requirements, material compatibility, and production volume. Different techniques have varying costs associated with them.
Batch Size and Turnaround Time
The number of PCBs ordered in a single batch and the required turnaround time significantly influence the pricing. Larger batch sizes often result in lower per-unit costs due to economies of scale. Shorter turnaround times may incur additional charges for expedited processing.
Batch Size | Relative Cost per Unit |
---|---|
Low | High |
Medium | Medium |
High | Low |
Quality Control and Testing
Rigorous quality control measures and testing procedures are essential to ensure the reliability and functionality of PCBs. These processes add to the overall manufacturing cost but are necessary to meet industry standards and customer requirements.
Additional Factors Affecting PCB Pricing
Apart from design complexity, material selection, and manufacturing processes, several other factors can impact PCB pricing:
Design Support and Prototyping
Many PCB manufacturers offer design support services and prototyping capabilities. These value-added services can incur additional costs but help streamline the development process and ensure design feasibility.
Certifications and Compliance
Certain industries, such as automotive, aerospace, and medical, have stringent certification and compliance requirements for PCBs. Meeting these standards may involve additional testing, documentation, and specialized manufacturing processes, which can increase the overall cost.
Shipping and Logistics
The cost of shipping and logistics can vary depending on the PCB manufacturer’s location, the customer’s location, and the chosen shipping method. International shipping and customs duties can add significant costs to the final price.
Cost Optimization Strategies
To optimize PCB pricing and reduce costs, consider the following strategies:
Design for Manufacturability (DFM)
Designing PCBs with manufacturability in mind can help minimize production challenges and reduce costs. This involves adhering to design guidelines, using standard components, and avoiding unnecessary complexity.
Material Selection and Standardization
Careful selection of materials based on the specific requirements of the application can help optimize costs. Standardizing materials across multiple designs can lead to volume discounts and improved supply chain efficiency.
Batch Size Optimization
Analyzing the trade-offs between batch size and per-unit costs can help identify the optimal production volume. Striking a balance between inventory holding costs and economies of scale is crucial for cost optimization.
Supplier Negotiations and Long-Term Contracts
Establishing long-term relationships with PCB manufacturers and negotiating favorable terms can lead to cost savings. Volume commitments and long-term contracts can provide pricing stability and enable better planning.
PCB Pricing Trends and Market Dynamics
The PCB industry is constantly evolving, with new technologies, materials, and manufacturing processes emerging. Keeping track of market trends and dynamics is essential for making informed decisions about PCB pricing. Some notable trends include:
- Miniaturization and increased density of components
- Adoption of advanced materials, such as high-frequency laminates
- Growing demand for flexible and rigid-Flex PCBs
- Increasing use of embedded components and 3D printing techniques
- Shift towards environmentally friendly materials and processes
Frequently Asked Questions (FAQ)
-
Q: What is the most significant factor affecting PCB pricing?
A: The complexity of the PCB design, including the number of layers, board size, and trace width and spacing, is often the most significant factor affecting pricing. -
Q: How can I reduce the cost of my PCB project?
A: To reduce costs, consider optimizing your design for manufacturability, standardizing materials, and carefully selecting the appropriate manufacturing process. Engaging in long-term contracts and negotiating with suppliers can also lead to cost savings. -
Q: What is the difference between subtractive and additive PCB fabrication techniques?
A: Subtractive techniques, such as etching, involve removing unwanted copper from the PCB substrate. Additive techniques, such as inkjet printing, involve depositing conductive materials onto the substrate. Each technique has its own advantages, limitations, and associated costs. -
Q: How does the choice of surface finish affect PCB pricing?
A: Different surface finishes, such as HASL, OSP, and ENIG, have varying costs associated with them. HASL is generally the most cost-effective option, while ENIG is more expensive due to the use of gold in the plating process. -
Q: Can I negotiate pricing with PCB manufacturers?
A: Yes, it is possible to negotiate pricing with PCB manufacturers, especially for large-volume orders or long-term contracts. Building a strong relationship with your supplier and demonstrating a commitment to ongoing business can help secure more favorable pricing terms.
Conclusion
PCB pricing is a multifaceted topic that requires careful consideration of various factors, including design complexity, material selection, manufacturing processes, and additional elements such as certifications and logistics. By understanding the key drivers of PCB pricing, electronics manufacturers, designers, and buyers can make informed decisions to optimize costs and ensure the success of their projects.
Effective cost optimization strategies, such as designing for manufacturability, standardizing materials, optimizing batch sizes, and negotiating with suppliers, can help mitigate the impact of pricing challenges. Staying updated on PCB industry trends and market dynamics is also crucial for adapting to changing requirements and maintaining a competitive edge.
Ultimately, the goal is to strike a balance between cost, quality, and performance while meeting the specific needs of the application. By carefully evaluating the price composition of PCBs and implementing appropriate cost optimization measures, businesses can achieve their objectives and succeed in the dynamic world of electronics manufacturing.
No responses yet